Printable Version of Topic
914World.com _ 914World Garage _ too much oil pressure?
Posted by: Vacca Rabite May 17 2010, 08:57 AM
My 2056 is getting elevated oil temps on the freeway. I am using a high volume pump, and seeing about 40 pounds of pressure on the freeway when my oil is up to temp.
What I think is happening is that there is too much pressure, and the oil is not being pumped through the oil cooler due to the check valve closing the passage. However, this is just a guess, as I don't have any way to test it. All I know is that when I am driving at revs, oil temp goes up and if I keep driving at higher revs the oil temps stay up). if I drop revs, oil temps fall back into place, but I can't do that on the freeway without building a lot of head heat.
Before I go through the trouble and expense of adding an oil cooler, I want to make sure that I have checked out the simple fixes first.
What do I do to make sure oil if going through the oil cooler? What is the point where pressure cuts off passage through the cooler?
All tin is in place, and fan housing flaps divert air over the oil cooler 100% of the time (no thermostat in place, so the flaps are always set to cool).
Zach
Posted by: r_towle May 17 2010, 09:00 AM
Interesting issue.
I dont know the pressure cut off, but I would ask a question.
Do you have the little air flappers on the bottom of the firewall?
We have seen a considerable cooling affect on the oil specifically when those are in place.
Rich
Posted by: Vacca Rabite May 17 2010, 09:03 AM
Yep, the little flaps are in place.
And I should mention that all the tin is in place. The flaps in the fan housing the always open, as I don't have a thermostat installed, so there is also air being diverted over the oil cooler. Oil used is Brad Penn 20-50.
Zach
Posted by: r_towle May 17 2010, 09:06 AM
I have always seen high oil temps at 65 mph up to 100.
The air gets so smooth over the car that it heats up and highways speeds...odd car.
We used a simple sandwich adapter and a 2*10 inch oil cooler strapped right on the engine bar...so its simple top install.
We put a little duct to divert air from under the car...kinda like a shovel scoop deal.
It did the trick and we could retain the heat...not run long ass hoses etc etc.
Rich
Posted by: Vacca Rabite May 17 2010, 09:11 AM
QUOTE(r_towle @ May 17 2010, 10:06 AM)

We used a simple sandwich adapter and a 2*10 inch oil cooler strapped right on the engine bar...so its simple top install.
We put a little duct to divert air from under the car...kinda like a shovel scoop deal.
It did the trick and we could retain the heat...not run long ass hoses etc etc.
Rich
I was either going to do it this way, or put it right under the engine lid above the engine. Are you using a thermostat to control when the oil goes to the cooler?
What temps were you seeing before you added the cooler.
What I want to determine is if I have a problem that I can fix via tuning, or adding a stronger spring to the plunger or something. I'd like to make adding an oil cooler the last option.
Zach
Posted by: underthetire May 17 2010, 09:13 AM
I get 40 PSI at 210 deg on the Fwy as well. Fought this a long time, some reasons I found are
Sound pad not anchored correctly to the firewall, allowing it to move closing off the air intake.
Heater flappers and loose tin. Mine did a huge drop in temp when I pulled of the heater crap and blocked the air ports from the shroud. I believe it was just blowing air around the big gaps in the ducting. Once I got the header in, temps dropped even more. I would think bad flapper valves could cause this as well?
Switched oil to a part synthetic.
Mine used to climb up to about 240 on the freeway before this (80 deg day or so) now i'm down to 190-200 or so.
Posted by: Lennies914 May 17 2010, 09:14 AM
Zach,
I had this exact discussion with BDStone at WCR this weekend. You should PM him. He has worked for Hayden coolers for many years and is very knowledgable. I questioned him on oil pressure vs. cooling, and it's a myth. Rather than me try to give you second hand info you should contact him directly.
Lennie
Posted by: r_towle May 17 2010, 09:18 AM
I recall that either aircooled.net, cbperformance, or one of the german type 4 tuners had a spring/plunger kit for the type 4.
I also (its foggy) remember that when you go to a high output pump, you need to swap over the spring to match.
I think if you call CB, they should be able to advise...or aircooled.net.
I agree, you should not have to put in a cooler.
I took it out once the car stopped being a track car...the track is what was killing it.
Autox is simple one minute runs...no need for an oil cooler.
Street is also simple enough...no need for a cooler.
To much advance....even 2-4 degrees, will raise up the temps quite a bit.
If you have a real good digital timing light that you can set the advance....tune it to 30 degrees first...then drop back.
I found it a really hard start at anything below 28 degrees.
It gets really hot at anything from 30-34 degrees.
So that is the level of detail in timing that I have experienced...and its amazing what a couple of degrees will do to an aircooled.
Given your carbs....I would still check the timing at full advance
Get the car up to 3500 and pin the linkage there with a ziptie or a piece of string..
Then check you timing.
If you dont have the fancy timing light (I dont) you can mark the fan (printable gauge on PP)
I used a pic or sratch awl to mark the ten degrees in both directions...I did the first on in the car (it sucked) I did the next ones on the bench....much easier.
If you have the time, pull the front tin and pull the fan...mark it really well with a dremel...cut in little grooves.
Wipe the edge with a rag full of white paint...then wipe it all off so just the grooves are full.
This (BTW) is how to restore a framing square so you can read it again.
Rich
Posted by: Vacca Rabite May 17 2010, 09:19 AM
QUOTE(underthetire @ May 17 2010, 10:13 AM)

Heater flappers and loose tin. Mine did a huge drop in temp when I pulled of the heater crap and blocked the air ports from the shroud. I believe it was just blowing air around the big gaps in the ducting. Once I got the header in, temps dropped even more. I would think bad flapper valves could cause this as well?
Mine used to climb up to about 240 on the freeway before this (80 deg day or so) now i'm down to 190-200 or so.
I could try blocking the vents at the bottom of the car. My car has no heat (I use headers) so all the fan and heat ducting is out of the car. I also don't have the rubber pad on the firewall.
However, my fan shroud vents are vented to open air. I had read somewhere that capping them could be bad for cooling as it caused cavitation. But I don't think it would be that hard to cap and test them.
Your oil temps are what mine are right now on the freeway - until I pull off the freeway and take the B roads home.
Zach
Posted by: Vacca Rabite May 17 2010, 09:22 AM
My timing right now is at 28.5* Checked it two weeks ago when I did my valves. I have a mallory unilite and seem to have full advance by 3K - so that is where I checked it. I have tried 30* advance, and got more power for sure, but thought I heard slight pinging so I backed it off. I may try it again, though.
I'll also send a PM to BDStone. Thanks Lemmy.
Zach
Posted by: realred914 May 17 2010, 09:47 AM
these cars ran hot even stock (hence the factory adding the air flaps under the car, and the shrinking of the red zone on the oil temp gage.. Youhave a larger motor so even more heat is expected.
the 40 psi on freeway is not too high a pressure, any less and I'd be worried.
you may need an extra cooler.
I would certainly run a thrmostate bellows. it is poor economy to not get one, you will have much faster engine wear with no warm up ability. would you be fine running your chevy ford or honda with the thermostat removed???? come on now and get that thing in there to assure longer engine life
as far as the high temps, you might also want to check head temps to see what mihgt be out of control.
leaves and crap can block the oil cooler, check that
my stock 2.0 also runs hot on warm days on long freeway drives. have to back opff else temp keeps going up (and pressure donw!) I have all tin in place and sealed, every thing right to optimize the stock system, yet it still runs hot, i even retarded the timing a few degrees, no change!
I will be adding one oil cooler to my car becuase of this, until then I drive easy when it is hot and pay close attention to my gages and slow donw if too hot.
Posted by: Vacca Rabite May 17 2010, 09:55 AM
Thanks RealRed.
I have a Dakota Digital Head Temp gauge, with the sender on the #3 spark plug. My headtemps to rise on the freeway, but are about what should be expected given my terrain type and ambient temps (lots of elevation gain spread over 45 miles). As long as I put it in 4th before hitting the big hills on the freeway, my head temps stay in check. But my oil temps go up.
As I said, I will add an oil cooler, but I want to make sure that I hit the other stops first so that my fix is not actually masking the real issue.
Zach
Posted by: yeahmag May 17 2010, 10:29 AM
Got an O2 on the car? If not might want to get one or try richening up a tad and see what happens. I'm playing that game now. I'd also definitely block the heater outlets in the fan shroud. Too easy to *not* try...
My heads *never* heat up. When I'm racing (full throttle) I'm lucky to see 350F. A long climb will get them to almost 400F in 5th gear.
-Aaron
Posted by: detoxcowboy May 17 2010, 10:36 AM
"I recall that either aircooled.net, cbperformance, or one of the german type 4 tuners had a spring/plunger kit for the type 4.
I also (its foggy) remember that when you go to a high output pump, you need to swap over the spring to match." quote Towle
-this makes sense, seroiously balances the high output oil cooler.the ho cooler has givin you problems before? this is worth looking into.. 2 cents
Posted by: Jake Raby May 17 2010, 11:24 AM
40 PSI is perfect on the highway, its not high enough to cause oil temp elevations.
How hot is the oil getting? What oil is it?
Tuning is a big part of oil temperature, of course.
Posted by: 70_914 May 17 2010, 11:30 AM
QUOTE(realred914 @ May 17 2010, 08:47 AM)

I would certainly run a thrmostate bellows. it is poor economy to not get one, you will have much faster engine wear with no warm up ability. would you be fine running your chevy ford or honda with the thermostat removed???? come on now and get that thing in there to assure longer engine life
I have a pile of these laying around now, let me know if you need one. I heard they are hard to find, but I don't have that problem... I go and look on my work bench and find 4 of them
Like everything I have sold it would be cheap.
Posted by: Vacca Rabite May 17 2010, 11:36 AM
QUOTE(Jake Raby @ May 17 2010, 12:24 PM)

40 PSI is perfect on the highway, its not high enough to cause oil temp elevations.
How hot is the oil getting? What oil is it?
Tuning is a big part of oil temperature, of course.
~235 to 245 before I get off the freeway and on to the B roads for the rest of my trip. Oil is Brad Penn 20-50.
QUOTE
Got an O2 on the car? If not might want to get one or try richening up a tad and see what happens. I'm playing that game now. I'd also definitely block the heater outlets in the fan shroud. Too easy to *not* try...
I am going to try blocking them this week and then driving my car to work.
I want to add an O2, but have not done so yet.
The other thing, which you just reminded me... I bet I can get another degree or two of advance. the last time I tried it, I was using the IDF44s, which were a little lean to start with. I don't know why I did not think of that this morning when Rich asked about timing. My current 40IDF set up is much nicer, and not a tad lean like the 44s were. I need to try a little more advance. I don't know that it will solve all the problems, but it will help I bet.
Zach
Posted by: mightyohm May 17 2010, 11:37 AM
QUOTE(r_towle @ May 17 2010, 08:06 AM)

We used a simple sandwich adapter and a 2*10 inch oil cooler strapped right on the engine bar...so its simple top install.
We put a little duct to divert air from under the car...kinda like a shovel scoop deal.
It did the trick and we could retain the heat...not run long ass hoses etc etc.
Do you have a pic of this?
Posted by: Vacca Rabite May 17 2010, 11:42 AM
QUOTE(70_914 @ May 17 2010, 12:30 PM)

QUOTE(realred914 @ May 17 2010, 08:47 AM)

I would certainly run a thrmostate bellows. it is poor economy to not get one, you will have much faster engine wear with no warm up ability. would you be fine running your chevy ford or honda with the thermostat removed???? come on now and get that thing in there to assure longer engine life
I have a pile of these laying around now, let me know if you need one. I heard they are hard to find, but I don't have that problem... I go and look on my work bench and find 4 of them
Like everything I have sold it would be cheap.
I actually have a bellows, and I think it is even functional - though I have not tested it (and may have even given it away). my issue is that the flaps, which are supposed to fail open for cooling, twice failed closed. The bushings are crap and need to be replaced - and I need to drop the motor to do that , I think. I'd rather be driving now. if the motor fails after 50K miles from longer cold starts, that would still give me ~10 years of drive time - and by then I'll want to build a new motor anyway. Given that it is usually pretty warm during the driving season, I am not too concerned about my lack of a bellows. if i did a lot of driving in the cold (remember, my car has no heat), I would put one in for sure.
Zach
Posted by: yeahmag May 17 2010, 11:43 AM
I haven't gotten a solid answer on this, but I don't think you can run the thermostat with a header.
Posted by: HAM Inc May 17 2010, 11:54 AM
You need to keep in mind that all of the oil does run through the cooler before it hits the bypass valve.
Tight piston clearances will cause high oil temps.
Posted by: tradisrad May 17 2010, 11:57 AM
I'm curious how high oil pressure makes the oil temp rise?
My car does not run too hot, between 180 and 220, and my oil pressure is 60 psi on the freeway and over 80psi (pegged gauge) on cold starts.
Also, Zach mentioned that there is a check valve to bypass the oil cooler how and at what pressure does this work?
Posted by: Vacca Rabite May 17 2010, 12:14 PM
QUOTE(HAM Inc @ May 17 2010, 12:54 PM)

You need to keep in mind that all of the oil does run through the cooler before it hits the bypass valve.
Tight piston clearances will cause high oil temps.
Interesting. Is the bypass valve just for the oil filter? I thought it was for the oil cooler. So adding a more powerful spring would have zero effect in this case, as it makes no difference if the valve is open or closed?
When you say tight piston clearances, do you mean the piston on the spring that works the valve, or the 4 biggies that move the car?
Learning every day.
Zach
Posted by: DanT May 17 2010, 12:20 PM
When I built my 2056 I did away with the thermostat for the motor and permanently put the flaps to the position to always direct air over the stock oil cooler...I also ran a very large cooler and fan up front...
Car never had an issue with temps...but I also ran stock oil pump and did not change any of the bypass springs...also ran a Tuna Can.
I had good oil pressures at all operating RPMS and temps....
Posted by: HAM Inc May 17 2010, 12:31 PM
Zach the pressure bypass drops the pressure in the entire circuit from the pump to the bearings. It doesn't matter which end of the circuit the relief occurs. That is the cool thing about the circuit design. Bypassed oil has already been through the cooler before it is dumped back into the case. And since a certain amount of oil is always being bypassed (if the system is working properly) you have a % of oil that routes through the cooler more than once before it sees the bearings.
By tight piston clerances I meant the piston to cylinder clearance of the 4 pistons.
Posted by: Vacca Rabite May 17 2010, 12:39 PM
Okay. Bear with me, as I am just thinking through my fingers right now.
If a percentage of the oil is always going through the cooler, would adding a stiffer spring to the relief valve increase or decrease the percentage of oil going through the cooler? Or would it give no change to the oil going through the cooler?
I don't think that my pistons are too tight. before I put the rings on, you could put them in and out of the cylinders w/o issue.
Zach
Posted by: mightyohm May 17 2010, 12:52 PM
What oil temps are you actually seeing?
Posted by: jhadler May 17 2010, 12:53 PM
QUOTE(HAM Inc @ May 17 2010, 09:54 AM)

...Tight piston clearances will cause high oil temps.
Thanks! I guess I kinda knew that in the back of my head, but seeing it written but one who knows has reminded me again to look at everything on my few hours old rebuild that was running way too hot.
Haven't had the time to finish the full tear down as work and family obligations have priority. But I've now got a clean bench in the garage, and will start going over it in detail.
Just to ask the question... What is the mechanism for the high oil temps with tight pistons. Is it just ring-wall friction wear that causes it? Or something else?
I found out later on that the builder claimed to have needed to "hammer" the pistons into the cylinders... Might be my culprit...
Sorry for the hijack....
-Josh2
Posted by: Vacca Rabite May 17 2010, 12:54 PM
QUOTE(mightyohm @ May 17 2010, 01:52 PM)

What oil temps are you actually seeing?
235-245 when on the freeway, before I get off the freeway and hit the side roads so my car cools down. Right now I am just not on the freeway that much.
Zach
Posted by: Spoke May 17 2010, 02:06 PM
QUOTE(Vacca Rabite @ May 17 2010, 11:19 AM)

I could try blocking the vents at the bottom of the car.
These are the tubes that used to go to the heat exchangers, correct?
If you think about it, with all the HE stuff in place, blowing air in the HE would cause some backpressure and limit some of the volume of air flowing.
Now you have removed the HE and all the tubing so the little stub of the tube on the fan assembly has no backpressure and would allow more air to escape to the atmosphere instead of being forced across the cylinders and oil cooler.
Kinda like if you put a big hole in the top of the fan shroud. The air will blow out through the hole where there is no backpressure instead of going across the cylinders and oil cooler where there is some resistance to air flow.
You don't want any air escaping from the fan shroud that could be going to the cylinders and oil cooler.
Posted by: jhadler May 17 2010, 02:32 PM
I forgot who originally mentioned the cavitation issue with block off the HE ports (Jake probably?). But I do see how it's possible if you're not venting enough pressure that you can decrease the efficiency of the fan by retaining too much pressure downstream of the fan blades.
Perhaps a small hole in the block-off plate to allow some of that excess pressure to bleed off?
-Josh2
QUOTE(Spoke @ May 17 2010, 12:06 PM)

QUOTE(Vacca Rabite @ May 17 2010, 11:19 AM)

I could try blocking the vents at the bottom of the car.
These are the tubes that used to go to the heat exchangers, correct?
If you think about it, with all the HE stuff in place, blowing air in the HE would cause some backpressure and limit some of the volume of air flowing.
Now you have removed the HE and all the tubing so the little stub of the tube on the fan assembly has no backpressure and would allow more air to escape to the atmosphere instead of being forced across the cylinders and oil cooler.
Kinda like if you put a big hole in the top of the fan shroud. The air will blow out through the hole where there is no backpressure instead of going across the cylinders and oil cooler where there is some resistance to air flow.
You don't want any air escaping from the fan shroud that could be going to the cylinders and oil cooler.
Posted by: Spoke May 17 2010, 03:00 PM
I thought cavitation was in respect to closing off the HE at the output of the HE or just leaving the HE on with no air flowing through them. Then you have a cavity. I'm not sure how the little (about 6 inch) part of the tube on the fan shroud could cause the fan to be less efficient.
One could block off the entrance of the tube inside the fan shroud to allow air to flow more efficiently to the cylinders and oil cooler.
Posted by: underthetire May 17 2010, 03:45 PM
Wouldn't blocking them off be the same as if you had a nice tight heat exchanger system and simply closed off the flapper valves with the heat lever ? I don't see how blocking off the shroud ports would be any different than that. I guess it could make a difference at a constant 8K rpm, but I will never see that kind of RPM.
Posted by: HAM Inc May 17 2010, 04:37 PM
QUOTE
If a percentage of the oil is always going through the cooler, would adding a stiffer spring to the relief valve increase or decrease the percentage of oil going through the cooler? Or would it give no change to the oil going through the cooler?
The stiffer the spring the higher the oil pressure and therefore the less bypass oil. Zach what is your oil pressure at the highest temps, 235-240?
QUOTE
Just to ask the question... What is the mechanism for the high oil temps with tight pistons. Is it just ring-wall friction wear that causes it? Or something else?
The friction is from the pistons dragging down the bores. Piston friction also increase if the jugs aren't square to the crank center line. That also leads to poor head sealing too. The head sealing issues are not as easy to pickup on as you might think. Jake is damn good at detecting it, but he has had some practice!
Posted by: AndrewP May 17 2010, 05:32 PM
Do you know if your oil temp gauge is accurate?
Andrew
Posted by: r_towle May 17 2010, 06:47 PM
Do you think your header might be adding heat to the motor?
How about some header wrap?
I dont remember how its designed but is there a tube or two that run under the motor and could create some additional thermal heating to the motor?
Did you have the case machined square prior to the build?
Rich
Posted by: Vacca Rabite May 17 2010, 07:55 PM
[quote name='HAM Inc' date='May 17 2010, 05:37 PM' post='1319705']
[quote]If a percentage of the oil is always going through the cooler, would adding a stiffer spring to the relief valve increase or decrease the percentage of oil going through the cooler? Or would it give no change to the oil going through the cooler?[/quote]
The stiffer the spring the higher the oil pressure and therefore the less bypass oil. Zach what is your oil pressure at the highest temps, 235-240?
35 psi when it gets hot cruising on the highway. I have only let it get there twice though. By the time the oil gets that thin I am looking for an exit.
At idle it will be about 10psi.
Rich, I might consider some header wrap for the pipes thatgo under the case. The headers are ceramic coated coated so they should not rust.
Posted by: r_towle May 17 2010, 08:14 PM
I had a decent idea for your header leak issue.
Cut a star that would fit into the middle of the pipes but it will only fit if the middle is higher than the points.
This would raise up the middle so you CAN get to it with the mig gun.
The sides and outer areas you can already get to...
Try it with posterboard....you will see what I mean.
Rich
Posted by: HAM Inc May 18 2010, 07:53 AM
QUOTE
35 psi when it gets hot cruising on the highway. I have only let it get there twice though. By the time the oil gets that thin I am looking for an exit.
At idle it will be about 10psi.
Zach that is propbably in the 10lbs/1000rpm's range. You sure don't want a softer bypass spring. I would be inclined to leave that alone and look elsewhere for your heating issue.
What is the history of your O.E. cooler?
Posted by: Vacca Rabite May 18 2010, 08:09 AM
QUOTE(HAM Inc @ May 18 2010, 08:53 AM)

What is the history of your O.E. cooler?
Came with the motor. I flushed the inside with oil and made sure the outside had no obstructions that would block air passage when I rebuilt the motor. I did not have it ultrasonicly cleaned.
I am using a EuroRace header, and the drivers side pipes do pass right under the oil pan, so that can't be helpful.
So, right now, these are the actions I am going to take:
1) Cap the stubby vents that are supposed to go to the heaters that currently just vent to open air, and see if that puts more air into the tins.
2) Try to add a little more advance to the timing (go from 28* to 30* and see what happens).
3) add a little header wrap or header blanket to the pipes that cross under the engine case.
Do the experts here see any issues with this plan?
Zach
Posted by: realred914 May 18 2010, 09:30 AM
QUOTE(DanT @ May 17 2010, 11:20 AM)

When I built my 2056 I did away with the thermostat for the motor and permanently put the flaps to the position to always direct air over the stock oil cooler...I also ran a very large cooler and fan up front...
Car never had an issue with temps...but I also ran stock oil pump and did not change any of the bypass springs...also ran a Tuna Can.
I had good oil pressures at all operating RPMS and temps....
Bad Bad Bad You NEED the proper warm up that the thermostat provides. Would you be ok running a Ford, Toyota or Honda with the thermostat removed? are you sure your temps are ok? running cold like after you first start the car after having it off and cool will increase wear, there is no doubt about it. also understand that ther is evidence posted that the flaps actually move during driving to help regulate the optimal temp.
I'd get the thermostat installed,do it right, your car is suffering from cold running with out the thermostat. false economy to skimp on a thermostat.
Why do so many folks with air cooled cars insist that removing of the warm up system is good for there cars? That dont happen in the world of water cooled cars, I wish folks would stop thinking they cool better or just fine with no warm up flaps and thermostat bellows.
get all that stuff installed and your engine will be much much happier.
high oil pressure usually means low temps (viscus oil) thus the relief valve when under higher pressure bypasses the cooler. as oil warms up and pressure drops, the relief valve sends more of the oil too the cooler. as the oil cools, the relief valve them starts to send some of the oil away from the cooler.
If you have some supper high pressure oil pump, more oil will bypass the cooler untill it gets hot enough to get thin enough for pressure to drop enough to be sent thru the cooler. If you run 90 wieght gear oil in the motor, the oil pressure would be way too high, and you'd be bypassing the cooler untill the oil got hot enough to thin it down such that pressure drops. however 90 is way too thick and it may have to get way too hot before it gets thin enough to be sent to the cooler.
your doing a balance act of pressure and temps. but you must keep in mind you motor needs a miminal oil pressure to lube ok (general rule of thimb is 10 psi per 1000 rpm as a minimal oil pressure) your oil has limits on how hot it can get before it is damaged, oil like to be not much more than 100C (boiling water at sea level) get too hot (say 125C and the oil can break down)
so you have some parameters to play with, you could put a stiffer spring int eh bypass such that the oil is sent thru the cooler at a higher pressure (ie when oil is cooler) but there is only so much you can do with springs. if the engine is shot, your oil pressure may not be high enough to ever by the cooler. if your oil is too thin, you may alway run it thru the cooler (and hence it might run cooler) however dont go too thin with the oil in attempst to get more to flow thru the cooler. there is a minimal viscosity you need to get good lubracation.
there are some knobs you can turn here to play with, the spring pressure (by pass point) and the oil viscosity.
Posted by: Racer Chris May 18 2010, 11:06 AM
I drive like a bat out of hell, pretty much all the time, and have trouble getting my oil temp up to 180. No external oil cooler. Except at idle oil pressure is always 40+psi.
Posted by: yeahmag May 18 2010, 11:08 AM
Damn... So what's your secret?
Posted by: Borderline May 18 2010, 11:23 AM
Zach, I haven't had the opportunity to verify this, but. I read an article on the internet which was promoting lower viscosity oil. This guy said that high viscosity oil limits the amount of oil flow through the bearings. He said that going to a lower viscosity oil will allow the oil to flow through the bearings more easily and will result in lower oil temps. That's the short version. I was going to test this on my new engine. The Brad Penn break-in oil is 30 wt and I figured if the oil pressures and temps stayed good during break-in I would stay with the the 30 wt when I changed the oil. I know B-P oil is not cheap, but it might be worth a try. Also, the original spec in the owners manual specified 30 wt. I'm one of those guys who fell into the trap of thinking higher viscosity is better. Not always.
FWIW just trying to help
Posted by: Elliot Cannon May 18 2010, 12:25 PM
Start your car and put your hand down by the vents that go to the HEs and you will find a lot of cooling air goes out those vents. Definately block those off then drive the car and see if there is a difference. I have the same euro headers on a 2.2 liter type IV and I don't think they effect the oil temp much at all. I also use an aux. oil cooler under the rear trunk with the sandwich type adapter with thermostat. I duct cooling air from a scoop in the rocker panel to the cooler. It seems to work really well. 235 to 240 degrees is a bit much. Blocking off the vents is probably the easiest, cheapest thing to try and I would do that first.
Attached thumbnail(s)
Posted by: Cap'n Krusty May 18 2010, 01:37 PM
Having seen the devastating effects of CV bolt failures on tranny cases and starters, I would be afraid such an event might take out the oil cooler and consequently all the oil in a rather hasty fashion .........................
The Cap'n
Posted by: realred914 May 18 2010, 01:53 PM
QUOTE(Elliot Cannon @ May 18 2010, 11:25 AM)

Start your car and put your hand down by the vents that go to the HEs and you will find a lot of cooling air goes out those vents. Definately block those off then drive the car and see if there is a difference. I have the same euro headers on a 2.2 liter type IV and I don't think they effect the oil temp much at all. I also use an aux. oil cooler under the rear trunk with the sandwich type adapter with thermostat. I duct cooling air from a scoop in the rocker panel to the cooler. It seems to work really well. 235 to 240 degrees is a bit much. Blocking off the vents is probably the easiest, cheapest thing to try and I would do that first.
if your running heater exchangers, you NEED to keep air flowing thru them. else they will self distruct from too much heat. that is why the factory had bleed air going thru them even when the heater was turned "off".
Posted by: Elliot Cannon May 18 2010, 01:53 PM
QUOTE(Cap'n Krusty @ May 18 2010, 12:37 PM)

Having seen the devastating effects of CV bolt failures on tranny cases and starters, I would be afraid such an event might take out the oil cooler and consequently all the oil in a rather hasty fashion .........................
The Cap'n
That's a good point and I will be re-locating the oil cooler to the front some day, however if I heard the noise of a broken cv and an axle flailing around back there, using my lightning like reflexes, I would probably have the engine shut off befor the green light came on.
Posted by: Cevan May 18 2010, 02:27 PM
QUOTE(realred914 @ May 18 2010, 03:53 PM)

QUOTE(Elliot Cannon @ May 18 2010, 11:25 AM)

Start your car and put your hand down by the vents that go to the HEs and you will find a lot of cooling air goes out those vents. Definately block those off then drive the car and see if there is a difference. I have the same euro headers on a 2.2 liter type IV and I don't think they effect the oil temp much at all. I also use an aux. oil cooler under the rear trunk with the sandwich type adapter with thermostat. I duct cooling air from a scoop in the rocker panel to the cooler. It seems to work really well. 235 to 240 degrees is a bit much. Blocking off the vents is probably the easiest, cheapest thing to try and I would do that first.
if your running heater exchangers, you NEED to keep air flowing thru them. else they will self distruct from too much heat. that is why the factory had bleed air going thru them even when the heater was turned "off".
I hope I'm not hijacking the thread. I'm just sorting out my new motor and didn't install any of the heat components, figuring that checking the torque on the HE nuts and checking for oil leaks would be that much easier. Is this ok for short (up to 20 minutes) break-in runs?
Posted by: Bleyseng May 18 2010, 02:32 PM
yeah, it will be fine.
Posted by: r_towle May 18 2010, 05:42 PM
QUOTE(Vacca Rabite @ May 18 2010, 10:09 AM)

QUOTE(HAM Inc @ May 18 2010, 08:53 AM)

What is the history of your O.E. cooler?
Came with the motor. I flushed the inside with oil and made sure the outside had no obstructions that would block air passage when I rebuilt the motor. I did not have it ultrasonicly cleaned.
I am using a EuroRace header, and the drivers side pipes do pass right under the oil pan, so that can't be helpful.
So, right now, these are the actions I am going to take:
1) Cap the stubby vents that are supposed to go to the heaters that currently just vent to open air, and see if that puts more air into the tins.
2) Try to add a little more advance to the timing (go from 28* to 30* and see what happens).
3) add a little header wrap or header blanket to the pipes that cross under the engine case.
Do the experts here see any issues with this plan?
Zach
Advanced timing creates heat.
Keep a close eye on the heat and move one degree at a time..same day, same run on the highway and you might get it.
Put some header tape on...it may help.
My son just put tape on his motorcycle pipes...you can now touch them.
No way to touch them prior, so it really does work.
Amazon sells it online...that is where he got it.
Rich
Posted by: yeahmag May 18 2010, 05:44 PM
I think too retarded makes heat too... At least that's what I've read.
Posted by: 70_914 May 18 2010, 07:03 PM
Too much oil pressure could cause excess heat because the oil would be flowing too quickly through the cooler for it to take enough heat out of the oil.
Posted by: Jake Raby May 18 2010, 07:19 PM
Thats my least favorite exhaust... For many reasons.
QUOTE
Jake is damn good at detecting it, but he has had some practice!
Yep, can hear it a mile away. Smell it too.
Posted by: Chris Hamilton May 18 2010, 07:40 PM
QUOTE(70_914 @ May 18 2010, 06:03 PM)

Too much oil pressure could cause excess heat because the oil would be flowing too quickly through the cooler for it to take enough heat out of the oil.
I'm sorry but that is not correct. More pressure causes better thermal conductivity to the walls of the cooler. Heat is a continual flow from the engine to the cooler, moving it more slowly is not going to help, it is simply going to conduct less thermal energy.
edit: rather than just tell you "you're wrong lol" I'll link here to an explanation which is probably more helpful than a random post on an internet forum
http://en.wikipedia.org/wiki/Thermal_contact_conductance
Posted by: 70_914 May 18 2010, 11:24 PM
QUOTE(Chris Hamilton @ May 18 2010, 06:40 PM)

QUOTE(70_914 @ May 18 2010, 06:03 PM)

Too much oil pressure could cause excess heat because the oil would be flowing too quickly through the cooler for it to take enough heat out of the oil.
I'm sorry but that is not correct. More pressure causes better thermal conductivity to the walls of the cooler. Heat is a continual flow from the engine to the cooler, moving it more slowly is not going to help, it is simply going to conduct less thermal energy.
edit: rather than just tell you "you're wrong lol" I'll link here to an explanation which is probably more helpful than a random post on an internet forum
http://en.wikipedia.org/wiki/Thermal_contact_conductance
"In physics, thermal contact conductance is the study of heat conduction between solid bodies in contact." First line in your article. Oil is not a solid, or there are more problems here than oil pressure.
Posted by: 70_914 May 18 2010, 11:33 PM
Here is some information:
http://www.machinerylubrication.com/Read/680/hydraulic-overheating
and another article:
http://www.engineersedge.com/heat_transfer/convection.htm
There are a lot of systems for fluid cooling that need to take into account length of hoses, every fitting, direction changes for fluid and then adjust fluid flow rate to achieve the cooling effect desired. Plastic injection presses use a manifold to precicely control nozzle temperatures and is the 1 example I know about from a hands on perspective.
Posted by: Chris Hamilton May 19 2010, 01:00 AM
Could you point out what part of your links apply to a front mounted oil cooler on a type IV motor?
I see a link about inefficiencies in high pressure hydraulic systems, and a second link that doesn't address pressure at all.
edit: actually your first link shows the heat dissipation of it's cooling system as directly proportional to the flow rate, which is the exact opposite of what you say above. Looks like a good example.
QUOTE
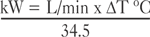
Where: kW = heat dissipation of exchanger in kilowatts
L/min = oil flow through the exchanger in liters per minute
T ºC = inlet oil temperature minus outlet oil temperature in Celsius
Posted by: 70_914 May 19 2010, 08:24 AM
Sorry to hijack the thread discussing basic thermodynamics but I will make a couple real world examples- since now I have agreement that fluid speed is the only variable in a closed system with a fixed cooler.
Example A: You are a college student. You are going to WWU taking plastics engineering with a double minor in physics and chemistry. You want to throw a killer party, and decide that running copper coils throgh a bucket of ice water is a good way to cool your beer as it exits a keg. The ice water is a constant temperature, the keg beer is also a constant temperature. You have a pressure valve to control flow through the copper coils. Your beer won't be the same cold temperature if you crank the pressure up to 50 psi and blast it through the coils, it will be colder if it goes through the coils a little slower and allows the ice water to remove more of the heat from the beer.
Example B: You are a fry cook and want to leave work early. You have a large griddle that needs to be cold before you can go home. You also have a piece of ice that is the exact width of this griddle. You can take the ice and rush it across the surface of the griddle at 2 inches per second and have over half the ice cube left at the other end- inefficient because the ice was not able to remove all the heat from the griddle and did not do as much work as it could of, or you could move the ice across the griddle at 1 inch per second and at the very last moment the ice is completely melted- very efficient because the ice was able to do all the work possible.
Both examples are abstract, neither example shows specifically a type IV engine with a pass through cooler, both examples show thermodynamics. Laws of physics don't change on a whim.
The overall heat transfer coefficient for a wall or heat exchanger can be calculated as:
1 / U A = 1 / h1 A1 + dxw / k A + 1 / h2 A2 (1)
where
U = the overall heat transfer coefficient (W/m2K)
A = the contact area for each fluid side (m2)
k = the thermal conductivity of the material (W/mK)
h = the individual convection heat transfer coefficient for each fluid (W/m2K)
dxw = the wall thickness (m)
The thermal conductivity - k - for some typical materials:
•Polypropylene PP - 0.12 W/mK
•Stainless steel - 21 W/mK
•Aluminum - 221 W/mK
The convection heat transfer coefficient - h - depends on
•the type of fluid - gas or liquid
the flow properties such as velocity
•other flow and temperature dependent properties
Heat transfer coefficient for some common fluids:
•Air - 10 to 100 W/m2K
•Water - 500 to 10 000 W/m2K
Posted by: realred914 May 19 2010, 08:26 AM
QUOTE(70_914 @ May 18 2010, 06:03 PM)

Too much oil pressure could cause excess heat because the oil would be flowing too quickly through the cooler for it to take enough heat out of the oil.
too much pressure causes the oil to flow more quikly???? seems that is the passage was blocked (ie no flow ) the pressure would really get high, the opposite of what your saying. if the oil flow had no resistance and no restiction, the pressure would be low and the flow rate very high.
flow rate and pressure are not always corrolated this way.
I high flow rate
may give better cooling than a low flow rate. if the flow rate is too slow, the heat flux is too low and less cooling is done. remeber the heat exchanger is most efficinet when there is a big temperature delta.
I say there maybe an optimal flow verses heat rejection. but it will not be the highest flow nor the lowest flow rate
Posted by: 70_914 May 19 2010, 08:30 AM
QUOTE(realred914 @ May 19 2010, 07:26 AM)

QUOTE(70_914 @ May 18 2010, 06:03 PM)

Too much oil pressure could cause excess heat because the oil would be flowing too quickly through the cooler for it to take enough heat out of the oil.
too much pressure causes the oil to flow more quikly???? seems that is the passage was blocked (ie no flow ) the pressure would really get high, the opposite of what your saying. if the oil flow had no resistance and no restiction, the pressure would be low and the flow rate very high.
flow rate and pressure are not always corrolated this way.
I high flow rate
may give better cooling than a low flow rate. if the flow rate is too slow, the heat flux is too low and less cooling is done. remeber the heat exchanger is most efficinet when there is a big temperature delta.
I say there maybe an optimal flow verses heat rejection. but it will not be the highest flow nor the lowest flow rate
Exactly... If the fluid is not moving no work is being done. If the fluid is flowing too quickly, inefficient work is being done.
I only answered the question of the post- would too much oil pressure cause high engine oil temps. Yes, in theory. There are a lot of variables in fluid systems, though...
Posted by: 70_914 May 19 2010, 08:31 AM
GO VIKINGS! WWU is in Bellingham and has an outstanding engineering program... didn't figure everybody would get that reference.
Posted by: realred914 May 19 2010, 08:35 AM
QUOTE(70_914 @ May 19 2010, 07:24 AM)

Sorry to hijack the thread discussing basic thermodynamics but I will make a couple real world examples- since now I have agreement that fluid speed is the only variable in a closed system with a fixed cooler.
Example A: You are a college student. You are going to WWU taking plastics engineering with a double minor in physics and chemistry. You want to throw a killer party, and decide that running copper coils throgh a bucket of ice water is a good way to cool your beer as it exits a keg. The ice water is a constant temperature, the keg beer is also a constant temperature. You have a pressure valve to control flow through the copper coils. Your beer won't be the same cold temperature if you crank the pressure up to 50 psi and blast it through the coils, it will be colder if it goes through the coils a little slower and allows the ice water to remove more of the heat from the beer.
Example B: You are a fry cook and want to leave work early. You have a large griddle that needs to be cold before you can go home. You also have a piece of ice that is the exact width of this griddle. You can take the ice and rush it across the surface of the griddle at 2 inches per second and have over half the ice cube left at the other end- inefficient because the ice was not able to remove all the heat from the griddle and did not do as much work as it could of, or you could move the ice across the griddle at 1 inch per second and at the very last moment the ice is completely melted- very efficient because the ice was able to do all the work possible.
Both examples are abstract, neither example shows specifically a type IV engine with a pass through cooler, both examples show thermodynamics. Laws of physics don't change on a whim.
The overall heat transfer coefficient for a wall or heat exchanger can be calculated as:
1 / U A = 1 / h1 A1 + dxw / k A + 1 / h2 A2 (1)
where
U = the overall heat transfer coefficient (W/m2K)
A = the contact area for each fluid side (m2)
k = the thermal conductivity of the material (W/mK)
h = the individual convection heat transfer coefficient for each fluid (W/m2K)
dxw = the wall thickness (m)
The thermal conductivity - k - for some typical materials:
•Polypropylene PP - 0.12 W/mK
•Stainless steel - 21 W/mK
•Aluminum - 221 W/mK
The convection heat transfer coefficient - h - depends on
•the type of fluid - gas or liquid
the flow properties such as velocity
•other flow and temperature dependent properties
Heat transfer coefficient for some common fluids:
•Air - 10 to 100 W/m2K
•Water - 500 to 10 000 W/m2K
if you run the beer slow enough, it will some get to near the temp of the ice water. however your party friends may get a little upset that teh flow rate is just a trickle. they want their mugs filled fast. the engine has a requierment for pressure to keep up lubrication. you drop the oil presusre to slow up the time in the cooler and you lose the important pressure needed to keep up luibrication of the bearings.
also keep in mind the oil is in a closed loop system. the faster it gets thru the cooler, the sooner it can make the return trip and be cooled again. Lets look at flow rate not speed or time in the cooler on any single pass of a molecule of oil. the faster any molecule of oil makes it thru the cooler, the faster it will be back for a second round thru the cooler.
the argument about speed thru the cooler is not taking this into account. The oil will return, it is not a one pass system like the hypothetical beer keg.
Posted by: Chris Hamilton May 19 2010, 12:46 PM
If you wanted Example A to apply to this situation you would try to determine how much ice you could melt with the beer, not how much beer you could cool with the ice.
You seem to have the concepts in your mind but you are misapplying them pretty badly here.
realred914 is correct here in pointing out that this is a closed system and we are dealing with an energy transfer problem. We are trying to transfer the most energy from the motor to the oil cooler in the smallest time possible.
The Bottom Line: More flow through his cooler is going to cool the motor more. You can try to bring up as much misapplied theory here as you want, but the bottom line is that oil pressure is not going to overheat his 914.
Posted by: Racer Chris May 19 2010, 04:10 PM
Higher pressure from a high volume pump isn't necessarily going to increase the flow rate through the cooler.
At a certain point, the primary pressure relief valve will open and allow some oil to bypass the cooler. The flow rate through the cooler is therefore regulated to a large degree by the pressure relief valve.
The viscosity of the oil changes with temperature. When the oil is very hot it won't develop as much pressure and will flow more quickly through narrow passages such as in the cooler and between the bearings and crank.
Even though it is flowing faster and has less time to dump heat, the delta T is greater thereby increasing the rate of thermal transfer.
Posted by: Racer Chris May 19 2010, 04:12 PM
QUOTE(Chris Hamilton @ May 19 2010, 02:46 PM)

but the bottom line is that oil pressure is not going to overheat his 914.
unless the pressure could be so high that added friction causes the oil to heat up more.
Posted by: 70_914 May 19 2010, 04:47 PM
QUOTE(Racer Chris @ May 19 2010, 03:12 PM)

QUOTE(Chris Hamilton @ May 19 2010, 02:46 PM)

but the bottom line is that oil pressure is not going to overheat his 914.
unless the pressure could be so high that added friction causes the oil to heat up more.

Or unless the cooler is not able to remove enough heat from the oil as it passes through...
Or unless there is a bypass somewhere in his oiling system (oil thermostat, bypass spring, pressure causing the oil filter case to flex and bypass internally...)
Or unless.... I don't care anymore.
My engines don't overheat. I am done with this thread- it is turning into an "I am right, you are an idiot and you can't prove otherwise" thread.
Posted by: Vacca Rabite May 20 2010, 09:02 AM
So, coming back down from high science to backyard engineering...
For those of you that added oil coolers, how did you route the oil from the case to the cooler?
Did you use a spin on type adapter and relocate the oil filter? Or did you pull the motor and tap the galley plugs? If I use a cooler, I'd like to use a spin on type adapter, but don't know if thats a good or bad idea.
Zach
Posted by: jhadler May 20 2010, 09:29 AM
QUOTE(Vacca Rabite @ May 20 2010, 07:02 AM)

So, coming back down from high science to backyard engineering...
For those of you that added oil coolers, how did you route the oil from the case to the cooler?
Did you use a spin on type adapter and relocate the oil filter? Or did you pull the motor and tap the galley plugs? If I use a cooler, I'd like to use a spin on type adapter, but don't know if thats a good or bad idea.
Zach
The first iteration of aux cooling I did used a spin on adapter with a built in thermostat. While it was easy, and convenient to install. Service was a bit of a PITA, as the filter then came very close to a bunch of other things under the car, so it added effort to every oil change. It worked, I guess... But the oil cooler was not optimally installed, hanging on the engine lid. Now the motor is out and getting re-done, I'll be tapping the plugs, relocating the filter, and hopefully (if time and money permit) installing a cooler up in front.
-Josh2
Posted by: type11969 May 20 2010, 10:04 AM
Spin on type, drops the filter about an inch, no clearance problems. If anything it makes the filter a bit easier to remove when changing the oil.
-Chris
Posted by: realred914 May 20 2010, 10:08 AM
QUOTE(type11969 @ May 20 2010, 09:04 AM)

Spin on type, drops the filter about an inch, no clearance problems. If anything it makes the filter a bit easier to remove when changing the oil.
-Chris
You can buy a shorter filter also, that will help.
Posted by: sean_v8_914 May 20 2010, 10:22 AM
did you check, make sure your fan did not eat something?
Posted by: yeahmag May 20 2010, 10:26 AM
I had that happen on my 2276 Type I once... Good point! Took me quite a while to figure it out.
Posted by: realred914 May 20 2010, 10:40 AM
hence you put on a fan screen taken from a late model VW bus. fits right on the 914 fan housing
Powered by Invision Power Board (http://www.invisionboard.com)
© Invision Power Services (http://www.invisionpower.com)