Printable Version of Topic
914World.com _ 914World Garage _ Trunk pan replacement progress.
Posted by: Bartlett 914 Mar 25 2007, 04:15 PM
QUOTE(LowGT @ Mar 25 2007, 01:21 PM)

Finally got to do some work on the V8 car I picked up, starting with patching the front floor pan to help air-flow.
Before, you can see the A/C hole under the muffler. Why would air go through the radiator when it could just go out the hole in the floor?

Trimmed up the replacement pan and the floor in the car. The opening was cut with 90 degree corners, so the metal was split about 2 inches up the corners.


Now the pan is tacked in, it's not lined up perfect but this will never be a concourse car. Not too bad for my first time doing any kind of body work. I do need to go back in with my wire wheel and clean stuff up. I keep melting tar and stinking myself out of the garage. Live and let learn I guess.

Dan
I have been working on the opposite end of my car doing much the same. I would suggest cleaning a lot more around the welds on both sides better. It will weld nicer with a lot less smoke. Your fit looks good.
Posted by: LowGT Mar 25 2007, 05:16 PM
QUOTE(Bartlett 914 @ Mar 25 2007, 05:15 PM)

I have been working on the opposite end of my car doing much the same. I would suggest cleaning a lot more around the welds on both sides better. It will weld nicer with a lot less smoke. Your fit looks good.
Yea, I agree. I tried to wire wheel it before but the metal is so flexible it wasn't working. I figured once I tac the pan in it should flex a lot less.
It is a much slower and tedious process than I originally expected.
Posted by: watsonrx13 Mar 25 2007, 05:18 PM
Here's how I replaced the front floor pan, http://www.tampabay914.com/7491420050327.html..
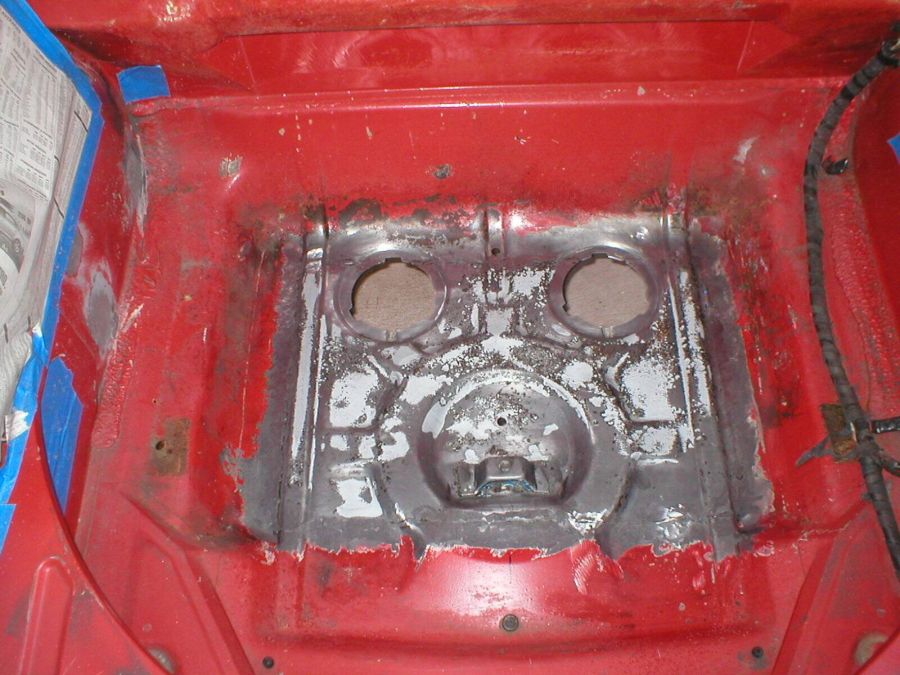
-- Rob
Posted by: LowGT Mar 25 2007, 06:16 PM
Thanks for the link, I need to get some copper. I think that will help me a lot. Also, I have some larger gaps in my panel. What kind of gaps can I weld?
Posted by: burton73 Mar 25 2007, 08:53 PM
I guessing that you have a big intake hole on the front bumper and the area under that in the body? No pictures in your blog on the front of car. Some people have the fan pulling air. Did I miss something?
Bob
Posted by: LowGT Mar 25 2007, 09:57 PM
QUOTE(burton73 @ Mar 25 2007, 09:53 PM)

I guessing that you have a big intake hole on the front bumper and the area under that in the body? No pictures in your blog on the front of car. Some people have the fan pulling air. Did I miss something?
Bob
Yes, mine is the typical air through hole in front bumper/body and exit through the wheel wells. And then I had a AC hole in the floor thrown in there as well.
Posted by: burton73 Mar 25 2007, 11:03 PM
The A/C hole was huge
Bob
Posted by: So.Cal.914 Mar 26 2007, 02:16 AM
I just have to ask...Whats with the muffler up front?
Thinking about it for a minute I guess I could hook it up to my wife when she
starts to bitch that I am driving to fast.
Work looks good.
Posted by: fitsbain Mar 26 2007, 08:55 AM
Guess this means you got the parts.
Glad to seem going to good use.
Now if only I could sell the rest of the car.
Posted by: LowGT Mar 26 2007, 11:43 AM
QUOTE(fitsbain @ Mar 26 2007, 09:55 AM)

Guess this means you got the parts.
Yup, I meant to email you but I forgot. I picked them up the day after you called me. Everything looks great, thanks again!
Dan
Posted by: LowGT Mar 26 2007, 11:45 AM
QUOTE(So.Cal.914 @ Mar 26 2007, 03:16 AM)

I just have to ask...Whats with the muffler up front?
It's the fad, engine it the back and the exhaust out front.
That's just where it was when I bought it, they are old pics from when I got the car home.
Posted by: URY914 Mar 26 2007, 12:16 PM
QUOTE(LowGT @ Mar 26 2007, 09:45 AM)

QUOTE(So.Cal.914 @ Mar 26 2007, 03:16 AM)

I just have to ask...Whats with the muffler up front?
It's the fad, engine it the back and the exhaust out front.
That's just where it was when I bought it, they are old pics from when I got the car home.
God, I'm glad someone asked about that muffler. I thought I was the only one that saw it.
Posted by: LowGT Mar 28 2007, 09:20 PM
This whole deal has made me realize that I suck at welding more than I thought I did, and the cuts I made aren't as tight as I need them to be.
Where there is minimal gap, I can tac/weld just fine. Where there is a slight gap, I can't weld it together worth a shit.
Posted by: Bartlett 914 Mar 29 2007, 01:16 PM
QUOTE(LowGT @ Mar 28 2007, 07:20 PM)

This whole deal has made me realize that I suck at welding more than I thought I did, and the cuts I made aren't as tight as I need them to be.
Where there is minimal gap, I can tac/weld just fine. Where there is a slight gap, I can't weld it together worth a shit.

First.. Clean metal welds properly. Dirty metal will pop and splatter. This will make the welding job a PITA.
Second.. I am told you can back up the gap with copper to help bridge the gap. Use a flat copper bar or smash a copper pipe flat. Place this behind the weld. Do small welds. Multiple tacks.
Third..Don't give up. You can do it/
Posted by: tdgray Mar 29 2007, 02:03 PM
QUOTE(Bartlett 914 @ Mar 29 2007, 03:16 PM)

QUOTE(LowGT @ Mar 28 2007, 07:20 PM)

This whole deal has made me realize that I suck at welding more than I thought I did, and the cuts I made aren't as tight as I need them to be.
Where there is minimal gap, I can tac/weld just fine. Where there is a slight gap, I can't weld it together worth a shit.

First.. Clean metal welds properly. Dirty metal will pop and splatter. This will make the welding job a PITA.
Second.. I am told you can back up the gap with copper to help bridge the gap. Use a flat copper bar or smash a copper pipe flat. Place this behind the weld. Do small welds. Multiple tacks.
Third..Don't give up. You can do it/
Absolutely... get some copper. I think Eastwood or somebody sells a copper block for this purpose.
and I hope you are mig welding. You need the shielding gas to make nice strong welds to bridge those gaps.
Posted by: wbergtho Mar 29 2007, 08:34 PM
The copper block is a good idea and try to use an angle when welding as well as moving the tip (stitching) a bit. If you shoot the wire straight into the gap...it just blows right on through. This is why you should back it up with copper. Once you practice and get more proficient...you'll be able to fill in substantial gaps. Your fitment looks well within any normal welder's range. In fact it looks pretty damn good. Get a 90 degree angle die grinder and a pile of 80 grit pads and clean up any "ugly welding" by simply grinding away the high spots. If you get real anal, you can sometimes have a hard time telling where you were welding. Keep up the good work and don't give up. You will become as good as you want to be.
Posted by: jd74914 Mar 29 2007, 09:22 PM
QUOTE(tdgray @ Mar 29 2007, 04:03 PM)

QUOTE(Bartlett 914 @ Mar 29 2007, 03:16 PM)

QUOTE(LowGT @ Mar 28 2007, 07:20 PM)

This whole deal has made me realize that I suck at welding more than I thought I did, and the cuts I made aren't as tight as I need them to be.
Where there is minimal gap, I can tac/weld just fine. Where there is a slight gap, I can't weld it together worth a shit.

First.. Clean metal welds properly. Dirty metal will pop and splatter. This will make the welding job a PITA.
Second.. I am told you can back up the gap with copper to help bridge the gap. Use a flat copper bar or smash a copper pipe flat. Place this behind the weld. Do small welds. Multiple tacks.
Third..Don't give up. You can do it/
Absolutely... get some copper. I think Eastwood or somebody sells a copper block for this purpose.
and I hope you are mig welding. You need the shielding gas to make nice strong welds to bridge those gaps.
Just get a copper pipe and hammer it flat, then you have a heat sink with a handle so you can hold it with your hand further from the welding.
Posted by: CoolAirVw Mar 29 2007, 09:33 PM
QUOTE(jd74914 @ Mar 29 2007, 10:22 PM)

Just get a copper pipe and hammer it flat, then you have a heat sink with a handle so you can hold it with your hand further from the welding.
Like this.
Posted by: LowGT Mar 29 2007, 09:54 PM
I did buy a copper pipe yesterday, but I didn't hammer it flat, I'll try that.
Unfortunately I am using flux core right now, but I'm looking into buying the MIG conversion.
Posted by: jd74914 Mar 29 2007, 10:31 PM
I wouldn't use pipe with lead soldier on it. It can do bad things to your health. You want to hammer it flat so it has the greatest possible area touching the work surface.
You can get good welds with flux core, there is just a little more spatter. You really don't need MIG. Your biggest problem is the amount of rust, paint and other crap on the two pieces. Once you take that off it will be cake to weld.
Posted by: CoolAirVw Apr 1 2007, 08:12 PM
QUOTE(LowGT @ Mar 29 2007, 10:54 PM)

I did buy a copper pipe yesterday, but I didn't hammer it flat, I'll try that.
Unfortunately I am using flux core right now, but I'm looking into buying the MIG conversion.
I'm also using a flux core welder right now. Welding with flux core is ugly and hard. I have a welder coming on loan that I had to buy the bottle for. We got a small bottle and it cost 130.00 here, but that doesn't include the regulator. The loaner welder has all that. I need some "EZ grind" wire also. The stuff I'm using now is hard!
Here's a link to some rust I'm repairing on my Turbo Diesel Jetta. Getting some good practice to repair 914's! Propane torch to melt tar, wire wheel and then patch in floorboard.
http://www.vwdieselparts.com/forum/viewtopic.php?p=37216#37216
Powered by Invision Power Board (http://www.invisionboard.com)
© Invision Power Services (http://www.invisionpower.com)