drive-ability
Oct 20 2009, 01:51 PM
I'm replacing my Renegade/Chrysler BB pump, since it locked up last night. I didn't here any noise at all ? The engine does make a bit of noise but you would think there would be some warning. Nope ! Maybe something broke off and jammed up the impeller etc. The pump just locked up and melted the drive belt.
My question is I have been running a standard pump and decided to get a high volume unit. My assumption is the quality is better than my last one and with A/C it might perform better moving more water. I guess with more pressure comes it own set of issues. One thought is the belt was too tight, and that's a good bet.
I'm not running a Thermostat but am running a minor restriction in the thermostat housing, which I think I should remove.. ?
Any one have any input here.
Bruce Hinds
Oct 20 2009, 02:59 PM
I had some of the same issues, and found that there is something called a High flow thermostat. Even though Hi Flow is not neccessarily what we need. There are some holes around the thermostat diaphram that allow coolant to flow slowly when closed and a higher volume when open. With the radiator so far away it helps to keep the coolant flowing for better cooling than if the coolant has to start and stop. It seems without the thermostat the stuff flows through the radiator too fast and it doesn't have a chance to cool down. I'm not sure why it flow so fast with out the restriction, it may by the MOPAR pump I got with my renegade kit. It's and easy solution and I bet you'll see a big difference.
Let me know how it works.
B
JRust
Oct 20 2009, 03:11 PM
Are you going with another belt driven water pump? Meziere make a great electric pump. Taking the belt off the pump is easier on your motor. Yes it takes a little more juice from your electrical system. Most v8 conversions have a good enough alternator that isn't a problem. More horsepowere is always a good things too

. I am doing this on my buick 215 v8. Although the major reason is my water pump comes into the cab to much
drive-ability
Oct 20 2009, 03:33 PM
people talk about the speed the water goes through the radiator and how it might be a factor, who knows its sounds reasonable to me, but I am running a double pass radiator and that may effect the concept.?? I did run a thermostat but you need a good bypass system or as I did BEND all the impeller blades flat if you don't wait to rev the engine.... LOL
I did look at a electric pump and passed because I have more trust in the belt driven units. Having said that I am replacing a failed one at this time LOL. I would go there if I was running a 215 just for the reason stated.
This might be a good time to set up a by-pass system. I have seen some pictures but don't have a real good Idea yet.. I'll let you know how the higher volume pump works...
dakotaewing
Oct 20 2009, 04:05 PM
In regard to electric water pumps, it appears that Davies Craig actually makes the the best, most controlable unit out there...
It pumps about 115l per minute/ made in AUS -
http://www.daviescraig.com.au/http://www.hrpworld.com/index.cfm?form_pro...;action=productThis is what I am planning on using in my car -
drive-ability
Oct 20 2009, 04:24 PM
I have seen that electric pump and do like the overall setup, I would need to see it work with this application first.. I just wonder if the distance equals weight or drag on the pumps motor, and since I drive my car allot its concerns me. I would love to here how things work for you!
I removed my pump and the vanes are trashed, bent and broken off ! This unit has been in there for 2 or 3 years. My guess and its a guess at this point for sure is the blades (stamped not cast ) slowly bent back until they hit the housing. Surely a other thing could be there's a greater restriction in flow somewhere. At this point I don't know...
SLITS
Oct 20 2009, 06:18 PM
The speed of flow thru the radiator greatly effects cooling. To fast ... no cooling; to slow overheating. There is an optimum flow rate, hence the use of blanking sleeves, thermostats, plates with holes drilled in them, etc.
In your other thread on the subject, I gave you the opinion of a man with 35 years experience diagnosing/rebuilding water pumps as to what went wrong with the pump.
burton73
Oct 20 2009, 07:38 PM
I went over this with Rod Simpson at his shop the other day. I wanted to go to an electric water pump on my V8 car I am building and he had a few things to say. One thing was Renegade copied his design on there water pump and Rod took the main part from a design from an older Chrysler unit that had the widest bearings. These units Rod says live for 70,000 miles on his customers cars.
I know of Simpson conversions because I had one car that was a combo of Kennedy and his parts. This was over 30 years ago. There are a number of ways to do these V8 conversions. His house shop is very close to my home.
On the electric pump, he said that an electric pump couldn’t put out a strong enough pump to pump the water that far with out burning out. It is to far to the front of the car and then back to the engine. He said the electric pumps are designed for front engine cars and front mounted radiators. He said it would take to much HP to pump that amount of backpressure. At least I found this out before I got that far. He said the pumps made do not have that amount of power and only a mechanical pump will work.
Bob
drive-ability
Oct 20 2009, 09:42 PM
QUOTE(SLITS @ Oct 20 2009, 05:18 PM)

The speed of flow thru the radiator greatly effects cooling. To fast ... no cooling; to slow overheating. There is an optimum flow rate, hence the use of blanking sleeves, thermostats, plates with holes drilled in them, etc.
In your other thread on the subject, I gave you the opinion of a man with 35 years experience diagnosing/rebuilding water pumps as to what went wrong with the pump.
Hey SLITS I didn't mean to say flow wasn't a major factor, but it may have looked that way. I discounted it because I don't have a cooling issue to date.

I looked back and didn't find what you referenced above, could you fill me in.
I know people run electric pumps and seem to like them but most V8 guys use there cars as weekend drivers. Short runs here and there mostly, I on the other hand will drive my car long distances sometimes 1,000 miles one way. This is where I think the electric pumps might be pushed to failure.
charliew
Oct 20 2009, 09:54 PM
It's sorta like when you use a paint spray gun on a 50 ft air hose, you gotta crank the pressure up to about 80 psi to get the gun to atomize the paint like it would with a 20 ft hose. The other option is to use bigger water lines so the restriction is less and that would reduce the effort at the pump. try it without a thermostat and if the water is moving too fast start using a restrictor till it cools. Then you will know whether or not you can use a thermostat. If the thermostat was closed or had too much restriction a stamped impeller would probably bend at high rpm.
I have a 63 jeep j200 truck with a sbc. When I was trying to get it to run cooler I tried a flowcooler waterpump and eventually blew the tank off the radiator. The flowcooler waterpump basically has a plate on the back side of the impeller to move more water through the pump.
andys
Oct 21 2009, 02:19 PM
Meziere makes a real nice looking mechanical (belt driven) pump should you be apprehensive with using the electric one. Available from Summit:
http://www.summitracing.com/search/Part-Ty...iere&page=2Andys
computers4kids
Oct 21 2009, 06:20 PM
TC just lost his Renegade "chrysler" pump the same way last month...the vanes were toast. I sure would like to better understand this all a bit better...perhaps avoid the the same end with mine. I'll be looking forward to reading more.
drive-ability
Oct 21 2009, 07:13 PM
I just got my new pump from Edelbrock, well it wont fit. I guess the High output pumps are a little bigger. The impeller circumference is larger and likely the depth is as well. I think the stamped units stress over time, bend and blow up !!! I'm going to look for a unit which has a cast impeller. P.S the Edelbrock impeller was a cast unit... Hummmmm.
SLITS
Oct 21 2009, 08:40 PM
I don't remember when you started the last thread. You posted images of the water pump. I'll ask if he remembers the image I showed him. I do remember the discussion centered around cavitation.
I can also see if we have the Chrysler pumps as a core or if we have any rebuilt. I can get them rebuilt if necessary. I don't remember asking about vanes as to whether they came in cast iron. I do remember that they are big bearing / small bearing pumps. I had also posted the engine size and years that they were used on.
I'll give it a shot.
computers4kids
Oct 21 2009, 09:26 PM
QUOTE(jmmotorsports @ May 30 2008, 07:51 AM)

The gasket should be a Fel-Pro 11730
Jerry
QUOTE(plymouth37 @ May 29 2008, 10:50 PM)

If I remember correctly the gasket you need is off of a 70's big block V-8 Chrysler water pump. That should at least get you close.
Maybe this will help a bit running the pump down.
SLITS
Oct 22 2009, 03:12 PM
Here are your answers:
1.) the image I showed him he agreed that the impeller came apart, but the cibearing did not fail.
2.) The pump used is a Lester 1352, small bearing, A/C pump, with 6 fins. In the manufacture of the impeller, there is a small round hole at the base of the impeller that is a weak point. This pump was used on 1961 - 1964 Chrysler 361 CID engines, the 1959 - '1971 383 CID engines, 1963 - 1964 426 CID engines and 1966 - 1971 440 CID engines. Impeller diameter is 3.500". This unit moves water faster, but with less volume.
3.) The alternate pump is a Lester 1317. It was used on NON-A/C vehicles. It has an 8 fin impeller. Same engine, same years, but NON-A/C vehicles. It moves water slower, but a higher volume. Diameter of the impeller is 4.185".
4.) The next series came due to the use of the engines in Motor Homes and they would overheat on climbing hills. This is the Lester 1519. It featured an 8 fin impeller with the big bearing housing. Generally fitted to the '74 - '78 400 / 440 CID engines. Slow water / high volume. This one may be the one Edelbrock copied.
Below are images of the 1352 with CAST IRON impeller ... they do exist.
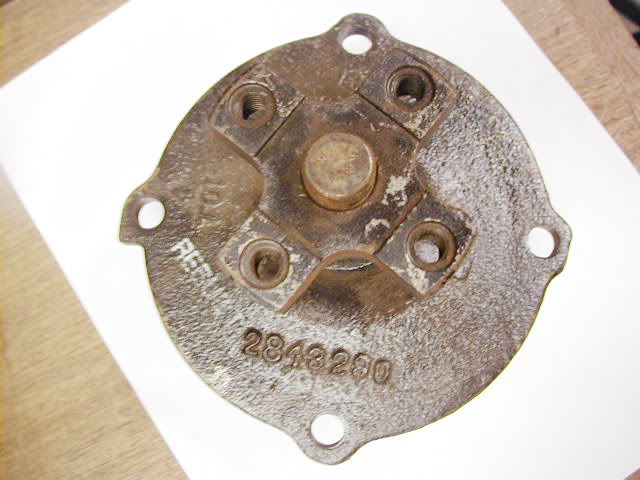
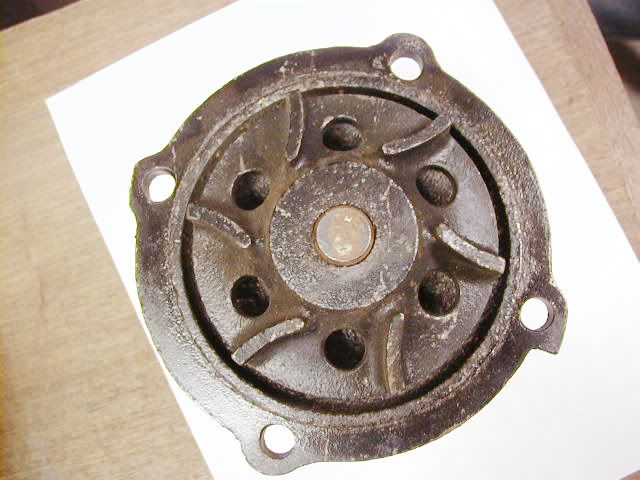
I can obtain and supply these pumps if you so desire.
Good luck!
Bruce Hinds
Oct 22 2009, 04:04 PM
Thanks for the Interesting thread on the water pump situation. I remember replacing my pmup years ago, other things had grounded the car, but since I'd gotten it going in it's second life, there were cooling issues.
Hopefully I'll get this thing resurected again for it's 3rd life and I'll double check the pump to see if I got one of the wrong ones.
I'd long thought about going with an electric pump and would be curious to know if anyother renegades have done that.
B
SLITS
Oct 22 2009, 06:20 PM
Renegade tried an electric pump on at least one 914 conversion that I know of. The electrics were hell to figure out due to the harness they were using. I believe they finally figured it out. I do believe this was their first attempt at an electric one. Better information should come from them.
Years ago I remember an SCCA racer than burned up an engine 'cause he forgot to flip the switch for the pump. Whether that makes a mechanically driven one better or not is up to the individual.
Oh, and Renegade confirmed that the motor home pump / Edelbrock pump will not fit the housing.
charliew
Oct 22 2009, 07:02 PM
While you are studying you might look at the reason chev went to reverse flow cooling. That seems to be easy on the 914 application. I must have tried 6 different crank to waterpump pulleys to try and improve cooling on the jeep. With ac and the small grill opening on the early gladiator it was hard to get better than 210-220-230 on a 100 degree day with the ac on.
burton73
Oct 23 2009, 05:32 PM
I would look to the quality of the machine work of the casting of the water pump body. I just spoke to Rod Simpson on this and said he has had only one pump come back in over 30 years after a guy ran his car without water. If the machining is too close the impeller will get too hot and it can bend and jam up. If is to far away it will not pump right because the clearances are wrong.
In Orange County the thermostat should make no difference in this happening.
I never had this problem with my V8 before 30 years ago
Bob
computers4kids
Oct 23 2009, 10:41 PM
ouch
drive-ability
Oct 24 2009, 12:11 AM
QUOTE(computers4kids @ Oct 23 2009, 09:41 PM)

ouch
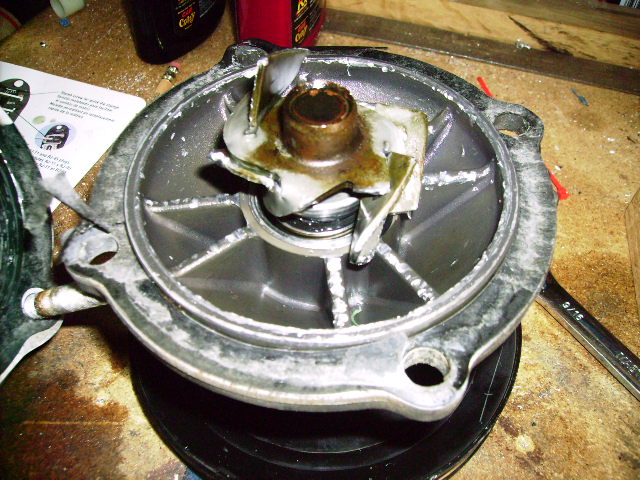
computer4Kids,
That looks just like my pump, I'm really not too worried about the situation. I went out and got a pump that uses 8 blades. Looking at its stamped design using smaller paddles my thoughts are it will handle the pressure better. I'm no expert on the subject and would like a unit with a cast impeller so I will be looking into the pump our expert SLITS pictured as a back up..
Its sure a odd way for a pump to fail but I think it goes back to the weight of the water volume acting upon the impeller blades. If it were from a single hydro event my thoughts are a hose would blow or my recovery bottle would show signs of action. Sounds reasonable to me but what the

do I know !
computers4kids
Oct 24 2009, 08:42 AM
I would have dismissed this whole water pump incident had it not also just rececently happened to my friend Tony as well.
Tony's Thread You guys should put your heads together and see what you have in common. Sorry you had to go through all this as well, but at least perhaps we can learn from it. I sure like the idea of the cast iron model. It's interesting that others have had never had problems. I know Tony has his water lines run through the longs. Other than that our systems are pretty all similar
SLITS
Oct 24 2009, 10:39 AM
There is nothing to say other than there could have been a run of defective impellers .... it wouldn't be the first time outsourced material from our friends to the East or South didn't screw up or substituted an inferior material. Quality Control is not one of their strongpoints.
All it would take is one fin to break off and the carnage would begin. Our water pump expert insisted that it appeared there was a foreign object in the system that caused the failure or something along the lines stated above as he had not seen that happen.
At one time, rebuilders would not accept "aftermarket" cores for rebuilding due to the poor metallurgy and castings.
Draw your own conclusions ... They supply what we demand ... Cheap.
drive-ability
Oct 27 2009, 09:10 PM
I have had some time to drive the car and have found this 8 blade pump isn't cooling the engine as well at idle speed. At this point I don't know why, there's a restrictor in the thermostat housing and I will be removing it tomorrow. Lets see if anything changes.
SLITS
Oct 27 2009, 09:15 PM
8 vane moves water slower .... low rpm even slower ..... longer residence time in the engine.
Could be incorrect impeller depth for the housing.
Where are you measuring the temp?
drive-ability
Oct 27 2009, 09:49 PM
QUOTE(SLITS @ Oct 27 2009, 08:15 PM)

8 vane moves water slower .... low rpm even slower ..... longer residence time in the engine.
Could be incorrect impeller depth for the housing.
Where are you measuring the temp?
I'm using a spot at the intake manifold, a few inches from the thermostat housing.
![popcorn[1].gif](http://www.914world.com/bbs2/style_emoticons/default/popcorn[1].gif)
I take comfort in knowing you know what your talking about when commenting about the 8 blade pumps. LOL
drive-ability
Oct 28 2009, 11:02 PM
I have found the 6 vane pumps (Chrysler 440) work better in my cooling system, but I am having trouble finding one. The two I have looked at were both 8 vane units. Anyone here able to help out.
I have posted this question in a Chrysler forum as well
burton73
Oct 29 2009, 02:06 PM
QUOTE(drive-ability @ Oct 28 2009, 10:02 PM)

I have found the 6 vane pumps (Chrysler 440) work better in my cooling system, but I am having trouble finding one. The two I have looked at were both 8 vane units. Anyone here able to help out.
I have posted this question in a Chrysler forum as well

Call Rod Simpson Hybrids at 310 826 3304 and ask Rod if he will sell you one.
Bob
SLITS
Oct 29 2009, 02:24 PM
How many do you want?
Stamped steel
Cast iron.
Aluminium body
Cast iron body
drive-ability
Oct 29 2009, 04:47 PM
QUOTE(SLITS @ Oct 29 2009, 01:24 PM)

How many do you want?
Stamped steel
Cast iron.
Aluminum body
Cast iron body
I used a aluminum 6 blade stamped steel unit and it worked well until it blew apart.
6 blade stamped & Cast impeller, do they flow different ?
Thanks Bob for the phone number
I wonder if I could use the 6 blade stamped unit and weld on a anti-cavitation plate ?
Can't see how that would be hard, but would it dumb down the flow ?
SLITS
Oct 29 2009, 06:22 PM
Ok, last shot at this subject.
The man I am talking to worked with Rod Simpson on his designs and also Weiand on their designs.
One of the problems of the pumps was that they would cavitate on transition from idle to motion (starting and stopping in traffic). This would destroy the seal, but not the impeller.
Rod Simpson's problem was the diameter of the lines running to and from the radiator. Overheating was a problem due to pressure and diameter needed to push the water up and back about 6' each way and the type of radiator used. He couldn't remember what diameter line was finally finalized (work was done in the 80's)
Another problem that can occur is the RPM of the water pump which is controlled by drive pulley size. You spin a pump to fast and it will cavitate. Much work has been done on pulley size to optimize impeller speed.
Now back to the water pump itself. Cast iron or stamped steel should not make any great difference in flow, but the cast iron blades are somewhat cupped which enchances water capture (just think boat propeller). We said that the weak point on the stamped steel was the notch at the base of the blade. Some manufacturers either welded a plate on top of the fins or at least a donut to stabilize the fins. That's one fix.
Also, the fins (or the donut / plate) should be no farther away from the back housing than 1/32" (0.031"). Father away will create cavitation and lessen pumping capability.
That's about it ...... carry on .......................
Bruce Hinds
Oct 29 2009, 07:00 PM
Sorry for the diversion, but has anyone used an electric pump on a thermostat?
drive-ability
Oct 29 2009, 07:07 PM

Thank You, I now understand there was allot of R&D done a long time ago. Surely there's more going on here then you might expect. I think I can use this pump for a while because it cooler here and I'm not running over 200 at any time. I would like to get the 6 blade unit installed soon. Thanks
svsv
Oct 29 2009, 09:30 PM
QUOTE(drive-ability @ Oct 29 2009, 05:07 PM)


Thank You, I now understand there was allot of R&D done a long time ago. Surely there's more going on here then you might expect. I think I can use this pump for a while because it cooler here and I'm not running over 200 at any time. I would like to get the 6 blade unit installed soon. Thanks

This might be a dead topic, but cooling everything from hypo BB's to hyped up 4cyls i do know. First thing is you always run a thermostat! and you never run a pump with stamped steel impellers, unless it's to the parts store to get a cast one. magnum 440's 68 through 71 have the pump your looking for buy them from mopar parts. As far as electric pumps, your on the money with longjevity issues they are made for drag racing or last resorts.Your moving water along way through a restricted enviorment. Large as possable lines are required to reduce your pressure. Similar is rear mounted rad's on mud boggers 1.5" lines are typical on thoes installs and work fine for up to around 600hp. Good luck and I hope I was of some help.
charliew
Oct 29 2009, 10:28 PM
One thing I remember is that a temp sensor in the intake manifold is showing about 10-15 degrees cooler than a temp sender in the head. The head is a lot better if it really is marginal on cooling. The intake temp will make you feel better though.
burton73
Oct 30 2009, 08:55 PM
QUOTE(SLITS @ Oct 29 2009, 05:22 PM)

Ok, last shot at this subject.
The man I am talking to worked with Rod Simpson on his designs and also Weiand on their designs.
One of the problems of the pumps was that they would cavitate on transition from idle to motion (starting and stopping in traffic). This would destroy the seal, but not the impeller.
Rod Simpson's problem was the diameter of the lines running to and from the radiator. Overheating was a problem due to pressure and diameter needed to push the water up and back about 6' each way and the type of radiator used. He couldn't remember what diameter line was finally finalized (work was done in the 80's)
Another problem that can occur is the RPM of the water pump which is controlled by drive pulley size. You spin a pump to fast and it will cavitate. Much work has been done on pulley size to optimize impeller speed.
Now back to the water pump itself. Cast iron or stamped steel should not make any great difference in flow, but the cast iron blades are somewhat cupped which enchances water capture (just think boat propeller). We said that the weak point on the stamped steel was the notch at the base of the blade. Some manufacturers either welded a plate on top of the fins or at least a donut to stabilize the fins. That's one fix.
Also, the fins (or the donut / plate) should be no farther away from the back housing than 1/32" (0.031"). Father away will create cavitation and lessen pumping capability.
That's about it ...... carry on .......................
I am sorry that I do not remember the size of the lines for sure that Rod runs in his cars but he did say that re runs a bigger line for the cool water and a thinner line for the hot water. He said the cooler water is thicker and needs the bigger diameter to carry it and the hot will work with the smaller. He did say this was a mater of cost. I think the Hot was ¾” ID and the COLD was 7/8” ID.
Bob
computers4kids
Oct 30 2009, 11:01 PM
QUOTE(burton73 @ Oct 30 2009, 07:55 PM)

QUOTE(SLITS @ Oct 29 2009, 05:22 PM)

Ok, last shot at this subject.
The man I am talking to worked with Rod Simpson on his designs and also Weiand on their designs.
One of the problems of the pumps was that they would cavitate on transition from idle to motion (starting and stopping in traffic). This would destroy the seal, but not the impeller.
Rod Simpson's problem was the diameter of the lines running to and from the radiator. Overheating was a problem due to pressure and diameter needed to push the water up and back about 6' each way and the type of radiator used. He couldn't remember what diameter line was finally finalized (work was done in the 80's)
Another problem that can occur is the RPM of the water pump which is controlled by drive pulley size. You spin a pump to fast and it will cavitate. Much work has been done on pulley size to optimize impeller speed.
Now back to the water pump itself. Cast iron or stamped steel should not make any great difference in flow, but the cast iron blades are somewhat cupped which enchances water capture (just think boat propeller). We said that the weak point on the stamped steel was the notch at the base of the blade. Some manufacturers either welded a plate on top of the fins or at least a donut to stabilize the fins. That's one fix.
Also, the fins (or the donut / plate) should be no farther away from the back housing than 1/32" (0.031"). Father away will create cavitation and lessen pumping capability.
That's about it ...... carry on .......................
I am sorry that I do not remember the size of the lines for sure that Rod runs in his cars but he did say that re runs a bigger line for the cool water and a thinner line for the hot water. He said the cooler water is thicker and needs the bigger diameter to carry it and the hot will work with the smaller. He did say this was a mater of cost. I think the Hot was ¾” ID and the COLD was 7/8” ID.
Bob
That's how my setup is...just followed the directions provided, but I always wondered why the different sizes...
drive-ability
Nov 8 2009, 10:14 PM
Was thinking about a smaller pulley, so looking around I found one. Its about
4 " inch pulley, it seems to be around 2" smaller than the one I'm using now(6"). I'm hoping it will push water at idle but not cause cavitation at higher rpm. It wasn't much to adapt to fit the pump and will be interesting to see how it preforms being 33% smaller.
charliew
Nov 9 2009, 10:45 AM
I'm not sure I follow the idea of a smaller hot water line and a bigger cold water line. Most things expand with heat and contract when cold except for water that freezes that I work with. I do have three fieros and they use at least 1.250 or 1.50 id lines to get to the front radiator. I noticed the small lines on some v8 conversions but I never planned on running any smaller than 1.250 id on my suby conversion. I think I've read where mercedes or some mfg uses a electric water pump controlled by a electric thermostat. This kinda reminds me of the guys that use to badmouth the airride stuff when we discuss the electric water pump. I know mezerie probably makes a good pump but the small lines may put to much restriction on the pumps.
I'm afraid the 33% may be too much change and the pressure will get really high at 6 or 7k. I never had any success changing the pulleys on sbc pumps.
You can gets lots of ideas here and there are probably lots of people that have fought cooling problems on hot rods. I would check on what the gt40, pantera, or the others do or any other how high performance mid engine cars work on their cooling.
Phoenix-MN
Nov 9 2009, 11:09 AM
QUOTE(charliew @ Nov 9 2009, 08:45 AM)

I'm not sure I follow the idea of a smaller hot water line and a bigger cold water line. Most things expand with heat and contract when cold except for water that freezes that I work with. I do have three fieros and they use at least 1.250 or 1.50 id lines to get to the front radiator. I noticed the small lines on some v8 conversions but I never planned on running any smaller than 1.250 id on my suby conversion. I think I've read where mercedes or some mfg uses a electric water pump controlled by a electric thermostat. This kinda reminds me of the guys that use to badmouth the airride stuff when we discuss the electric water pump. I know mezerie probably makes a good pump but the small lines may put to much restriction on the pumps.
I'm afraid the 33% may be too much change and the pressure will get really high at 6 or 7k. I never had any success changing the pulleys on sbc pumps.
You can gets lots of ideas here and there are probably lots of people that have fought cooling problems on hot rods. I would check on what the gt40, pantera, or the others do or any other how high performance mid engine cars work on their cooling.
I also had a Fiero for nearly 10 years and plumbed my 914 V6 just like a Fiero (ncluding using the filler neck on the intake manifold). I used 1.25" to the radiator and 1.5" return lines. I dont have many street miles on it yet but everything works well so far.
GS Guy
Nov 9 2009, 06:45 PM
Pretty sure the "Renegade way" is to use a 1" line from engine to radiator and 1-1/4" line from radiator back to the water pump. It was stated the smaller "hot" line was to speed up flow, reducing the return time. It also creates slightly more internal pressure inside the engine, I presume to help reduce chances of hot spots in the heads and promote heat transfer. Larger return line to the pump to give a nice lower pressure steady feed back into the pump and combined with the pump housing inlet shape - minimize cavitation. They claim this works exceptionally well (with their radiator of course!) in the hot 100F+ Nevada heat with the AC on....
I can imagine the 1" line would increase pressure against the water pump, but can't imagine any pressure increases causing that kind of pump damage? I would gather full warm-up would be the order of the day before any significant revving - else too much pressure is built up - maybe blowing off hoses?
Jeff
drive-ability
Nov 9 2009, 08:14 PM
I'm not sure of anything that's the reason for testing different ideas. I run my engine between idle and 4500 rpm 99% of the time and don't run a thermostat, the rev limiter is set at 5k so when I get off a AS* I'll install the new pulley and let you know how things turn out..
computers4kids
Nov 9 2009, 08:23 PM
QUOTE(drive-ability @ Nov 9 2009, 06:14 PM)

don't run a thermostat:
When I spoke to you at Slits place (Rustmeat) a couple years ago, I remember you saying that you didn't run a theromstat. I forget...why? I have a thermostat with three air bleed holes drilled in the housing per Renegade instructions. What would be the pros and cons of running a thermostat?
drive-ability
Nov 9 2009, 10:07 PM
QUOTE(computers4kids @ Nov 9 2009, 07:23 PM)

QUOTE(drive-ability @ Nov 9 2009, 06:14 PM)

don't run a thermostat:
When I spoke to you at Slits place (Rustmeat) a couple years ago, I remember you saying that you didn't run a theromstat. I forget...why? I have a thermostat with three air bleed holes drilled in the housing per Renegade instructions. What would be the pros and cons of running a thermostat?
I ran a thermostat as most V8 guys do with out any water pump bypass. Chevrolet stock setups have a water pump bypass to keep pressure from building up before the thermostat opens. About 2 years ago I revved the engine cold and my water pump impellers bent. From that point on I haven't run one. I'm sure its better for the engine to run one, its best to keep an engine at a tight coolant temp range, but for now I'm not.
I do understand about the holes drilled in the thermostat and that does work fine.
I have started working on using the holes in the heads where you can plum water to a tee to act as a bypass, just haven't done the work.. Once I do that I will run a thermostat. If its working for you by all means run one..
charliew
Nov 10 2009, 09:13 AM
The quicker a motor gets up to 200f the better it will burn off deposits and moisture in the oil and the clearances will work the way they are engineeded to work. The pistons need to expand, the oil needs to thin, and the castiron needs to stabilize to allow all the clearances to be where they willnot be on their tight side. 10w oil is very thick when it is cold.
Some people think the suby has a factory oil cooler but it's really a oil warmer.
drive-ability
Nov 19 2009, 10:43 PM
I thought I would share to the V8 guys what I ended up doing. I used the standard pulley, shelved the smaller one for now. I ordered a pump via ebay that has a cast impeller which states it moves 30% more water.
When I got the pump I found it wouldn't fit in the Renegade housing, so I spent a few hours porting the housing to accommodate the pump. I took time to grind out only what was needed for a tight fit. There was some shaping involved to accommodate the larger oval shaped impeller. I got it to spin free without the gasket installed, then boiled and froze the unit to make sure its not going to hit during expansion or contraction. I used clay as well to guide the porting process.
I've had the pump in operation for 2 days and the overall cooling system is working much better than the 8 paddle stamped steel unit. I installed a pressure gauge because at 3k I could feel the coolant hose expand a bit. The pressures are moving between 5 and 14 psi, that works for me. There's no dough this pump moves more water and thus cools better.
I am going to set up the smaller pulley in a week or so and see how the system responds to the different ratio.
computers4kids
Nov 20 2009, 09:17 AM
Thanks for keeping us informed on your progress. Do you have any pics of the porting, the part # for the cast pump and a source?
How did you add a pressure gauge...I would be very interested in what pressure my systems runs since it is your 'typical renegade setup.'
This is a "lo-fi" version of our main content. To view the full version with more information, formatting and images, please
click here.