r_towle
Mar 29 2010, 06:25 PM
Hi,
So, Mig welds are hardened and cannot be hammered to much.
Tig welds are really small but I believe they are also hardened so they cant be hammered.
Torch can be hammered.
I also want to weld aluminum.
Torch and Tig can both do this.
Torch has the added benefit of being a red hot wrench which comes in handy in the rust belts.
Torch can also cut...which is good.
So, which would you guys buy? Tig or Torch.
I already have mig...its just not good for sheet metal butt joints...I like smooth metal.
RIch
tat2dphreak
Mar 29 2010, 06:34 PM
tig for the welding, but a small torch is not expensive. for the heat wrench or cutting....
tig welds come out so much nicer than even MIG imo.
r_towle
Mar 29 2010, 06:38 PM
QUOTE(tat2dphreak @ Mar 29 2010, 08:34 PM)

tig for the welding, but a small torch is not expensive. for the heat wrench or cutting....
tig welds come out so much nicer than even MIG imo.
Just so I can gauge your opinion...
Do you know how to torch weld? both steel and aluminum?
Rich
tat2dphreak
Mar 29 2010, 06:41 PM
steel yes. and I've been around really good welders(which I'm not as skilled as) and I have seen them pull off nice welds with torch... but I've also seen them pull off even nicer welds on steel or aluminum with TIG... I'm not a good welder, but I know a few people that have been welders(by trade) forever...
r_towle
Mar 29 2010, 06:49 PM
I have also seen both.
The torch can be hammered flat and the Tig cannot without breaking...
Nor can mig.
For bodywork...real all metal bodywork, the torch seems to be the best.
I am questioning aluminum...
The thing is...most welders that could weld aluminum with a torch have retired...heliarc welding...tig welding has been around for a long time.
Rich
aircooledtechguy
Mar 29 2010, 06:50 PM
I LOVE my Lincoln Pro-TIG 185amp AC/DC TIG welder. It handles everything I need to do so far and can lay weld as well as your ability will allow.
OTOH, I was just given a spool gun to try out for aluminum welding that is used with my 110V MIG unit and argon bottle. I'm looking forward to trying that out as the guy I got it from said it makes aluminum welding easier than TIG with equally pretty results.
I have done limited aluminum welding with my torch set; I SUCK at it; yeah, parts are stuck together, but that's about it

I leave aluminum welding to my TIG machine.
76-914
Mar 29 2010, 07:55 PM
QUOTE(r_towle @ Mar 29 2010, 05:49 PM)

I have also seen both.
The torch can be hammered flat and the Tig cannot without breaking...
Nor can mig.
For bodywork...real all metal bodywork, the torch seems to be the best.
I am questioning aluminum...
The thing is...most welders that could weld aluminum with a torch have retired...heliarc welding...tig welding has been around for a long time.
Rich
Hey Rich, and I am NOT a welding God, but if you really want to gas weld aluminum the head that I know of has a pistol grip and takes your standard oxy/acet hoses. I think it's made by Henrob, if I remember correctly. Before I started hanging with you guys I used to mess around with home built airplanes and saw one of these used. But I tell you this. It happens FAST. I don't know how many passes it would take to master this thing, but that shit flows like water. And as you mentioned earlier, electric welds are brittle. That's why A/C tube frames are gas welded. If you can't find them pm me and I'll trace them down.
al weidman
Mar 29 2010, 09:35 PM
Rich, on my mig, I use ESAB easygrind .023 on 20 gauge and hammer the weld flat. I also use an aluminum spool gun on alloy wheel repair, cracks etc., works really good. When we widen wheels we use a tig miller wave auto welder, like they use on houseboat hulls. You for sure won't need that. The guy that helped us can weld cast iron in a hot box, which they will tell you can't really be done any more. He's in his late 60's and the last of his breed. Get a small spool of easygrind and see how it goes. If it works, think about getting a spool gun for your mig. I like it just fine. Al.
jd74914
Mar 29 2010, 09:49 PM
I'm not sure about not being able to hammer a TIG weld. I've never tried it, but in general they are very malleable if you use the correct filler. I've TIGed pieces, both steel and aluminum, sanded the minimal bead, and bent them pretty much on the bead without cracking problems. When I TIG I do make sure the object and rod is ridiculously clean which will help in that respect.
I have never torch welded before so I cannot come from that perspective. My grandpa was a torch welder and he really wants to teach me so I'm planning on trying it out this summer. Its much more cost effective than buying a TIG.
rick 918-S
Mar 29 2010, 09:51 PM
When I was 18 I went to welding school. I worked in fab shops for a few years and ended up at the ship yard. I worked on cars doing rust repairs and custom work in my garage during the summer. I eventually opened a collision and resto shop. If I had a bunch of money laying around I would buy an AC/DC tig machine.
For sheet metal: a butt joint will be less likely to warp with a tig as the heat is concentrated in a small area. You can get a small concentrated weld in the middle of a panel. With proper fit up and good welding technic you should be able to slap and file your seams with little effort. If you need to work a seam you can grind your weld then use a torch to anneal the metal. (still need the torch) Same with a mig weld. Use good welding technic, grind and file, then if you can't work the panel and feel like you are facing a crack if you mess with your seam, anneal the area and work the panel. (torch)
With a 00 torch tip you can also butt weld a seam. (ali or sheet steel one tool) It takes practice like any trade or art related skill. The reason the gas welded seam is easier to work is because the heat spreads out the molecules in a larger area. Because the heat is spread wider the metal natualizes slower allowing the molecules to stay expanded instead of compacting during a concentrated fast cool. The cool down still needs to be controlled and will need to be hammered and quenched. But you learn by practice when you need to get involved. Same with 4130 in race car and air frame work. Tig looks nice but is not as good or safe. (flame me, go ahead)
A Henrod torch is a very nice tool. I don't agree you need one but the benifit is it stays set the way you like it. You simply pull the trigger and relight it and your ready to weld. Unlike a hand set you have to adjust every time you turn it off. Either work.
Best value for a hobby shop? IMO: The torch set and a mig. You can weld almost any metal. You can change the metals character, you can cut and heat. You may need to dedicate a week of evening to practice, practice, practice. But once you have it you will have a skill most others won't.
Oh, recently I've gas welded the aluminum 4 cylinder intake manifold for the Shealey, I have a 4130 tubing anti-sway bar project under way I butt welded a couple of the seams on my friends Mercedes 280 SL. Like I said, If I had a bunch of money laying around I would buy the tig. But I have yet to really NEED one.
Porcharu
Mar 29 2010, 10:18 PM
Take a look here
metal godI have some of his videos showing repairing an aluminum racecar nose (I think it was Porsche to boot) he took a hatchet to it and had it welded up and ready for the body shop in about 15 minutes - using a torch. The big issue with a torch is getting on small enough for sheet-metal work, those 'journeymen sets' you see at the welding shops are for welding and cutting very thick steel and absolutely suck with sheet-metal - they will do nothing but pop and blow holes in your welds and you will get frustrated. They are also heavy. Get yourself a nice 'aircraft welding set' this is made for welding thin tubing and sheet metal and works fantastic, the one I have is made by Smith and I sprung for the ultra light hoses and it is a nice setup. I made a tank last year and it was a snap. You can pound on a torch weld all you want - I have cracked TIG beads and aluminum sheet is really bad in this respect.
Even though I have a TIG I mostly use the MIG (to get the job done quick and would not be without for basic welding) and the little torch. I will be using it for my flares when I get to that point.
I do like the TIG when it's the right way to go - it's also clean and quiet and I sometimes will use it late at night when I would normally use the MIG.
sww914
Mar 29 2010, 10:30 PM
My Friend Urs Gretener makes aluminum 550 spyders from scratch. He forms the aluminum sheets on an English wheel and TIG's the panels together wherever necessary. His welds don't need any hammering, they lightly sand them and primer. He doesn't need any filler, his panels are perfect.
Every seam is so perfectly aligned that he doesn't even use very much filler rod and he doesn't warp anything. Funny how the very best make it look so easy.
ghuff
Mar 30 2010, 07:05 AM
This is convincing me to get a torch.
That and an awesome vintage poster:
This is one of my favorite posters EVER
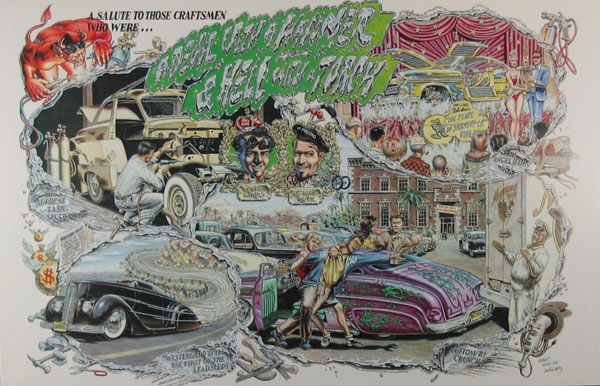
I want to learn that almost lost art.
underthetire
Mar 30 2010, 10:50 AM
I love my TIG. The only bad part of TIG on aluminum is you will need the high freq start, and if you do a fair amount of welding with it the water pump cooler sure is nice. This starts to add up in price quick like. The cheapo HF ones and such can't reverse, won't do aluminum.
ChrisFoley
Mar 30 2010, 10:59 AM
All my flared fenders are tig welded and never crack.
My aluminum fan shrouds are tig welded and don't crack when I hammer on them either.
charliew
Mar 30 2010, 02:26 PM
A few years ago at the annual air show I got into a conversation with a student at the local Texas State Technical Institute. It's on the old James Connaly airforce base in waco. He was in aircraft mechanics at the time but was also building a homebuilt expermental aircraft. The subject came up about 4130 welding and he said he had to gradually torch anneal the welds to make sure they didn't crack later on. He was tigging them and I thought that was the reason to be using the tig. He said the tig for him was prettier but actually the torch might be better. I do know that I spent many hours torch welding on a old jeep body and the welds never seemed too hard. The trick was to not get it too hot which is easy to do with a torch.
John Kelly has a video about making flares on the karman ghia and only uses a torch. He also shows how to use the shrinking disk and how to make one.
I've seen the henrob in action and if they wern't so expensive I would have one. I watched a guy weld a aluminum can. I also watched him cut 3/4 plate. He cut his initials in a piece of 1/4 inch plate while we watched.
I also have the 185 lincoln tig machine and the first time I used it was building a basket/stand to hold a aquamist tank for my son out of 1/4 x 1 inch strap aluminum and 3/16 sheet. If I didn't stop and wait the duty cycle would be reached and it would cut off. That was just going from one weld to another in 1 inch beads. Aluminum takes a lot of heat on thicker material.
The easygrind is nice wire but it is really expensive.
My welder friend wanted to sell me his extra 250 syncro wave but it requires a 100 amp breaker and I didn't want that extra expense but it would have done anything I wanted to weld.
I don't think I could get by without my 200 amp ac crackerbox for stick welding like on my shop structure or the 180 mig for small structural stuff or the 185 tig for ss or small aluminum. I also don't think I can do without a torch.
I have done sheetmetal welding with the ac stick welder when it was all I had. The torch came next, then the mig and now the tig. I still think there might be a need for the henrob though.
I have removed several broken off studs in cast iron with welding a big nut on the stud with the ac crackerbox. It sure beats drilling them out.
ChrisFoley
Mar 30 2010, 03:31 PM
QUOTE(charliew @ Mar 30 2010, 04:26 PM)

... 200 amp ac crackerbox for stick welding ...
AC stick welding
DC all the way
Speaking of SMAW - anyone ever weld aluminum with stick? Talk about requiring good technique...
Porcharu
Mar 30 2010, 04:09 PM
QUOTE(charliew @ Mar 30 2010, 01:26 PM)

A few years ago at the annual air show I got into a conversation with a student at the local Texas State Technical Institute. It's on the old James Connaly airforce base in waco. He was in aircraft mechanics at the time but was also building a homebuilt expermental aircraft. The subject came up about 4130 welding and he said he had to gradually torch anneal the welds to make sure they didn't crack later on. He was tigging them and I thought that was the reason to be using the tig. He said the tig for him was prettier but actually the torch might be better. I do know that I spent many hours torch welding on a old jeep body and the welds never seemed too hard. The trick was to not get it too hot which is easy to do with a torch.
John Kelly has a video about making flares on the karman ghia and only uses a torch. He also shows how to use the shrinking disk and how to make one.
I've seen the henrob in action and if they wern't so expensive I would have one. I watched a guy weld a aluminum can. I also watched him cut 3/4 plate. He cut his initials in a piece of 1/4 inch plate while we watched.
I also have the 185 lincoln tig machine and the first time I used it was building a basket/stand to hold a aquamist tank for my son out of 1/4 x 1 inch strap aluminum and 3/16 sheet. If I didn't stop and wait the duty cycle would be reached and it would cut off. That was just going from one weld to another in 1 inch beads. Aluminum takes a lot of heat on thicker material.
The easygrind is nice wire but it is really expensive.
My welder friend wanted to sell me his extra 250 syncro wave but it requires a 100 amp breaker and I didn't want that extra expense but it would have done anything I wanted to weld.
I don't think I could get by without my 200 amp ac crackerbox for stick welding like on my shop structure or the 180 mig for small structural stuff or the 185 tig for ss or small aluminum. I also don't think I can do without a torch.
I have done sheetmetal welding with the ac stick welder when it was all I had. The torch came next, then the mig and now the tig. I still think there might be a need for the henrob though.
I have removed several broken off studs in cast iron with welding a big nut on the stud with the ac crackerbox. It sure beats drilling them out.
The first welder I bought was a Henrob. It's OK but the pistil grip is fatiguing and the whole thing is really to big and to heavy for bodywork. It is OK for general welding and it is a very nice cutting torch. The little Smith torch I have is like a scalpel compared to an axe vs. the Henrob.
Porcharu
Mar 30 2010, 04:12 PM
QUOTE(Racer Chris @ Mar 30 2010, 09:59 AM)

All my flared fenders are tig welded and never crack.
My aluminum fan shrouds are tig welded and don't crack when I hammer on them either.
Hey Chris, Have you looked into "Tip Tig" I have been following this process for about a year and it looks like the way to go if you do a lot of welding.
Tip Tig
r_towle
Mar 30 2010, 05:07 PM
Great advice guys....keep it coming.
I have to say...I am leaning towards the torch...it does more.
If/when I need a special aluminum project welded....one coming soon...I know where Chris is.
Rich
scotty b
Mar 30 2010, 05:14 PM
https://www.tinmantech.com/html/aluminum_ga...ding_system.phpDeluxe kit.
Had one, works great. And it is TINY !! No good for cutting obviously but great for sheet welding. Get the ULW hoses. Much nicer
ChrisFoley
Mar 30 2010, 08:05 PM
QUOTE(Porcharu @ Mar 30 2010, 06:12 PM)

Hey Chris, Have you looked into "Tip Tig" I have been following this process for about a year and it looks like the way to go if you do a lot of welding.
Tip TigI never saw that before, thanks.
I've thought about semi-automatic tig for some of the production work I used to do but never with the features Tip Tig offers. I don't really think its worth the investment for the work we are doing currently but its worth keeping an eye on.
Porcharu
Mar 30 2010, 08:44 PM
QUOTE(scotty b @ Mar 30 2010, 04:14 PM)

https://www.tinmantech.com/html/aluminum_ga...ding_system.phpDeluxe kit.
Had one, works great. And it is TINY !! No good for cutting obviously but great for sheet welding. Get the ULW hoses. Much nicer
My Smith rig is just like that - except it has a lifetime warranty from a company that still exists. I am waiting for my cast iron welding setup from TM should be here soon - the lenses are really nice. I need to repair my nice old table saw that has cracked castings.
Steve
Porcharu
Mar 30 2010, 08:52 PM
Here is a pic. You should be able to get everything for about $500 including buying the tanks.
Porcharu
Mar 30 2010, 08:53 PM
Another with my ugly hand holding the torch.
Steve
This is a "lo-fi" version of our main content. To view the full version with more information, formatting and images, please
click here.