This may be old hat to many of you, but I have never done it before and figured some of you may be interested as well, especially if you are considering putting one of these into your 914.
The engine that I am starting with is a 4 bolt main block truck engine out of a 1985 Chevy K20 3/4 ton pickup. I am not yet sure what the engine will be when I am done with it. I want to build a 383 stroker engine. But, the parts for this engine are so nice that I may stick with stock displacement and just go with better heads and intake. The heads and intake have all the smog stuff on them, so they are not going to be used.
Enough with words. Time for pictures.
First, lay out your tools on the rear trunk of your old Porsche. Only the finest work jacket will do to keep the paint scratches to a minimum.
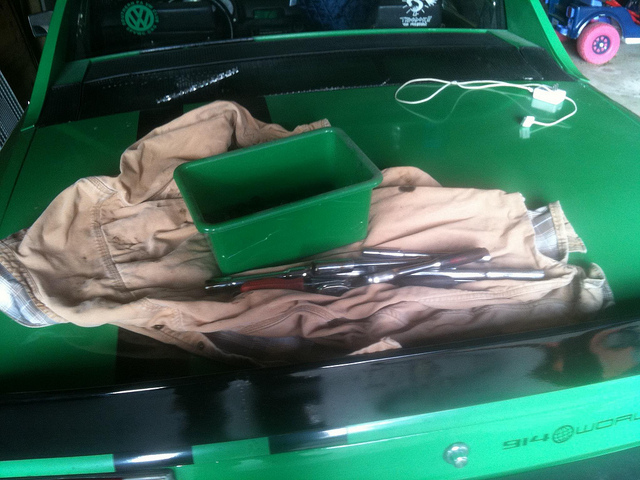
For tear down you need 4 wrench sizes (all inch sizes). 3/8, 7/16, 9/16, and 5/8th. You will want to have these sizes in deep sockets and wrenches. You will want to have at least one breaker bar to break torque on most of the 9/16 and 5/8 bolts. Also a rubber hammer, pry bar, and scraper will be needed.
The beast:
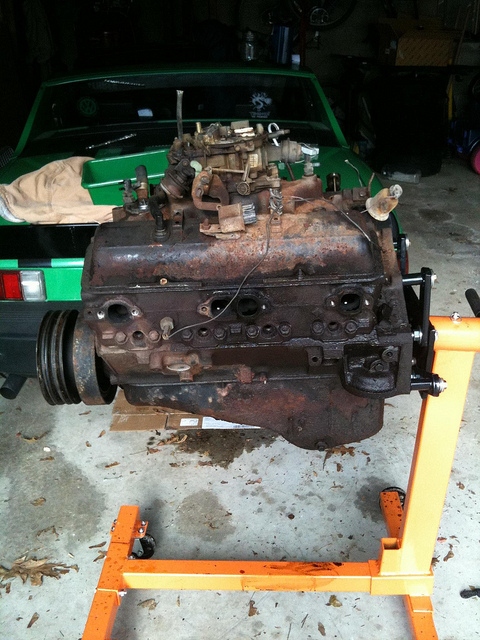
This is the engine that I am going to be tearing down. It was pulled out of the donor truck Dec 10th and mounted on the engine stand the next day. Don't even think of trying to do this without an engine stand. This 1000 pound stand only cost $50, and it is money well spent. Fair bet my 914 has a little bit of engine envy right now....
Valve covers first.
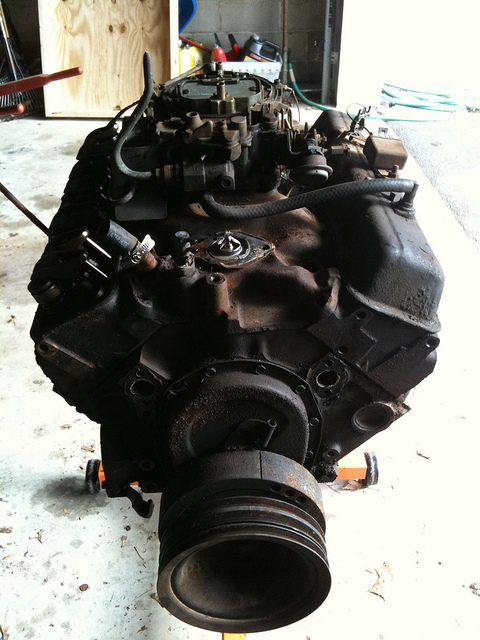
Valve covers need to come off first, as they impinge removing the intake. One off in the picture above. You need a 7/16 deep socket to take off the nuts that hold the valve covers on. Lots of sealant was used here.
Valve covers, carb and intake are off.
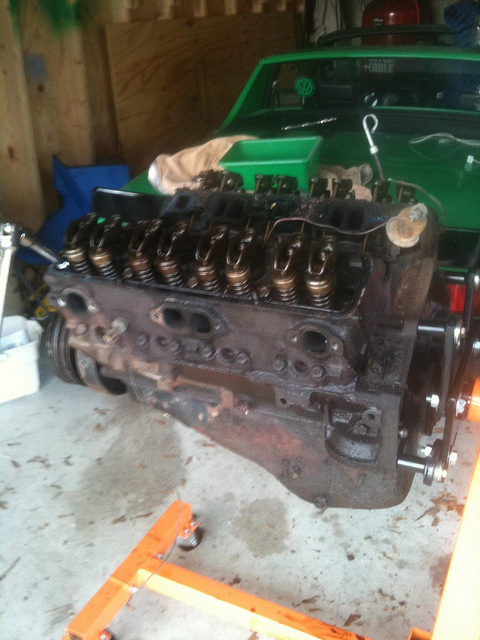
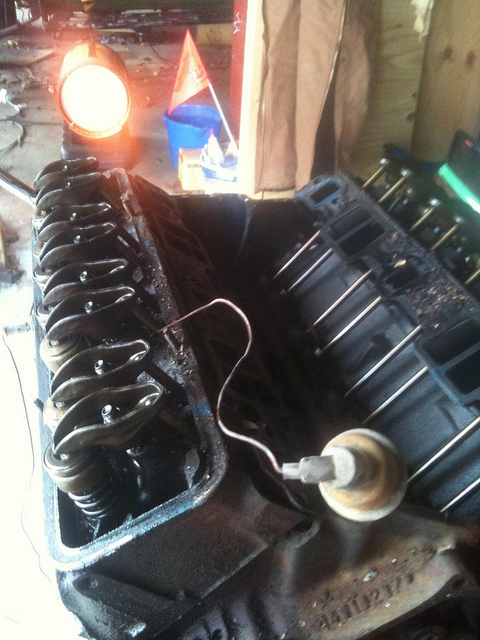
Pretty easy so far. Time to go for the heads. The rods going into the block are all the push rods. They come up from the cam and operate the valves. The orange ball of fire is my heater. 70K BTU of warmth to stave off the cold, even with the garage door open. I even had to take off my warm overalls, as I started sweating with the heater and the overalls both. The intake was attached with 9/16th bolts. There was considerable sealant used, and getting the intake off was difficult. I ended up using a pry bar to get it started, and hold it up enough to get my fingers in there to pull the rest off.
First head is off.
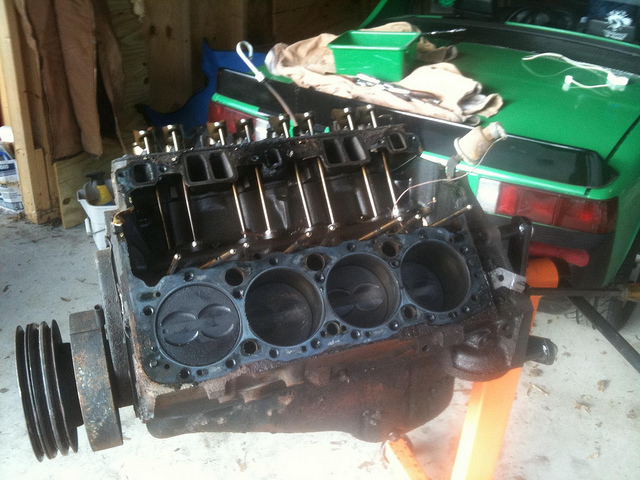
This is the point where I had to do some soul searching. It was pristine! The cylinder walls look like they were just done. There was no carbon ring at the top of the cylinders, which is common for an engine with miles on it. The PO of the donor truck said the engine had been rebuilt 4000 miles ago. But given the condition of the truck and the electrical system (the spark plugs were rusted and fell apart on removal) I had my doubts. Now, though... it took a fair deal of will power to not just button the engine back up again and put new heads and intakes on it. But, I am a stubborn man at times... I am going to rebuild this engine, darn it! This is how I learn. The heads bolts were 5/8s and were heavily torqued. I needed a breaker bar to get them started.
With the heads off I took off the pulley and damper. The damper was a PAIN to get off. Lots of prying with the pry bar all over to keep it from cocking. One of those things where I probably should have used a puller, but I did not have one the right size or the desire to go and get one.
to be continued....