HalfMoon
Oct 14 2013, 02:09 PM
Getting ready to add front and rear sway bars to my 1973 914 v-8 converted.
I ordered the front and rear plates from GPR today
http://www.gprparts.com/index.wws(Thanks for the referral Dr. Evil on an unrelated part)
And I was suprised to hear my sales rep advising NOT to weld the front plate. He claimed that only a very skilled welder should do that weld as the metals are dis-similar in terms of thickness and it's easy to "blow" through the cars sheet metal when welding the much thicker plates.
That's a notation that's well known and discussed at length here at world, but I had no idea the installation could be done without welding that plate at all and simply doing a "through" bolting.
What the concensus on this?
All welcome to weigh in especially those who have done a "through" bolting as opposed to a welding in of the plates :-)
Thanx!
David
SirAndy
Oct 14 2013, 02:11 PM
QUOTE(HalfMoon @ Oct 14 2013, 01:09 PM)

What the concensus on this?
biosurfer1
Oct 14 2013, 02:12 PM
I did not weld mine in and it has worked fine so far. I agree with the rep that only a trained welder should should do it if you go that route, its pretty tight in there. As for if welding is that much better, couldn't say.
HalfMoon
Oct 14 2013, 02:14 PM
How long ago in time and miles did you do your install friend?
Thanks for the input :-)
D
QUOTE(biosurfer1 @ Oct 14 2013, 04:12 PM)

I did not weld mine in and it has worked fine so far. I agree with the rep that only a trained welder should should do it if you go that route, its pretty tight in there. As for if welding is that much better, couldn't say.
biosurfer1
Oct 14 2013, 02:36 PM
about 2 years and I'd say 5000 miles ago
worn
Oct 14 2013, 02:41 PM
QUOTE(HalfMoon @ Oct 14 2013, 12:09 PM)

Getting ready to add front and rear sway bars to my 1973 914 v-8 converted.
I ordered the front and rear plates from GPR today
http://www.gprparts.com/index.wws(Thanks for the referral Dr. Evil on an unrelated part)
And I was suprised to hear my sales rep advising NOT to weld the front plate. He claimed that only a very skilled welder should do that weld as the metals are dis-similar in terms of thickness and it's easy to "blow" through the cars sheet metal when welding the much thicker plates.
That's a notation that's well known and discussed at length here at world, but I had no idea the installation could be done without welding that plate at all and simply doing a "through" bolting.
What the concensus on this?
All welcome to weigh in especially those who have done a "through" bolting as opposed to a welding in of the plates :-)
Thanx!
David
Well, let's say the gas tank is out of the way...that may alter the discussion.
The trick in all heat joining of metals is to direct the torch/heat at the larger piece in a way that the two masses heat at the same rate. I have silver soldered with the torch pointed at a point some distance from the actual joint in order to protect very thin work, while heating the thick. In mig welding, the torch needs to be angled to the plate to get the heat to that before the sheet metal falls away. An alternative is plug welding through the thinner body metal. If you have a puddle started in the thick, it will naturally encompass the thin as it spreads. Maybe you already know all of this. I apologize if you do. Good luck.
I am going to be trying this trick myself in a week or few, so we will see how I fare.
HalfMoon
Oct 14 2013, 03:16 PM
Good data!
When you did the install, since you weren't welding, did you remove the tank or not? I've often wondered if the job can be done without tank removal if it was going to simply be "through bolted"...
D
QUOTE(biosurfer1 @ Oct 14 2013, 04:36 PM)

about 2 years and I'd say 5000 miles ago
HalfMoon
Oct 14 2013, 03:19 PM
Lol, well the truth is I simply don't feel I have the skill neccessary for delicate work like this and....if it can be through bolted and has a history of holding up, that would save me dollying the unit to a skilled welder (as the tank obviously would need to be removed, thus making the unit inoperable)
Thanks for the input :-)
D
QUOTE
Well, let's say the gas tank is out of the way...that may alter the discussion.
The trick in all heat joining of metals is to direct the torch/heat at the larger piece in a way that the two masses heat at the same rate. I have silver soldered with the torch pointed at a point some distance from the actual joint in order to protect very thin work, while heating the thick. In mig welding, the torch needs to be angled to the plate to get the heat to that before the sheet metal falls away. An alternative is plug welding through the thinner body metal. If you have a puddle started in the thick, it will naturally encompass the thin as it spreads. Maybe you already know all of this. I apologize if you do. Good luck.
I am going to be trying this trick myself in a week or few, so we will see how I fare.
Jeffs9146
Oct 14 2013, 03:21 PM
When I welded mine I just started the weld on the thick metal and rolled it into the thin back and forth pausing a bit on the thick to get the heat going!
Eric_Shea
Oct 14 2013, 04:51 PM
I would "never" install one without welding it in.
HalfMoon
Oct 14 2013, 05:55 PM
"Never" is strong language. Could you expand on your thoughts?
Have you seen failures in through bolting, ie-ripped sheet metal and or stress fracturing? (which is my primary concern)
QUOTE(Eric_Shea @ Oct 14 2013, 06:51 PM)

I would "never" install one without welding it in.
chads74
Oct 14 2013, 05:57 PM
QUOTE(HalfMoon @ Oct 14 2013, 02:16 PM)

Good data!
When you did the install, since you weren't welding, did you remove the tank or not? I've often wondered if the job can be done without tank removal if it was going to simply be "through bolted"...
You have to remove the tank to but the thinker plate on the inside. You will have to trim for the bottom bolt hole. I just did this to mine this weekend, before and after pics of what I had to trim for the backing plate to fit.
Click to view attachment
chads74
Oct 14 2013, 05:58 PM
euro911
Oct 14 2013, 06:13 PM
Yeah, you have to remove the tank either way. Dave (maddog) is now manufacturing Engman 'clone' reinforcement plates too ... I would suggest having a set welded in to spread the loads over a larger area.
Click to view attachment ...
Click here
HalfMoon
Oct 14 2013, 06:13 PM
Terrific images Friend! Thanks for that. Were you planning on welding or through bolting? Very helpful image. No doubt my tank will have to come out either way, lol.
QUOTE(chads74 @ Oct 14 2013, 07:57 PM)

QUOTE(HalfMoon @ Oct 14 2013, 02:16 PM)

Good data!
When you did the install, since you weren't welding, did you remove the tank or not? I've often wondered if the job can be done without tank removal if it was going to simply be "through bolted"...
You have to remove the tank to but the thinker plate on the inside. You will have to trim for the bottom bolt hole. I just did this to mine this weekend, before and after pics of what I had to trim for the backing plate to fit.
HalfMoon
Oct 14 2013, 06:19 PM
Well that's quite interesting. Certainly more re-enforcing than I intended. My bar is stock and my driving is "spirited" (it is after all a v-8 converted) but I'm not at all sure that level of re-enforcing is needed given the level of driving. Seems more "race carish". Pretty neat stuff though :-)
D
QUOTE(euro911 @ Oct 14 2013, 08:13 PM)

Yeah, you have to remove the tank either way. Dave (maddog) is now manufacturing Engman 'clone' reinforcement plates too ... I would suggest having a set welded in to spread the loads over a larger area.
Click to view attachment ...
Click here
Jeff Hail
Oct 14 2013, 06:45 PM
Weld the reinforcements in. The apron is fairly thin and I have seen many crack with the through bolt only method. Nothing like hearing that loud thud when carving through a wet off camber turn when one side lets loose. The only thing that will hold you in the seat

is a balloon knot.
SirAndy
Oct 14 2013, 07:25 PM
QUOTE(HalfMoon @ Oct 14 2013, 04:55 PM)

Have you seen failures in through bolting, ie-ripped sheet metal and or stress fracturing? (which is my primary concern)
Yes, more than once ...
Mblizzard
Oct 14 2013, 07:47 PM
QUOTE(euro911 @ Oct 14 2013, 04:13 PM)

Yeah, you have to remove the tank either way. Dave (maddog) is now manufacturing Engman 'clone' reinforcement plates too ... I would suggest having a set welded in to spread the loads over a larger area.
Click to view attachment ...
Click hereI had my hands on some of Dave's plates at Okteenerfest this weekend. Quality stuff for sure. I am planning to do my install this winter so I will be following what happens here. Don't plan on auto crossing so I had convinced my self there was no need to weld. Now I am not as convinced.
Dave_Darling
Oct 14 2013, 08:56 PM
When you bolt in, you are sandwiching the fender between two thicker pieces of metal. It's reasonably strong.
When you weld in, you are adding another layer of material permanently. It's stronger.
The factory just welded nuts onto the fender. It seems to hold up reasonably well, but the weld nuts are much thicker than the fender sheetmetal, and will keep cracks from propagating at the start.
A good welder can weld the inboard plate on. That should be the best way to go.
We have seen some tearing of the fender sheetmetal around the bolt-holes when a bolt-in setup has been used. It's not that common, but it does happen. There have even been one or two instances of problems starting with a weld-in setup. I think those may have only been in race cars? They were part of the impetus behind the design of the large reinforcement kit.
We see quite a bit more tearing if the U-bolt setup is used. (The one that proudly advertises "no gas tank removal required!") You don't want to use this one.
--DD
McMark
Oct 14 2013, 09:14 PM
This is a little overblown IMHO. Welding it in is not any harder than any other welding. The welding is just to keep things in place. It doesn't need to be welded all the way around. The benefit to welding it is that you can remove and reinstall the sway bar without pulling the tank in the future. That's worth it for me. I wouldn't put the large reinforcement plates on a street car.
Eric_Shea
Oct 14 2013, 09:17 PM
QUOTE(HalfMoon @ Oct 14 2013, 05:55 PM)

"Never" is strong language. Could you expand on your thoughts?
Have you seen failures in through bolting, ie-ripped sheet metal and or stress fracturing? (which is my primary concern)
QUOTE(Eric_Shea @ Oct 14 2013, 06:51 PM)

I would "never" install one without welding it in.
Never is simple language not strong. I would simply never do it because yes, I've seen many failures.
bulitt
Oct 14 2013, 09:31 PM
PMB sells the backing plates-
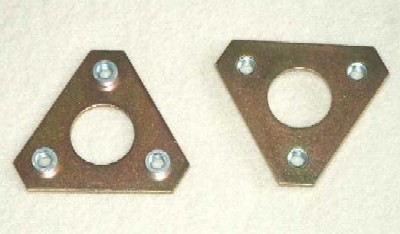
So does tangerine racing-
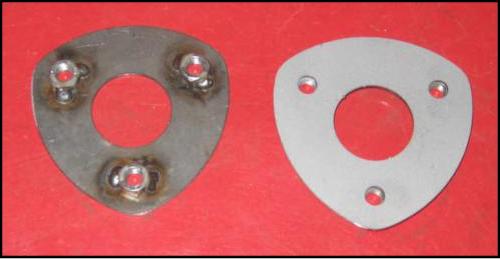
And a good installation write up on Pelican-
Pelican Link.
HalfMoon
Oct 14 2013, 10:23 PM
Well I must say I'm leaning toward getting them welded in based largely on the replies to my post. It'll be something of a pain as this will mean getting the vehicle to a welder (and with the fuel tank out....well you can do the math).
If the vehicle wasn't converted to a v-8 (radiator), right about now I'd be thinking about a fuel cell mounted forward permamently making the sway bar accessable. But sadly, I'm concerned a fuel cell would interupt needed air flow through my radiator so that's not a solution that would work in this application :-/
D
And Thanks for the valuable input Dave (and all other friends)
QUOTE(Dave_Darling @ Oct 14 2013, 10:56 PM)

When you bolt in, you are sandwiching the fender between two thicker pieces of metal. It's reasonably strong.
When you weld in, you are adding another layer of material permanently. It's stronger.
The factory just welded nuts onto the fender. It seems to hold up reasonably well, but the weld nuts are much thicker than the fender sheetmetal, and will keep cracks from propagating at the start.
A good welder can weld the inboard plate on. That should be the best way to go.
We have seen some tearing of the fender sheetmetal around the bolt-holes when a bolt-in setup has been used. It's not that common, but it does happen. There have even been one or two instances of problems starting with a weld-in setup. I think those may have only been in race cars? They were part of the impetus behind the design of the large reinforcement kit.
We see quite a bit more tearing if the U-bolt setup is used. (The one that proudly advertises "no gas tank removal required!") You don't want to use this one.
--DD
rjames
Oct 14 2013, 10:36 PM
QUOTE(HalfMoon @ Oct 14 2013, 09:23 PM)

Well I must say I'm leaning toward getting them welded in based largely on the replies to my post. It'll be something of a pain as this will mean getting the vehicle to a welder (and with the fuel tank out....well you can do the math).
If the vehicle wasn't converted to a v-8 (radiator), right about now I'd be thinking about a fuel cell mounted forward permamently making the sway bar accessable. But sadly, I'm concerned a fuel cell would interupt needed air flow through my radiator so that's not a solution that would work in this application :-/
D
And Thanks for the valuable input Dave (and all other friends)
QUOTE(Dave_Darling @ Oct 14 2013, 10:56 PM)

When you bolt in, you are sandwiching the fender between two thicker pieces of metal. It's reasonably strong.
When you weld in, you are adding another layer of material permanently. It's stronger.
The factory just welded nuts onto the fender. It seems to hold up reasonably well, but the weld nuts are much thicker than the fender sheetmetal, and will keep cracks from propagating at the start.
A good welder can weld the inboard plate on. That should be the best way to go.
We have seen some tearing of the fender sheetmetal around the bolt-holes when a bolt-in setup has been used. It's not that common, but it does happen. There have even been one or two instances of problems starting with a weld-in setup. I think those may have only been in race cars? They were part of the impetus behind the design of the large reinforcement kit.
We see quite a bit more tearing if the U-bolt setup is used. (The one that proudly advertises "no gas tank removal required!") You don't want to use this one.
--DD
See if you can find someone to come to you. May be cheaper than towing your car to a shop. It'll be a quick job.
nine9three
Oct 14 2013, 10:47 PM
QUOTE(HalfMoon @ Oct 14 2013, 09:23 PM)

Well I must say I'm leaning toward getting them welded in based largely on the replies to my post. It'll be something of a pain as this will mean getting the vehicle to a welder (and with the fuel tank out....well you can do the math).
If the vehicle wasn't converted to a v-8 (radiator), right about now I'd be thinking about a fuel cell mounted forward permamently making the sway bar accessable. But sadly, I'm concerned a fuel cell would interupt needed air flow through my radiator so that's not a solution that would work in this application :-/
D
And Thanks for the valuable input Dave (and all other friends)
No matter which version you use bolt it all together before you weld it up. Welding really was the easy part. I welded all the way around, short of where it is hidden below the shelf.
HalfMoon
Oct 15 2013, 07:29 AM
Can't help wonder what the concensus would be on cold welding given the delicacy of this area (thick metal v thin metal weld area)? I hear the race crowd often uses cold welding for applications like this.
Racers welcome to chime in....
D
bulitt
Oct 15 2013, 07:46 AM
Aircraft epoxy? Holds the wings on planes. Probably would work. Why don't you try it?
TheCabinetmaker
Oct 15 2013, 08:47 AM
I thru bolted and welded mine. Ten years of spirited driving and DE's at Hallett with no problems. I did my own welding and I'm certainly no accomplished welder. I don't think this can be done with gas tank in car. No way to get to inside with a wrench or welder.
Spoke
Oct 15 2013, 09:01 AM
Weld it in.
If you are even somewhat mechanically inclined, buy a welder and have fun.
Bought mine several years ago and I've welded a lot on my 914, along with mufflers and hangers on 3 other cars, and the mower deck on my lawn tractor, and other stuff around the house.
ChrisFoley
Oct 15 2013, 10:26 AM
Weld it in. Weld it all the way around.
Don't cheat or it may bite you later on.
The factory used a tri-oval shaped reinforcing plate with nuts welded onto it.
However, they spot welded the plate to the body from the outside instead of perimeter welding it on the inside.
I've seen original factory installations that cracked but only after the suspension had been upgraded with a larger anti-sway bar.
HalfMoon
Oct 15 2013, 10:56 AM
Hmmm...I'm quickly becoming interested in the Loctite industrial Hysol E-60HP Aircraft cold weld epoxy system with a shear strength between 3000-5000 Lbs. and a cure time of an hour.
See the data sheet here
http://tds.loctite.com/tds5/docs/HYSAE-60HP-EN.PDF
Mblizzard
Oct 15 2013, 12:09 PM
QUOTE(HalfMoon @ Oct 15 2013, 08:56 AM)

Hmmm...I'm quickly becoming interested in the Loctite industrial Hysol E-60HP Aircraft cold weld epoxy system with a shear strength between 3000-5000 Lbs. and a cure time of an hour.
See the data sheet here
http://tds.loctite.com/tds5/docs/HYSAE-60HP-EN.PDFThat is interesting but I think that I will weld in as it seems like even a few small spot welds would be better than no weld and welding around would be the best. Seems like welding is a do it once with predictable results approach where the epoxy could have questions.
HalfMoon
Oct 15 2013, 01:58 PM
Here's my thinking.
It seems there's been failures both with through bolting and welding. It occurs to me the surrounding area has a two fold problem due to sheetmetal that may be too thin for the intended application (sway bar stresses).
1. Through bolting in and of itself isn't all that great an option as the loads are carried pretty much on the three bolts and so those bolt hole area's are taking alot of stress (tearing possibility in surrounding sheetmetal).
2. In an effort to reduce that stress and spread the load to the plate, we've come up with either spot welding or line welding in addition to through bolting. Either add heat to an already compromised area thus weakening the metal (surely spot welding less).
So....perhaps a cold weld with a quite serious aircraft quality product in addition to through bolting would spread the load to the entire plate (not just the bolts) without having heated the surrounding thin metal thereby reducing it's strength?
QUOTE(Mblizzard @ Oct 15 2013, 02:09 PM)

QUOTE(HalfMoon @ Oct 15 2013, 08:56 AM)

Hmmm...I'm quickly becoming interested in the Loctite industrial Hysol E-60HP Aircraft cold weld epoxy system with a shear strength between 3000-5000 Lbs. and a cure time of an hour.
See the data sheet here
http://tds.loctite.com/tds5/docs/HYSAE-60HP-EN.PDFThat is interesting but I think that I will weld in as it seems like even a few small spot welds would be better than no weld and welding around would be the best. Seems like welding is a do it once with predictable results approach where the epoxy could have questions.
McMark
Oct 15 2013, 08:47 PM
This thread is waaay overthough...
Eric_Shea
Oct 15 2013, 09:20 PM
...a problem that wasn't even there in the first place.
You mean like welding two different thickness metals?

McMark
Oct 15 2013, 09:51 PM
Yeah, something like that.
HalfMoon
Oct 15 2013, 10:24 PM
Not sure I agree.
The thread started as an address of alternatives to hot welding as I don't have ready access to welding equiptment (nor the required skill in welding dissilimar metals) but quickly became a discussion addressing advantages and disadvantages to hot welding -v- through bolting as failure had been recognized in both. This led to the introduction a discussion of other alternatives possibilities like high tech cold welding which could have raminfications in many other problem solving areas.
So, perhaps it's not a "problem" but rather a thread that's led to a possibly innovative alternative idea?
Isn't it "possible" that using a high tech cold weld epoxy compound is not only an alternative, but possibly (in this application), the "best" alternative, knowing that through bolting has stress dis-advantages and hot welding regardless of skill, weakens surrounding area's (area's that are already compromised by less than robust thickness)?
So, no not a "problem" but rather, "kicking around" ideas.
At the end of the day, had it not been a fellow poster having introduced the idea of cold welding in a private message, I'd have no doubt gone with through bolting and spot welding. But the idea of high tech cold welding had me intrigued so what better place to kick that idea around than here
McMark
Oct 15 2013, 10:47 PM
Absolutely. Make sure to keep us posted on how it holds up. I have my doubts, but all data is good data.

We learn more from failure than success. And if it does work, we have a new alternative for people who don't have access to welding.
On a side note, you can stop thinking about the 'dissimilar metals' because they're both steel and their thicknesses aren't drastic. Welding it is not tricky in the grand scheme of things.
pete000
Oct 15 2013, 11:08 PM
Any one in the South Bay (CA) have a portable welding out fit that does house calls that might be able to help me weld in my sway bar mounts???
914_teener
Oct 15 2013, 11:22 PM
If you can bring it up my way I can do it for you. I live up the SG Valley though.
I don't do aircraft epoxy.....
You can also rent an Lincoln MIG at Home Depot if you want to learn to do it yourself.
No offense to the OP....but you should learn how to weld...taint that difficult.
euro911
Oct 15 2013, 11:31 PM
Well, I'm going to weld the reinforcement plates in the wheel wells. It's pretty much proven ... and I already have the parts
Interested in hearing how well the epoxy holds up though
SirAndy
Oct 16 2013, 01:31 AM
QUOTE(McMark @ Oct 15 2013, 09:47 PM)

On a side note, you can stop thinking about the 'dissimilar metals' because they're both steel and their thicknesses aren't drastic. Welding it is not tricky in the grand scheme of things.
I agree. I'm not sure who came up with the "Can't weld this because the thickness is not the same" excuse, but even a crappy welder like myself can do this without burning holes all over the place ...
Eric_Shea
Oct 16 2013, 12:34 PM
QUOTE
but even a crappy welder like myself can do this without burning holes all over the place ...
Glad I'm not alone.

I weld like a 3-year old on acid.
HalfMoon
Oct 16 2013, 02:45 PM

It'll make for an interesting experiment and the data good or bad will be valuable.
While I do know how to weld, I don't currently have a welder (not to mention I suck at welding) and once the car is disabled (fuel tank out) it would be a pain to get it to a welder, so if this alternative works out it'd be useful knowledge for those in the same boat.
QUOTE(McMark @ Oct 16 2013, 12:47 AM)

Absolutely. Make sure to keep us posted on how it holds up. I have my doubts, but all data is good data.

We learn more from failure than success. And if it does work, we have a new alternative for people who don't have access to welding.
On a side note, you can stop thinking about the 'dissimilar metals' because they're both steel and their thicknesses aren't drastic. Welding it is not tricky in the grand scheme of things.
damesandhotrods
Oct 16 2013, 05:05 PM
I have a question about the epoxy verse welding, maybe someone here with a stronger mechanical engineering background could address. The problem seems to be the thin steel of the inner fender. Wouldn’t the epoxied sway bar backing plates distribute the stress over the whole of the plate? Were as the welded plate, wouldn’t the stress be concentrated on the welds and then radiate out?
HalfMoon
Oct 16 2013, 05:17 PM
Actually I think there's no difference in terms of spreading the load out. The alternative cold welding has a benefit in that it wouldn't be heating the inner wheel well sheet metal which in theory would be weakened due to the induction of heat through welding. I can't say how much if any difference hot welding could/would compromise the metal but failure has been detected in both through bolting alone and through bolting with hot welding.
QUOTE(damesandhotrods @ Oct 16 2013, 07:05 PM)

I have a question about the epoxy verse welding, maybe someone here with a stronger mechanical engineering background could address. The problem seems to be the thin steel of the inner fender. Wouldn’t the epoxied sway bar backing plates distribute the stress over the whole of the plate? Were as the welded plate, wouldn’t the stress be concentrated on the welds and then radiate out?
Matt Romanowski
Oct 16 2013, 05:24 PM
People are making a way bigger deal out of this than it is. If you don't have access to a welder, don't panic. Put it together. If it tears in ten years, then fix it then. Lots of cars last a long time just bolted together.
Remember, people used to just use the u bolts! I'm surprised those cars didn't blow up!
euro911
Oct 16 2013, 10:28 PM
QUOTE(pete000 @ Oct 15 2013, 10:08 PM)

Any one in the South Bay (CA) have a portable welding out fit that does house calls that might be able to help me weld in my sway bar mounts???

Hey Pete, Milt Becker (Zeke) does mobile welding. Try to PM him on this forum, if no response, try him on Pelican. If that don't work, PM me
0396
Oct 16 2013, 10:40 PM
Here's my .02. If your going to do some DE events, never worry about it via the do it once attitude, use larger wheels, heavier sways, shocks..etcetera, etc. Weld it and be over with it. Other wise, for the want a be daily driver stock. Through bolts should be good.
I welded mine.
This is a "lo-fi" version of our main content. To view the full version with more information, formatting and images, please
click here.