This is a rough schematic of how it's going to work.
The main spine and the cross members are 60mm steel box section.
The short stubs at either end will then connect to conventional 'engine stand' type stands.
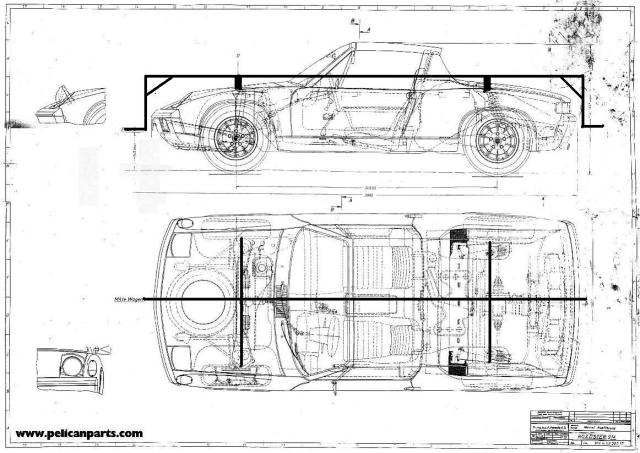
I've never liked the idea of picking a car up the conventional way, by it's extremities, as it means putting loads into the car in directions it wasn't designed for - and besides 2 of my bumper mounts are rotten and one has crash damage - and is rotten.
My next thought was to fix the spit to the suspension mounts underneath which is another common way of doing it but this would be difficult to measure and fabricate - working upside down - and besides there's work to be done on the suspension mounts as well !
So finally I hit on the idea of mounting off the top of the shock towers - easy access, the loads will be in more or less the right direction and it will be very easy to build something with the minimum of fancy fabrication. A bonus is that the whole structure will act as a brace although I have got door braces fitted as well. The biggest plus is that the whole of the underside is completely open and easy to get at.
At the moment I'm just finishing off the front crossmember which will be welded to the clamping plates which normally hold the tops of the shocks.
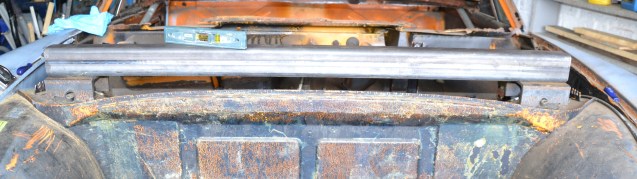
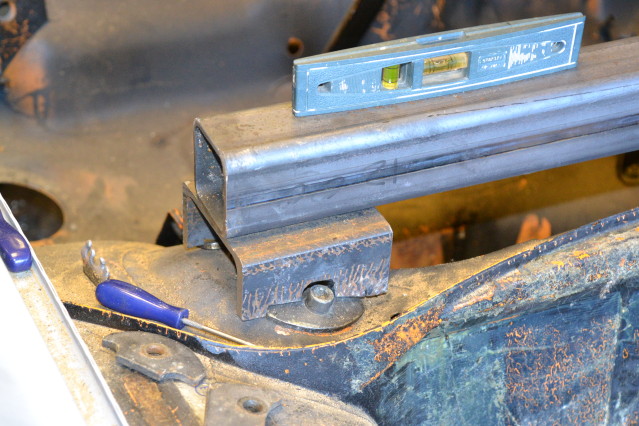
Has anyone done anything like this before ?