I don't claim to be an expert, but I've done some welding.
I was waist deep in a Locost project when someone offered to buy it for more than I had into it. It would have had a Volvo 4cyl eventually.
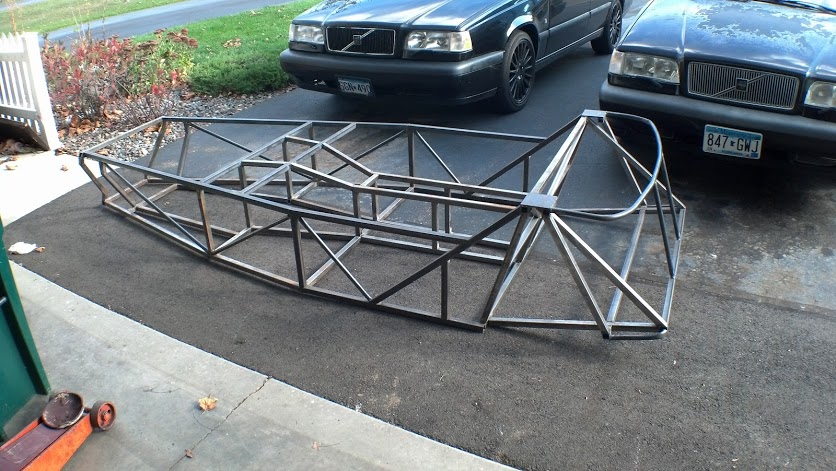
Also welded sheetmetal on a few occasions. I welded a new rocker into this VW, hard to tell but the seam was midway down the side of the car, going vertical.
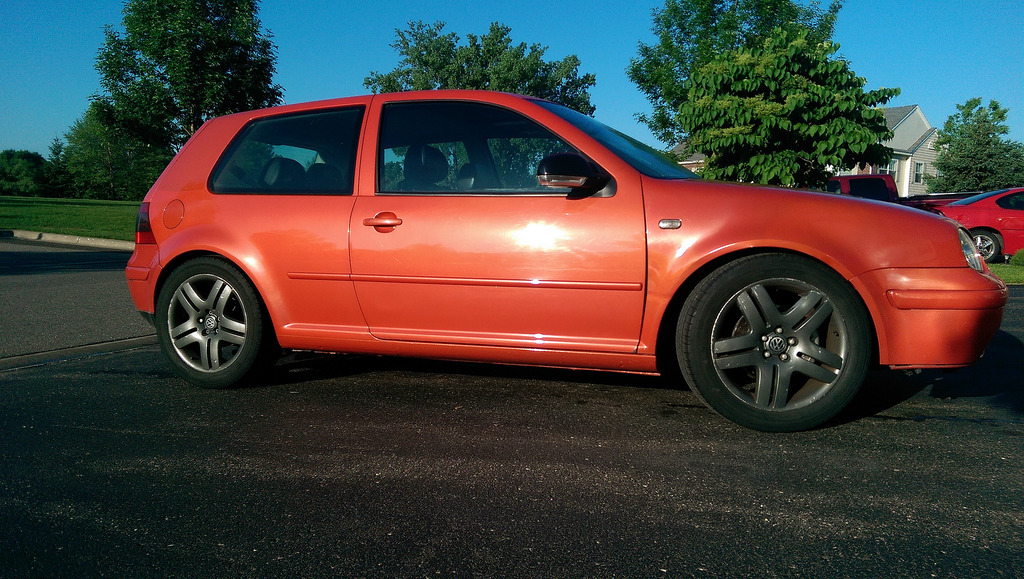
Trick for minimizing shrink is completing the weld using small spot welds so as not to introduce too much heat.