Some smart person here should be able to come up with a formula for square inches needed of the opening for air in and the same for air out. I'm not that smart.
It probably has to do with how much heat the engine is going to generate, the size of the radiator, the material of the radiator, and the CFM of the radiator fans.
I took a guess. Mine is an LB9 305 Chevy making maybe 230 HP.
The opening I cut in my bumper is 22.5" x 5" or 112.5 square inches.
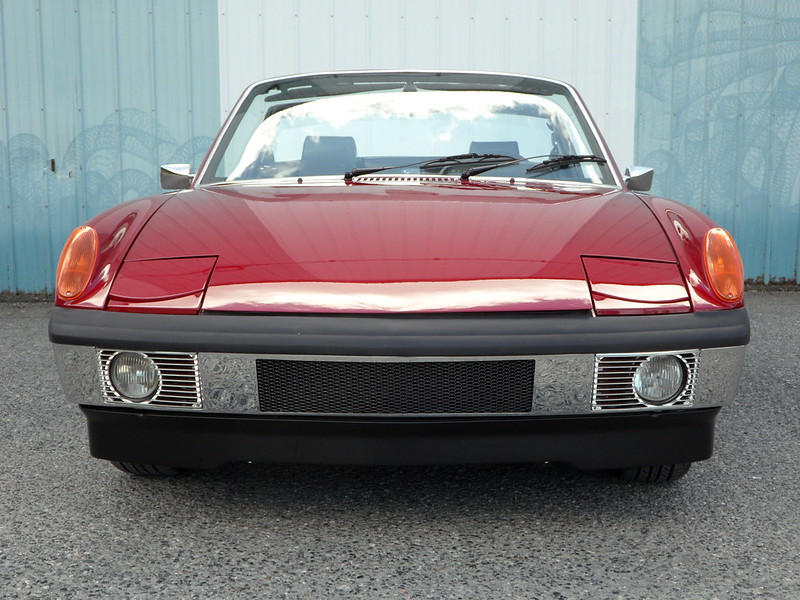
I felt the openings for the air out should be at least as big as the air in opening. Mine are 10" x 8" or a total of 160 square inches for both.
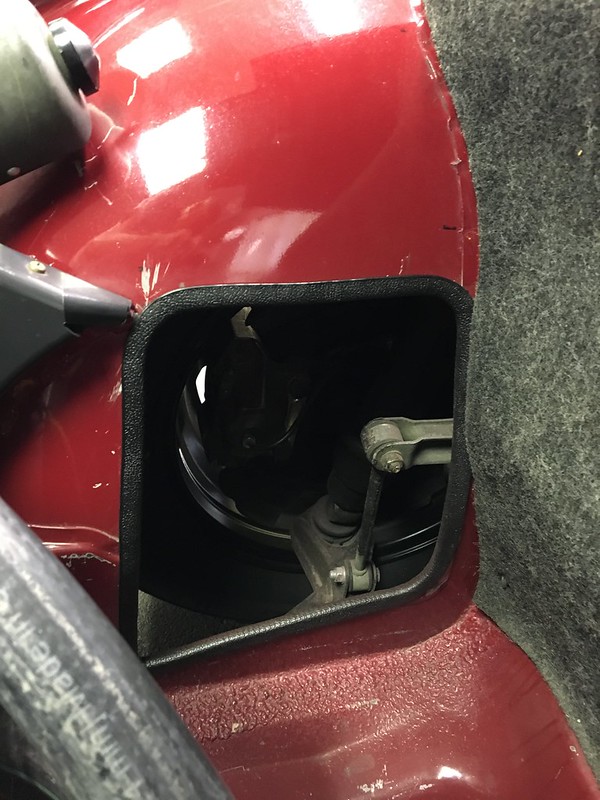
My radiator is Renegade's Ron Davis for a SBC. Aluminum.
It cools fine. Running down the road, the fans do not come on. Idling they will cycle on and off. It runs right on the 160 t-stat. (Disclaimer...I don't live in Phoenix.

)
The hood vents linked to are 12" x 5.5" overall. It looks like there is about a 1" mounting boarder on all sides leaving a vent area of 10 x 3.5. This would give you 70 square inches of air out. My GUESS is that this would not be enough (although Sir Andy's seems to work fine with even less space for air out...it could be the custom plenum helps?)
The good news about the vents linked to is that it appears both will fit (barely) without cutting any of the hood support structure and will fit between the rad and the bulkhead in front of the fuel tank.