BeatNavy
Sep 6 2019, 03:06 PM
The last week or so I've been breaking in a new engine I built last winter and finally manage to install a couple of weeks ago. I'm pretty happy with how it pulls, and after a LOT of fiddling with the MPS and timing I think I've got it where it will start right up, idle cold (barely), idle nicely when warm, and run with nice cool head temps. I do seem to have a slight bit of ping/detonation under load around 2800 to 3000 RPM, so I guess I need to play with timing a bit more.
I am much less happy with the oil leaks. I know building a leak-free Type IV is a challenge, and given this is my first effort, I didn't expect perfection. But right now it's leaking pretty badly in a couple of places: out of the transmission weep hole (probably RMS, I guess), somewhere around oil filter console and/or pressure relief valve, and, surprisingly, what seems to be sort of spraying out and around oil filler neck.
Here I need help from the World; I see a combination of three possible causes for this many leaks (when I otherwise took my time and tried to follow guidelines, using Jake's recommended sealants):
1. My own inexperience
2. Too much crankcase pressure from rings not seating yet
3. Too much crankcase pressure from no head venting.
Here are some details on build:
2056 with 9950 Cam using D-Jet
Brand new AA Heads built by HAM, and Len sealed up the vents
96mm KB Pistons with Hastings Rings
8.6 CR
A couple of notes: I didn't gap the rings per Jake's philosophy that crankcase pressure is what causes oil leaks, and the rings come properly gapped. Also, Len (and Jake) don't like head venting for oil flow (so my heads had vent plugged). If I understand him correctly, Len told me the stock PCV vale should provide enough crankcase pressure relief on a street car. RMS is the Sabo brand (the "good" one).
Any thoughts on 1, 2 or 3 above? I'm willing to pull the engine and reseal, but I wanted to see if 2 or 3 are possibilities that I need to address. Is the stock PCV valve (which I am sure is not clogged) enough pressure relief?
Thanks for any help.
Superhawk996
Sep 6 2019, 03:17 PM
Sounds an awful lot like too much crank case pressure. How many miles are on it? Even if only a few miles, I've never seen that much crank pressure even before break in to have oil coming out the fill neck / breather assembly.
When you say you didn't gap the rings, I'm assuming you mean ring end gaps. Do you at least know what the end gaps were when you built it?
Likewise, did you stagger the ring gaps between top, middle, and oil scraper rings? If all of those ring gaps are lined up, that could be a source of too much blow by.
Likewise you could potentially do a leakdown test and see if you have cylinders that aren't sealed and blowing into the case.
BeatNavy
Sep 6 2019, 03:50 PM
Thanks for the ideas.
QUOTE(Superhawk996 @ Sep 6 2019, 05:17 PM)

How many miles are on it? Even if only a few miles, I've never seen that much crank pressure even before break in to have oil coming out the fill neck / breather assembly.
Right now I've got only about 65 miles on it.
QUOTE(Superhawk996 @ Sep 6 2019, 05:17 PM)

When you say you didn't gap the rings, I'm assuming you mean ring end gaps. Do you at least know what the end gaps were when you built it?
Correct, ring end gaps. I don't have it written down in my notes but I seem to recall gaps being roughly 15 thousandths or thereabouts. I really debated whether to gap them further, but deferred to Jake's philosophy.
QUOTE(Superhawk996 @ Sep 6 2019, 05:17 PM)

Likewise, did you stagger the ring gaps between top, middle, and oil scraper rings? If all of those ring gaps are lined up, that could be a source of too much blow by.
Yes, definitely tried to stagger the gaps.
QUOTE(Superhawk996 @ Sep 6 2019, 05:17 PM)

Likewise you could potentially do a leakdown test and see if you have cylinders that aren't sealed and blowing into the case.
Good point. I don't have a leakdown tester, but that may change.
HAM Inc
Sep 6 2019, 04:46 PM
Rob try this. Remove the oil filler cap and fashion a plastic water bottle bottom to fit over the filler that you can tape in place. Before you tape it in place drill a 3/4" hole in it. This is more than enough breather for a 8000 rpm race engine.
Drive it and it and see if the leaks go away. If they do then the pcv system isn't enough ventilation, at least not while you're breaking in the engine.
Once everything is broken in crankcase pressure shouldn't be that high. A properly functioning PCV system should handle it. But maybe not. This trick will tell you.
I would zip tie a clean shop rag over the assembly, over the opening.
You can fool around with different size openings in the plastic bottle to see what size breather you need from the chimney, which is baffled by design and is the highest point on the engine.
Breath the engine from the highest point, locate sump pick up at the lowest point. Pretty basic engine theory.
Superhawk996
Sep 6 2019, 04:54 PM
0.015 ring end gap is great. Factory manual is 0.014" - 0.022". I definitely wouldn't have gapped them further either.
Buy (or make) a leakdown tester. probably your best bet to ID where it is blowing by. By 65 miles you should have enough break in to not be seeing these types of crank pressure issues.
On the rear main seal leak. Did you use a new flywheel? I've had issues in the past with the flywheel being worn such that a new seal still can't seal properly due to groove/taper wear in the sealing surface. The other possibility is a cocked installation of RMS or folded seal lip.
When you say leaking at the filler neck. Is that at the base of the breather? You do have the case to breather gasket in there right?
I'm so sorry you're going through this.
Are the head vents welded or plugged? I just bought a set of Len's AA 2.0L heads and they are threaded. if just plugged with a tapped plug, you could pull the plugs, install barbed fittings, route hoses to an EMPI breather and see if the situation improves. However, I would fear that is just a band aid even if it did improve.
Superhawk996
Sep 6 2019, 04:55 PM
Great suggestion Len! Simplicity. I love it!
Olympic 914
Sep 6 2019, 05:07 PM
Regarding KB pistons ring gap. They recommend a larger top ring gap.
http://www.hughesengines.com/TechArticles/...cticpistons.phpAlso I suspected a RMS leak and it was one of the oil galley plugs I had put in.
BeatNavy
Sep 6 2019, 05:12 PM
QUOTE(Superhawk996 @ Sep 6 2019, 06:55 PM)

Great suggestion Len! Simplicity. I love it!
So do I! Good stuff, Len, thanks. Just to be clear (and because I'm stupid), I should leave the top of the water bottle off but cover it all with a rag to keep oil from spraying around, correct?
The flywheel was resurfaced, and I used a fine sand paper, like emory paper, to polish the surface where the RMS runs.
On the oil filler, I definitely have the gasket. I ended up putting Dirko on it to try to seal it in place, thinking that may be the issue. I don't actually SEE oil spraying, but it collects all over the top of the engine and on the flanges of the oil filler. I changed oil filler caps thinking maybe I had one that wasn't sealing.
Heads are threaded.
HAM Inc
Sep 6 2019, 05:27 PM
QUOTE(BeatNavy @ Sep 6 2019, 04:12 PM)

QUOTE(Superhawk996 @ Sep 6 2019, 06:55 PM)

Great suggestion Len! Simplicity. I love it!
So do I! Good stuff, Len, thanks.
Just to be clear (and because I'm stupid), I should leave the top of the water bottle off but cover it all with a rag to keep oil from spraying around, correct?
The flywheel was resurfaced, and I used a fine sand paper, like emory paper, to polish the surface where the RMS runs.
On the oil filler, I definitely have the gasket. I ended up putting Dirko on it to try to seal it in place, thinking that may be the issue. I don't actually SEE oil spraying, but it collects all over the top of the engine and on the flanges of the oil filler. I changed oil filler caps thinking maybe I had one that wasn't sealing.
Heads are threaded.
Yes. The rag is to filter oil vapor exiting the crankcase and filter air moving into the crankcase. Crankcase pressures pulse from negative to positive with every crank revolution.
It doesn't have to be the cut off bottom of a water bottle. I just used that example to illustrate the concept. You can make the thing out of anything that you can drill a hole in and get taped and sealed tight to the filler neck. If you had a junk oil filler cap you could drill a hole in it. That would be the easy button.
rhodyguy
Sep 6 2019, 05:32 PM
Is the PCV valve functional?
Superhawk996
Sep 6 2019, 05:37 PM
I just gotta ask on other question that I've assumed.
When you installed the rings, there is usually one side marked Top that goes toward the piston crown.
Hoping that you installed with ring oriented top/bottom correctly.
Even if rings were pre-installed on pistons as they usually are, you can usually shift them side to side and see the Top mark.
NOTE: that is interesting on KB pistons. I was not aware that they specify that large of an end gap.
BeatNavy
Sep 6 2019, 06:04 PM
Yeah, interesting on the KB pistons. Hmmm....hope that's not an issue.
Good point on the RMS versus galley plug. I did install galley plugs, so that's certainly a potential point of failure.
I did mind which way the rings were installed (oriented up/down). They were not actually preinstalled, and I double/triple checked proper orientation.
Thanks, Len. I'll give that a shot and see what happens.
Edit: Yes, sorry Kevin. PCV is functional. I can still taste oil on my lips from testing it
BeatNavy
Sep 9 2019, 04:07 PM
Just to follow up on this. I tapped a hole in the oil filler, threaded a fitting in it, and connected it with vacuum hose to air cleaner t reduce crankcase pressure. I also realized that I'm missing a sealing ring on my oil filler neck. Not the cork gasket, but there is a sealing gasket below the oil filler. Comparing with one from my other engine, I realized that must be part of the issue, so I swapped oil filler housings.
Right now the oil leaks on top have stopped. Some combo of relieving crankcase pressure, making sure the oil filler was sealed, and/or rings seating seem to have helped. I don't see anything really bad underneath, and I am now thinking at least part of the oil under the case was actually leaking from on top.
Now I still have three outstanding issues to deal with:
1. Oil temps seem fairly high (240-ish after 15 minutes of driving, with ambient temps around 80). I can see a freshly rebuilt engine having tighter tolerances contributing to higher temps. Anyone have thoughts on that?
2. Can won't idle cold. Idles too low to the point of stalling until head temps get over 240 or so. AAR is working. Need to figure this out best I can.
3. Exhaust leak, probably at heads. Need to redo these, and it may be part of my issue(s) above. Not sure I trust my AFR readings at idle if I have an exhaust leak.
Thanks to Len and everyone else for thoughts on this
Superhawk996
Sep 10 2019, 06:18 PM
Try this trick for item #3. Anneal the copper exhaust gaskets for a better seal.
Heat to dull red with torch, drop in water. Now you have a dead soft copper exhaust seal that will deform nicely to the heat exhanger pipe. Still need to make sure pipe mating surface is reasonably squared and snugged in all the way but soft copper seal will help a bit.
Don't go crazy over tightening the exhaust studs trying to pull a poorly fitting or cocked heat exchanger flange home. That doesn't end well. Ask me how I know.
Superhawk996
Sep 10 2019, 06:24 PM
On item #1, oil temp gauge or temp sensor could be offset by 10F or more degrees.
IR temp check the case sump immediately upon shut down as a 2nd check or if you have access to a Fluke thermocouple reader, I'd drop thermoucouple down the dipstick tube into the oil to get a 2nd data point to check the gauge accuracy.
BeatNavy
Sep 10 2019, 07:05 PM
QUOTE(Superhawk996 @ Sep 10 2019, 08:18 PM)

Try this trick for item #3. Anneal the copper exhaust gaskets for a better seal.
Heat to dull red with torch, drop in water. Now you have a dead soft copper exhaust seal that will deform nicely to the heat exhanger pipe. Still need to make sure pipe mating surface is reasonably squared and snugged in all the way but soft copper seal will help a bit.
Don't go crazy over tightening the exhaust studs trying to pull a poorly fitting or cocked heat exchanger flange home. That doesn't end well. Ask me how I know.

Good stuff, yes, thanks. In the past I have annealed the rings with good results, but I did not do that this time. Don't ask me why (ok, I was "in a hurry"...to do it half-assed). I did the shop vac blower test which has also worked for me in the past. Sure enough, HE on 1/2 side was leaking big time. Waiting for new exhaust nuts to arrive.
QUOTE(Superhawk996 @ Sep 10 2019, 08:24 PM)

On item #1, oil temp gauge or temp sensor could be offset by 10F or more degrees.
IR temp check the case sump immediately upon shut down as a 2nd check or if you have access to a Fluke thermocouple reader, I'd drop thermoucouple down the dipstick tube into the oil to get a 2nd data point to check the gauge accuracy.
Good idea. Buying an IR thermometer now.
Superhawk996
Sep 10 2019, 07:21 PM
Good luck! If heat exchanger 1/2 was leaking a lot, that is dumping 1600F exhaust gas right out onto your heads and could help explain the elevated oil temp a bit.
Keep us posted. Don't give up!
BeatNavy
Sep 16 2019, 02:48 PM
Ok, small update. It took a frustratingly long time to get proper exhaust nuts shipped to me. Got the 1/2 side HE installed again after annealing the exhaust rings. Before tightening the nuts up, I tested again with the shop vac technique. I think I'm good with no leaks now.
Took it out for spirited driving. It runs great, although I'm still hearing what I think is detonation under hard load between 2800 and 3200 RPM. My variable timing light is giving me fits -- it won't fire, so I'm using the standard timing light which makes it harder to determine where timing really is (anyone else have issues with a timing light and 1-2-3 distributor?). I'm already running premium fuel with CR calculated at 8.6. Maybe it's something else rattling.
Oil temp hit 240+ on my gauge with ambient temps at 90. Although I did buy an IR thermometer. Pointing it at the tuna can sump and it read more like 200+ degrees. It's possible I didn't match the sending unit to the gauge correctly even though I tried to. Should I trust the IR reading more?
Lastly, oil leaks are better, although I've got a persistent one that seems to be coming either from the oil filter console or the pressure relief valve. I think I need to reinstall that sealing ring and tighten it up to see if that relieves it.
Cold idle is still non-existent. Need to work on that too. Maybe try a different AAR although I know the one I'm using is at least mostly functional.
Progress, but it takes a ton of time to fine tune this bugger!
Frank S
Sep 17 2019, 02:47 PM
Progress, but it takes a ton of time to fine tune this bugger!
[/quote]
Went through this with two different engine combos, latest with same combo you are running.
Much easier and faster if you measure what you adjust.
If you hook up a vacuum gauge, using a T-Piece in front of the MPS and route the hose to the gauge, it's pretty easy to adjust the MPS, as you can clearly see in which region you are running (part load, transition, or full load).
Tune for drive ability first, then start to play with idle settings (ignition timing and maybe recalibration of AAR)
Click to view attachment
BeatNavy
Sep 17 2019, 03:53 PM
Thanks, Frank. Good points. The knocking/detonation thing is perplexing me a bit. Tried adjusting the MPS a little richer at WOT to see if that would help, but there was still some under heavy load. Still need to fiddle more with timing, I guess, but I either need to fix my advance timing light or buy a new one. Also entertaining buying a cooler range of spark plug. Anyone have thoughts there?
Good news is oil leaks are significantly better, and the engine gives nice power - a lot of fun to drive

and the weather is looking NICE for the next few days.
worn
Sep 17 2019, 06:47 PM
[quote name='Frank S' date='Sep 17 2019, 12:47 PM' post='2747922']
Progress, but it takes a ton of time to fine tune this bugger!
[/quote]
Went through this with two different engine combos, latest with same combo you are running.
Much easier and faster if you measure what you adjust.
If you hook up a vacuum gauge, using a T-Piece in front of the MPS and route the hose to the gauge, it's pretty easy to adjust the MPS, as you can clearly see in which region you are running (part load, transition, or full load).
Tune for drive ability first, then start to play with idle settings (ignition timing and maybe recalibration of AAR)
Click to view attachment[/quote]
Wow. I thought i was the only one driving with a lot of gauge data input. Looks pretty cool.
Frank S
Sep 18 2019, 03:32 AM
Also entertaining buying a cooler range of spark plug. Anyone have thoughts there?
[/quote]
I'm running NGK BP6RES and they are looking good.
Regarding the timing, I run a programmable system.
Idles fine between 10 and 12° BTDC with maximum advance of 27° BTDC from 3000 RPM onwards.
Had plans to adjust timing on a dyno, but next winter project is to update the engine with a DIY Stealth Megasquirt system, so I never tried to run more advance, I know Jake recommends 28° BTDC but the engine is running cool and strong as it is and I will put it on the Dyno after the upgrade...
Frank S
Sep 18 2019, 03:39 AM
Wow. I thought i was the only one driving with a lot of gauge data input. Looks pretty cool.
[/quote]
Hard to adjust something you can not measure. This is a easy and in-expensive way to tune it quick. Don't need more than 3 hours to adjust it perfect like this. Its a bid of effort to install the unit, but at the end of the day it's saving a lot of time...
Superhawk996
Sep 18 2019, 05:20 AM
[quote name='Frank S' date='Sep 17 2019, 04:47 PM' post='2747922']
Progress, but it takes a ton of time to fine tune this bugger!
[/quote]
Went through this with two different engine combos, latest with same combo you are running.
Much easier and faster if you measure what you adjust.
If you hook up a vacuum gauge, using a T-Piece in front of the MPS and route the hose to the gauge, it's pretty easy to adjust the MPS, as you can clearly see in which region you are running (part load, transition, or full load).
Tune for drive ability first, then start to play with idle settings (ignition timing and maybe recalibration of AAR)
Click to view attachment[/quote]
@Frank S
How about posting about your center console setup? Looks interesting.
BeatNavy
Sep 18 2019, 05:21 AM
QUOTE(Frank S @ Sep 18 2019, 05:39 AM)

Hard to adjust something you can not measure. This is a easy and in-expensive way to tune it quick. Don't need more than 3 hours to adjust it perfect like this. Its a bid of effort to install the unit, but at the end of the day it's saving a lot of time...
Yeah, that looks interesting, and I may try to set something similar up. I like the data, if for no other reason to help understand how things work. Need to find my vacuum gauge and enough correct size vacuum line.
It's also helping me that I have three working MPS's: one stock, that I use as a baseline for measurements, and two that I can tune and swap in and out to see the effects.
Frank S
Sep 18 2019, 10:30 AM
How about posting about your center console setup? Looks interesting.
[/quote]
Don't want high jack this thread...
But here you go:
Slightly modified last winter. Moved Oil Temp Gauge up into the instrument cluster.
Here from top down:
Innovate LC2 Lambda Gauge, modified and fitted into original instrument housing.
CHT Gauge.
Oil Pressure Gauge, new style fitted also into original instrument housing.
Original Voltmeter Gauge.
Click to view attachment
Frank S
Sep 18 2019, 10:31 AM
QUOTE(Frank S @ Sep 18 2019, 06:30 PM)

How about posting about your center console setup? Looks interesting.
And here the Vacuum Gauge I use for MPS tuning purpose only:
Click to view attachment
Frank S
Sep 18 2019, 10:43 AM
QUOTE(BeatNavy @ Sep 18 2019, 01:21 PM)

QUOTE(Frank S @ Sep 18 2019, 05:39 AM)

Hard to adjust something you can not measure. This is a easy and in-expensive way to tune it quick. Don't need more than 3 hours to adjust it perfect like this. Its a bid of effort to install the unit, but at the end of the day it's saving a lot of time...
Yeah, that looks interesting, and I may try to set something similar up. I like the data, if for no other reason to help understand how things work. Need to find my vacuum gauge and enough correct size vacuum line.
It's also helping me that I have three working MPS's: one stock, that I use as a baseline for measurements, and two that I can tune and swap in and out to see the effects.
Rob, as you are running exactly same CR then I do, here my MPS adjustments:
0.83H @ 15 inHG
1.37H @ 4 inHG
1,57H @ 0 inHG
Maybe this will help to find a base line.
BeatNavy
Sep 18 2019, 03:24 PM
This is excellent information, thanks Frank. Have you ever measured the numbers for a stock 2.0 MPS to baseline your meter? I have noticed that my inductance meter reads the stock MPS significantly lower than what Brad Anders publishes on his website (I know there may be some debate about those numbers, but that's all we have publicly, anyway).
So if I assume your inductance meter would measure the stock MPS (e.g., 043) like Anders, then:
1.
15 inHG. Stock: .71, Yours: .83 (17% higher)
2.
4 inHG. Stock: 1.18, Yours 1.37 (16% higher)
3.
0 inHG. Stock: 1.39, Yours 1.57 (13% higher)
I may be able to extrapolate with mine and see how that runs.
By way of comparison, a non-molested stock 043 that I have measures as follows:
1. 15 inHG: .7
2. 4 inHG: 1.03
3. 0 inHG: 1.20
It may be my cheap inductance meter, but I can work based on your numbers.
Didn't get a chance to work on the car today
Superhawk996
Sep 18 2019, 03:42 PM
In Franks case I assume he is using the lambda to adjust the MPS and not just relying on MPS inductance. That is why I wanted to see his console better. Am I correct - tuning to lambda?
@Frank S
BeatNavy
Sep 18 2019, 03:58 PM
Yeah, I think you do both. You can't just go on MPS numbers, but they are a good starting point, and you fine tune based on what your O2 sensor, and your engine, is telling you.
Superhawk996
Sep 18 2019, 04:06 PM
In your case do you have a wideband lambda sensor to tune to or are you flying seat of the pants?
BeatNavy
Sep 18 2019, 04:32 PM
I do. I didn’t really trust it when I had an exhaust leak, though. I’m also not sure how much I trust what I see with the wideband. That’s why Frank’’s vac gauge setup looks interesting.
Frank S
Sep 19 2019, 01:48 AM
QUOTE(BeatNavy @ Sep 18 2019, 11:24 PM)

This is excellent information, thanks Frank. Have you ever measured the numbers for a stock 2.0 MPS to baseline your meter? I have noticed that my inductance meter reads the stock MPS significantly lower than what Brad Anders publishes on his website (I know there may be some debate about those numbers, but that's all we have publicly, anyway).
So if I assume your inductance meter would measure the stock MPS (e.g., 043) like Anders, then:
1.
15 inHG. Stock: .71, Yours: .83 (17% higher)
2.
4 inHG. Stock: 1.18, Yours 1.37 (16% higher)
3.
0 inHG. Stock: 1.39, Yours 1.57 (13% higher)
I may be able to extrapolate with mine and see how that runs.
By way of comparison, a non-molested stock 043 that I have measures as follows:
1. 15 inHG: .7
2. 4 inHG: 1.03
3. 0 inHG: 1.20
It may be my cheap inductance meter, but I can work based on your numbers.
Didn't get a chance to work on the car today

Hi Rob, good points!
I was working with a cheap inductance meter in the beginning too and decided later to buy a expensive one as the cheap one simply couldn't do the job.
To be clear about the whole Set Up, I'm using a 043 ECU in combination with the MPS values. From my memory you are running the same Set Up.
Stock non-molested 043 MPS values I've measured are:
15 inHG: 0.75
4 inHG: 1.21
0 inHg: 1.49
Frank S
Sep 19 2019, 01:56 AM
QUOTE(Superhawk996 @ Sep 18 2019, 11:42 PM)

In Franks case I assume he is using the lambda to adjust the MPS and not just relying on MPS inductance. That is why I wanted to see his console better. Am I correct - tuning to lambda?
@Frank S
I'm tuning for Lambda. But by using the vacuum gauge you have a much better idea what adjustments are needed.
Just to provide an example driving up a slight slope in 4th gear with contstant throttle at 4000 RPM, I thought I might be already in a engine load situation where the full load diaphragm is active, but with the Vacuum gauge you can clearly see, that you are still far away from the transition point (so it's still the main mixture screw sou have to adjust).
As I also have more than one MPS I measured the values after final tuning, like this it was easier to adjust the other MPS units.
Mark Henry
Sep 19 2019, 11:46 AM
On the RMS leak always give the oil the sniff test.
There's a chance it's tranny oil, input main shaft seal, which has a distinctive smell.
BeatNavy
Dec 18 2019, 04:51 PM
Ok, circling back on this to add to the 914World knowledge base.
About 6 or 7 weeks ago I was having more trouble starting (and restarting) the car. Finally broke down and did a compression test. Based on the results, I pulled the engine and here's what I had:
Click to view attachmentYES! Special compression rings that have TWO gaps, not just one!
Ok, yes -- cylinder #1 had not just one but two broken compression rings. I probably broke at least one when I installed piston in the cylinder a while back. I had cold compression numbers of roughly 60 on #1 and more like 140+ on the others. The broken rings could explain a lot, including elevated oil temps and oil leaks due to all the blow-by.
Anyway, I dropped the engine and pulled the heads. I replaced the broken rings and also re-gapped all the #1 rings based on KB's guidance that Tom pointed out in an earlier post in this thread. Also put installed a new RMS (although the old one probably wasn't really bad). Most of the time over the last 6 weeks was spent cleaning up the underbody like I've been meaning to do for years -- removing / replacing undercoating, fixing isolated rust spots, and repainting engine bay and underside of trunk. What a LOT of work, and dirty too
Finally got the engine back in today, and got her fired up! Too early to say all my drivability and oil temp/oil-leak problems are solved, but I am encouraged so far, and glad to be back on the road (with a nice clean underside)
Several lessons learned:
1. When chasing your tail, break down and do a compression test earlier rather than later. I don't know why I tend to avoid it - it's only a minor PITA but can give good info.
2. I went with Jake's advice on ring gapping (go with out of the box gap) -- which is fine,
unless the manufacturer of the product engineered something different. Read the (****) instructions.
3. A type 4 can run surprisingly well on less than 4 full cylinders.
4. This came in handy both for engine drops/installs and installing the HE's and exhaust -- basically just lifted everything in place. If you have a lift and do lots of engine drops, you may want to treat yourself to something like this if you haven't already:
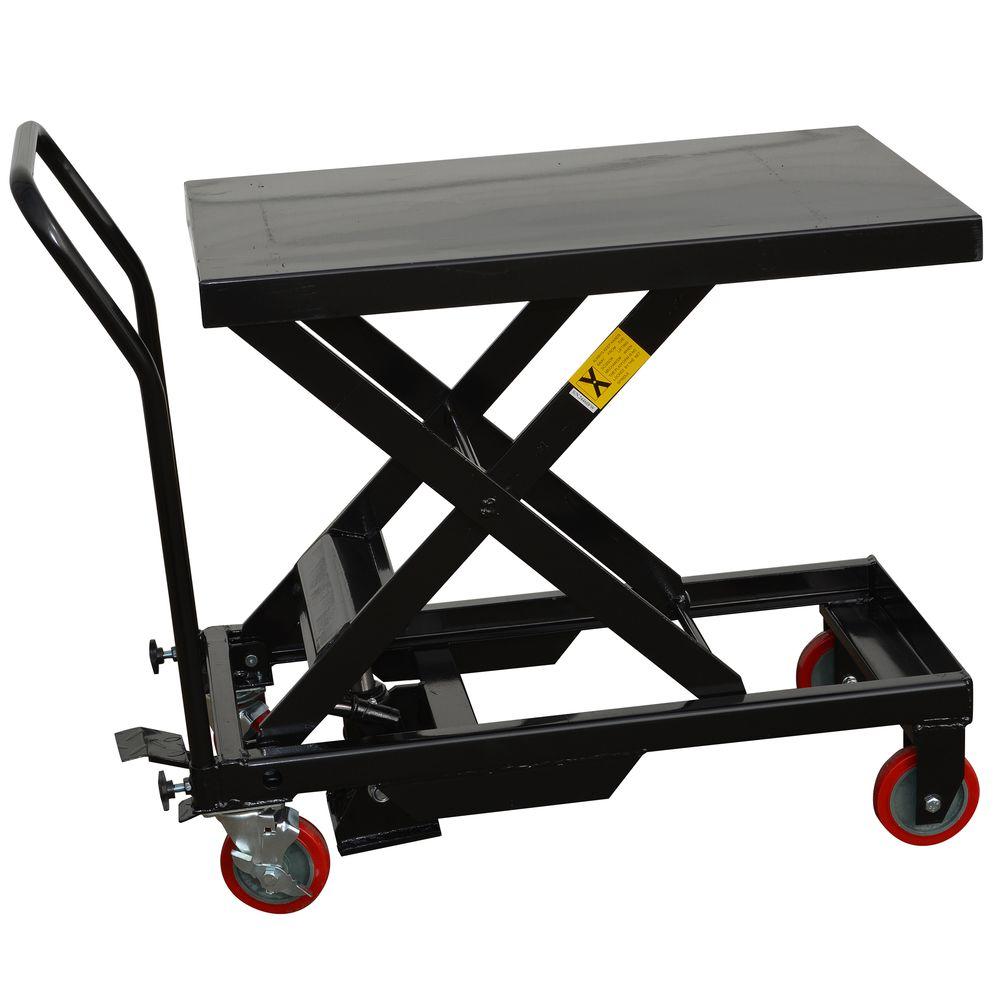
5. Even with a scissor lift and that cart, pulling the engine is still a PITA. Hope I'm done for a while.
Thanks for everyone's help. I'll post more when I get a chance to road test it more. In the meantime, here's my cleaned up butt (it's ok, you can look at it). Not perfect, but much better than before.
Click to view attachment
Superhawk996
Dec 18 2019, 05:28 PM
Wow.
That's a lot to digest. Thanks for posting and closing the loop and adding to the knowledge base. I was following this thread a while back and was curious what came of things.
I know it sucks to post when we've done stupid things. I have my own version of this coming shortly. But we all learn collectively from the success and sometimes failures of others.
Underbody looks immaculate. Nice Job.
Dion
Dec 18 2019, 05:55 PM
Special rings! :—) Heheheh, Uggh. Glad you found the issue Rob. Hope you work your way through more details successfully. Car chassis looks great underneath. Happy you have a running engine .
rhodyguy
Dec 18 2019, 05:59 PM
Putting a floor jack under each control arm will get the chassis way up. Angle the jacks and you can do it alone. With the drivetrain out the rear springs hardly compress. Put dunnage under the jacking donuts. Leave the muffler off.
Olympic 914
Dec 19 2019, 08:06 AM
BeatNavy
Dec 19 2019, 08:31 AM
QUOTE(Olympic 914 @ Dec 19 2019, 09:06 AM)

Tom, good stuff. I recall reading that article that's linked there.
Interesting, in your thread, you say instructions weren't included with the KB pistons. I don't think mine were either. To be fair (to me), I generally DO read instructions (if they are included). To be fair (to them), I have to believe one or both rings probably broke during initial install - my own lack of experience. If that's the biggest and really only mistake I made on my first T4 build, I'll be happy. It didn't require splitting the case.
Superhawk996
Dec 19 2019, 08:43 AM
QUOTE(BeatNavy @ Dec 19 2019, 09:31 AM)

To be fair (to them), I have to believe one or both rings probably broke during initial install - my own lack of experience. If that's the biggest and really only mistake I made on my first T4 build, I'll be happy. It didn't require splitting the case.
What did you use for a ring compressor? Really should be little risk of breaking a ring on install. Shouldn't take much effort at all to slide the piston into the cylider. If it hangs up for any reason, stop.
I've had terrible luck with those U shaped compressors. Junk in my opinion.
I use a Lisle spring steel compressor that encompasses the whole piston. I've never had any issues using this type.
https://www.lislecorp.com/specialty-tools/ring-compressor-79Use lots of oil, lube the ID of the spring compressor, and the piston should slide right in with only light taps from the wooden end of a mallet on the cylinder and/or a slight twisting motion (hard to get on VW's on the stud

) My compressor has 3 or four little nubs on the bottom side to sit on the top/bottom (for VW's) of the cylinder and keep the compressor from moving into the cylinder as you tap. A bit trickier with VW's going in from the bottom. They also offer a slick VW style "Take Apart" version. I just make do with mine and take it uncoil it to a large OD that will slip over the cylinder after the piston is in. A bit of a PITA but it works.
I might just buy one of the Lisle take aparts this next trip around given the cost isn't that high but somehow I've always made do with the other one both for VW's, for the Norton, for an old Honda motorcycle engines, etc.
https://www.lislecorp.com/specialty-tools/t...ring-compressorThe other trick that works in a pinch on small OD pistons is a very thin aluminum sheet (i.e. pop can) and a hose clamp. I believe the trick is to get complete encirclement of the ring so there is nothing to catch the cylinder lip as the piston/ring enters the bore. That is what the U shapped compressors lack.
BeatNavy
Dec 19 2019, 08:52 AM
QUOTE(Superhawk996 @ Dec 19 2019, 09:43 AM)

QUOTE(BeatNavy @ Dec 19 2019, 09:31 AM)

To be fair (to them), I have to believe one or both rings probably broke during initial install - my own lack of experience. If that's the biggest and really only mistake I made on my first T4 build, I'll be happy. It didn't require splitting the case.
What did you use for a ring compressor? Really should be little risk of breaking a ring on install. Shouldn't take much effort at all to slide the pison into the cylider. If it hangs up for any reason, stop.
I've had terrible luck with those U shaped compressors. Junk in my opinion.
I use a Lisle spring steel compressor that encompasses the whole piston. I've never had any issues using this type.
https://www.lislecorp.com/specialty-tools/ring-compressor-79Use lots of oil, lube the ID of the spring compressor, and the piston should slide right in with only light taps from the wooden end of a mallet. My compressor has 3 or four little nubs on the bottom side to sit on the top of the cylinder and keep the compressor from moving into the cylinder as you tap.
I used some generic, cheaper version of that one in your link. It works fine except it is a little tricky at first -- you really need to push down on it (on the top of cylinder) to make sure you have an even seal all the way around while tightening and installing. If you don't, one of the oil scrapers or compression rings might catch an edge. Might also have been exacerbated by the smaller ring gaps I initially had. That may have been my problem the first go-round. After the re-gapping everything went in much easier.
Yes, if you encounter a hang-up, stop and start over. Good advice!
This is a "lo-fi" version of our main content. To view the full version with more information, formatting and images, please
click here.