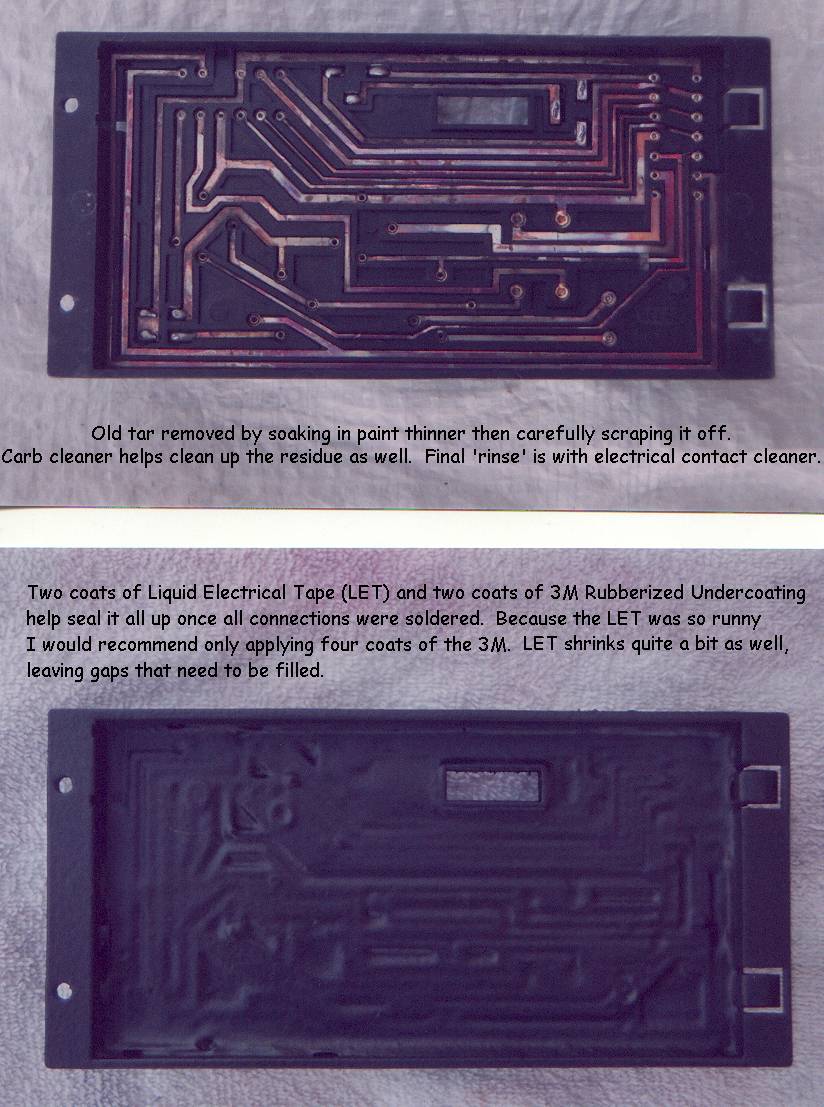
Mine showed only a couple cracks in the tar bottom and I'm sure I could've easily patched them but I wanted to see if recoating was easy. It is, just messy and I recommend wearing nitrile or latex gloves. The LET shrinks considerably. One container will be more than enough for two coats and left overs for later wiring projects. The 3M undercoating sprayed on easily and did not shrink. Several coats of that would probably be fine. I hesitated using RTV because I thought I read somewhere that it may be slightly acidic on some metals and I didn't want to risk having my copper strips and soldered joints disappearing on me one day while driving.
If anyone else has done this differently I would like to hear about it, be is successful or not. Mine was successful (short term at least

