---------Updated test results----------
Second experiment-
This time I submersed my 2 CHTs with the VDO CHT and a digital thermometer in cooking oil in a crock pot. I left the crock pot on for the entire experiment and stirred the pot before each reading.
Here's the chart:
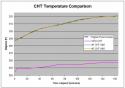
------------------------------------------
So, I've had some trouble with CHTs being too high in racing conditions. I've worked and reworked the cooling system a number of times. But the CHTs are still too high. That's led us to question the readings I'm getting from my system.
Currently I have a CHT sender under plug #1 and #3 and they connect to my AIM data logger. Jake suggested I get a VDO CHT guage to compare the two readings.
So, I put the VDO CHT spark plug ring on top of my #1 CHT for the data logger and screwed the plug into the head and started the engine. The #1 CHT reads "T3" on the data logger display.
I took several pictures as the engine warmed up and cooled off.
First picture:

1 minute later:
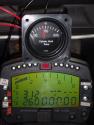
11 minutes later: (engine still on)
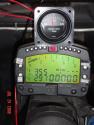
17 minutes later.... engine off now:
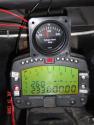
35 minutes later... engine off:
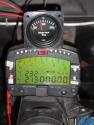
100 minutes after the first pic:
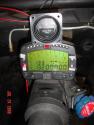
Here is a pic of the sender that I use with the data logger:
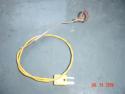
It sure seems like the VDO guage has a significant delay associated with it's display. I'm not sure I can conclude that my system is telling me the wrong temperature, but I can conclude that the two systems have very different reaction times.