yeahmag
Feb 2 2012, 12:49 AM
Installed crank, gears, cam, and rods. Dry fit CB's dry sump pump and modified the tang and clearanced drive tang boss.
Click to view attachment
EdwardBlume
Feb 2 2012, 01:01 AM
QUOTE(yeahmag @ Feb 1 2012, 10:49 PM)

Installed crank, gears, cam, and rods. Dry fit CB's dry sump pump and modified the tang and clearanced drive tang boss.
Click to view attachment
ThePaintedMan
Feb 2 2012, 06:43 AM
Cool! Wish I had the guts to attempt a rebuild. One day!
jaxdream
Feb 2 2012, 09:06 AM
Will the fan housing bolt up / clear the new pump ?? Or are using another cooling option ?? Looks good !!!
Jack
mrbubblehead
Feb 2 2012, 09:52 AM
what are you going to do about your engine mounts?
yeahmag
Feb 2 2012, 10:46 AM
I will need to modify the fan housing to clear the oil pump. I will also have to custom make some motor mounts.
mrbubblehead
Feb 2 2012, 03:55 PM
you are one step ahead of me. i am doing the same as you. same pump also.....
i just finished all my case mods, and concentrating on building my sump tank.
did you hav to grind your cam bolts? do you remember how much you took off the snout of the pump?
i am going to use tangerine racing's horizontal fan set up, so my engine mounts shouldnt be a problem.
yeahmag
Feb 2 2012, 04:01 PM
I ground about 2mm off that pump. Maybe more. I also made the tang have some angle at the end like the stock tangs. I made the tang length match the one I got from Raby years ago. I took a bit off the boss holding the drive tang to make sure it was clear of the cam. I probably took off 1mm at most on the boss.
I did grind my cam bolts to be safe, but I probably didn't have to with the ones Jake sent me.
What case mods did you do?
mrbubblehead
Feb 2 2012, 04:16 PM
since im not using the stock oil cooler or stock oil filter i took them out of the circuit. i also welded up the relief holes and took both relief system out of the circuit also.
yeahmag
Feb 2 2012, 04:19 PM
How are you routing the oil for the pressure stage? The galley from the pressure side of the pump goes right to the oil filter...
mrbubblehead
Feb 2 2012, 06:18 PM
i used this diagram
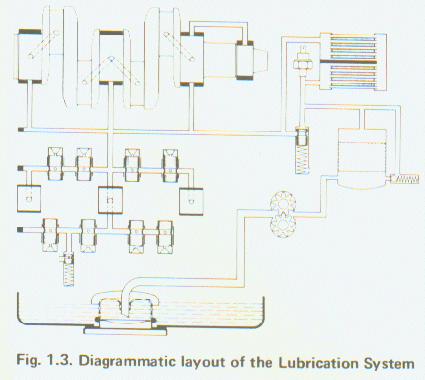
and modified it to this
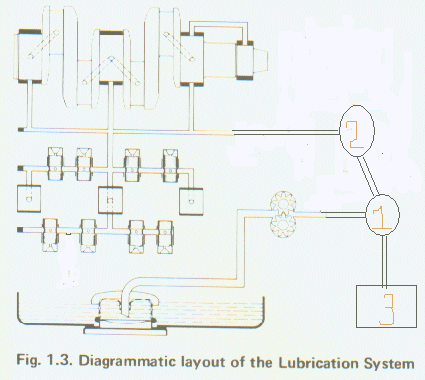
1. jaycee 3 port remote oil filter/relief @ 80 psi
2. remote oil cooler
3. sump tank
in my picture you can see i welded a fitting on the passage from the pump (where the old filter stand was)
then it goes thru the remote filter, oil cooler, and then straight to the mains via the oil cooler location. another welded fitting. i just cut of the the old cooler stand off the case.
yeahmag
Feb 2 2012, 09:41 PM
Here are pictures of the pistons after going through the ultrasonic cleaner and then me balancing them. I used a 1g scale, a 1/2" drill bit, and an air powered angle grinder with a small sanding disk (just to clean up any sharp edges). The all are at 570g now. They were as much a 3g out. Weights ranged from 570g to 573g.
Click to view attachment Click to view attachment
Valy
Feb 2 2012, 11:20 PM
QUOTE(mrbubblehead @ Feb 2 2012, 04:18 PM)

i used this diagram
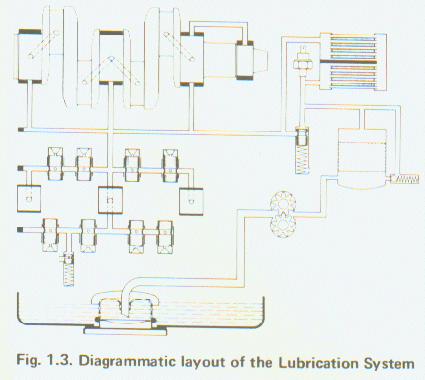
and modified it to this
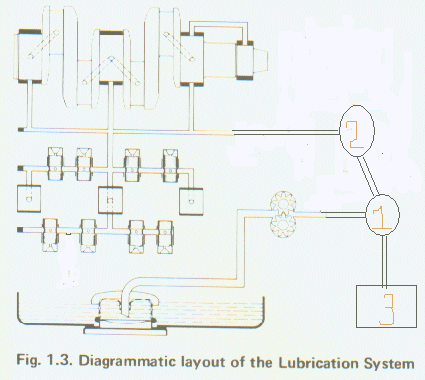
1. jaycee 3 port remote oil filter/relief @ 80 psi
2. remote oil cooler
3. sump tank
in my picture you can see i welded a fitting on the passage from the pump (where the old filter stand was)
then it goes thru the remote filter, oil cooler, and then straight to the mains via the oil cooler location. another welded fitting. i just cut of the the old cooler stand off the case.
So how do you pump oil out of the sump?
jmill
Feb 3 2012, 07:07 PM
I was thinking the same thing. Somehow youi need to get the oil in the tank to the suction side of the pump. All the dry sump systems I've seen have a scavenge and a pressure pump.
mrbubblehead
Feb 3 2012, 07:22 PM
QUOTE(jmill @ Feb 3 2012, 05:07 PM)

I was thinking the same thing. Somehow youi need to get the oil in the tank to the suction side of the pump. All the dry sump systems I've seen have a scavenge and a pressure pump.
i know, this diagram was just for me. i didnt draw them in because i know that the feed and return from the sump tank go to the oil pump. this diagram was to figure out how i was gonna get in and out of the case.
Woody
Feb 3 2012, 07:48 PM
You are going to love that engine.
mrbubblehead
Feb 4 2012, 04:18 PM
any more progress yeahman? do you know what you are going to use for a sump tank yet?
yeahmag
Feb 14 2012, 11:32 AM
Been cleaning parts like mad. Finally ready to close the case up after checking the fit of the drive tang and boss on the CB dry sump pump.
I also got around to modifying the oil filter housing. I used a slide hammer with a small, blind bearing pull attachment and removed the bypass system. I then cut an AL slug to fit and MIG'ed it in.
With regards to the tank, I'm using a very nice Patterson tank that Blake sold me. I'll be mounting it up front and trying to figure out how to mount an oil cooler up there too.
yeahmag
May 24 2012, 12:22 PM
OK. The long block is together and I'm starting on the valve train geometry. Here are some pic's:
Click to view attachment The head after using Ajax to lap the cylinders
yeahmag
May 24 2012, 12:23 PM
Click to view attachment After the copper spray to help with the carbon seal.
yeahmag
May 24 2012, 12:24 PM
Click to view attachment Long block together (more or less).
yeahmag
May 24 2012, 12:25 PM
Click to view attachment Ported the hell out of the CB Dry Sump Pump and made a custom engine bar bracket (which you can just barely make out).
yeahmag
May 24 2012, 12:26 PM
Click to view attachment Shot of the heads with Jakes "super" option. 911 adjusters, new 8mm studs, solid spacers, etc...
That's all for now!
Valy
May 24 2012, 01:39 PM
Those studs look to short to me.
And it looks to me that you need to shim the shafts more but that may be just the camera angle.
yeahmag
May 24 2012, 02:10 PM
The nuts are just there to keep the rockers from falling off if I space and turn the motor over on the stand. In that shot I had *not* started setting the geometry.
yeahmag
May 29 2012, 06:05 PM
Jake appears to like where I have my valve train geometry:
Intake: .438"
Exhaust: .412"
@ 50% lift adjuster and valve are perpendicular for both intake and exhaust.
1 full turn of adjustment available "in" available before bottoming out the foot with a .060" shim on the stands.
Click to view attachment Off to cut the pushrods!
yeahmag
Jun 6 2012, 12:19 PM
Measuring my pushrod tips using a flat table and a custom fixture made of fixture plate. Notice one of them differs by .002" - .003". Not sure if keying off the "flat" of the ball is valid, but still interesting to find one out of 8 with a variation.
Click to view attachmentClick to view attachment
Valy
Jun 6 2012, 03:40 PM
I would not measure them this way. Error is much higher than the 0.03" you measured, mostly because the dial-meter is probably not perfectly perpendicular to the table, the arm holding it has some elasticity and moves and you're measuring a round surface.
I suggest you take a micrometer and measure the rod head with the holding jig and then subtract the jig width.
yeahmag
Jun 6 2012, 04:14 PM
Nah... The rig is designed for telescopes and is on a flat table. The table is accurate to .001" across the *entire* surface and the tool plate is accurate to .001" across a 3' length. This micrometer rig is over $10K and I can't even guess what that huge hunk of rock of a table cost.
We surfaced the plate on the same flat table to be sure and then ran the tool plate under the micrometer to make sure there were no deviations.
7 of the 8 tips all came back within .001". Just one came back at .003" out. This was absolutely repeatable. I did first check them with calipers, but the end of the taper is not machined and made it impossible to hold a tolerance.
In an ideal world I would be measuring centerline to centerline of the ball and not keying off the flats at the end as I suspect they are not machined to a tight tolerance there.
yeahmag
Jun 6 2012, 04:16 PM
Here is a wider shot so you get a better feel for what we were doing.
Click to view attachmentThat's no kitchen counter top!!!
Valy
Jun 6 2012, 04:24 PM
The cost of the measuring equipment doesn't beat the physic laws

This is all you need. Cheep and more accurate than your big setup for this measurement. The finest dust particle at the base of your long arm will be distort your measurement big time.
yeahmag
Jun 6 2012, 04:42 PM
I don't want to debat this too much, but this simply isn't the case. The primary problem with the method you are suggesting is that ***in my case*** the bottom of the tip (opposite the ball) is not machined to any specific tolerance. Other tips from other vendors may be different.
Additionally, you can't measure from the shoulder to the flat on the tip with that tool as the ball is smaller than the shoulder. You would be measuring on an angle... Again, that's how my pushrods and tips are. Others may be different.
The rig I used was repeatable, which if nothing else shows me variances between parts. The micrometer and it's arm is stationary and the tip and tool plate was moved in and out. I imagine Carnegie would have a hell of a lot of telescopes not working if this guy didn't know what the hell he was doing...
But in my book, building these things is half the fun. Do what works for you! I can't remember what Jake always says, but it's something like, "...this is where you become the engine builder."
Valy
Jun 6 2012, 05:39 PM
QUOTE(yeahmag @ Jun 6 2012, 03:42 PM)

I don't want to debat this too much, but this simply isn't the case. The primary problem with the method you are suggesting is that ***in my case*** the bottom of the tip (opposite the ball) is not machined to any specific tolerance. Other tips from other vendors may be different.
Additionally, you can't measure from the shoulder to the flat on the tip with that tool as the ball is smaller than the shoulder. You would be measuring on an angle... Again, that's how my pushrods and tips are. Others may be different.
The rig I used was repeatable, which if nothing else shows me variances between parts. The micrometer and it's arm is stationary and the tip and tool plate was moved in and out. I imagine Carnegie would have a hell of a lot of telescopes not working if this guy didn't know what the hell he was doing...
But in my book, building these things is half the fun. Do what works for you! I can't remember what Jake always says, but it's something like, "...this is where you become the engine builder."
Well, you solved the problem of the not machined bottom tip with your little jig-plate and that's fine. You should have used that plate in a micrometer.
Anyway, it doesn't really make any difference as those tolerances can be compensated at the valve adjuster and the final lift difference is smaller than the deviation you measured.
And that deviation alone is not relevant. You need to measure the assembled valve train for meaningful results.
yeahmag
Jun 11 2012, 12:22 PM
This weekend I finished my valve train. I ended up somewhat redoing my rockers as originally I had ground them by hand on a grinding wheel (over 7 years ago!) and used a caliper to try and keep them square. Previously I was using Ford Courier style adjusters (captured ball), this wasn't good enough for the 911 adjusters...
I jigged them in the mill with a carbide ball end mill (to give a radius at the arm) and made them all *exactly* the same thickness as the thinnest of the group. That got all my adjusters where I wanted them to be. It's amazing how far some of them were off!
Pushrod tubes were assembled with Viton o-rings and a little Loctite-565. Finished up with a "loose zero" valve adjustment.
Things should start to come together fast now!
yeahmag
Aug 16 2012, 11:19 AM
While not quite part of the engine build I thought these interesting. Here is a picture of Chris' inner suspension console reinforcement piece all welded in:
Click to view attachmentLuckily the metal behind it was absolutely perfect. I was starting to get concerned due to running high spring rates (and wanting to go higher) along with DOT-R tires. Here it is painted:
Click to view attachmentWe did both left and right sides with a TIG and in addition seamed welded as much of the ear as we could reach.
yeahmag
Nov 5 2012, 11:47 AM
It's been quite a while, but I have been working! I've got all the holes drilled in the chassis for the scavenge side and am working on the return now. I also finally made the breather set up that enlarges the case breather (-10AN in my case) and blocks off the heads.
Click to view attachment
FourBlades
Nov 5 2012, 12:30 PM
Cool engine build!
John
yeahmag
Nov 5 2012, 04:59 PM
Forgot to show the port matching of the CB manifolds to the stock, 2.0 head gaskets...
Click to view attachment
yeahmag
Nov 25 2012, 09:07 PM
A few more... I have the scavenge line run up the passenger side, so it's time to get the oil cooler going. I got a Mercedes Benz oil cooler from Bruce and put a bend in it to match the curve of the front bumper. I then cut the original fittings off, welded them shut, and added -10AN fittings to the ends of the tank (vs. the face as original).
Click to view attachment Click to view attachment
yeahmag
Nov 25 2012, 09:08 PM
0396
Nov 27 2012, 09:00 AM
Cool engine build- oh thanks for the education too.
Cupomeat
Nov 27 2012, 09:44 AM
QUOTE(yeahmag @ May 24 2012, 01:25 PM)

Click to view attachment Ported the hell out of the CB Dry Sump Pump and made a custom engine bar bracket (which you can just barely make out).
Where does the engine bar bracket bolt into the case? Just the two lower bolts or does it mount in another place as well?
yeahmag
Nov 27 2012, 10:39 AM
Just the two lowers.
yeahmag
Dec 11 2012, 06:04 PM
Some craptastic iPhone photos of the progress. Passenger side scavenge side oil line run and the holes are drilled for the drivers side return. I still have to actually hook the lines up and clean up the install a bit.
Click to view attachment Click to view attachment
mrbubblehead
Dec 11 2012, 07:15 PM
looks good. what size is that? -8, -10?
yeahmag
Dec 11 2012, 07:31 PM
-10 on the scavenge side. -12 for most of the run, necking down to -10 at the very end for the return.
Gint
Dec 11 2012, 07:39 PM
Nice! When do you fire it?
pete-stevers
Dec 11 2012, 11:20 PM
how did you bend the oil cooler?
yeahmag
Dec 12 2012, 10:56 AM
I bent the cooler in a press supporting it with 2x4's and then another 2x4 perpendicular in the middle to distribute the load. It's not perfect, but should work.
Not real sure when I'll start it, I'm guessing early January.
914_teener
Dec 14 2012, 02:22 PM
QUOTE(yeahmag @ Dec 12 2012, 08:56 AM)

I bent the cooler in a press supporting it with 2x4's and then another 2x4 perpendicular in the middle to distribute the load. It's not perfect, but should work.
Not real sure when I'll start it, I'm guessing early January.
Nice work Aaron.....gotta get those cobwebs off the longs!
This is a "lo-fi" version of our main content. To view the full version with more information, formatting and images, please
click here.