I have encountered several problems however. First, my welding skills are extremely rusty and are proving quite challenging.
Second, I cut the hole out a bit too large so that the gaps are a bit more than the expected .040 inches I had hoped for.
Here's a picture of the damage:
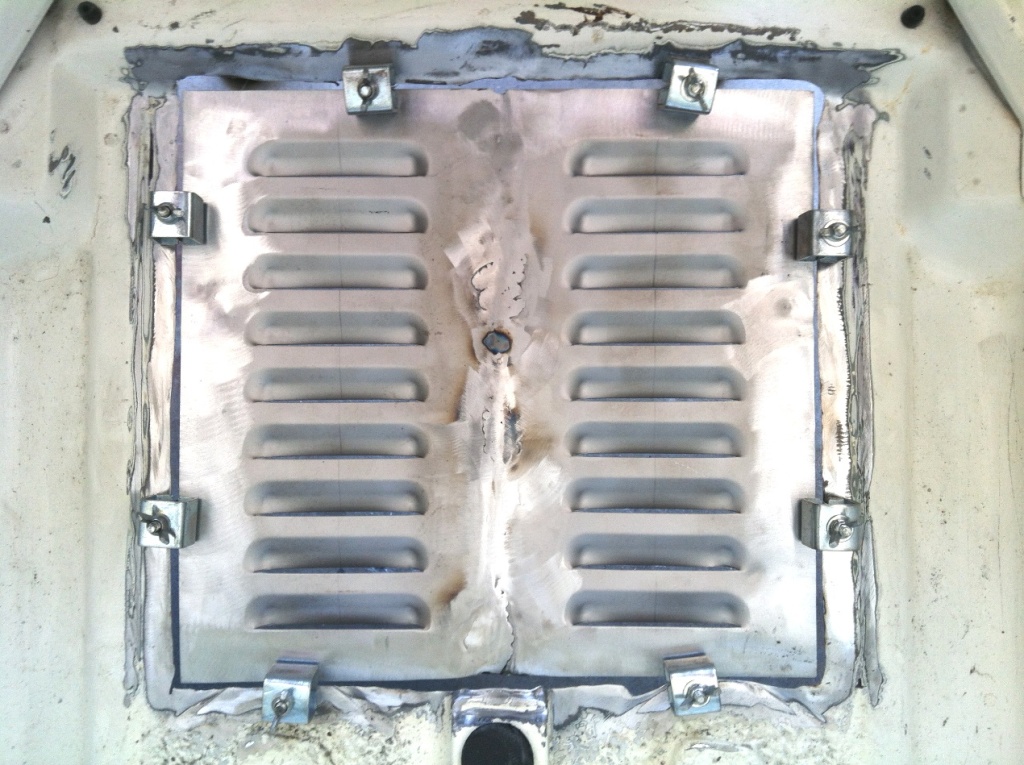
So here's my question. Should I simply start trying to tack the points I can easily tack and then fill in the big gaps with lots of welding wire? Or is there a better way to do this?
As usual, all advice is greatly appreciated in advance. Thanks.