FourBlades
Dec 17 2012, 10:14 PM
I have been thinking about learning to TIG weld for a few years and took the plunge.
I bought the Eastwood AC/DC unit and have been playing with it for a few weeks.
Click to view attachmentI did all the obvious learning stuff, watching you tube videos, reading about it.
I like WeldingTipsAndTricks.com videos.
At first I just could not see what was going on well enough so I bought a 3x magnifier for my helmet. I also had a lot of trouble with fogging so I got some FogTech drops which completely stopped the fogging. These tips made it a lot easier to see the arc and the puddle.
Now if I could just stop touching the tungsten to the puddle it would be nice.
I'd like to be able to TIG thin metal to limit heat input, do good roll bar welding, and make stuff from aluminum. I know this will take a lot of time and practice.
What tips really helped you, what practice exercises did you do, what war stories do you have?
Thanks,
John
stugray
Dec 17 2012, 10:43 PM
Some quick tips for you:
To learn control of the arc, you want a pedal start arc. Scratch start works for most of what we need, but is not the perfect thing to learn with.
I do not trust the electronic welding filters that turn dark once you strike the arc. Learn to use with the basics, not the "bling".
If you are doing really well, you can weld two aluminum cans (start with steel) and weld them end to end. If you can master that, you can do rusty steel exhaust pipe ;-)
Tig is all about laying down a stack of dimes as that is what the weld should look like once you get the hang of it.
For welding aluminum, you really want a High frequency tig with a water cooled tig torch jacket. You can get by with the basics, but it will never look perfect and will always need grinding.
I have a MIG that can do structural Al., but it is not always pretty....
Stu
Elliot Cannon
Dec 17 2012, 10:50 PM
You'll get real good at sharpening the tungsten rods.

I have a dedicated grinder for that. I put the tungsten rod in a cordless drill and turn it slowly while sharpening it on the grinding wheel. If you have done a lot of oxy acetylene welding, it amounts to just about the same thing except your using an arc to make the puddle with. It takes a LOT of practice. (Speaking for myself of course)

Which reminds me, I need to get out in the garage and do some of that. My goal is to be able to TIG weld upside down. Maybe I'm aiming a little too high.
Cheers, Elliot
McMark
Dec 17 2012, 10:53 PM
Since my first exposure to welding was OxyAcetelene, it made sense. IMHO, forget stack of dimes, forget zig-zag, and C shaped sweeps. Forget push ahead and the pull back while feeding rod. I learned by just doing what works. Find some 16g steel to start on because the 18 & 22g steel on a 914 is too thin to learn on. Hold two pieces right butted up against each other with ViceGrips and practice getting those pieces to flow together without filler rod. It won't work if there is any gap, but this will teach you how to move you foot and how to move your torch. Then do the same process with a 1/16" gap and start using filler rod.
You don't need to learn technical processes, you just need to build muscle memory and unconscious recognition of what you're seeing. Everything that happens while welding happens faster than you can consciously think. So time spent under the helmet is the only good first step. It's like learning a musical instrument. It's gonna sound like shit for a few months.
Elliot Cannon
Dec 17 2012, 10:57 PM

Yeah. That's pretty much what I meant to say.
FourBlades
Dec 17 2012, 11:05 PM
QUOTE(McMark @ Dec 17 2012, 09:53 PM)

Since my first exposure to welding was OxyAcetelene, it made sense. IMHO, forget stack of dimes, forget zig-zag, and C shaped sweeps. Forget push ahead and the pull back while feeding rod. I learned by just doing what works. Find some 16g steel to start on because the 18 & 22g steel on a 914 is too thin to learn on. Hold two pieces right butted up against each other with ViceGrips and practice getting those pieces to flow together without filler rod. It won't work if there is any gap, but this will teach you how to move you foot and how to move your torch. Then do the same process with a 1/16" gap and start using filler rod.
You don't need to learn technical processes, you just need to build muscle memory and unconscious recognition of what you're seeing. Everything that happens while welding happens faster than you can consciously think. So time spent under the helmet is the only good first step. It's like learning a musical instrument. It's gonna sound like shit for a few months.

Thanks Mark, the whole stack dimes is really intimidating, my beads look more like piles of bird guano. Should I use a copper backing plate for the butt welds? So far all the joints I have made in anything less than 14 guage turn into holes that just keep getting bigger..
John
McMark
Dec 17 2012, 11:14 PM
No copper. No filler rod. You'll have some problems with the welder though.

on my Miller I can adjust the peak power, then the pedal moves through that range. So if I set it to 100A then half pedal is 50A. If I set the knob to 150 then half pedal is 75. On yours full pedal is full power and the only way to get low power is to move the pedal less. That's gonna be working against you, sorry to say.
nathansnathan
Dec 17 2012, 11:40 PM
Some things to note, you should hold the electrode in your bare hands when grinding it as not to ever let it get too hot. If it is too hot to hold it will oxidize/discolor. Aluminum especially will be very temperamental about contamination.
About backing the a butt weld, copper flashing is ideal or aluminum backing for steel will work but may contaminate some; backing with steel for aluminum. Backing a weld certainly makes it easier. You would have to back aluminum unless you were back purging.
From my understanding, the Eastwood tig is all on or off? -that would be pretty tough to work.
Everything has to be very clean with tig, more so than mig welding. You hit some rust and it might explode actually, like blow up the electrode. You really have to clean for tig, the hand held wire brush, as it cools, before you weld, wire brush like mad.
The whole "stack of dimes" should be thought of as a means rather than an end. You move the puddle across and that is the pattern it leaves when you do it right. By 'move' I mean that you draw it over with heat. That the metal/puddle will go toward the heat is key.
FourBlades
Dec 18 2012, 06:23 AM
Thanks folks!
I am using the foot pedal to start and control the heat.
It has a knob on the pedal which is supposed to set the maximum amps with the pedal fully depressed. It does seem to make a big difference what I set it to.
You can see the unit does a high frequency start with a long thin arc and humming sound before the main arc comes on. I try to never touch the electrode to the metal but that seems to be my downfall right now.
I will keep at it...
John
scotty b
Dec 18 2012, 06:38 AM
I'm tigging 1/4 on a 911 right now. this is the fitup. Forget about the stack of dimes on sheet metal. You'll need to get good at fusion for 20 gauge stuff. I also buy .035 tig wire. You may have to order it as it is not a big seller, but it is a lot better than trying to strighten mig wire like I used to do
scotty b
Dec 18 2012, 06:40 AM
also starrt out with some scrap working on your puddle, then try fusing. Once you can fuse the two pieces together without filler, then start diping the rod.
SUNAB914
Dec 18 2012, 06:52 AM
diping the rod
That's what Doc Evil said.
FourBlades
Dec 18 2012, 10:01 AM
Thanks Scotty!
So really tight fit up is important, which makes sense.
Do you start the puddle on one side then move across the joint to fuse the sides together or do you start in the middle of the joint?
When I try to start in the middle of the joint, all I end up with is a hole.
John
IronHillRestorations
Dec 18 2012, 10:22 AM
If you are just learning, I'd suggest learning how to lap weld with filler rod first. If you are new to TIG, you'll have a tendency to make tall, proud welds with insufficient weld penetration. Learn how to control the torch and get good weld penetration, then move on to fusion welding. That's just my free advice. Or you can just practice on your car.
ConeDodger
Dec 18 2012, 10:51 AM
Welding clinic Mark?
The Metal Surgeon
Dec 18 2012, 11:03 AM
Practice oxy acet welding first. I went to Coventry university ,England for my 4 year engineering apprenticeship with the Jaguar. I never learnt tig back then but I did oxy acet .I applied the same skill set to tig and never looked back.
Black22
Dec 18 2012, 11:08 AM
My 20yr old cousins work...damn kids!!!
Click to view attachment
ruby914
Dec 18 2012, 11:18 AM
I took welding in high school. I think I was very good at oxy acetylene welding.
We would make things like 2 stroke dirt bike pipes.
My first job out of high school, I did some TIG welding for an off road race company, again I feel I was very good at it.
This year, 30 years later, I got a Everlast TIG welder and after 6 months I don't think I am very good at it.
I now wear glasses, just seeing the puddle is my biggest challenge.
I must be getting old because as soon as I move my hand from a steady rest I am in the puddle as well.
stugray
Dec 18 2012, 12:01 PM
QUOTE
My 20yr old cousins work...damn kids!!!
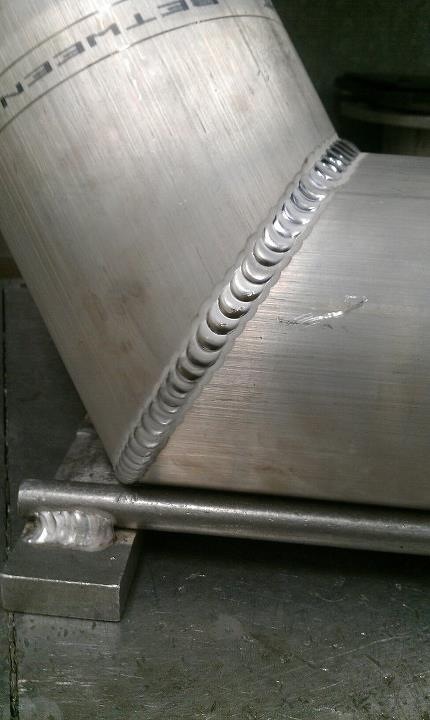
Nope! That cant be right because that is exactly how I said it should look....
Black22
Dec 18 2012, 12:22 PM
QUOTE(stugray @ Dec 18 2012, 10:01 AM)

QUOTE
My 20yr old cousins work...damn kids!!!
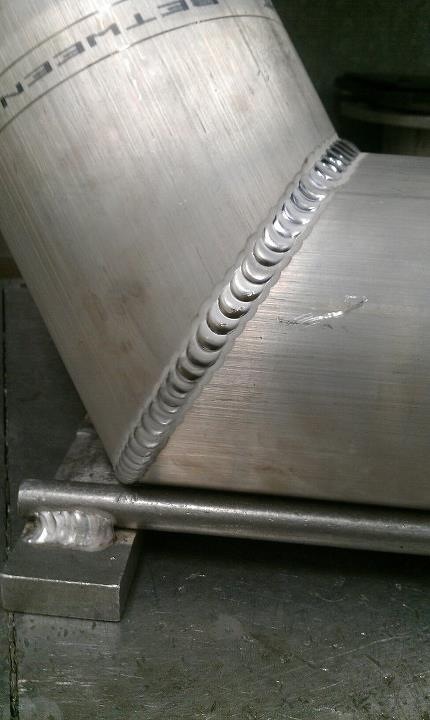
Nope! That cant be right because that is exactly how I said it should look....
You should see the inside (no pics), but it looks exactly the same!
andys
Dec 18 2012, 12:23 PM
QUOTE(ruby914 @ Dec 18 2012, 10:18 AM)

I now wear glasses, just seeing the puddle is my biggest challenge.
I must be getting old because as soon as I move my hand from a steady rest I am in the puddle as well.

Yeah, worsening eyesight is my achilles heel too. Can't find the glasses that give me just the right distance correction; and of course you're always welding at odd angles so there's never just one solution. Weird too, is I get these occasional momentary lapses of hypnosis when welding. Anyone experience this? I used to be pretty good at TIG, but now it's relegated to hit or miss. Enough of that.....
Oxy/acet proficiency is a huge benefit when learning how to TIG weld. Of course a lot of practice is key.
Andys
FourBlades
Dec 18 2012, 02:39 PM
I will look into the oxy/acetylene welding.
Is it easier than TIG welding but helps to pick up TIG welding?
If it is harder then I may skip it.
I saw an interesting you tube video where a guy ("the tinman?") flame welded two plates together and then beat it into a very convex shape without the weld breaking. His point was MIG and TIG make a brittle weld while flame welding leaves a flexible weld.
I can see the rod dipping similarity between the two.
John
The Metal Surgeon
Dec 18 2012, 05:05 PM
Tig welding doesn't leave a brittle weld on sheet metal,mig does in my opinion
okieflyr
Dec 18 2012, 06:49 PM
My strategy is to sharpen 4-5 electrodes at a time to help reduce the down time while i'm trying to get everything synchronized... Still a long way to go....
FourBlades
Dec 18 2012, 09:02 PM
Kevin,
That is a great tip to sharpen more than one tungsten at a time.
I also bought a small benchtop grinder to dedicate to sharpening tungstens.
If seeing the puddle is a problem then get the magnifier lens for your welding helmet. I have tried 2x, 2.5x, and 3x. They cost about $5 each so I thought I would try a range of them. You can only see close up with the magnifiers but I think they help a lot. I like the 3x the best so far. I am almost 50 (shudder) and my eyes are not the greatest. You youngish folk probably don't need them.
I am pretty sure the eastwood ac/dc tig varies the amperage as you press down more or less on the pedal. I can back off the amps slowly at the end of a weld. The trigger that is on the torch is an on/off switch though.
John
scotty b
Dec 18 2012, 09:09 PM
QUOTE(The Metal Surgeon @ Dec 18 2012, 03:05 PM)

Tig welding doesn't leave a brittle weld on sheet metal,mig does in my opinion

Gas will leave the softest weld, BUT if you aren't sufficient with it, it will also warp the worst. As far as tig goes, no I do not weld long lengths even in tig. Get the tight fit and spot it. I typically end up with spot welds about 3/4 of an inch apart before running any kind of a bead, but, I also am nowhere near the level of
the metal surgeon. I have watched his work on the HAMB for a few years now and that level, is what I aspire to be soon
FourBlades
Dec 18 2012, 09:21 PM
Scotty, you will definitely get there...
WOT: The HAMB is the bomb for crazy metal work rustorations.
This dude took a POS 4 door and turned it into a cool 2 door.
Talk about rusty, this is worse than almost any 914 you've seen fixed.
http://www.jalopyjournal.com/forum/showthread.php?t=466490John
strawman
Dec 18 2012, 11:57 PM
QUOTE(FourBlades @ Dec 18 2012, 07:21 PM)

WOT: The HAMB is the bomb for crazy metal work rustorations.
This dude took a POS 4 door and turned it into a cool 2 door.
Talk about rusty, this is worse than almost any 914 you've seen fixed.
http://www.jalopyjournal.com/forum/showthread.php?t=466490John
Thanks, John. That is 90 minutes I'll never get back. But it was fun reading about that dude's sickness for all things rusty... I can now say my rusty basket-case 914 was not THAT bad to begin with!
sean_v8_914
Dec 19 2012, 09:33 AM
the oxy practice tip is good. i also use a little home depot torch to burn off contaminants and moisture prior to weld. dont need to go nuts with the heat. we all want to make nice looking welds but flow and penetration of surrounding metal is far more important than the lovely stack of dimes
i do small spots along the panel. this helps transfer the heat on thin metal and has helped reduce blow thru on yhe thin stuff
mr914
Dec 19 2012, 03:39 PM
I signed up for a class at the local community college.
Lots of good tips, an instructor to tutor you.
It's just practice and more practice.
Told the instructor, i just wanted to do thin sheet metal and aluminum under 1/4 inch.
Best memory....
Tried to weld a 1/8" aluminum box. was looking beautiful. Kept welding and poof, a puddle of aluminum.
stugray
Dec 19 2012, 05:09 PM
QUOTE
Tried to weld a 1/8" aluminum box
A friend of mine was fusion welding together a 1/8" steel cube about 4 inches on a side.
He got to the very last ~1/4" of weld and decided he should let it cool before "sealing" it. When he shut off the torch there was a flame coming out of the box for almost another minute.
Later he decided to show someone the cool flame so he filled it up with Acetylene and lit it - BOOM - his cube flew across the shop and was now a sphere!
He forgot that between the two demonstrations of the "cool flame" he tried to clean out the box through the little seam with Oxygen.
Do not try this at home kids!
Stu
rick 918-S
Dec 20 2012, 12:08 AM
Lots of great suggestions here. Like many others here I started out gas welding also about 40 years ago. I probably burned up a water tower size tank of ox/ac in my early daze.

I attended welding school when I was 18 and worked at fab shops and the ship yard. I have welded with all kinds of stick rods and wire welders including 3/16" flux core wire.
Try running 3/16 wire in a vertical V butt, multi-passes on 1" plate. I've run a mile of 1/4 jet rod, Air ached and welded stress cracks on the pivot of a scrapper, I was trusted to be one of the guys to weld on the hull for the lengthening of the great lakes ore boat the William Clay Ford. The boat was cut in half, the drydock was flooded, the rear half was floated out, a new mid-section was floated in and we welded the seams back together. Think about the stress on the hull. There are tunnels below the deck that run the full length of the boat. In heavy seas when you are at one end of the tunnel looking to the other end the lights will disappear from the end of the tunnel as the hull flexes.
I purchased my first mig welder when I was 18 from the Snap-on man.
It was $ 1800.00 37 years ago!
I have the Eastwood 200 AC/DC Tig also. Great welder. I don't use the foot peddle much. The Eastwood unit comes with an optional little on/off thumb switch. I set the welder up with test pieces first. I have to use 350 power cheater glasses as it is hard to see the puddle. Like most my eyes are getting older than I feel I am. Sux
I purchased a small bench grinder and have a separate dedicated grinding wheel for the separate aluminum and steel electrodes. I use a small battery powered drill to spin the elctrodes against the grinder. Makes a very nice consistant point.
Practice makes proficient.
stugray
Dec 20 2012, 12:34 AM
rick - NICE experience. I like the flexing, floating boat bit. My grandmother actually welded in the East coast shipyards during WWII on some of the Destroyers. She was one of the few that could get all the way into the Bow because she was so tiny.
I learned to weld while setting up Airco-Pulse Arcs in the mids 80's when they first came out.
We had the robotic track welders used on nuke subs that attach with magnetic tracks.
We even tried the electromagnet that could move the spray from side to side without moving the nozzle as the gun climbed the track. It was very cool, but hard to keep consistent because we could not keep the wind out of the chamber.
We calculated that on one job we welded over 1 million feet of weld (3/8" Plate) and that every foot (on average) was welded and ground out-rewelded three times.
The floor was 3" think 45% bevel. The room was designed for acoustic testing of space shuttle payloads...... :-0
Same job where we had a Manitowoc-4000 crane colapsing over our heads while 5 stories up, but I digress....
I currently have a powcon that still runs.
Stu
rick 918-S
Dec 20 2012, 08:43 AM
QUOTE(stugray @ Dec 20 2012, 12:34 AM)

rick - NICE experience. I like the flexing, floating boat bit. My grandmother actually welded in the East coast shipyards during WWII on some of the Destroyers. She was one of the few that could get all the way into the Bow because she was so tiny.
I learned to weld while setting up Airco-Pulse Arcs in the mids 80's when they first came out.
We had the robotic track welders used on nuke subs that attach with magnetic tracks.
We even tried the electromagnet that could move the spray from side to side without moving the nozzle as the gun climbed the track. It was very cool, but hard to keep consistent because we could not keep the wind out of the chamber.
We calculated that on one job we welded over 1 million feet of weld (3/8" Plate) and that every foot (on average) was welded and ground out-rewelded three times.
The floor was 3" think 45% bevel. The room was designed for acoustic testing of space shuttle payloads...... :-0
Same job where we had a Manitowoc-4000 crane colapsing over our heads while 5 stories up, but I digress....
I currently have a powcon that still runs.
Stu
I never the the pulse but they used that type of rig on the deck straps. They laid thick plates down both sides of the deck and welded them with an automated machine. the flux was poured over the molten weld metal as the machine worked it's way along the V butt. Very cool machine, huge roll of wire. I did run a track welder with .045 wire on the slope plates in the cargo hold a couple times. It was an adapted machine that had a hand torch clamped into an motor. You would watch the arch and adjust the sweep, speed and adjust the position as the motor walked up the magnetic track. It allowed for nice long uninterupted welds on the vertical slopes. I ran miles of .035 wire on the horizontal seams. But I'm a small guy so I spent alot of time crawling through the bildge stick welding. Great job but very cold here. It could get 50 with the wind chill. Work was never called off due to the cold.
Anywho, Tig welding is a fine art that takes practice. Like McMark said, muscle memory.
FourBlades
Dec 20 2012, 09:21 AM
Mark's comment really struck a nerve with me.
I have done 10 hours of practice so far and watched all the videos, etc.
I know intellectually what to do, I just need to train my hands to do it right without thinking.
It does remind me a lot (as Mark said) of the difference between knowing how to fret a G chord on the guitar and being able to actually do it smoothly and quickly, without looking while playing.
John
jd74914
Dec 21 2012, 08:19 AM
It's all about practice time. I learned the basics about 6 years ago from a machinist at school and then some tips from Chris Foley. Since then I've TIGed 5 FSAE car frames, headers, and a bunch of aluminum intakes, intercoolers, coolant lines, etc.
My personal TIG learning progression went something like this:
10 hours - Wow, I'm really terrible.
100 hours - Hmm, I'm not too bad, but how do those professionals do it?
500 hours - Better, but not great. Now I'm good enough to teach others.
1000 hours - Lets go weld some cans together!

After spending so much time behind a torch I feel pretty good about my skills, though I'm still always blown away people who have been welding for decades. I've taught a bunch of people now, and like to tell them that its a skill that takes a few hours to aquire and a lifetime to master.
Good luck! Post up some welds-I got great critique from some very experienced people hear when I was learning!
stugray
Dec 23 2012, 12:29 AM
Another trick I learned from welding that most wouldnt appreciate: When setting up the weld joint, there are tricks that help align the joint.
Sometimes we would "hot tack" a joint and then pound it closed while still red hot, or tack on a "dog" on one side of the seam and drive in a wedge to close the seam. After the seam gets tacked, you just remove the wedge and break off the "dog" leaving minimal cleanup if done right.
We even had "sacrificial pry-bars" that you could directly tack on one side of a joint and press the joint together, then break off and repeat....
Stu
This is a "lo-fi" version of our main content. To view the full version with more information, formatting and images, please
click here.