Tdskip
May 1 2019, 08:43 PM
Or, in other words, where is a first time engine builder most likely to go wrong?
Mark Henry
May 1 2019, 08:49 PM
Main bearing pinched on a dowel pin.
Trying to cheap out on headwork.
That one part you didn't replace.
Thinking you know more about cooling tin, flaps, T-stat, etc., than VW/Porsche....
Tdskip
May 1 2019, 09:17 PM
That’s a good starting list-thanks
Superhawk996
May 2 2019, 05:50 AM
QUOTE(Mark Henry @ May 1 2019, 10:49 PM)

Thinking you know more about cooling tin, flaps, T-stat, etc., than VW/Porsche....
Love it --
Can't tell you how frustrating it is to see so many 914's that have had cooling flaps pulled over the years.
Mblizzard
May 2 2019, 06:59 AM
Incorrect alignment of cam and crank timing marks.
Breaking the eyelet off oil pickup when installing the bolt through the case.
Not checking deck height and confirming compression ratio.
Not lapping the cylinders to the heads.
Not using correct sealant for case.
Improper installation of oil cooler seals = leak
Incorrect setting of the crank end play.
Not surfacing pressure plate mounting surface the same amount as the clutch surface.
Not that I have ever done any of those things.
Tdskip
May 2 2019, 07:24 AM
I won’t ask how you know Mike.
Grin.
bbrock
May 2 2019, 07:35 AM
QUOTE(Mblizzard @ May 2 2019, 06:59 AM)

Not surfacing pressure plate mounting surface the same amount as the clutch surface.
Is grinding the ridges off the flywheel bolts a suitable work around for this? When I had my flywheel resurfaced decades ago, I asked them to surface the mounting hub to match but I don't think they did it. I decided to grind the bolts to be sure I have clearance but haven't run the engine yet. Is that going to bite me in the butt?
Also, it's been a long time, but it seemed like installing the distributor gear was a little tricky.
Mblizzard
May 2 2019, 08:00 AM
QUOTE(bbrock @ May 2 2019, 05:35 AM)

QUOTE(Mblizzard @ May 2 2019, 06:59 AM)

Not surfacing pressure plate mounting surface the same amount as the clutch surface.
Is grinding the ridges off the flywheel bolts a suitable work around for this? When I had my flywheel resurfaced decades ago, I asked them to surface the mounting hub to match but I don't think they did it. I decided to grind the bolts to be sure I have clearance but haven't run the engine yet. Is that going to bite me in the butt?
Also, it's been a long time, but it seemed like installing the distributor gear was a little tricky.
I have seen that done but I think that is due to the removal of too much material from the surface and the bolts extend above the flywheel surface.
If you fail to machine both surfaces clutch slippage will be a problem. If so much material was removed that you had to grind the bolts you might want to look at it again. I grade on a good bad scale. Anytime you have to modify bolts to fit stock parts it is likely bad!
Tdskip
May 2 2019, 08:19 AM
I am assuming the do/don't on this is all written up somewhere?
For those that have also rebuild a more conventional water cooled engine, say inline 4 or 6, how much harder / easier are the Type 4 rebuild?
Great discussion, hope it helps others thinking about this too.
bbrock
May 2 2019, 08:21 AM
QUOTE(Mblizzard @ May 2 2019, 08:00 AM)

QUOTE(bbrock @ May 2 2019, 05:35 AM)

QUOTE(Mblizzard @ May 2 2019, 06:59 AM)

Not surfacing pressure plate mounting surface the same amount as the clutch surface.
Is grinding the ridges off the flywheel bolts a suitable work around for this? When I had my flywheel resurfaced decades ago, I asked them to surface the mounting hub to match but I don't think they did it. I decided to grind the bolts to be sure I have clearance but haven't run the engine yet. Is that going to bite me in the butt?
Also, it's been a long time, but it seemed like installing the distributor gear was a little tricky.
I have seen that done but I think that is due to the removal of too much material from the surface and the bolts extend above the flywheel surface.
If you fail to machine both surfaces clutch slippage will be a problem. If so much material was removed that you had to grind the bolts you might want to look at it again. I grade on a good bad scale. Anytime you have to modify bolts to fit stock parts it is likely bad!
Whoops! Looks like a misread what you were saying. Yes, when my flywheel was surfaced, they took .027 off the friction surface and a matching amount off the outer ring where the pressure plate mounts. I mistakenly thought you were talking about the center hub where the flywheel bolts to the crank. That's what may not have been surfaced so I ground the ridges on the bolts just to make sure they don't hit the friction disc.
Disregard my question. Carry on.
jcd914
May 2 2019, 10:12 AM
QUOTE(bbrock @ May 2 2019, 07:21 AM)

I mistakenly thought you were talking about the center hub where the flywheel bolts to the crank.
This is not something that should be machined down when the flywheel is surfaced.
It is a structural part of the flywheel and should be left alone.
If enough material has been removed from the clutch surface of the flywheel the clutch disc can contact the flywheel bolts.
Really that means the flywheel is past its wear limit and should be replaced but I have seem many the have had the ridges on the flywheel bold ground down to add clearance. I have not seen a failure related to the specific modification.
There is a diagram with the machining specs for the 914/6 flywheel that seems to be the accepted standard for the 4cly flywheel as well. I don't think the bolts need to be ground if the flywheel is kept within the limits in the diagram.
I don't have a copy of the diagram handy or I would post it here.
Jim
Tdskip
May 2 2019, 10:17 AM
So really only an issue if the fly wheel has been lightened? I suppose given who knows what has happened to our cars in the last 40+ years it’s probably worth not assuming anything .
rhodyguy
May 2 2019, 10:26 AM
The run out on the fly wheel must be taken in to account prior to machining. You need to weigh the bolts when grinding them down. Kind of time consuming. The center area has a critical dimension. Hines has the numbers for this procedure.
VaccaRabite
May 2 2019, 10:46 AM
Echoing what Mark said.
The dowel pin munching a main bearing is a prime newbie error. It certainly got me. And when you do it the bearing is trashed - no chance to fix it. Buy a new set of bearings...
The other issue is making sure you have proper clearances for your bearings when everything is tightened down. And if you don't, knowing how to fix it.
Zach
worn
May 2 2019, 11:22 AM
QUOTE(Tdskip @ May 1 2019, 06:43 PM)

Or, in other words, where is a first time engine builder most likely to go wrong?
I didn't realize just how important the main case bolt rubber seals are. The bolts go through oil galleys, and have to hold back full oil pressure. I tried to reuse the old ones and now I have lots of weeping oil leaks.
Everything has to fit close and tight to seal in the oil.
Mblizzard
May 2 2019, 11:28 AM
QUOTE(jcd914 @ May 2 2019, 08:12 AM)

QUOTE(bbrock @ May 2 2019, 07:21 AM)

I mistakenly thought you were talking about the center hub where the flywheel bolts to the crank.
This is not something that should be machined down when the flywheel is surfaced.
It is a structural part of the flywheel and should be left alone.
If enough material has been removed from the clutch surface of the flywheel the clutch disc can contact the flywheel bolts.
Really that means the flywheel is past its wear limit and should be replaced but I have seem many the have had the ridges on the flywheel bold ground down to add clearance. I have not seen a failure related to the specific modification.
There is a diagram with the machining specs for the 914/6 flywheel that seems to be the accepted standard for the 4cly flywheel as well. I don't think the bolts need to be ground if the flywheel is kept within the limits in the diagram.
I don't have a copy of the diagram handy or I would post it here.
Jim
Click to view attachment
bbrock
May 2 2019, 11:38 AM
QUOTE(jcd914 @ May 2 2019, 10:12 AM)

QUOTE(bbrock @ May 2 2019, 07:21 AM)

I mistakenly thought you were talking about the center hub where the flywheel bolts to the crank.
There is a diagram with the machining specs for the 914/6 flywheel that seems to be the accepted standard for the 4cly flywheel as well. I don't think the bolts need to be ground if the flywheel is kept within the limits in the diagram.
I don't have a copy of the diagram handy or I would post it here.
Jim
Ah, Mike beat me to it.
Is this the diagram you reference? It's the one I gave the machinist who resurfaced my flywheel anyway.
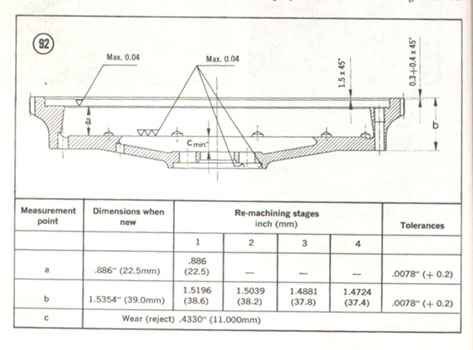
Looking at it again, I may have been misinterpreting all these years. I took it to mean you would have to machine the center hub to maintain dimension C, but now I see it is probably just saying if machining the other two surfaces puts C out of tolerance, your flywheel is no good. I guess the machinists followed the diagram I gave them after all.
Superhawk996
May 2 2019, 11:59 AM
is it just me misreading? I don't think dimension "b" is changing with machining. It would amount to taking material off the ring gear.
material would be taken off the friction surface and an equal amount off the ledge that is below b. This dimension is show as "a".
This maintains the same relationship between the friction surface and the ledge surface that the pressure plate mounts. Again this is dimension 'a'.
I see no reason dimension b would ever change. What am I missing?
rhodyguy
May 2 2019, 12:01 PM
I was under the impression that 'C' is the minimum. Dependent what C is on a new one there might be room for dressing it down. Do I have that correctly Jeff?
Superhawk996
May 2 2019, 12:03 PM
@bbrock To Brent's point, as long as the 11mm dimension 'C' doesn't go below 11mm you'll have room for the flywheel bolt heads.
I just measured a bolt head and it is 9.2mm from shoulder to top of the head.
sjhenry1075
May 2 2019, 12:21 PM
I echo Mark's post about cooling tin; it's there for a reason, no matter how irrelevant it looks. Yes, I know from personal experience except in my case a friend told me "you know if you leave that off the engine will actually run cooler..."
mepstein
May 2 2019, 12:31 PM
QUOTE(sjhenry1075 @ May 2 2019, 02:21 PM)

I echo Mark's post about cooling tin; it's there for a reason, no matter how irrelevant it looks. Yes, I know from personal experience except in my case a friend told me "you know if you leave that off the engine will actually run cooler..."
People often (incorrectly) assume that the mods made for a race engine directly translate to the street.
bbrock
May 2 2019, 01:45 PM
QUOTE(rhodyguy @ May 2 2019, 12:01 PM)

I was under the impression that 'C' is the minimum. Dependent what C is on a new one there might be room for dressing it down. Do I have that correctly Jeff?
Seems clear that is correct. I was 30 years dumber when I first read that diagram and simply missed the "Wear (reject)" part of that dimension. Makes perfect sense to me now.
Tbrown4x4
May 2 2019, 06:33 PM
I'm also confused by that diagram. Always thought it had a typo.
I have an NOS 4 cyl flywheel I need to get the dimensions from. I see no reason to grind the ring gear, and the only critical dimension should be "C".
Mark Henry
May 2 2019, 07:18 PM
IIRC That diagram is for a 914/6 flywheel and isn't correct for a /4.
I've had brand new NOS flywheel and compared to those specs it failed.
bbrock
May 2 2019, 07:31 PM
QUOTE(Tbrown4x4 @ May 2 2019, 06:33 PM)

I'm also confused by that diagram. Always thought it had a typo.
I have an NOS 4 cyl flywheel I need to get the dimensions from. I see no reason to grind the ring gear, and the only critical dimension should be "C".
"A" is also critical but sounds like the number doesn't apply to a Type 4. Sounds like the important things when resurfacing are to take the same amount of material off the pressure plate mounting surface as is removed from the friction surface, and make sure "C" is sufficient to clear the flywheel bolts.
Tbrown4x4
May 3 2019, 04:55 AM
I agree. ^^^^
My machinist was all hung up on the measurements (that he couldn't find) so he wouldn't cut my flywheel. I have 4 or 5 flywheels now, and the only one I know is junk for sure has the ring gear teeth all chewed up.
And I guess the only one I hope is good is the NOS. haha
Superhawk996
May 3 2019, 05:22 AM
QUOTE(Mark Henry @ May 2 2019, 09:18 PM)

IIRC That diagram is for a 914/6 flywheel and isn't correct for a /4.
I've had brand new NOS flywheel and compared to those specs it failed.
That would make sense because when I measured mine (used & has some wear) I measured C as 10mm with a machinist scale. Not precision for sure but I also don't see any evidence that it started much higher at one point.
I also have two other flywheels - I'll take a quick look at those this weekend.
Is there any sort of diagram or spec in the Factory manual for the four cylinder flywheel?
sixnotfour
May 3 2019, 09:32 AM
QUOTE(rhodyguy @ May 2 2019, 12:01 PM)

I was under the impression that 'C' is the minimum. Dependent what C is on a new one there might be room for dressing it down. Do I have that correctly Jeff?
yup, there is a thread,,
For reference my 914-4 flywheel uncut measured "A"22.5 and "C" 9.5.
Tdskip
May 3 2019, 10:01 AM
Great stuff.
Short of splitting the case is there a way beyond oil pressure and lack of bad noises to tell if the bottom end is ok?
Tdskip
May 9 2019, 07:33 AM
Good morning.
Came across this while doing more research - thought I’d post it for other first timers like me who are curious.
http://www.ephotomotion.com/914engine/index01.htmlBack to my question on the bottom end - it would seem that unless you are 100% sure the bottom end is fresh it is false economy to not split the case and make sure. Yes?
Thanks!
Bleyseng
May 9 2019, 08:23 AM
Yes! Most cams are pretty worn after 75,000 miles and the bearings are suspect too. Once the engine is stripped down is easy to pull it apart. Then clean clean the case and install the threaded plugs in the oil gallerys.
rhodyguy
May 9 2019, 09:42 AM
You will have to tap the case for the threaded plugs.
mepstein
May 9 2019, 10:36 AM
QUOTE(Tdskip @ May 9 2019, 09:33 AM)

Good morning.
Came across this while doing more research - thought I’d post it for other first timers like me who are curious.
http://www.ephotomotion.com/914engine/index01.htmlBack to my question on the bottom end - it would seem that unless you are 100% sure the bottom end is fresh it is false economy to not split the case and make sure. Yes?
Thanks!
Yes. There is always something and while it might have gone another 5k, who wants to tear it down a second time.
Tdskip
May 9 2019, 10:45 AM
Oh fine - steer me towards doing it right. Some help you guys are.
Thanks!
BTW - we should really get some people together to do this and film it and then post it back here to help other members of the community.
sixnotfour
May 9 2019, 12:21 PM
QUOTE(Tdskip @ May 9 2019, 10:45 AM)

Oh fine - steer me towards doing it right. Some help you guys are.
Thanks!
BTW - we should really get some people together to do this and film it and then post it back here to help other members of the community.
there s a video ...jake did ???
https://vwparts.aircooled.net/Bug-Me-Video-...build-vol-8.htm
Montreal914
May 9 2019, 01:53 PM
I have really enjoyed Van Svenson's website for hints, rebuild process and videos.
Not a stock engine though.
http://www.ephotomotion.com/914engine/
iankarr
May 9 2019, 01:57 PM
QUOTE(Tdskip @ May 9 2019, 12:45 PM)

Oh fine - steer me towards doing it right. Some help you guys are.
Thanks!
BTW - we should really get some people together to do this and film it and then post it back here to help other members of the community.
I'd be happy to produce it....
Tdskip
May 9 2019, 02:02 PM
QUOTE(cuddy_k @ May 9 2019, 02:57 PM)

QUOTE(Tdskip @ May 9 2019, 12:45 PM)

Oh fine - steer me towards doing it right. Some help you guys are.
Thanks!
BTW - we should really get some people together to do this and film it and then post it back here to help other members of the community.
I'd be happy to produce it....
OK. So we’ve got an engine, machine shop wind up, producer, now we need a coach to make sure I assembled properly and a good way to film it.
Let me ping Evan
This is a "lo-fi" version of our main content. To view the full version with more information, formatting and images, please
click here.