My plan was to use a left twist drill bit to drill it out, and use an Irwin extractor (easy out, recommended by Project Farm)
https://www.youtube.com/watch?v=XVTn6wI4g6s
I saw in another recent thread about building it up with weld.
Here is where I am:
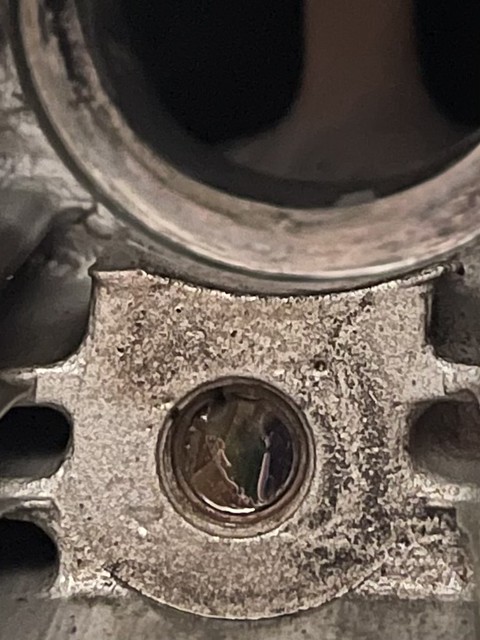
The stud broke 2mm (~.10 inch) below the surface of the head.
Head is on the car, exhaust is off.
I have been brushing my usual penetrant oil (50/50 acetone/ATF) on it 2x a day for three days.
Questions:
1) weld up? I've not done this before on a stud that is so far under the surface. Would this work here? Usually when I weld a broken stud its proud a little of the surface and I can weld a nut on. That very well could be an option here, but I don't want to hurt/melt the head.
2) left hand drill? Mark center, drill a pilot hole and then drill the stud out with a left hand twist bit. How deep do I need to set my drill stop to make sure I don't go through the stud into head.
3) combine the LHD and an easy out and hope for the best? If the extractor breaks the head has to come off and the car may be down for most of the summer. Risky.
4) LHD, and keep going bigger till I can tap for a step stud or insert?
And there is another option that I have considered but would leave the car down and I may miss the NE Gathering this summer:
The 2.3 that @Eric_Shea is building for me will be done sometime this summer. I could just go ahead and pull this engine now. Then wait and install the new engine when it gets here and fix this issue with the head off the motor and on a workbench.
But, again - the issue is that the global supply crunch is effecting the FI bits to my motor, and it may not be ready till fall for install. So the risk here is I miss the NE Gathering. Ugh.
So. What does the brain-trust think?
Zach