Deusexmachina77
Nov 25 2023, 11:24 AM
I have to weld in a new front trunk pan replacing the hole left from an AC unit. I have taken two MIG classes. Beside being a newbie, I have other limitations to consider.
I don’t have access to a 220 line.
I’m inexperienced.
It would cost me $1000 to have it professionally done. And I don’t want to buy a bunch of equipment for one job.
Can I use a flux welder? There a couple cheap units at Harbor Freight (under $150) on sale right now. What don’t I know that I should know?
Thanks
Shivers
Nov 25 2023, 11:31 AM
Just patching the hole, absolutely. I do all sorts of stuff with rosin core wire. Get a good mini grinder and flapper wheels for it. It is messy. I have a handful of small pieces of sheet copper to mask off anything machined or sensitive.
iankarr
Nov 25 2023, 11:32 AM
Get a 120v Hobart Handler. U can set it up for mig or flux. It will be far less than 1K and be useful for years. I’d go right for the mig setup. Not a big deal to get a tank.
Superhawk996
Nov 25 2023, 12:03 PM
May I suggest you’ve asked the wrong question.
Can you . . . Yes.
Should you use a cheap sub $150 HF flux core unit? No.
Why or why not?
Flux core spatter is going to be a mess and will be a PITA to clean up all the splatter.
The cheaper the unit, the harder it is to get a decent weld. Cheap units tend to have limited control over welding current and wire speed. They also tend to have issues with the wire feed mechanism that results in wire slippage or worse yet, jamming and birds’ nesting. Can be very frustrating.
I’d bet with a little searching, you can find a nice used 120v Hobart Handler or Lincoln weld pack 140 in the $250-350 range. As stated by Ian, the ability to use shielding gas is a huge upgrade and even if you choose not to use gas right now, it’s huge as your skills progress.
Bottom line: the cheaper the welder may impair your learning and is more likely to frustrate you.
930cabman
Nov 25 2023, 12:35 PM
QUOTE(Superhawk996 @ Nov 25 2023, 12:03 PM)

May I suggest you’ve asked the wrong question.
Can you . . . Yes.
Should you use a cheap sub $150 HF flux core unit? No.
Why or why not?
Flux core spatter is going to be a mess and will be a PITA to clean up all the splatter.
The cheaper the unit, the harder it is to get a decent weld. Cheap units tend to have limited control over welding current and wire speed. They also tend to have issues with the wire feed mechanism that results in wire slippage or worse yet, jamming and birds’ nesting. Can be very frustrating.
I’d bet with a little searching, you can find a nice used 120v Hobart Handler or Lincoln weld pack 140 in the $250-350 range. As stated by Ian, the ability to use shielding gas is a huge upgrade and even if you choose not to use gas right now, it’s huge as your skills progress.
Bottom line: the cheaper the welder may impair your learning and is more likely to frustrate you.
Don't cheap out with a welder or any tool as far as that goes. Just like anything else welding is practice and more practice. If you try with a cheapie the results will frustrate you.
Superhawk996
Nov 25 2023, 12:38 PM
Looked up what is on sale
Definately don’t get this one. Only current control is a single min/max switch.
Click to view attachmentThis one at least has variable wire speed and variable current controls. Duty cycle is pretty low at 30% @ 90A but would work in a pinch.
Looks like a smaller inverter type unit - meaning no big heavy transformer but slightly more fragile. This has complicated power electronics, and if anything fails, it is a throwaway unit.
Click to view attachmentStill would recommend a better used unit that can support shielding gas but wanted to see what was being offered by HF.
rjames
Nov 25 2023, 01:08 PM
Echoing the advice to look for a quality unit that allows the use of a tank. Check Craigslist. I was able to find a Lincoln with a tank, a cart, and a bunch of accessories fairly cheap. Plus if you decide to sell it afterwards, you’ll likely make of your $ back.
Deusexmachina77
Nov 25 2023, 03:12 PM
Guys,
Thanks everyone for really good advice. I was looking at Craig’s list but I felt I didn’t know enough to evaluate the condition and value. But that seems like the way to go to keep my costs down.
Superhawk996
Nov 25 2023, 05:47 PM
QUOTE(Deusexmachina77 @ Nov 25 2023, 05:12 PM)

felt I didn’t know enough to evaluate the condition and value.
If buying used, have whoever you are buying from demo it by laying down some beads for you.
I probably wouldn’t buy used if a seller won’t demo it and wants to just unload in a Walmart parking lot or something like that.
Put out feeler with car guys / car clubs. Usually someone knows someone looking to upgrade. Good opportunity to avoid Craigslist randomness.
Bought this one used almost 30 years ago for about $100.
Click to view attachmentI don’t use it much (moved on to TIG) but it still works. This one is pretty low end with two switches that only allow 4 current levels. Very basic but came with hoses and regulator and it can use shielding gas which was a decent enough machine to get me started way back when.
mb911
Nov 25 2023, 07:54 PM
Ugh I need to do a sticky on this. Superhawk has you rolling in the right direction so I won’t touch this topic for now
bkrantz
Nov 25 2023, 08:13 PM
Find a friend with a welder.
Or (better) find a friend who is a welder.
emerygt350
Nov 26 2023, 07:15 AM
I have had the titanium for 4 years now. I have used it on 1/4 plate and on sheet metal. I use aluminum foil to protect surfaces. It will give a very nice weld on thick metal, takes a little practice on the thin stuff. It has been very reliable and worth what I paid for it. No jamming or any other issues. Practice your welds before attempting thin metal work. I was a welder in a previous life (30 years ago) though. Mig or tig would of course be better but I really think the titanium has its applications and this may be one of them. No gas, super cheap, decent quality, and 120 with the guts to make really nice welds on pretty heavy metal.
IronHillRestorations
Nov 26 2023, 08:12 AM
True MIG (shielding gas) is the only way to go for any body work. Without the shielding gas you have slag on every weld, and invariably you will get weld inclusions (bad spots) as a result. With shielding gas you can weld on a prior bead without knocking the slag off. You can also use a .023 wire which is better for thin metal. I’ve never used a flux wire welder, so I’m not sure what size wire.
stownsen914
Nov 26 2023, 08:21 AM
As a self taught hobbyist welder, I'd have to agree that the right equipment is important. Good you took a class, so you are off to a good start. It's worth spending a little more and/or being patient to find a deal on a quality used unit. It's hard enough to learn to weld well without poor equipment stunting your leaning and/or contributing to mediocre outcome.
Another option - I borrowed a good MIG for a while at one point before I had my own.
Mayne
Nov 26 2023, 08:43 AM
I have a small Titanium flux core welder that has served me well for a couple of years. Sometimes I can weld quite well with it, other times not so much. But I’ve done the front pan, hell hole, and passenger side floor pan repairs with it. I’ll upgrade to mig before I tackle steel GT flares.
Spoke
Nov 26 2023, 08:48 AM
QUOTE(Deusexmachina77 @ Nov 25 2023, 12:24 PM)

I don’t have access to a 220 line.
I was worried about that when I bought my 110V welder but virtually all the welding you'll do on your 914 doesn't require the higher power of a 220V unit.
Like you I wanted to spend as little as possible to get started with a 110V Millermatic 135 welder and flux core wire as I didn't have a tank.
My first job with the welder was to repair the muffler hanger on my 914 which I had hose clamped together to keep running. I remember standing there after finishing that weld looking around at anything else I could weld because it was so much fun.
Since then I've welded so many areas of my 2 914s and my 930 as well as items on friend's cars. I'm just bummed that I waited so long to purchase the welder.
Whatever equipment you buy if you do buy, make sure it has variable speed and power. Not rotary click switches or hi/med/lo or hi/lo switches.
MikeK
Nov 26 2023, 10:29 AM
QUOTE(Deusexmachina77 @ Nov 25 2023, 12:24 PM)

I have to weld in a new front trunk pan replacing the hole left from an AC unit. I have taken two MIG classes. Beside being a newbie, I have other limitations to consider.
I don’t have access to a 220 line.
I’m inexperienced.
It would cost me $1000 to have it professionally done. And I don’t want to buy a bunch of equipment for one job.
Can I use a flux welder? There a couple cheap units at Harbor Freight (under $150) on sale right now. What don’t I know that I should know?
Thanks

I know it can be challenging, but can you post a picture of the project? Maybe it's something that a panel can be made and patched over with rivets?
If it does require complete replacement, you could remove it, prep and fit the new panel with sheet metal screw or clecos, then rent a machine or hire welder to compete the job. I would think a half day rental would be pretty affordable and enough time if it was prepared properly.
As was suggested, a used, name brand machine can be found for not a lot of money and having the ability to weld is a nice skill to have. I have MIG, TIG and O/A. If I could have just one, it would be O/A.
Root_Werks
Nov 26 2023, 05:32 PM
That much welding, I'd use a gas shielded MIG. I have a small one, 110V and it works well for thinner metal like body panels.
I also have one of those little Flux MIG welders I use for field repairs. It's saved my bacon many times welding up tools, carts etc. out in the middle of nowhere. I wouldn't use a Flux welder on body work. Others have already stated all the reasons.
Best option is find a buddy who welds and pay him in beer to do the work.
mgarrison
Nov 27 2023, 12:59 PM
I used the HF titanium flux core welder because I was working outside, and didn't want to fuss with a tank & gas. Not great, but works pretty decent in my opinion...
http://www.914world.com/bbs2/index.php?sho...p;#entry2883421
porschetub
Nov 28 2023, 03:48 PM
Seems to be all about wire and feed control which my 2 yr old BOC Smootharc 180 240V has in spades ,I went from new machine and built a farm hay trailer that was framed in 6mm wall thickness box section galv-coated , I was on co2 gas the welding was so easy it was fun, vertical welds were so simple .
Fairly recently closed up the front panel OP had been cut for a cooler ,had no gas left so changed to flux wire and did some test welds after changing settings for 1mm thickness panel steel , my welding experience is pretty extensive but don't have a lot of time with panel steel , this machine made me look like a real "star" TBH.
To me welding is like painting ...its all in the prep , correct gaps,clean surfaces ,correct feed and current ,good helmet and gloves and you get a decent result IMO.
If you are a bit short of cash buy a half decent one then on sell when you are done .
Cheers.
Click to view attachmentClick to view attachment
Deusexmachina77
Dec 11 2023, 08:26 AM
After much deliberation and searching, I found the best option for my situation—a friend with a welder AND a garage to work on it.
I have another question for this group since you were all so helpful.
Should I butt weld or lap weld the new floor pan in? I'm thinking lap weld. I don't want to weld from the bottom. I don't have access to a lift, and I'm not going to be able to weld on my back. I'm too old for that.
Click to view attachment Click to view attachment
930cabman
Dec 11 2023, 08:50 AM
"A friend with a welder and a garage" sounds like a winner, compensate him/her well for this. Is it safe to assume the friend is a welder? they should be versed
Generally lap welds are frowned on, it is an easier joint but the entire car is put together with lap welds and spot welded.
I have the same repair to a project currently on our lift and was mulling the lap/butt question.
I bet others will chime in and suggest a butt weld. Working from the top will be easier, but harder on your back
Don't feel alone, many or most of us are too old for this nonsense too
Superhawk996
Dec 11 2023, 09:07 AM
Butt weld is the gold standard for panel repair.
Lap welds harbor moisture and lead to corrosion no matter how well sealed. Sealant eventually fails and then compounds the trapped moisture and corrosion problem. Lap weld repair better than no repair but it will eventually need to be cut out and repaired properly when it begins to corrode.
A butt weld on that panel can be done from the top.
Geezer914
Dec 11 2023, 09:13 AM
I picked up a used Sears flux core welder for $100. Repaired the hell hole, replaced the battery tray, and patched the bottom of the firewall due to a leak from the back window. Also welded a fuel door in the front hood. It's messy, but a wire wheel and a grinder are your friend.
MikeK
Dec 11 2023, 10:53 AM
There's no shame in a lap weld if the joint is prepared properly. You could do a very clear repair if the replacement panel is joggled at the edges and fits the opening properly. Spend extra time during fitting to ensure it looks correct. Prep the lapped areas with a weld-thru primer, clean your plug weld holes and burn it in. With a 100V machine, you will likely have to crank that welder up as high as it will go to get a clean, flat weld.
With your skill set, this would give you a better looking repair than trying to fit a complex panel to the car with little to no gap and trying to MIG it in. Clean up any weld thru primer overspray, brush or spray on some epoxy primer, seam seal top and bottom and you'll have a repair better than most.
Other than for authenticities sake, to make the weld disappear and have it appear that no work was done, I would do it the way I described. A MIG weld on a butt joint is about the worst tool you can possibly use for sheet metal repairs, other than chassis work. External panels to be finished: TIG or OA with little to no filler rod.
Geezer914
Dec 11 2023, 12:14 PM
Trace a pattern of the cut out on a piece of poster board for a nice tight fit.
Spoke
Dec 11 2023, 12:19 PM
QUOTE(Deusexmachina77 @ Dec 11 2023, 09:26 AM)

After much deliberation and searching, I found the best option for my situation—a friend with a welder AND a garage to work on it.
I have another question for this group since you were all so helpful.
Should I butt weld or lap weld the new floor pan in? I'm thinking lap weld. I don't want to weld from the bottom. I don't have access to a lift, and I'm not going to be able to weld on my back. I'm too old for that.
Click to view attachment Click to view attachmentI've butt welded a bunch of small panels on the floor of my 914 w/o going under the car. All done from the top.
930cabman
Dec 11 2023, 12:26 PM
QUOTE(Spoke @ Dec 11 2023, 01:19 PM)

QUOTE(Deusexmachina77 @ Dec 11 2023, 09:26 AM)

After much deliberation and searching, I found the best option for my situation—a friend with a welder AND a garage to work on it.
I have another question for this group since you were all so helpful.
Should I butt weld or lap weld the new floor pan in? I'm thinking lap weld. I don't want to weld from the bottom. I don't have access to a lift, and I'm not going to be able to weld on my back. I'm too old for that.
Click to view attachment Click to view attachmentI've butt welded a bunch of small panels on the floor of my 914 w/o going under the car. All done from the top.
With a TIG?
Spoke
Dec 11 2023, 12:40 PM
QUOTE(930cabman @ Dec 11 2023, 01:26 PM)

QUOTE(Spoke @ Dec 11 2023, 01:19 PM)

QUOTE(Deusexmachina77 @ Dec 11 2023, 09:26 AM)

After much deliberation and searching, I found the best option for my situation—a friend with a welder AND a garage to work on it.
I have another question for this group since you were all so helpful.
Should I butt weld or lap weld the new floor pan in? I'm thinking lap weld. I don't want to weld from the bottom. I don't have access to a lift, and I'm not going to be able to weld on my back. I'm too old for that.
Click to view attachment Click to view attachmentI've butt welded a bunch of small panels on the floor of my 914 w/o going under the car. All done from the top.
With a TIG?
With a MIG.
porschetub
Dec 11 2023, 01:29 PM
QUOTE(Superhawk996 @ Dec 12 2023, 03:07 AM)

Butt weld is the gold standard for panel repair.
Lap welds harbor moisture and lead to corrosion no matter how well sealed. Sealant eventually fails and then compounds the trapped moisture and corrosion problem. Lap weld repair better than no repair but it will eventually need to be cut out and repaired properly when it begins to corrode.
A butt weld on that panel can be done from the top.

,also the shape of area is a problem already , if repair panel isn't butt welded it's never going to fit properly if lapped the overlay will cause gaps ,its not you can just dolly them down due to all the curves.
Rust is a certainty and just a matter of time and it will look ugly ....ask me how I know all this ?? ,PO did this after welding up a patch to cover the hole for a cooler ,too much heat and not enough tacks ,the patch has also buckled upwards as no gap as there would be with butt weld .
I'am faced with trying to fix this as I can't bring myself to cut it out but may have to ,have scrapped all the sealer out there is rust.
Click to view attachmentClick to view attachmentIt looks much worse that the photos trust me on that

.
Superhawk996
Dec 11 2023, 07:22 PM
@porschetub Try a shrinking wheel on it to remove the buckling / oil-can effect.
930cabman
Dec 12 2023, 02:44 PM
QUOTE(Spoke @ Dec 11 2023, 01:19 PM)

QUOTE(Deusexmachina77 @ Dec 11 2023, 09:26 AM)

After much deliberation and searching, I found the best option for my situation—a friend with a welder AND a garage to work on it.
I have another question for this group since you were all so helpful.
Should I butt weld or lap weld the new floor pan in? I'm thinking lap weld. I don't want to weld from the bottom. I don't have access to a lift, and I'm not going to be able to weld on my back. I'm too old for that.
Click to view attachment Click to view attachmentI've butt welded a bunch of small panels on the floor of my 914 w/o going under the car. All done from the top.
Being a CSOB I suppose a bunch is cheaper/easier than an entire floor pan. I will probably follow suit.
mb911
Dec 12 2023, 05:15 PM
Ok I have to pipe up a little bit here as I do this for a living.
A: no lap joint is acceptable on a 1/4, floor pan or any where where moisture can get trapped. The floor pan is a lap joint onto the longs and look what happened from the factory
B: flux core is a good solution for many welding applications. NR211 is used as a normal construction filler within the Iron workers on the west coast for structural. That said they are using high end power sources to achieve high quality earthquake code welds.
C: patch panels in a floor are completely acceptable for CSOBs and I have done that before myself but ultimately it takes more time
D: MIG or proper term in the US would be GMAW or MAG in Europe requires the least skill for the average car person. GTAW is way harder to do correctly but requires much less grinding and blending
E: to control warping and oil canning just use small tacks and skip all around. Also use your hand with a glove on to absorb some of the heat from the weld area (HAZ) using a wiping motion. You can also use a damp rag or air nozzle for sheet metal repairs. This should never be done on a structural weld(only let air cool )
Here is a demo weld I did the other day for a reference weld for you TIG welders
Click to view attachment
mb911
Dec 12 2023, 05:16 PM
930cabman
Dec 12 2023, 07:14 PM
Nothing short of artwork, thanks for posting.
How many years have you been at it? Many I am sure
bkrantz
Dec 12 2023, 09:05 PM
Another vote for butt welding, and you can doing it from the top (inside).
You might get away with a lap weld, but only if you weld on the side most exposed to weather/water. That means from below.
Deusexmachina77
Dec 13 2023, 04:49 PM
@mb911 That TIG weld is a thing of beauty. I only have access to a MIG welder and am not skilled enough to lay down beads like that.
Re-reading my follow-up post, the litany of not wanting to weld from the bottom was about the lap weld. I thought I would have to do the top and the bottom.
I have a pretty good mess to clean up first, so I'll see how I do with all that work first. And then I'll decide how comfortable I am with the butt weld. I usually have to do things twice. Something tells me I'll be paying a professional–eventually.
Thank you everyone for your thoughts. It is a constructive discussion. I've learned a lot.
mb911
Dec 13 2023, 04:56 PM
QUOTE(Deusexmachina77 @ Dec 13 2023, 02:49 PM)

@mb911 That TIG weld is a thing of beauty. I only have access to a MIG welder and am not skilled enough to lay down beads like that.
Re-reading my follow-up post, the litany of not wanting to weld from the bottom was about the lap weld. I thought I would have to do the top and the bottom.
I have a pretty good mess to clean up first, so I'll see how I do with all that work first. And then I'll decide how comfortable I am with the butt weld. I usually have to do things twice. Something tells me I'll be paying a professional–eventually.
Thank you everyone for your thoughts. It is a constructive discussion. I've learned a lot.

Use magnets to hold the but joint tight until it’s tacked in.
bkrantz
Dec 13 2023, 08:05 PM
QUOTE(mb911 @ Dec 13 2023, 03:56 PM)

QUOTE(Deusexmachina77 @ Dec 13 2023, 02:49 PM)

@mb911 That TIG weld is a thing of beauty. I only have access to a MIG welder and am not skilled enough to lay down beads like that.
Re-reading my follow-up post, the litany of not wanting to weld from the bottom was about the lap weld. I thought I would have to do the top and the bottom.
I have a pretty good mess to clean up first, so I'll see how I do with all that work first. And then I'll decide how comfortable I am with the butt weld. I usually have to do things twice. Something tells me I'll be paying a professional–eventually.
Thank you everyone for your thoughts. It is a constructive discussion. I've learned a lot.

Use magnets to hold the but joint tight until it’s tacked in.
And make sure metal on both sides of the butt is solid and clean. Thin, dirty, and/or rusty metal edges will instantly burn through.
MikeK
Dec 14 2023, 09:48 AM
QUOTE(mb911 @ Dec 13 2023, 05:56 PM)

QUOTE(Deusexmachina77 @ Dec 13 2023, 02:49 PM)

@mb911 That TIG weld is a thing of beauty. I only have access to a MIG welder and am not skilled enough to lay down beads like that.
Re-reading my follow-up post, the litany of not wanting to weld from the bottom was about the lap weld. I thought I would have to do the top and the bottom.
I have a pretty good mess to clean up first, so I'll see how I do with all that work first. And then I'll decide how comfortable I am with the butt weld. I usually have to do things twice. Something tells me I'll be paying a professional–eventually.
Thank you everyone for your thoughts. It is a constructive discussion. I've learned a lot.

Use magnets to hold the but joint tight until it’s tacked in.
I find that my arc likes to wander when I'm tacking things up with a MIG while using magnets. Maybe I'm imagining it.
It also took me a couple of Winters to figure out that my welds went to shit when my shop heater turned on. Then I realized all my shielding gas was blowing away...
MikeK
Dec 14 2023, 10:10 AM
Here's an alternative method for fitting and holding panels. I cut a bunch of these little tabs, punch an 1/8" hole for a cleco, tack to either side of the panels your joining.
Regarding butt vs. lap welding; My suggestion to lap was based solely on the OP's lack of experience. The most skilled part of this job is the welding, the rest of the job is patience and the grunt work of putting the panel in and out to obtain a good fit. With enough fitting, the panel could be made to fit like a glove, then rosette welded with proper surface preparation. Is it the best way? Let's just say it isn't how I would do it, but fitting a panel with little to no gaps is a skill that needs to be developed as well.
Considering that EVERY joined panel on your Porsche is a lap weld, I think it's a viable option. In fact, the only butt welded panels I can think of on a Porsche would be 356 outer panels, and you would never want to weld those with a MIG because you wouldn't be able to metal finish it.
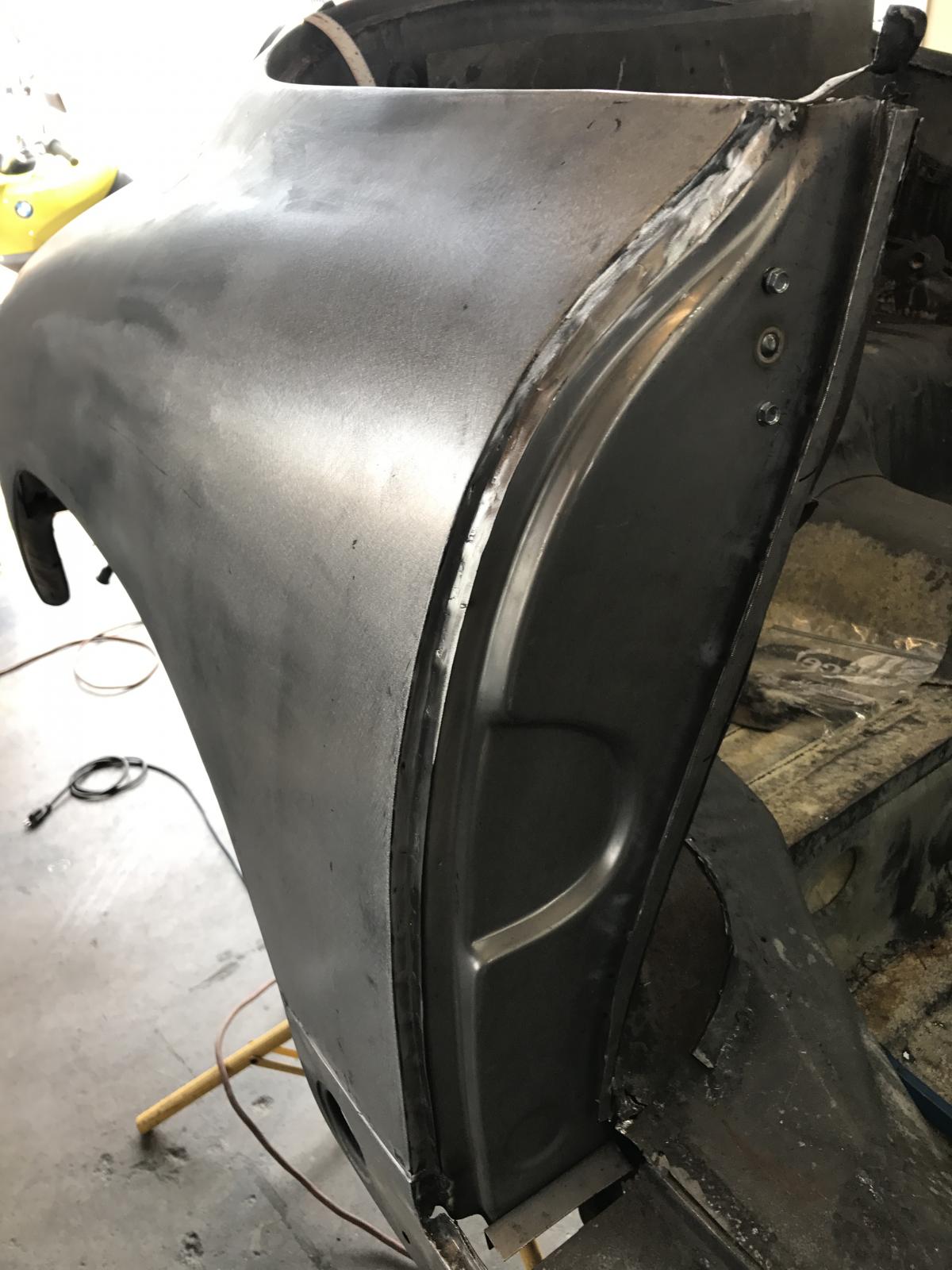
Good luck!
930cabman
Dec 14 2023, 01:01 PM
Great advice MikeK, thanks
I will making the same (frunk floor) replacement and will shoot for the butt, it just looks cleaner.
Who will look under the spare tire anyways?
BTW: looks like you have a nice little project with the 356
914rrr
Dec 15 2023, 07:59 PM
Is flux welding more apt to have paint adhesion issues vs MIG? IIRC, one of my first 914's had a what looked like a rust spot in the drivers side front fender near the bottom. When we started grinding it, we discovered it had been repaired / patched already and welded (brazed) with brass. I was told that unless you are meticulous in removing every bit of flux then then the body filler and paint wouldn't stick to it properly. Is this correct?
930cabman
Dec 16 2023, 08:55 AM
QUOTE(914rrr @ Dec 15 2023, 08:59 PM)

Is flux welding more apt to have paint adhesion issues vs MIG? IIRC, one of my first 914's had a what looked like a rust spot in the drivers side front fender near the bottom. When we started grinding it, we discovered it had been repaired / patched already and welded (brazed) with brass. I was told that unless you are meticulous in removing every bit of flux then then the body filler and paint wouldn't stick to it properly. Is this correct?
Not only flux, but any contaminant. painting is all about prep and it can be anything
914rrr
Dec 16 2023, 09:42 AM
QUOTE(930cabman @ Dec 16 2023, 09:55 AM)

QUOTE(914rrr @ Dec 15 2023, 08:59 PM)

Is flux welding more apt to have paint adhesion issues vs MIG? IIRC, one of my first 914's had a what looked like a rust spot in the drivers side front fender near the bottom. When we started grinding it, we discovered it had been repaired / patched already and welded (brazed) with brass. I was told that unless you are meticulous in removing every bit of flux then then the body filler and paint wouldn't stick to it properly. Is this correct?
Not only flux, but any contaminant. painting is all about prep and it can be anything
So, is flux core welding generally a bad idea for anything that will be painted, especially if it's on an exterior body panel vs pans or trunk areas?
mb911
Dec 16 2023, 01:37 PM
QUOTE(914rrr @ Dec 16 2023, 07:42 AM)

QUOTE(930cabman @ Dec 16 2023, 09:55 AM)

QUOTE(914rrr @ Dec 15 2023, 08:59 PM)

Is flux welding more apt to have paint adhesion issues vs MIG? IIRC, one of my first 914's had a what looked like a rust spot in the drivers side front fender near the bottom. When we started grinding it, we discovered it had been repaired / patched already and welded (brazed) with brass. I was told that unless you are meticulous in removing every bit of flux then then the body filler and paint wouldn't stick to it properly. Is this correct?
Not only flux, but any contaminant. painting is all about prep and it can be anything
So, is flux core welding generally a bad idea for anything that will be painted, especially if it's on an exterior body panel vs pans or trunk areas?
No it will be just fine. They literally paint buildings and the frame work of sky scrapers that have been flux core welded. Just clean it properly
mb911
Dec 16 2023, 01:39 PM
QUOTE(MikeK @ Dec 14 2023, 07:48 AM)

QUOTE(mb911 @ Dec 13 2023, 05:56 PM)

QUOTE(Deusexmachina77 @ Dec 13 2023, 02:49 PM)

@mb911 That TIG weld is a thing of beauty. I only have access to a MIG welder and am not skilled enough to lay down beads like that.
Re-reading my follow-up post, the litany of not wanting to weld from the bottom was about the lap weld. I thought I would have to do the top and the bottom.
I have a pretty good mess to clean up first, so I'll see how I do with all that work first. And then I'll decide how comfortable I am with the butt weld. I usually have to do things twice. Something tells me I'll be paying a professional–eventually.
Thank you everyone for your thoughts. It is a constructive discussion. I've learned a lot.

Use magnets to hold the but joint tight until it’s tacked in.
I find that my arc likes to wander when I'm tacking things up with a MIG while using magnets. Maybe I'm imagining it.
It also took me a couple of Winters to figure out that my welds went to shit when my shop heater turned on. Then I realized all my shielding gas was blowing away...
A few magnets to hold it in place not near where you are tacking
gereed75
Dec 16 2023, 03:00 PM
It will also destroy the strength of the magnet
Always recommend listening to Ben’s advice. Very knowledgeable. Just bought a used helmet from him (reasonably priced too) Even though used was a significant upgrade over my base line helmet. Vis is so much better. Used it for the first time yesterday and actually made a bunch of welds I did not feel compelled to grind!!
Thanks Ben
PS: go check out Fitzee on YouTube. He uses a method he calls cut and butt. I’m a rank amateur but it has worked for me in several applications repairing floor pans.
mb911
Dec 17 2023, 07:23 AM
QUOTE(gereed75 @ Dec 16 2023, 01:00 PM)

It will also destroy the strength of the magnet
Always recommend listening to Ben’s advice. Very knowledgeable. Just bought a used helmet from him (reasonably priced too) Even though used was a significant upgrade over my base line helmet. Vis is so much better. Used it for the first time yesterday and actually made a bunch of welds I did not feel compelled to grind!!
Thanks Ben
PS: go check out Fitzee on YouTube. He uses a method he calls cut and butt. I’m a rank amateur but it has worked for me in several applications repairing floor pans.
That does work for sure
Deusexmachina77
Dec 18 2023, 04:56 PM
I cut the panel to where I thought it would lay best and found the best metal to adhere to. I tacked the panel in place, then cut around the panel with the thinnest cutting wheel I could find. Sometimes I used a Dremel. Cut and tack. Cut and tack. The backside closest to the vertical is not as bad as it looks. The old floor sagged away after it was cut. With just a little help it meets the new panel perfectly. I had a couple of mistakes cutting making bigger gaps than I wanted. Rookie mistakes. But all in all I think I'm going to be okay.
This is a "lo-fi" version of our main content. To view the full version with more information, formatting and images, please
click here.