r_towle
Jan 11 2006, 08:07 PM
Hi guys,
Through a local DOD contractor I found a few small shops that will make Berillium Diaphrams...
Apparently the new fighter jets use alot of the material, so they are set up to work with it, and do small runs...
So , what I need, to get a price, is CAD drawings of the diaphram, and the piece that gets pressed into the middle..
I have been told that they can do it, based upon my description.
So, did anyone ever make a drawing of the diaphram...or maybe please......mike...could you...
Rich
JeffBowlsby
Jan 11 2006, 09:41 PM
Cool....!
Mike, you are the man to do a drawing. I could do a hand-drafted drawing if needed.
I hope this works out, it would save a lot of D-Jet systems.
Demick
Jan 11 2006, 09:51 PM
Jeff
If you have a diaphragm lying around that you can get over to me, I'll make a 3D CAD model and some detailed engineering drawings of it.
Demick
jimkelly
Jan 11 2006, 10:07 PM
do they really need a cad drawing or can they work with an actual part?
did they quote you a ballaprk price range?
if you can't get anyone to do a cad - I can send you a bad mps.
Jim
r_towle
Jan 11 2006, 10:09 PM
cad.
if they need to measure, and make the drawing...that takes time.
rich
rick 918-S
Jan 11 2006, 11:13 PM
Dude!
Bleyseng
Jan 11 2006, 11:37 PM
I have a spare decent diaphram laying around if you need one. Ray Greenwood is working on making some but I am not sure about the center pieces fitting.
Demick
Jan 12 2006, 09:44 AM
Jeff is going to send me a diaphragm. After I get it in CAD, I'll make the files and drawings available.
Demick
Bleyseng
Jan 12 2006, 09:56 AM
Is it Berillium? The ones I have are copper or atleast mostly copper. Now the aneroid cells are something different.....
ppickerell
Jan 12 2006, 10:01 AM
I can make the beryllium piece in my shop, but there will be form tooling required to make the concentric rings.
r_towle
Jan 12 2006, 10:27 AM
I was just going on what you guy have been saying for years...
I read lots of threads here...I was told the original diaphram (the one that breaks) was made from berillium.
The replacements that were being used were made of a copper bronze alloy that did not work the same way and were harder to tune.
So, I ran into this guy, and I am willing to take this through to a price etc...
And yes, they would make a press tool for the ridges, and they would make new center pieces, and assemble the whole deal...at least that was the concept.
At least we can have a healthy discussion and possibly they may have some setup ideas...
I would prefer we make these entirely new, no need to hunt down cores just for the middle part,,,then have to disassemble them...
Rich
Jeroen
Jan 12 2006, 10:37 AM
funny, I've been looking into the same thing
was doing some investigating on the issue, but because of being too busy, I got a little side-tracked
lets see what you can come up with...
Jenny
Jan 12 2006, 10:57 AM
Jenny
Jan 12 2006, 11:00 AM
bugger... the picture didn't take.
airsix
Jan 12 2006, 12:11 PM
QUOTE (r_towle @ Jan 12 2006, 08:27 AM) |
I was just going on what you guy have been saying for years...
I read lots of threads here...I was told the original diaphram (the one that breaks) was made from berillium.
The replacements that were being used were made of a copper bronze alloy that did not work the same way and were harder to tune. |
Copper and Copper-bronze will work harden. Beryllium won't. It's also over 30% more elastic than steel..... however it's NASTY stuff. If any of you DO decide to work with it be aware that absorbsion of airborne particles is a VERY serious health risk. :deadsmiley:
IMHO it's more likely that the diaphrams were made from Beryllium copper rather than pure Beryllium. Beryllium copper is 98% copper 2% beryllium.
B.C. is highly ductile which makes it great for forming complex stamped parts (see picture above) It's also the only copper alloy I know of that can be heat-treated. It is used for springs and such in specialized applications (it's light, doesn't work harden easily, and is a good electrical conductor).
-Ben M.
Demick
Jan 12 2006, 01:22 PM
Yep. I would guess that the appropriate callout for this would be half-hard BeCu.
Demick
r_towle
Jan 12 2006, 01:41 PM
ok, you sound smart...
can you arrange to have someone test the original diaphram to determine what it is?
At least if we start with the correct alloy we will be better off...
Rich
Demick
Jan 12 2006, 06:31 PM
Im not sure how to have it tested, but BeCu is the natural choice for this application. Not many materials suited to this. Only question in my mind is the degree of hardening.
Demick
TimT
Jan 12 2006, 06:41 PM
You will have to sacrifice one and send it to a Materials Testing Lab and have an assay done.
Since we know kind of what it is made of makes it much easier for the lab, and sort of less costly for us.
Bleyseng
Jan 12 2006, 07:02 PM
I can send someone dead OEM ones.....got a few of those sitting around in a box along with 50 dead mps's.
JeffBowlsby
Jan 12 2006, 08:10 PM
If I recall, Brad anders posted a series of patents for the MPS on his website...the material was specified there...but don't trust my memory without verifying it.
r_towle
Jan 12 2006, 09:23 PM
ok..
So Demick will get a CAD drawing done...
Bolwsby will look up the material name...
If not, can airsix help us get the material propoerly tested?
Geoff will donate old material for testing...
I will get the drawings to the engineering firms and get a price/size of the run...
I am told that we can work with at least three companies that are all set up to do this...
Demick, is there a standard CAD file type....(Im thinking similar to ascii text, or gcode) that can be given to multiple companies...so they can read it with whatever software they happen to have???
Or is Autodesk a standard...know what I mean here...
Demick
Jan 12 2006, 10:19 PM
I will do the CAD models in Solidworks. I can output most any format that shops can import. Most likely, they will prefer a 3d IGES or STEP file. They can also simply work straight from the drawings I will create and skip the CAD models if they choose.
I've read the patent documents. I have them at work and can take a look at the material - but extremely unlikely that it will actually have a useable material callout and hardness.
I believe that heat treatment is done after forming. So we have the option to have some diaphragms made and then heat treated differently. 1/4 hard, 1/2 hard, 3/4 hard. They we can make a simple fixture to pull a vacuum on the different diaphragms and compare them to stock to see which one most closely matches the stock movement.
Be sure that we include Patrick in this. He has a great shop and does great work and is an honest guy (as well as a 914 guy). He knows what he is doing and will give us the lowdown without any BS as far as the mfg and tooling of this.
Demick
r_towle
Jan 12 2006, 10:21 PM
Im all for Patrick doing it...
I just want a solution available...
Rich
Demick
Jan 12 2006, 10:34 PM
QUOTE (r_towle @ Jan 12 2006, 08:23 PM) |
I will get the drawings to the engineering firms and get a price/size of the run... |
I'm all for this, but I think this will be the stumbling block. My guess is that price for tooling + the first 50 parts will be in the $5000+ range.
So you'll need to find someone to front this money, and then you'll have to then find 50 people to buy them for $100 each (and this still doesn't include the rebuilding of the MPS to install the new diaphragm). And that is all just to break even.
Anyway, this is just my estimate of the situation. Once quotes are in, then you can evaluate if it is worthwhile and where the $$ will come from.
Demick
r_towle
Jan 12 2006, 10:40 PM
you may very well be right on the price, but I would like to get that real information out on this board...
I am confident that we can put a real world number here, not a ballpark.
If it is truely cost prohibitive, it will make the decision regarding saving the FI pretty simple...
Eventually, all the used MPS's that are out there will be gone...
So, either we find a cost effective way to do this, or we change our cars...
I personally would prefer to solve this problem..
If we find out that the alloy is not berrilium, that would reduce the price, because it will increase the number of companies that could do the work..
So, I think we need both answers, how much to make this part, and what the actual material is..
Rich
SLITS
Jan 13 2006, 12:37 AM
QUOTE (Demick @ Jan 12 2006, 09:34 PM) |
QUOTE (r_towle @ Jan 12 2006, 08:23 PM) | I will get the drawings to the engineering firms and get a price/size of the run... |
I'm all for this, but I think this will be the stumbling block. My guess is that price for tooling + the first 50 parts will be in the $5000+ range.
So you'll need to find someone to front this money, and then you'll have to then find 50 people to buy them for $100 each (and this still doesn't include the rebuilding of the MPS to install the new diaphragm). And that is all just to break even.
Anyway, this is just my estimate of the situation. Once quotes are in, then you can evaluate if it is worthwhile and where the $$ will come from.
Demick |
Your estimate was about 5K cheaper than I thought...I was trying to get a contact in China to make them...but the funding issue killed that idea.......
Bleyseng
Jan 13 2006, 09:17 AM
Let's just break into Brett Inst. and steal their stash of diaphrams!
Where is Miles when you need a good plan!
Demick
Jan 13 2006, 09:38 AM
QUOTE |
Your estimate was about 5K cheaper than I thought...I was trying to get a contact in China to make them...but the funding issue killed that idea....... |
Here's what I wrote sometime last year on the subject:
QUOTE |
The material for the diaphragms is most likely beryllium copper (BeCu). Not really exotic, but is environmentally hazardous to process. Companies like Laird buy it by the ton to make EMI gaskets out of. The material is not really the problem - it is the cost of the tooling to have the correct shape for the diaphragm stamped out. Then the low volume once you've got the tooling paid for. It really all comes down to money. Figure $2K for tooling, and then around $50 each to buy them in low quantities like 25/batch. Then you've still got to have the center boss machined and pressed into the diaphragm - a little more in tooling to create the tools that will press and flare the boss into place. So figure a cost of $100 each for a complete diaphragm. Then you've got the labor to rebuld the MPS, some extra profit to pay off tooling. It all adds up. Hard to justify when you can still get used MPS's for $100 or less (last ones I bought were $15 each at a swap meet). |
This is all even harder to justify when you can buy a Brett Instruments rebuilt unit for just over $200. Some people have complained that the Brett diaphragms are the wrong material and don't have the right response. But my opinon is that the diaphragm response is not all that critical. Sure, it need to be close, but not exact since it only provides the transition from part load to full load enrichment. It's the aneroid cells that are most important in their response and how they expand - not the diaphragm.
Demick
Bleyseng
Jan 13 2006, 10:33 AM
QUOTE (Demick @ Jan 13 2006, 07:38 AM) |
QUOTE | Your estimate was about 5K cheaper than I thought...I was trying to get a contact in China to make them...but the funding issue killed that idea....... |
Here's what I wrote sometime last year on the subject:
QUOTE | The material for the diaphragms is most likely beryllium copper (BeCu). Not really exotic, but is environmentally hazardous to process. Companies like Laird buy it by the ton to make EMI gaskets out of. The material is not really the problem - it is the cost of the tooling to have the correct shape for the diaphragm stamped out. Then the low volume once you've got the tooling paid for. It really all comes down to money. Figure $2K for tooling, and then around $50 each to buy them in low quantities like 25/batch. Then you've still got to have the center boss machined and pressed into the diaphragm - a little more in tooling to create the tools that will press and flare the boss into place. So figure a cost of $100 each for a complete diaphragm. Then you've got the labor to rebuld the MPS, some extra profit to pay off tooling. It all adds up. Hard to justify when you can still get used MPS's for $100 or less (last ones I bought were $15 each at a swap meet). |
This is all even harder to justify when you can buy a Brett Instruments rebuilt unit for just over $200. Some people have complained that the Brett diaphragms are the wrong material and don't have the right response. But my opinon is that the diaphragm response is not all that critical. Sure, it need to be close, but not exact since it only provides the transition from part load to full load enrichment. It's the aneroid cells that are most important in their response and how they expand - not the diaphragm.
Demick |
I disagree......crappy stiff diaphrams make the mps transition response shitty or worse a off/no type. Aneroid cells in for altitude differences I thought although early type 3 MPS don't even have a diaphram!
r_towle
Jan 13 2006, 11:05 AM
so, did someone send the diaphram to Demick to get a drawing produced?
I would like a real price from a real shop (one that handles this material)
We need to get a celar idea what the material is also.
Rich
redshift
Jan 13 2006, 11:17 AM
QUOTE (Bleyseng @ Jan 13 2006, 11:17 AM) |
Let's just break into Brett Inst. and steal their stash of diaphrams!
Where is Miles when you need a good plan! |
Probation.

M
Katmanken
Jan 13 2006, 12:29 PM
Copper sheet would prolly be too soft. Berrylium copper is a spring and can be obtained in various thicknesses and tempers. (full hard, half hard, quarter hard).
I've designed parts using the stuff so I prolly have design info in a box in the basement- somewhere.
Stuff is EXTREMELY TOXIC if ground. Makes a lotta places not want to deal with it.
Anyhoo, stuff aint that hard to emboss features in. Made embossed parts once with little "V"s. Was told it couldn't be done. Off I went. Little fixture, coupla crude dies, wham, bam and workable parts.
Looking at Brad's page, the diaphragm has addressed the same problems I ran into. One, berrylium copper doesn't like to stretch too much without cracking. Two, radii in the embossing areas is critical to good parts, and three, it can be done.
Done a lotta progressive die sheet metal parts and this thing is cake to do - once the dimensions are obtained. Worked with Mr. Brunk (Brunk tooling) a buncha times making formed titanium parts. He was a master die maker from the old school and made unbelievable things with simple dies or from a progressive die line. (steel strip into machine, formed parts on a retainer strip out).
Anywhoo, you need a hardened form die to emboss the plates and a cut die to cut the diameter and punch the holes simultaneously. The hole die can be done easily with EDM wire. The form die has to be machined or ram EDM'd. (burned).
If the dies are right, then the parts could be made repeatably and relaibly. Put a sheet into the form die, and whack it with a BF hammer to form the embossing. More than one whack is ok as the dies prevent overforming the material. Remove from the form die, place in the punch die and whack with a BF Hammer.
Voila, instant part.
So, what to do?
1. Anybody have access to a rockwell hardness tester? Need to find out temper of material
2. Anybody have aloose part and a micrometer? Measure raw material stock thickness away from embossed (stretched) areas- prolly at rim is best.
3. Anybody have access to an optical measuring system? Laser or comparitor. A simple comparitor with XY readouts and a cross sectional slice of the part can do it. Need to pot the diaphragm in clear epoxy so the cut and grind won't distort the part.
Guess what we really need is an engineer with lunchtime access to a company materials lab to get the temper and dimensional info.
Ken
JeffBowlsby
Jan 13 2006, 02:18 PM
1 perfect diaphragm shipped to Demick. It may be worth considering to reuse original inner and outer screws to minimize the cost. These are generally in excellent condition and would only add to the cost if reproduced.
Let me know if you need anything Demick. If the price is right I'd buy in quantity.
r_towle
Jan 13 2006, 02:23 PM
I think that re-using these parts may make it to difficult...
Although, if you devise a process to press the inner fitting in place, then we just need to raw diaphram with the correct size hole....
That would be alot less costly...
Rich
JeffBowlsby
Jan 13 2006, 02:33 PM
There is the diaphragm with a female threaded fixture pressed into it. I know where to obtain the press-on rings for the fixture, but a new fixture would need to be milled and that assembly completed. This is the essential assembly we need as a minimum.
The original inner and outer screws which thread into the fixture are what I am suggesting can be reused. The inner screw looks like some kind of chromium steel with a specially milled 'mushroom' shape where it bears onto the aneroid cell. The outer screw has both inner and outer threads, its a double threaded tube essentially. Both would be costly to fabricate and unnecessary IMHO.
I wish I had a photo it would be immediately clear.
r_towle
Jan 13 2006, 02:43 PM
I got it.
So, lets say hypothetically we get two or three parts made..
Part one is the diaphram, with the correct ridges, and the correct hole
Part two is the fitting (for lack of a better term) that goes into the middle and it is threaded for the outer screw...
Or part two/three is a two piece fitting that can be pressed together from both top and bottom into the diaphram...
The actual installation of the fitting could be done by one of us, versus a shop...If we design it to be that way.
The screws, I agree can be re-used.
Rich
JeffBowlsby
Jan 13 2006, 02:50 PM
Yep thats it. The center fixture (its about a 1/2" OD cylinder with a flange on one end) is simply inserted through the diaphragm center hole, press-fit and contained onto the diaphram with a press-on ring. 2 new custom parts should do it, the ring is off the shelf.
Demick
Jan 13 2006, 02:54 PM
Pics from Brad Anders web site.
First, the diaphragm with inner and outer screws:
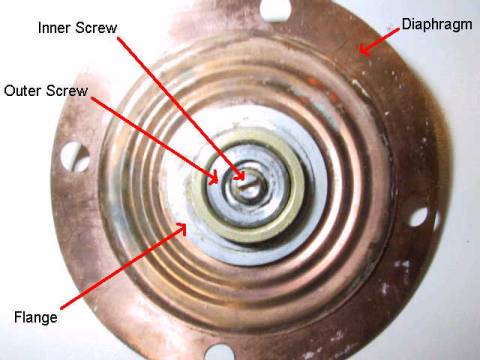
And here is the inner screw:
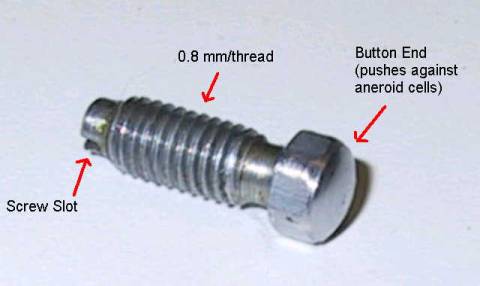
And here is the outer screw:
r_towle
Jan 13 2006, 03:19 PM
Jeff, or Geoff,
Have you guys ever taken one completely apart...
Can the middle section be removed...
I think we need to do this to obtain the correct dimensions for the inner part (s) and the hole in the middle...if we guess, it may not behave the same way.
Rich
Bartlett 914
Jan 13 2006, 03:30 PM
The last part looks like it could be made by modifing a set screw. What are the ID and OD diameters?
I can measure the diaphram in vickers if wanted. We use vickers for measuring the hardness of copper cylinders used in printing. I would need an old diaphram for that.
Mark
Katmanken
Jan 13 2006, 05:21 PM
There is usually a conversion chart or equation for these testers so Vickers shouldn't be a problem.
Is the copper you test hard or soft?
Ken
Bleyseng
Jan 13 2006, 09:07 PM
I don't see how the center part can be taken apart but I'll try tomorrow at the shop. I have NO tools here at home tonight. Actually, I have a extra small screwdriver that I just stabbed myself with trying to pry it apart.
r_towle
Jan 13 2006, 09:11 PM
I will try tommorow also....it didnt grow like that, so it has to be able to come apart....
Rich
Bleyseng
Jan 13 2006, 09:13 PM
yeah, witha BFH and a drift!
I was over at the shop after work today but I can get internet when the neighbors turn on their wireless so I can steal it!
JeffBowlsby
Jan 13 2006, 09:24 PM
The center fixture and pressure ring do not come apart. I tried to cut the ring off with a dremel, no worky. Tried to separate them with a chisel...ruined the chisel.
Don't bother, they need to be fabbed new.
Trust me on this one.
Bleyseng
Jan 13 2006, 10:56 PM
I am going to cut one apart in the morning with a metal chopsaw for fun. They look like they are pressed together with a 20 ton press....
Bleyseng
Jan 14 2006, 06:07 PM
Here is a diaphram cut apart.....damn, I don't see how you can take it apart nor how its put together. Stamped with a press I guess....
r_towle
Jan 14 2006, 09:07 PM
Take a few close ups please...
Side view, I cant see it the way you took the pics...
Rich
Bleyseng
Jan 14 2006, 11:17 PM
Here's another...
The "C" shaped clip is pressed on and then the assembly is stamped to lock it in place. There is no way I can see to reuse these parts.
This is a "lo-fi" version of our main content. To view the full version with more information, formatting and images, please
click here.