Dr Evil
Nov 11 2010, 09:13 PM
Hey Folks,
I am looking to probe your colloective intellect [sound of rubber glove snapping](eeewe). I am about to embarque on a quest to install a 3.0 CIS system onto my bus corvair engine. I can not just put the stock 911 setup onto the engine because the tubes are not set up correctly and it would sit way too proud for my engine bay. So, I am planning to make a simple box plenum with 6 outlets to each cylinder. My intention is to have the distances from the box to the individual cylinders be identical so the box will be about as long as the engine and only as wide as the fuel metering gear. I will have it with 6 stems poking out and will use hose to connect the stems to down tubes bolted to the heads (much like our stock /4 stuff).
Question, I have a cheap flux wire welder that works fine, but I am thinking that I want to make the intake parts out of stainless (do I?) as the mild stuff that was originally on there corrodes and rusts and that is not ok. Can I weld stainless with my ghetto welder? Do I need special wire? This will be non-load bearing for the most part. The welding should be easy once I get the materials and tools needed figured out. I will make a box, weld it, weld stems onto it, yahtzee!
Mike Bellis
Nov 11 2010, 09:22 PM
My Miller Mig will do stainless with special wire and gas. I don't think flux wire will work well. You may be able to weld the stainless with it but your welds will rust and will be weak. Since your a Dr. and wealthy, you should spend $2k on a TIG and the next two years learning how to use it, then build your manifold.
Your runner length should be as equal as possible but slight differences will not be noticed. The injector locations must be equal distance from the cylinders.
Dr Evil
Nov 11 2010, 09:26 PM
I am an INTERN and will be a RESIDENT for the next 2.6 years. This = no $$$. However, I do have friends with TIGs. I wanted to build it myself, but I dont have the $$. Looks like I will be making some calls tomorrow
Dr Evil
Nov 11 2010, 09:28 PM
Oh ya, it is beacuse I lack gas that I will also need to outsource. (welding gas that is)
Mike Bellis
Nov 11 2010, 09:34 PM
You should mock it up with mandrel bends. mark and number them and have your buddy TIG them for you.
Dr Evil
Nov 11 2010, 09:46 PM
That sounds reasonable. Then I can have some fun. Metal oragami
Mark Henry
Nov 11 2010, 09:47 PM
Stainless will rust at the welds, but for what your doing it doesn't matter. Keep the welds on the outside and lap the major seams. Put them on the bottom so you can't see them much.
Or just use mild steel and get it powdercoated.
Here's two DYI's on making a good plenum:
http://www.sdsefi.com/techinta.htmhttp://www.sdsefi.com/air12.html
Mark Henry
Nov 11 2010, 09:50 PM
Nice
Dr Evil
Nov 11 2010, 09:51 PM
I guess I can powder coat now that I think about it. The fuel will be introduced at the head so it will only be air in the plenum. Duh. WIth the carb, the fuel eats away paint over time and then I am back to square one. Yet another reason my CIS is a better deal.
Dr Evil
Nov 11 2010, 09:52 PM
QUOTE(Mark Henry @ Nov 11 2010, 10:50 PM)

Nice
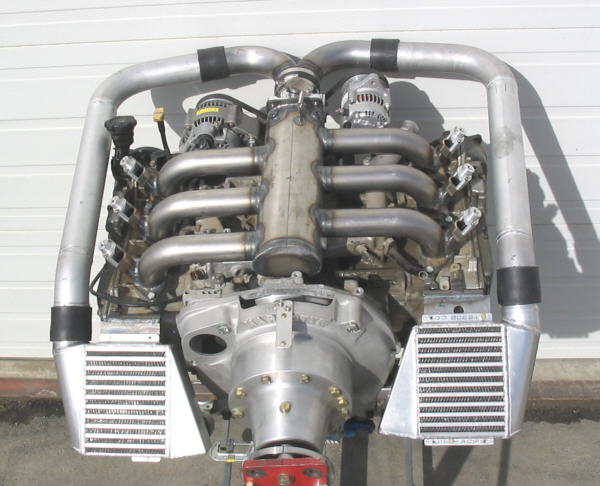
that......is....SEXY!!!!
Mark Henry
Nov 11 2010, 09:55 PM
QUOTE(Dr Evil @ Nov 11 2010, 10:51 PM)

The fuel will be introduced at the head so it will only be air in the plenum. Duh.
Yep
QUOTE
that......is....SEXY!!!!
yep
Mark Henry
Nov 11 2010, 09:57 PM
Bottom looks nice as well
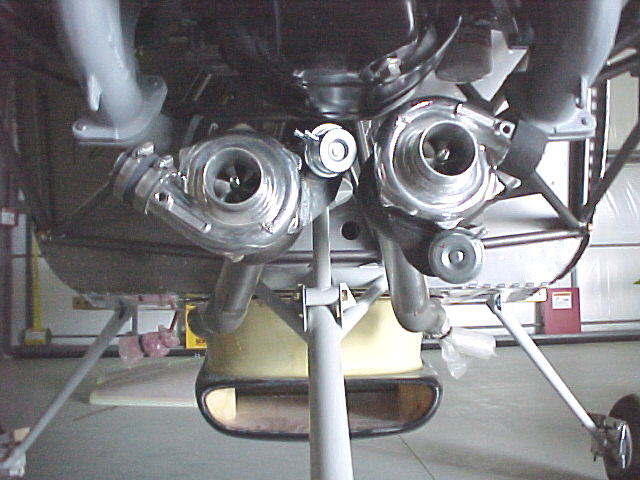
Dr Evil
Nov 11 2010, 10:00 PM
Ooooh, I need a wet nap
RJMII
Nov 11 2010, 10:06 PM
QUOTE
Ooooh, I need a wet nap
me too...
sean_v8_914
Nov 11 2010, 10:23 PM
what about composits? Phillip, a 914 world member was an engineering student. he graduated. while at SDSU, he was on teh formula SAE team. they made their intake system out of carbon fiber but FG might work just as well but less sexy.
GeorgeRud
Nov 11 2010, 10:55 PM
Welding stainless is quite hard and an art in itself when done well. I'd also think that steel with a powder coating would be the best all around choice.
Dr Evil
Nov 11 2010, 11:08 PM
I am going steel with powder. It allows me to do it myself and is good enough for my tank.
strawman
Nov 11 2010, 11:33 PM
QUOTE(Dr Evil @ Nov 11 2010, 07:28 PM)

Oh ya, it is beacuse I lack gas that I will also need to outsource. (welding gas that is)
Glad you clarified that... based on your prodigious emissions at Tahoe, I was gonna call
Dr Evil
Nov 11 2010, 11:45 PM
You and numerous others.
Andyrew
Nov 12 2010, 01:37 AM
What kind of flux core do you have? A lot of them can easily convert with about 60 bucks in parts (plus your tank and gas), Then you can run dual shield till you run out of wire and then get a true mig wire later..
HIGHLY recommended... You dont want to have to deal with pinhole leaks on an intake setup...
Dr Evil
Nov 12 2010, 11:50 AM
Thats what they make JB weld for

seriously, I should do gas. I welded with it for the first time a few months ago and was impressed at how beautiful the welds came out.
rick 918-S
Nov 12 2010, 07:53 PM
Here's a good read.
http://www.welding-advisers.com/Welding-stainless.htmlStainless steel is complicated but not impossible to weld. Done incorrectly the welds will still rust. Order some mild steel mandrel bent tubing and mig or gas weld it. Then powder coat it.
Dr Evil
Nov 12 2010, 08:32 PM
Chances are I can fab the whole shooting match up with exhaust pieces. I already have a few

I am off tomorrow so between rebuilding transmissions, doing things around the house, and workign on my projects, I will look into this
Dr Evil
Nov 12 2010, 08:37 PM
QUOTE(Andyrew @ Nov 12 2010, 02:37 AM)

What kind of flux core do you have? A lot of them can easily convert with about 60 bucks in parts (plus your tank and gas), Then you can run dual shield till you run out of wire and then get a true mig wire later..
HIGHLY recommended... You dont want to have to deal with pinhole leaks on an intake setup...
Harbor Freight 90amp $100 unit
rick 918-S
Nov 12 2010, 08:40 PM
QUOTE(Dr Evil @ Nov 12 2010, 08:32 PM)

Chances are I can fab the whole shooting match up with exhaust pieces. I already have a few

I am off tomorrow so between rebuilding transmissions, doing things around the house, and workign on my projects, I will look into this

You should use mandrel bent stuff not some old crushed corner exhaust pipe. Also you need to consider the movement of air through the tube. I may get cold and condensate. If the inside of the tubing is not powder coated it will begin to rust over time.
Another option is using an 1/8 wall aluminum tube. You could gas weld it and the thicker wall (and the aluminum) may hold heat better keeping it and the air charge dry.
Here's an aluminum intake I shortened. I gas welded it back together.
okieflyr
Nov 12 2010, 08:42 PM
I've found these to be helpful.
http://www.mandrel-bends.com/catalog/mandrel-bends-34/I've also found that welding with the gas setup is so much nicer as it has less splatter and gives cleaner welds. We have an IR oven at work, so we've been playing around with powder coating lately.
speed metal army
Nov 12 2010, 11:56 PM
You should just tack what you have together,and send it to me.I'll TIG it together (SS only),in trade for some 914 stuff.Dont even think of MIG welding it.We can make it beautiful if required.Its what we do.
Dr Evil
Nov 13 2010, 11:06 AM
Rick, when you say gas are you referring to oxy/acetylene? I am less likely to make it out of aluminum as I dont have a big center pipe that would easily work like steel. I will just make it out of steel and powder coat it. Simple, easy, cheap, I can do it myself. The current setup has pipes, this will be similar so I see no need to worry about design issues other than coating the metal.
SMA, that is a kind offer for trade, but I have a guy on my side of the world that has and does TIG for me
rick 918-S
Nov 13 2010, 02:54 PM
QUOTE(Dr Evil @ Nov 13 2010, 11:06 AM)

Rick, when you say gas are you referring to oxy/acetylene? I am less likely to make it out of aluminum as I dont have a big center pipe that would easily work like steel. I will just make it out of steel and powder coat it. Simple, easy, cheap, I can do it myself. The current setup has pipes, this will be similar so I see no need to worry about design issues other than coating the metal.
SMA, that is a kind offer for trade, but I have a guy on my side of the world that has and does TIG for me

Ya, Aluminum. You can gas weld it with an Oxy/Acetylene torch set. Aluminum is cool.
r_towle
Nov 13 2010, 04:24 PM
QUOTE(rick 918-S @ Nov 13 2010, 03:54 PM)

QUOTE(Dr Evil @ Nov 13 2010, 11:06 AM)

Rick, when you say gas are you referring to oxy/acetylene? I am less likely to make it out of aluminum as I dont have a big center pipe that would easily work like steel. I will just make it out of steel and powder coat it. Simple, easy, cheap, I can do it myself. The current setup has pipes, this will be similar so I see no need to worry about design issues other than coating the metal.
SMA, that is a kind offer for trade, but I have a guy on my side of the world that has and does TIG for me

Ya, Aluminum. You can gas weld it with an Oxy/Acetylene torch set. Aluminum is cool.
Stop showing off...
rick 918-S
Nov 13 2010, 04:53 PM
QUOTE(r_towle @ Nov 13 2010, 04:24 PM)

QUOTE(rick 918-S @ Nov 13 2010, 03:54 PM)

QUOTE(Dr Evil @ Nov 13 2010, 11:06 AM)

Rick, when you say gas are you referring to oxy/acetylene? I am less likely to make it out of aluminum as I dont have a big center pipe that would easily work like steel. I will just make it out of steel and powder coat it. Simple, easy, cheap, I can do it myself. The current setup has pipes, this will be similar so I see no need to worry about design issues other than coating the metal.
SMA, that is a kind offer for trade, but I have a guy on my side of the world that has and does TIG for me

Ya, Aluminum. You can gas weld it with an Oxy/Acetylene torch set. Aluminum is cool.
Stop showing off...

Just tryin ta hep.
jd74914
Nov 13 2010, 06:43 PM
I've made both aluminium and steel intake manifolds (though only for inline-4 motorcycle engines), and given your tools I would recommend staying with mild steel or going composite. That said, if you went with a composite plenum you could really make it in all sorts of cool shapes.
As far as working with steel is concerned, you would probably be ok welding mandrel bends with a flux core welder provided you were going to smooth out the welds after the fact to make it look pretty. I'm not sure how well powder coat holds up to repeated contact with gas, so I'd look into coating the insides with a gas tank sealer like the epoxy one made by Caswell Plating. The secondary benefit of an internal coating is that it will help seal any of the inevitable pinhole leaks.
Dr Evil
Nov 13 2010, 07:57 PM
There will be nothing but air going through the plenum. It is going to be fuel injected at the head so no worry of fuel erosion
rick 918-S
Nov 13 2010, 08:15 PM
QUOTE(Dr Evil @ Nov 13 2010, 07:57 PM)

There will be nothing but air going through the plenum. It is going to be fuel injected at the head so no worry of fuel erosion

CIS works good.
jd74914
Nov 13 2010, 10:39 PM
QUOTE(Dr Evil @ Nov 13 2010, 08:57 PM)

There will be nothing but air going through the plenum. It is going to be fuel injected at the head so no worry of fuel erosion

The amount of fuel that reverts to the plenum is surprising. These are different style intakes with shorter runners (the injectors are still near the head), and engines running much wackier cams, but from what I have seen it is not unusual for the inside of the plenum to be coated.
That said, its not nearly the amount that the lower runner area sees so it might not be of any concern. The last intake we built was rapid prototyped ABS plastic and even that small fuel coating was a concern so we ended up coating the entire thing.
And now for a picture hijack.
Dr Evil
Nov 13 2010, 10:59 PM
I am trying to follow the stock design which used mild steel, exterior chrome, no coating inside and that was for a carb mounted on one end. I dont want to over engineer this. Well, I do, but I want to use it before I die.
rick 918-S
Nov 13 2010, 11:08 PM
Doc, What is your cam profile? CIS may like a long duration to avoid excessive pulsing of the air door. Others may know more about that than me.
Krank
Nov 14 2010, 01:14 AM
If the bus is going to be parked for any extended lengths of time, definitely go with stainless! Stainless if done correctly with the correct filler materials will not rust! How many stainless steel hand rails at the nearest Federal building do you see rust on the joints? They are first prepped, welded, then ground and buffed so you cannot even see the joint....but they are there. Just the temperature change from running from peak operating temperature (heavy city traffic) to cooling off after coming home from a late night party in possibly a damp low of 45 degrees can cause condensation inside the plenum. Condensation can even form (and rust) inside a fuel tank given the right conditions. There is more than one reason manufacturers are going to plastic tanks. A number of manufacturers are starting to use mild steel for intake plumbing but I mostly see that on Russian farm equipment. Swap some tranny service (not the late night kind) and do it once without worries. Have you ever slapped in leather in to a main bearing location because it will work?
Katmanken
Nov 14 2010, 12:04 PM
Here ya go Evil!
If these guys can do non-rusting composite intake parts, so can you!
Dr Evil
Nov 14 2010, 12:11 PM
QUOTE(rick 918-S @ Nov 14 2010, 12:08 AM)

Doc, What is your cam profile? CIS may like a long duration to avoid excessive pulsing of the air door. Others may know more about that than me.
Excellent point. I had the CIS system before I got the engine together so I anticiapted this. I chose a mild cam as a wild one would make the bus kinda suck to drive and would not work with the CIS.
For the plenum, I am doing fast, easy, and now. I will make it all pretty in the future and have my buddy weld it up in beautiful stainless

Composite is unnecessary for my application. I am not interested in the weight reduction nor the commitment that buying all the materials and makng them would take. All hail Russian farm equipment!

"Have you ever slapped in leather in to a main bearing location because it will work?"

are you trying to say???
Andyrew
Nov 14 2010, 01:23 PM
Dr,
I agree with everyone who says tack it and have someone weld it... That HF welder wont cut it, I know, I owned one.
Dr Evil
Nov 14 2010, 01:39 PM
Now I gotta try.
Andyrew
Nov 14 2010, 11:09 PM
Lol,
Eh... knowing you I should have gone with reverse psychology.
Dr Evil
Dec 1 2010, 09:36 PM
OK, I have been doing research and pricing. It looks like it would be easy to do the plenum in 4" x 6" x 12" or 4x4x12. I am not sure about which one to go with. The intake pipes are 1.5", 1/8" wall.
speed metal army
Dec 1 2010, 09:41 PM
QUOTE(Andyrew @ Nov 14 2010, 11:23 AM)

Dr,
I agree with everyone who says tack it and have someone weld it... That HF welder wont cut it, I know, I owned one.
Word.(gad I had that expression)
Send it to us.We will do it for free,if you post the quaility you recieve.
GS Guy
Dec 2 2010, 06:44 AM
Maybe a length of this oval tubing would be a good start for the center plenum section? All you'd need is a "scap piece" length - might go cheap?
They show a 5" size now for special order - see if they have some test/throw away pieces they could send you a sample of.
http://drgas.mybisi.com/products/oval-tubing-and-bends
charliew
Dec 2 2010, 09:58 AM
On nasioc there is a discussion of plenum capacity for motor volume I was thinking it was 1.5 to motor volume as in 2liters motor to 3liter plenum volume. That might also be for a turbo motor though but they still run most of the time na.
Google plenum volume thats also including runners
http://speedtalk.com/forum/viewtopic.php?t=1142
VaccaRabite
Dec 2 2010, 11:24 AM
Mike, if you have the metal and want to weld it, I converted my welder to gas, and you are welcome to do it next weekend when you come over.
Zach
Borderline
Dec 2 2010, 06:43 PM
QUOTE(Dr Evil @ Dec 1 2010, 07:36 PM)

OK, I have been doing research and pricing. It looks like it would be easy to do the plenum in 4" x 6" x 12" or 4x4x12. I am not sure about which one to go with. The intake pipes are 1.5", 1/8" wall.

"1/8 wall" You're making an intake system not a roll bar!! Hell they don't even use 1/8 wall on roll bars!! How about 1/16" (16ga)???
Hi Mike! It's been a while.
Dr Evil
Dec 2 2010, 07:32 PM
Dude, 1/8" is the thinnest and is fine. Most plenums are like 1/4" (big!). I am now calculating the volume to figure out what sizes to use.
This is a "lo-fi" version of our main content. To view the full version with more information, formatting and images, please
click here.