I would agree with Andy based on the bottom photo.
In the case on this photo, I'd clean that up with ospho, neutralize the ospho,
coat it with about 4 coats of Zero Rust, and put in good patches and then the Mad Dog kit.
You wont be able to weld through the Zero Rust, so keep that in mind.
I know you want to have the best car you can,
but also remind yourself that this is not going to be a $100K original six.
Its your car - The only other thing I would say is,
whatever your decision to proceed is - enjoy it.
QUOTE(pploco @ Sep 23 2019, 09:40 AM)

I decided to spend some time cleaning up some of the rust in the interior. I got out the wire wheel and started cleaning up some of the metal around the passenger footwell. Cut out the rusted bit, and welded in a patch.

Feeling pretty good about myself, I worked my way back stripping the floor down and really digging into the pitted spots. With the exception of one small spot under the passenger seat, there were no pinholes or spots needing repair. Overall it looked pretty good. That is until I saw what was peeking out from behind the firewall
I found a few spots on the passenger firewall that I started poking and digging out with a screwdriver. Before too long, the cutter came out and I ended up with this:
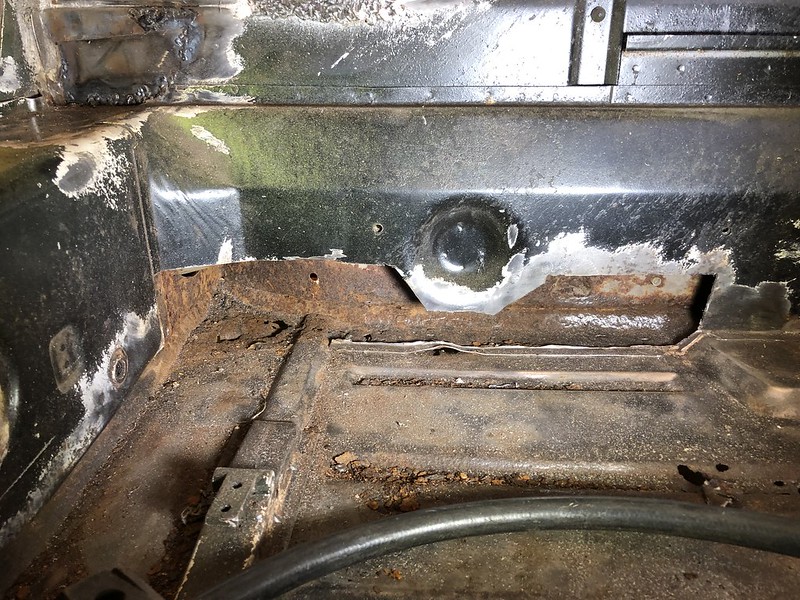
Now I'm afraid to see what the driver's side has hiding. What a friggin setback... Oh well. I think to do this right, I'm going to have to get it up on a rotisserie to fix the rear pan, and I'm super tempted to have the whole tub media blasted. I hope (fingers crossed) that the longs are still okay. I know there's a small spot under the hell hole, but everything else looks pretty solid.
I've heard it said here many times - its never the rust you can see in these cars, its what you can't see. Well, here's proof to that.