John
Jan 8 2012, 01:39 PM
QUOTE(rohar @ Jan 7 2012, 09:59 AM)

It would be a travesty if anyone over the age of 20 in this country didn't.
I am and I dont, so it must be a travesty. (BTW, I don't want to know) I know you guys out in CA have your own lifestyles, and it's none of my business.
Nice project by the way. It should be interesting to see it all work out.
yellowporky
Jan 8 2012, 02:37 PM
I believe that Rohar is in washington state. Not sure what they are into up there.
BMITCHELL
Jan 8 2012, 02:46 PM
For you younun's that was from the cult movie "Rocky Horror Show"
rohar
Jan 8 2012, 07:13 PM
And nobody picked up on the term "travesty" from the German "Travesty Cabaret".
Alright, I'll stop with the obscure tranny jokes and get back to work...
rohar
Jan 15 2012, 03:46 PM
Alright, engine and tranny are out for a while. Waiting on parts and have a LOT of work to do on the chassis. So back to rust abatement we go.
Anyone know a good howto thread on removing the motor tin shelf that runs along the long?
strawman
Jan 16 2012, 01:18 AM
QUOTE(rohar @ Jan 15 2012, 01:46 PM)

Anyone know a good howto thread on removing the motor tin shelf that runs along the long?
If you're removing them for good / not trying to salvage the shelf, I found it easiest to use an angle grinder and/or an air die grinder with a 3" cutting wheel to grind off the spot welds -- much faster than spot weld cutters. And if done slowly/judiciously you won't have to fill in the little circles left by the cutters.
Just grind the area of each spot weld until it is paper-thin, then carefully pry it away. Easy-peezy, especially after you get the hang of it.
Geoff
rohar
Jan 16 2012, 01:22 AM
It's been a couple hours and nobody replied, so I improvised with the grinder, seems to be my default. You don't want to know what happens when the wife leaves me without direction in the bedroom.
Seems much of my near future is grind, weld, grind, weld repeat until dead.
Andyrew
Jan 16 2012, 12:01 PM
Sawzall and a grinder would have been my choice.. I havent removed mine so I cant give you first hand experience.
rohar
Jan 18 2012, 08:35 AM
Ok, things are going slow lately. I'm not as mobile as I'd like and it's cold as hell in the shop. Some progress though, I managed to find cheep off the shelf axles for this conversion. By sheer luck, the driver's side axle off an early MKII Golf is a perfect match after the thickness of the flange adapters on the tranny.
One less thing to worry about, it's been nagging on my mind.
rohar
Feb 17 2012, 09:09 PM
More parts arrived today. I've got an airbox!
Problem is it's too damned tall, this isn't gonna fit under the engine lid:
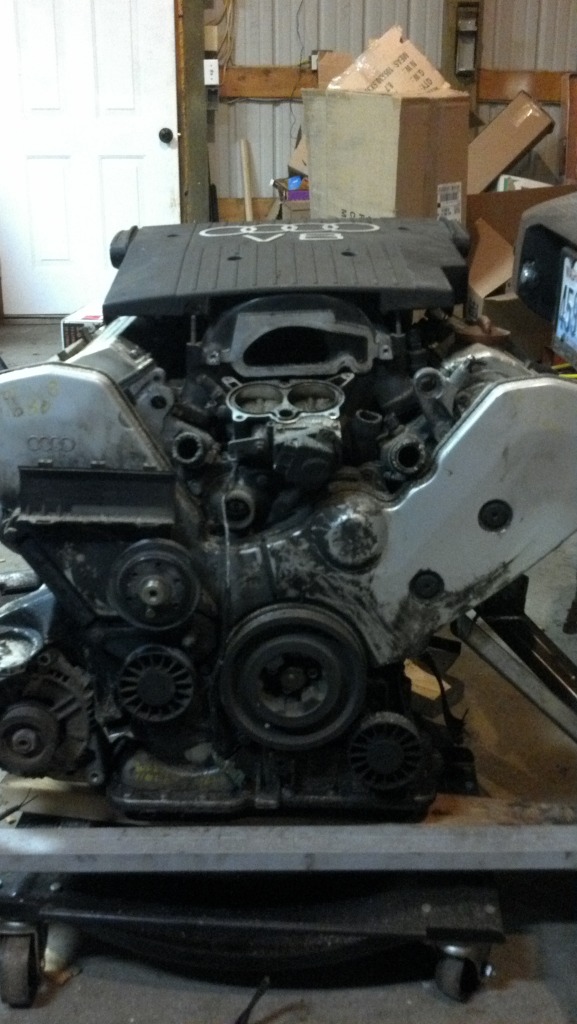
On the up side it didn't cost much and I've now got a plug to mold something that works. Who's dumb idea was it to put an Audi V8 in a 914 anyway?
rohar
Apr 15 2012, 02:46 PM
Alright, I'm shelving the v8 for now. I know, sad news and all. Just too many details to sort out and still get this car running this spring so v6 it is.
Got a little sidetracked, had to build one of these for the wife's goats:
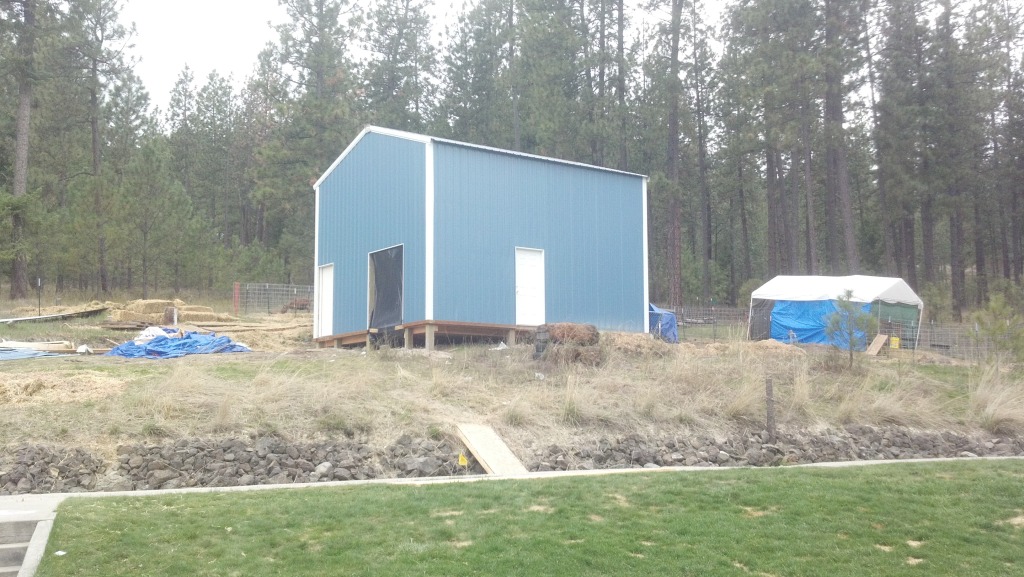
Took a while as I couldn't drive up there, with all the rain the clay soil turned to grease. Had to hump all the materials up that hill by hand. Happy wife happy life, what are ya gonna do?
Anyway, back to car business:
Ordered a new clutch and pressure plate Friday. Turns out the PP from the 30v v6 bolts up and has an integrated 60-2 trigger so that makes that part easy for the MS install. It's dual mass so I can use a solid center clutch from Kennedy and not get that "snap" that normally happens.
Lately there's been both time and money. This never happens. I just wasn't happy with the motor mounts I made so this happened:
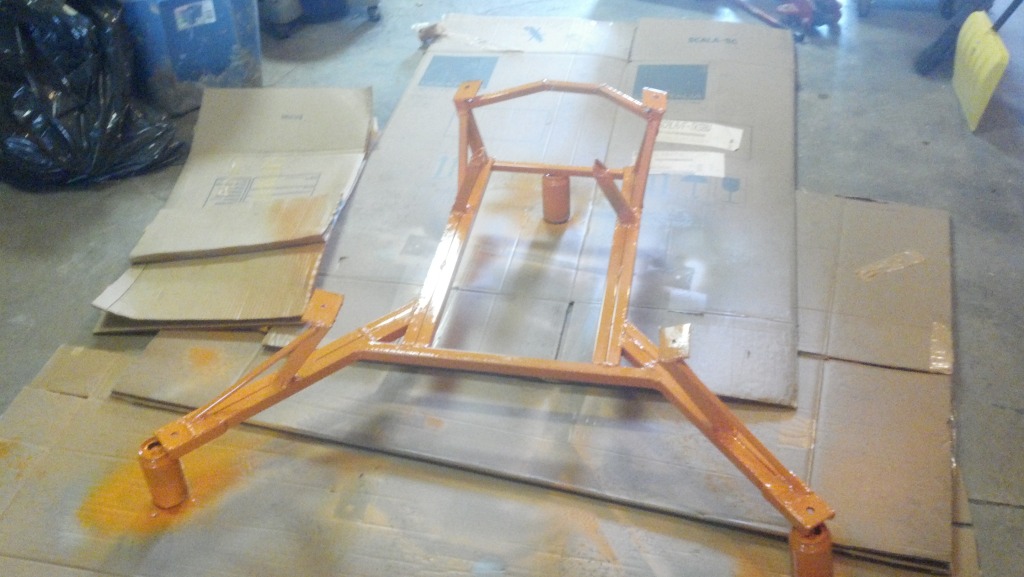
Now to wait for paint to dry and gut what's left of the interior...
rohar
Apr 18 2012, 07:18 PM
After a little blasting, that hell hole isn't so hellish after all. I'm gonna toss some more metal in there shortly just 'cause.
rohar
Jun 14 2012, 05:55 PM
WOOHOO! Clutch/flywheel solution is DONE! Flywheel's even got an integrated trigger wheel for the megasquirt!
JRust
Jun 14 2012, 06:43 PM
QUOTE(rohar @ Jun 14 2012, 04:55 PM)

WOOHOO! Clutch/flywheel solution is DONE! Flywheel's even got an integrated trigger wheel for the megasquirt!
tomeric914
Jun 14 2012, 07:17 PM
QUOTE(rohar @ Apr 15 2012, 04:46 PM)

I just wasn't happy with the motor mounts I made so this happened:
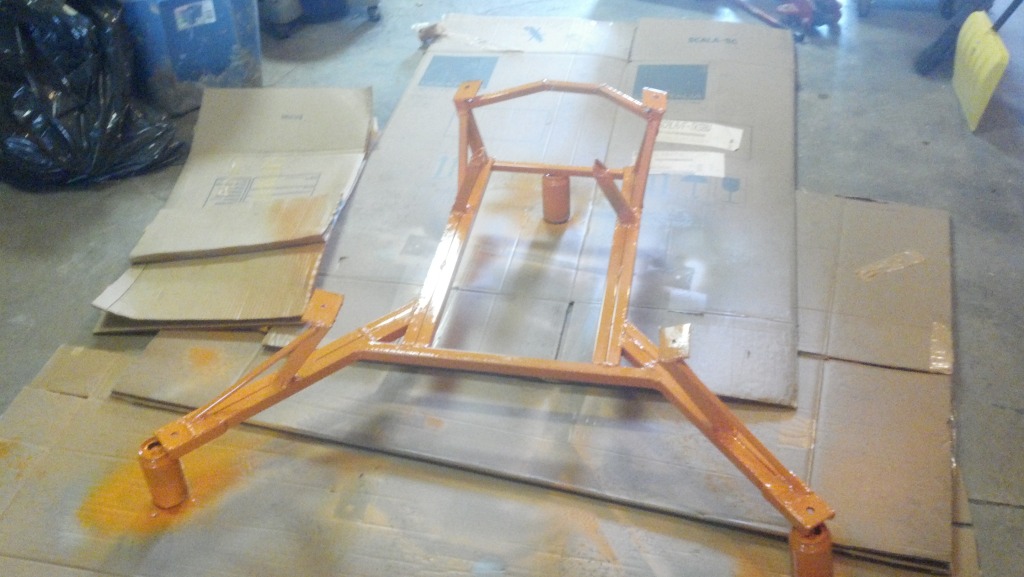
What size square tubing did you use? With all due respect, it looks too light.
rohar
Jun 14 2012, 08:22 PM
QUOTE(JRust @ Jun 14 2012, 05:43 PM)

QUOTE(rohar @ Jun 14 2012, 04:55 PM)

WOOHOO! Clutch/flywheel solution is DONE! Flywheel's even got an integrated trigger wheel for the megasquirt!

Sure, now that it's done you want picks?!
Sadly, I forgot to replace the pilot bearing when I put it together, guess it's coming apart again. Pics to follow.
rohar
Jun 14 2012, 08:27 PM
QUOTE(tomeric914 @ Jun 14 2012, 06:17 PM)

What size square tubing did you use? With all due respect, it looks too light.
It does doesn't it? 1" 12ga obviously doubled on the laterals and stitch welded with 1/2" solid diagonals on the forward mounts gusseted..
The math works out, the mount points will recover from a 500lb pressure deflection. Since the engine is only producing about 300lbs (ish) at those points all will be well if I managed to push some decent welds.
I agree though, it LOOKS dainty.
tomeric914
Jun 14 2012, 09:54 PM
QUOTE(rohar @ Jun 14 2012, 10:27 PM)

It does doesn't it? 1" 12ga obviously doubled on the laterals and stitch welded with 1/2" solid diagonals on the forward mounts gusseted..
The math works out, the mount points will recover from a 500lb pressure deflection. Since the engine is only producing about 300lbs (ish) at those points all will be well if I managed to push some decent welds.
I agree though, it LOOKS dainty.
Doubled horizontally (as compared to a single 1" square tube), the deflection is roughly cut in half.
Doubled vertically, deflection in this case would be reduced by a factor of 4.
There will be a lot of different forces at work. My concern is the basic vertical load. A 500 lb static load may result in deflection of 0.1" and a max stress in the range of 10ksi. A shock load (speed bump, railroad tracks, pot hole, etc.) could be 5 times that resulting in stresses higher than the material (and welds) can handle, especially when repeated.
Your design may be perfectly fine, I can only comment based on the picture and information given.
JRust
Jun 14 2012, 11:20 PM
QUOTE(tomeric914 @ Jun 14 2012, 08:54 PM)

QUOTE(rohar @ Jun 14 2012, 10:27 PM)

It does doesn't it? 1" 12ga obviously doubled on the laterals and stitch welded with 1/2" solid diagonals on the forward mounts gusseted..
The math works out, the mount points will recover from a 500lb pressure deflection. Since the engine is only producing about 300lbs (ish) at those points all will be well if I managed to push some decent welds.
I agree though, it LOOKS dainty.
Doubled horizontally (as compared to a single 1" square tube), the deflection is roughly cut in half.
Doubled vertically, deflection in this case would be reduced by a factor of 4.
There will be a lot of different forces at work. My concern is the basic vertical load. A 500 lb static load may result in deflection of 0.1" and a max stress in the range of 10ksi. A shock load (speed bump, railroad tracks, pot hole, etc.) could be 5 times that resulting in stresses higher than the material (and welds) can handle, especially when repeated.
Your design may be perfectly fine, I can only comment based on the picture and information given.
All I know is it looks Orange

Holy crapola we have some smart teeners out there. You actually did the math & engineered it? For a messed up build that has nothing right. Sounds like you know what your doin
rohar
Jun 14 2012, 11:28 PM
QUOTE(JRust @ Jun 14 2012, 10:20 PM)

All I know is it looks Orange

Holy crapola we have some smart teeners out there. You actually did the math & engineered it? For a messed up build that has nothing right. Sounds like you know what your doin

Don't get too excited, this is somewhere between rocket science and "hold my beer, this'll be cool".
Plenty of time and decisions left to screw everything up.
JRust
Jun 14 2012, 11:48 PM
mittelmotor
Jun 14 2012, 11:53 PM
A very ambitious build, Rohar! A fun thread to follow.
I have limited fabrication skills, so I'm doing a Renegade conversion with an LS1. Question: What do you use to cut the sheet metal for the openings? I was hoping to use a reciprocating saw with a carbide blade, and then do some finish grinding to neaten it up. Are you doing something similar?
Also, what size rear tires do you have? I want to fit 225/50-15s on 15x7 ATS wheels. Tonight's project was rolling the lip and pulling the fender out about 1/2" on the driver's side.
Thanks!
rohar
Jun 15 2012, 08:33 AM
Cheep jig saw from ACE (you know, the helpful place!) and a couple of bimetal blades. There's some tricky spots in there so I cut the deck on the saw down to a sliver so it wouldn't be in the way in some places. 1" hole saw for the corners, I wanted pretty radiuses. It goes pretty quick, but WEAR EYE PROTECTION. You're gonna bust a couple of blades and they'd suck if they stuck you in the eye.
I've got some interesting ideas on how to treat the cut edges that should abate flex cracking and make things a bit prettier. Stay tuned.
Tires are currently 225/45/17s on Enkeis. I'm not sure I'm gonna stick with the tires. They look a little too low profile for me.
rohar
Jun 15 2012, 08:41 AM
QUOTE(tomeric914 @ Jun 14 2012, 08:54 PM)

Doubled horizontally (as compared to a single 1" square tube), the deflection is roughly cut in half.
Doubled vertically, deflection in this case would be reduced by a factor of 4.
There will be a lot of different forces at work. My concern is the basic vertical load. A 500 lb static load may result in deflection of 0.1" and a max stress in the range of 10ksi. A shock load (speed bump, railroad tracks, pot hole, etc.) could be 5 times that resulting in stresses higher than the material (and welds) can handle, especially when repeated.
Your design may be perfectly fine, I can only comment based on the picture and information given.
If it were possible to go vertical, trust me I would have. Because of where everything ends up (half shafts, exhaust etc) there just isn't room for bigger steel.
Once the engine/tranny are back together I'll bolt it all up with the bigger assemblies and reassess. Thanks for the input though, that's a big part of why we post these things in the community!
mittelmotor
Jun 15 2012, 11:07 AM
QUOTE(rohar @ Jun 15 2012, 07:33 AM)

Cheep jig saw from ACE (you know, the helpful place!) and a couple of bimetal blades. There's some tricky spots in there so I cut the deck on the saw down to a sliver so it wouldn't be in the way in some places. 1" hole saw for the corners, I wanted pretty radiuses. It goes pretty quick, but WEAR EYE PROTECTION. You're gonna bust a couple of blades and they'd suck if they stuck you in the eye.
I've got some interesting ideas on how to treat the cut edges that should abate flex cracking and make things a bit prettier. Stay tuned.
Tires are currently 225/45/17s on Enkeis. I'm not sure I'm gonna stick with the tires. They look a little too low profile for me.
Thanks! I'm a ways off from cutting...I'm waiting on Renegade's cooling package, and there might be a template with it for the cooling exit holes.
Yeah, I know what you mean about sidewalls. These cars call out for a substantial sidewall. But the ones I have now are terrible....195s with a 65 aspect ratio. They look like big glazed donuts!
rohar
Jun 15 2012, 02:58 PM
As promised, trigger solution:
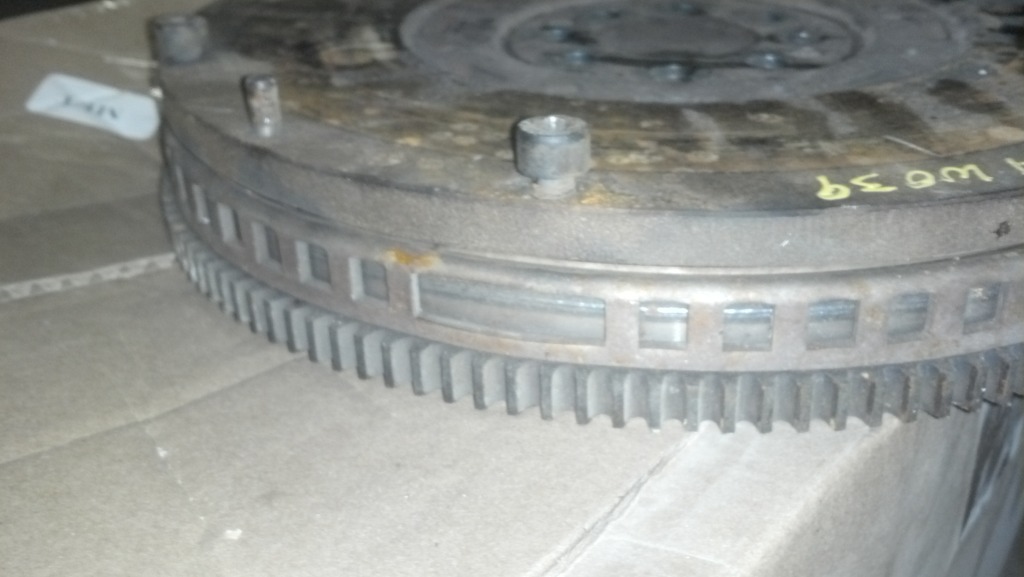
It's dual mass so it's heavy as hell and doesn't leave much option for lightening it. On the up side, I can run cheap solid center clutches and there's one less thing to fabricate.
There's even a mount point in the bellhousing for the hall sensor. The VAG parts bin is awesome.
rohar
Aug 6 2012, 07:26 PM
Ok, I've been neglecting the 914. I'm a bad man and I should feel bad. I can't help myself, the 944 is like 2 weeks away from being track ready so it's taking up the lion's share of my time. That said, I did procure these for the teener today. $275 for the pair, never used, only test fit. With ajustable sliders:
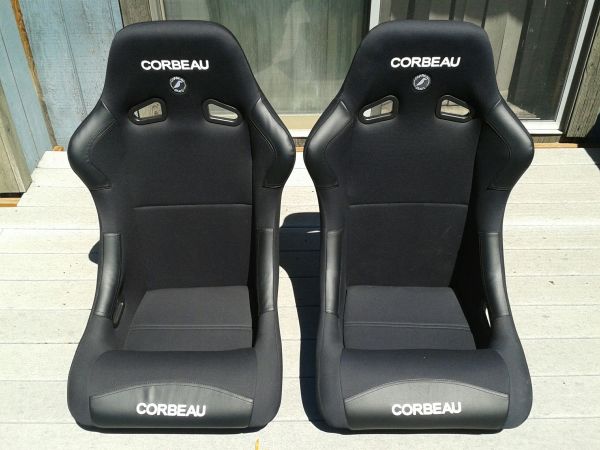
Gotta love craigslist!
speed metal army
Aug 6 2012, 08:35 PM
Assho!i want a deal like that!
Nice!
aircooledtechguy
Aug 7 2012, 05:39 PM
Way to go!! I like those, but they're a little snug for my , ummm "full figured teener @ss"
rohar
Oct 11 2012, 05:53 PM
So I've got this groupie that won't leave me alone. He's kindof a nice guy, but he pushes my ass into productivity. Honestly, some mornings, it seems more than I can take. He's the reason the '44 is up and ripping. I love him for that and hate him all at the same time.
He stole my beutiful seats and stuck them in the '44. Meh, such is life.
After many conversations in the shop, most of which sounded a lot like "you can't put that 6 in that car when there's an 8 sitting right over there" things got exciting this week. The six is officially on the scrap heap and I'll never speak of it again. The yoke is being modified for the 3.6. Given what that silly little '44 did this weekend, what happens from here will probably be epic on many levels. Here's to the next messed up chapter!
/still kinda want my damned seats back :|
Mike Bellis
Oct 11 2012, 08:37 PM
![popcorn[1].gif](http://www.914world.com/bbs2/style_emoticons/default/popcorn[1].gif)
Is it done yet?
rohar
Oct 11 2012, 09:15 PM
Not yet. Obligatory fuzzy picture for the day, progress however small:
Mike Bellis
Oct 11 2012, 09:19 PM
Hurry up already!
We need another active Audi conversion thread!!!
Oh yea, Give Sir Andy back his camera and get one with auto focus...
rohar
Oct 11 2012, 09:23 PM
Yeah yeah yeah. If it helps, I'm moving much faster than normal lately. Damned driver works evenings so he shows up at some god awefull hour in the morning to give me the to do list. Spring's gonna be a riot. One race care in pocket and another on the way.
Andy, sorry about stealing your camera. I couldn't help myself.
rohar
Oct 12 2012, 01:34 PM
Woot! I've just been given an offer on the '44. Sometimes things just come together. Gonna run through some numbers, but it looks good. Budget for the teener!
We're all going to die...
rohar
Oct 12 2012, 03:23 PM
I know, terrible question to ask on your wedding day, but do you mind if I put this in through the rear?
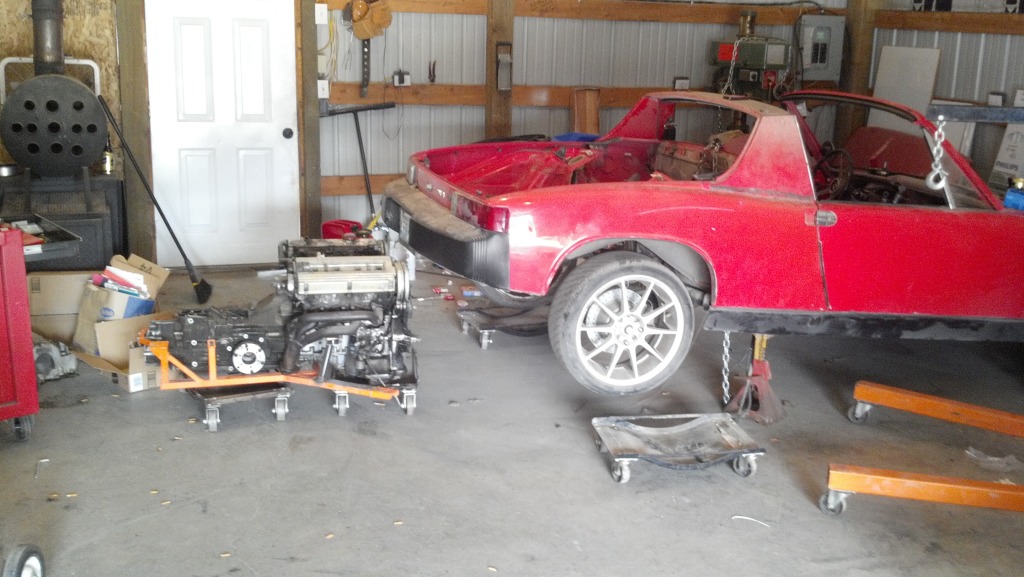
Oh, and yes, there's a lot more metal to add to that yoke, test fit.
aircooledtechguy
Oct 12 2012, 09:18 PM
OH MY GAWD!!! WHAT HAVE YOU DONE?!?!?!?
No really, are you done yet??????
rohar
Oct 12 2012, 09:39 PM
Tough end to the day. Somehow I'm an inch off on one of my dimensions. Car goes back up in the air and the engine comes out one more time. Then I think it's time for a shopping spree.
sixnotfour
Oct 13 2012, 08:46 PM
judging by the smoke in your pics, It appears you may have Burned an inch.
rohar
Oct 13 2012, 08:58 PM
I'm having one of those evenings. Go out to the shop, lay things out, get to work for all of 30 minutes then come back in to think as I've run out of steam. You're not helping there buddy!
Oh, and it's all those years of telling girls it's only 6 inches, it's warped my perspective as I'm starting to believe it.
Mike Bellis
Oct 13 2012, 10:03 PM
I double dog dare you to make it drive-able by WCR 2013!
rohar
Oct 13 2012, 10:23 PM
QUOTE(kg6dxn @ Oct 13 2012, 09:03 PM)

I double dog dare you to make it drive-able by WCR 2013!
The new deadline is May 1. He's nastier than you are. I may be buggered.
It might not be pretty, but it'll be mechanically sound and drivable by then. Welcome to the marathon.
rohar
Oct 14 2012, 12:42 AM
Ok, it got real:
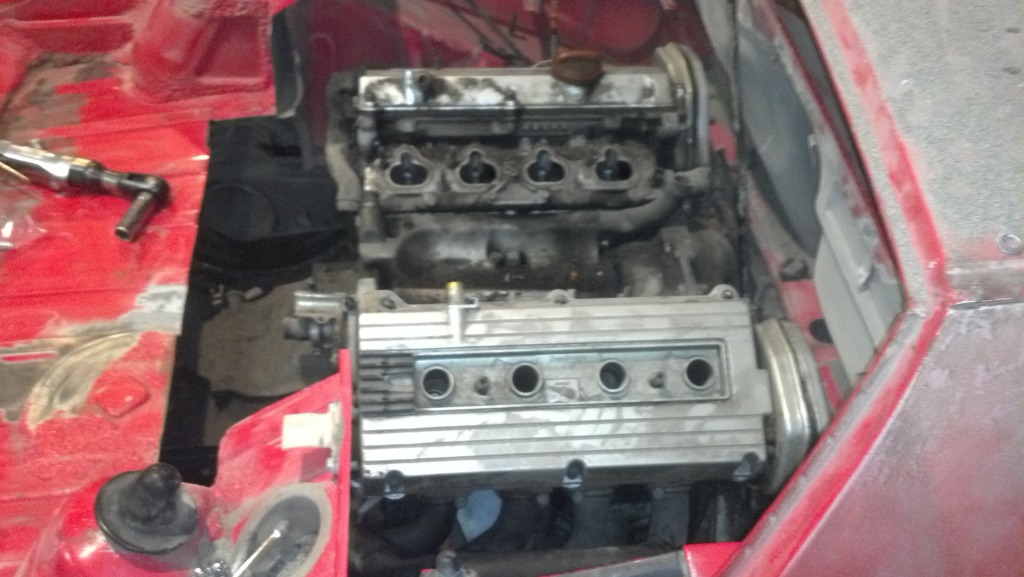
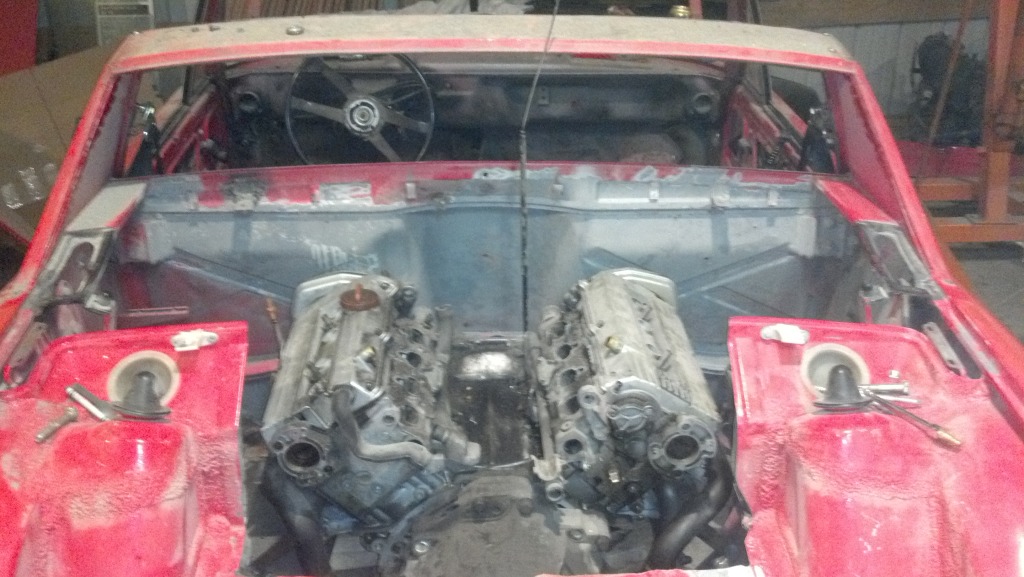
All level square and true. I'm starting to get a little skeered.
my928s4
Oct 14 2012, 08:33 AM
Coming on !! Be nice for this area to have a couple more running 914's !
rohar
Oct 17 2012, 10:43 AM
So I managed to get all the axle measurements done yesterday. What a PITA. Measure all the changes you did to the OE setup, do some geometry on the wall with a sharpie, cut a stock axle in half and hose clamp it to a piece of angle iron to verify. bolt it in, verify fit, lift the car so it goes to fully extended. Verify fit.
After all that, 18.5" exactly. Darnit, they make 18.75 off the shelf. Guess that means more phone calls and more $$$.
sixnotfour
Oct 17 2012, 04:10 PM
If you are talking sway aways, The spline length is 3 inches, so buy the 18-3/4 Trim off 3/8's each end and regroove for Snapring.
BodaBoom BadaBing
rohar
Oct 18 2012, 01:23 PM
Duh, why didn't I think of that. I knew there was a reason we keep you around!
rohar
Oct 18 2012, 03:21 PM
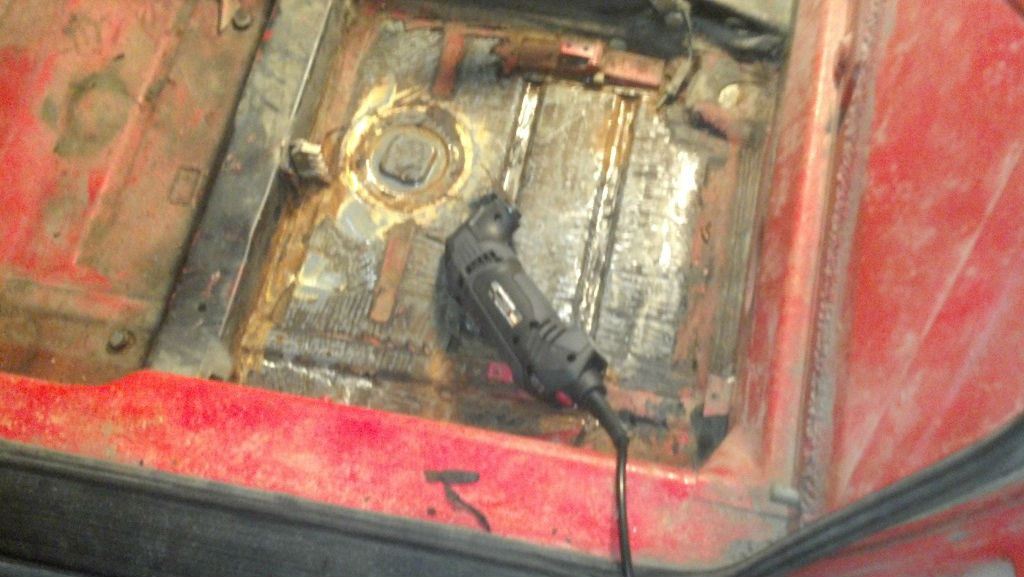
Yay! Everyone's favorite game!
rohar
Oct 19 2012, 03:16 PM
ALL the tar crap is off the floor pan. Only about 5 spots of light rust. Weather permitting I'll roll it out of the shop and blast them tomorrow. If all goes well, primer Sunday.
rohar
Oct 20 2012, 05:54 PM
QUOTE(kg6dxn @ Sep 4 2011, 03:03 PM)

I think you should keep the Audi bolt pattern too. More wheel choices and it's different than the masses...
Dang you, this thought crossed my mind again today. Wasted a whole hour with a pair of calipers figuring it out then realised, I've already got a full set of wheels, brakes and hubs.

The belly pan and trunk are now completely rust free. Couple of spots in the trunk that will have to be cut out and patched. Nothing bigger than 2x2 and only two spots so I'm feeling pretty lucky.
While I was there, I tore the pedal box out as it's not gonna work and even banged a couple of dents out of the floor where some DAPO put a jack in the wrong spot.
Primer in those two areas tomorrow then I'm done with bodywork for a while.
Stainless fuel lines and intake manifold gaskets will be here early next week. Time to start putting the old beast back together.
This is a "lo-fi" version of our main content. To view the full version with more information, formatting and images, please
click here.