Some of the challenges I’ve had to deal with or over come were:
- The height if the transmission case (at the nosecone)
- Connecting the trans to the stub axles (Porsche inners/VW outers)
- Choosing a shifter that will work
- Modifying a shifter to work
- Modify the tunnel for the shifter to fit (honestly, it’s not nearly as bad on a T-3)
- Designing shift linkage (linkage that will compensate for an un-parallel trans shift shaft)
We’ll discuss these in order. . .
Since the height of the trans at the nose cone was WAY taller than the stock T-1 trans, most times, as a fabricator you would simply add a pocket to the area under the seat and be done with it. However this is not an option with a Squareback (well at least if you still want to fold the rear seat flat like stock). So instead of moving the body up with a pocket, I had to move the mount down. Not wanting to have a trans nose hanging super low, I opted to lower the entire rear suspension sub-frame 1.5” (which effectively raised the rear of the car 1.5”). I had to make 5 custom spacers to pull this off and then also re-adjusted the height of the car with adjustable spring plates. Now, the lowest point on the car is the factory Porsche skid plate for the trans mount and it’s an acceptable 4.5”. Actual trans and engine is a full 6”+.
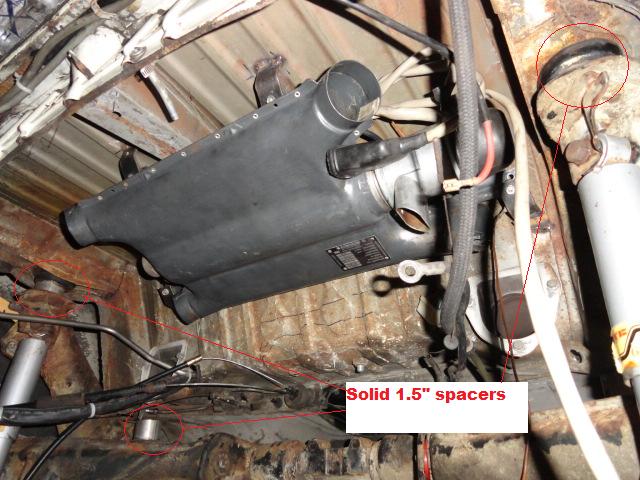
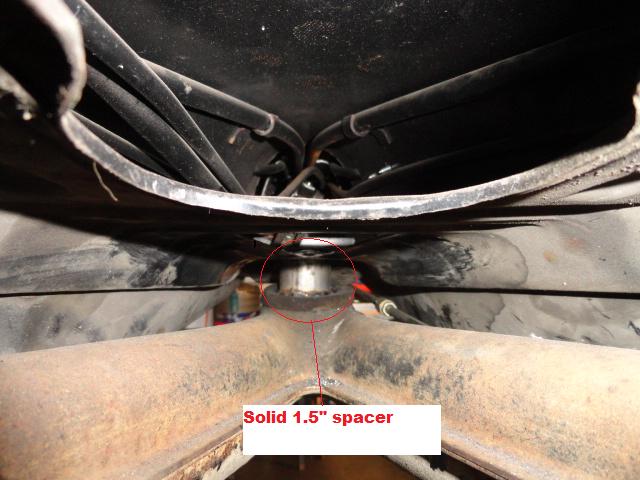
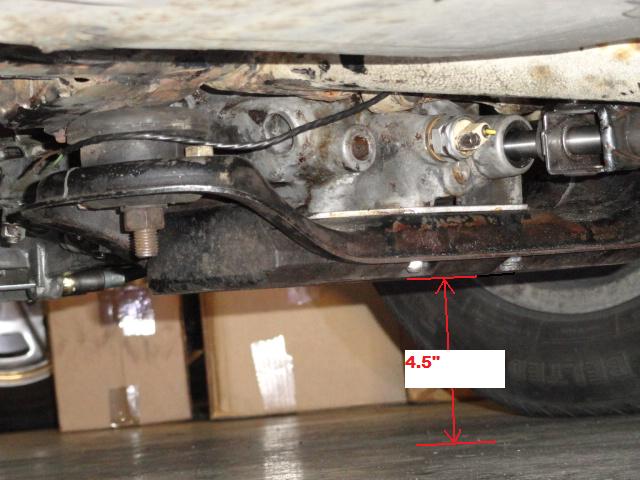
Once the trans was physically in place I had to figure out what CV/Axle arrangement to use. The 923 trans has output CV flanges that fit 911 CV joints. However I found that the output flanges are the course spline type just like a 914 (woohoo!!). I have a bumper-crop of 914 CV flanges around here, so I simply bolted a set to the trans, used stock Beetle axles with 914 CVs on the inner side and they bolt up as stock!!
When it came to shifters, I used 3 different ones before I ended-up with the one I like and worked. I did 90% of my mock-up using a slightly modified Superior Formula Vee (VW) shifter and honestly it worked great except that the shift pattern ended up being backwards due to the linkage arrangement. So that also precluded the use of a stock Porsche 911 shifter either early or the late 915 style since they all move the shift rod in the tunnel opposite of the shift handle. Normally that’s not a problem, but my shift linkage flips the movement at the trans so I had to use a shifter that would move the shift rod with the handle. My solution was a ’73-’76 Porsche 914 unit.
I did have to modify the shifter slightly so that the spring lock-out for Reverse/1st (for the 901 shift pattern) was flipped to the other side and correct for 5th/Reverse (for the 923/915 shift pattern) This was accomplished by first removing the springs and plate. Then I drilled out the welds for the alignment pin plate. Then I had to drill a new hole on the opposite side for the alignment pin plate and finally rosette welded the plate back to the other side. Viola!! A Porsche 914/923/915 shifter with correct 5th/rev lock-out.
Modifying the tunnel was pretty straightforward. On a T-3 the tunnel is wider and the shifter is more centered than a beetle. So I just needed to enlarge the center hole and mark/drill the three mount holes. I made simple nut plates out of flat stock and 8x1.25mm nuts and then welded them to the under-side of the tunnel. As a bonus to using a Porsche shifter, I was able to mount a stock Porsche 914 heater lever in the nose of the shifter for my gas heater. It won’t actuate a cable, but it will be wired as the ground for the gas heater and heater fan. It gives the look though of an early 911 shifter w/ the factory enrichment lever!!
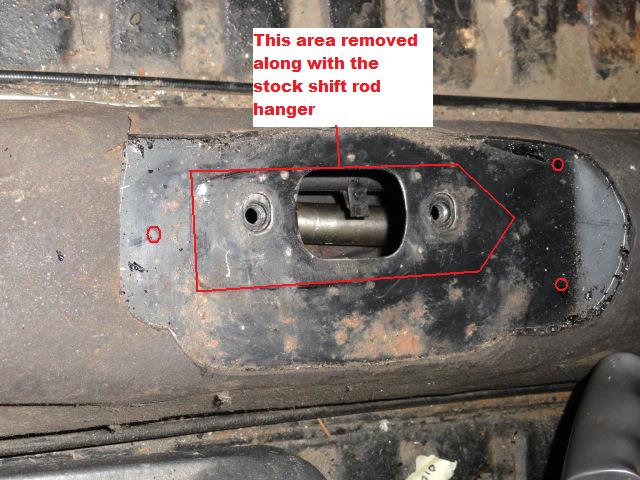
Designing the shift linkage was in a word, CHALLENGING!! Part of lowering the rear suspension was that if I lowered it straight down, not only would I have room for the trans nose cone, but an side effect was that the exhaust would also be showing more AND my intake air bellows would now not fit. So I had to mount it tilting down in front. What this did was disrupt the parallel plane between the shift linkage in the tunnel and the shift shaft at the nose of the trans (the trans was tilted about 10 degrees down). This caused stiction as you shifted. I had about a 6” drop and a 10 degree down angle to overcome. My design incorporated two, ½” heim joints to allow for movement at increasing angles without stiction. This linkage was redesigned and remade about 4-5 times before I had solved all the issues that came-up. You can now see why the stock style shifter caused the shift pattern to be flopped and why I had to go with a late 914 side-shift shifter to get the shifting back to normal. I’m really happy with the result. Shifting is positive and it’s infinitely adjustable
Rather than describe it, below are some photos to show exactly how it’s made.
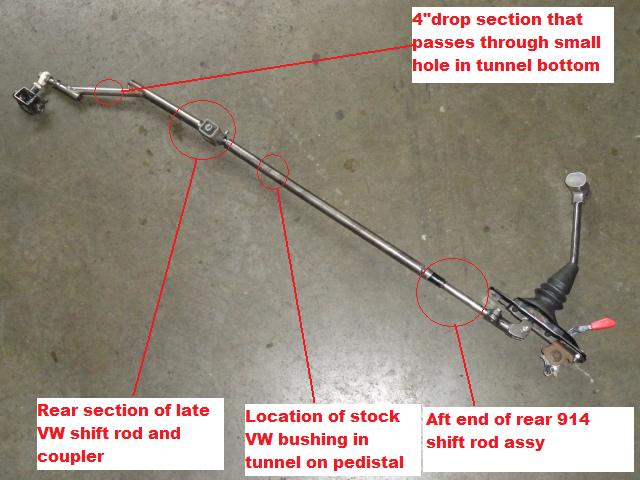
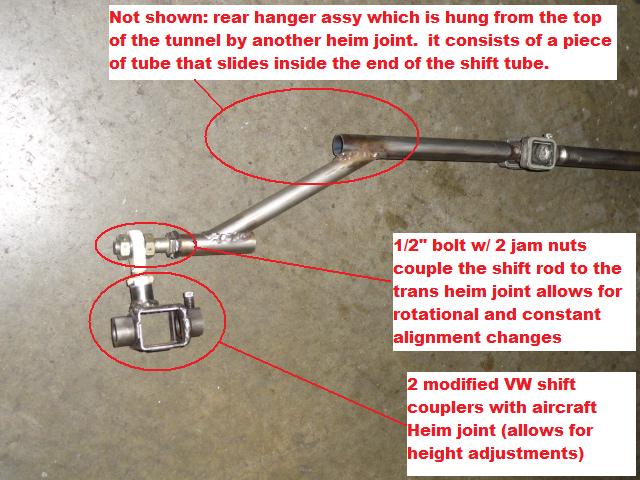
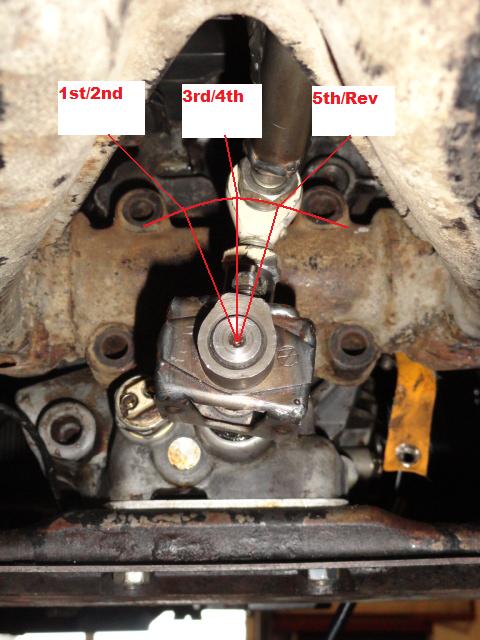