Mid week I got the combo dwell/timing light and I'm glad I spent the extra cash over a simple timing light. This unit has the digital display with volts, rpm, dwell, timing and advance timing. I had a couple hours in the evening to take a look. When I first checked dwell, it was actually really close, 43. I tried to tweek it but loosening the screw just made it much worse. So I used a feeler gauge and got it back to 43. Then I set the light to zero advance and got the engine running about 850 rpm and the timing mark was right on the money. Then I set the advance timing to 27 and rev'd up to 3500 rpm, again, right on the mark. Having the rpm display right on the light is great! Then I got out my flow meter for the carbs to see how those were breathing. With the linkage off the passenger side is 7 and the drivers side is 3.5. That's with the idle adjustment 1 1/2 turns out like the Redline manual recommends. Tweeking that adjustment enough to move the flow meter on the drivers side only makes the engine run rough. Also, with the engine on the bench stand, it's bouncing about and hard to get a good flow reading. I set my target on this weekend to get the engine in the car.
I'm up early today to beat the heat. I get the hardware together for transmission and motor mounts and start lower the car down over the engine. That goes well and I bolt up the new solid transmission mounts first. Then I lower a bit more to get the engine mount bar to line up and bolt that to the chassis. I've also got the solid motor mounts so I loosened up the old rubber mounts, put a jack under the sump and swopped the mounts. After tightening everything up and making neat coils out of the electrical and fuel lines (those are a little long so I can drop the engine and test) I get in the car a fire it up. What a difference having the engine solidly mounted! Idle is much smoother because the linkage isn't floping about. I get the flow meter out again and I'm able to bring the drivers side carb up to 7 by carefully adjusting the linkage. Smooth!
Now that the car is quite a bit lower, I decide to finish the peddle mounts. This floor pan is missing the peddle riser so there's a gap under the peddle assemble. I trim a couple of spacers to fit and bolt that proper to the pan. So now the gas peddle needs the same elevation. Instead of using more spacers, I had a piece of sheet metal that was a perfect shape (it's a segment of the floor pan cross member). I bolted the gas peddle to it and then pop riveted the sheet metal to the floor pan. Eventually I will need a large plate for my heels to rest on but that can wait.
Before I gave into to the sweltering heat, I got under the transmission to look at the shifter linkage and clutch cable. I had gotten a refurbished shifter coupler and I installed that on the the rear bar. I got that bar inserted into the correct position but I'm missing some linkage at the transmission. I also put on the clutch cable pulley and housing on but the cable itself is too far gone. Tonight I'm getting a list of parts together for clutch and shifter linkage.
All in all a very productive day!
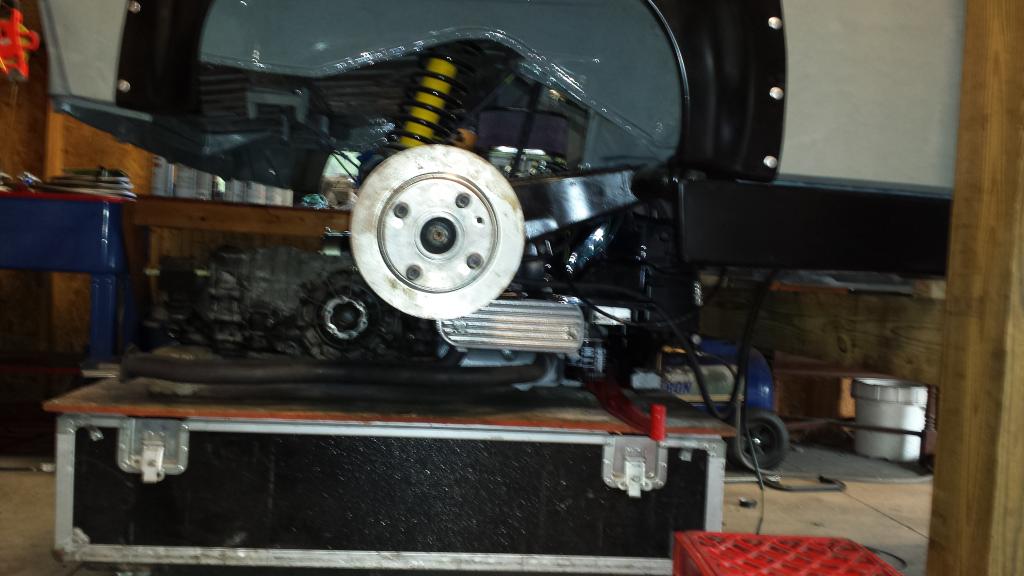
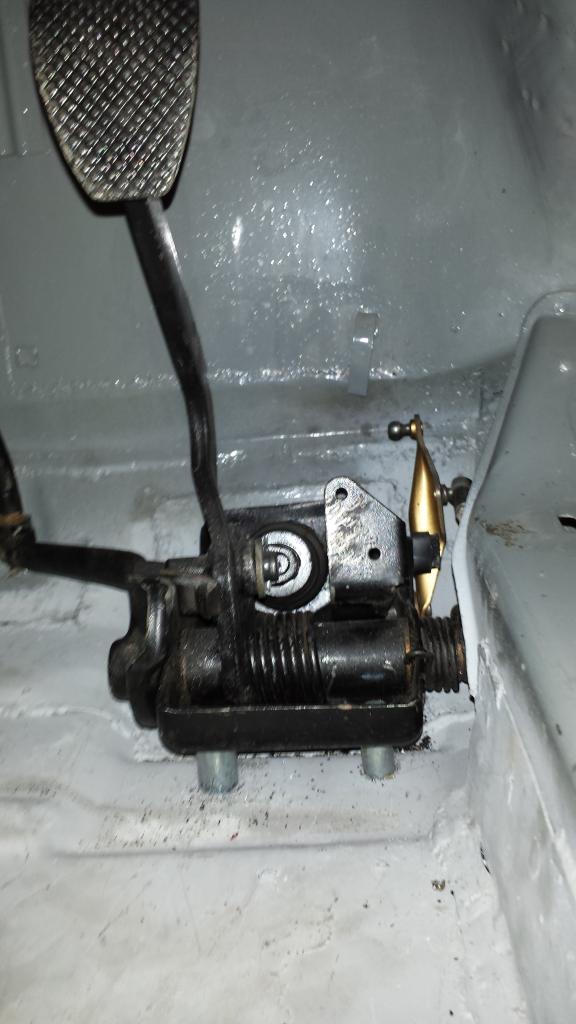
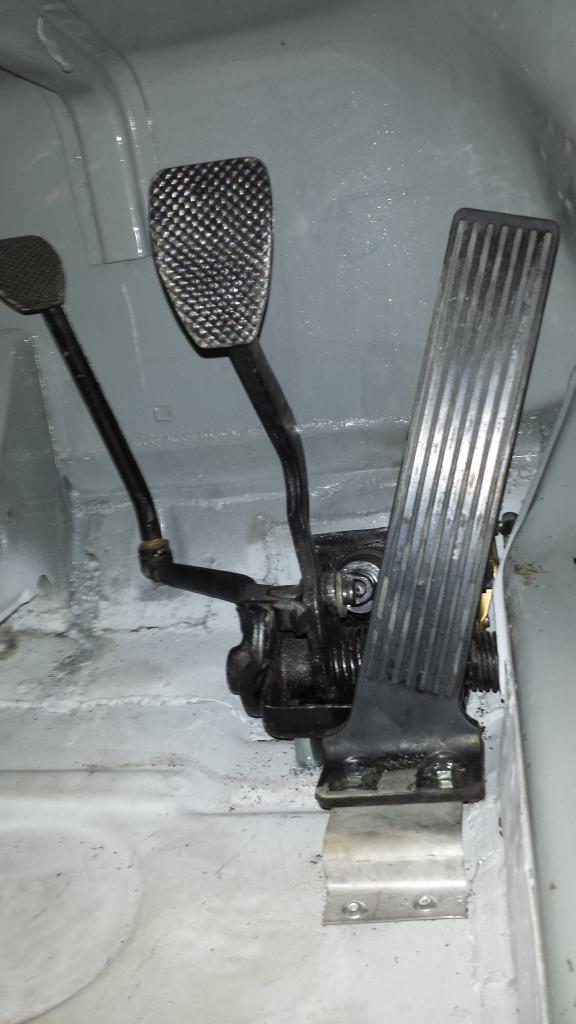