I've been thinking about how to make a jig for aligning the replacement suspension console and came up with what I think will work. I wanted a device that I could build and set up on the drivers side - then take it over to the passenger side. That meant something I could flip over and keep the same dimensions. I started with the plates that secure the outboard attachment point. Those can't be flipped over so I'm going to use both as alignment points and mark them the same.
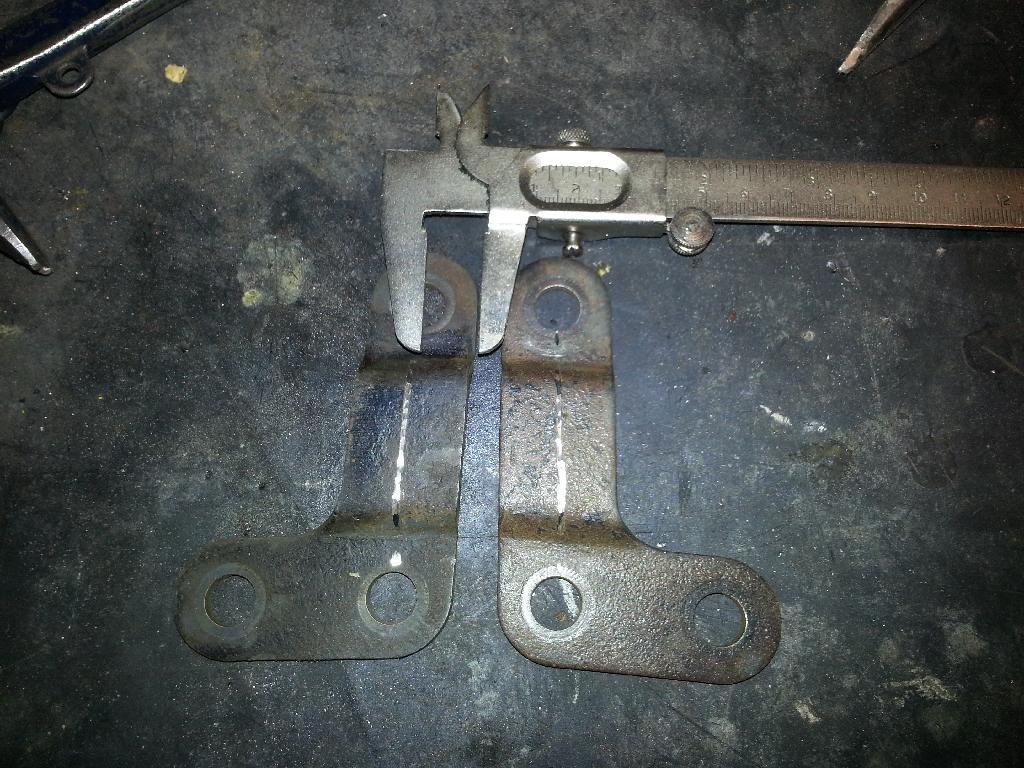
I scribed the plate down the middle (1/2" from either edge).
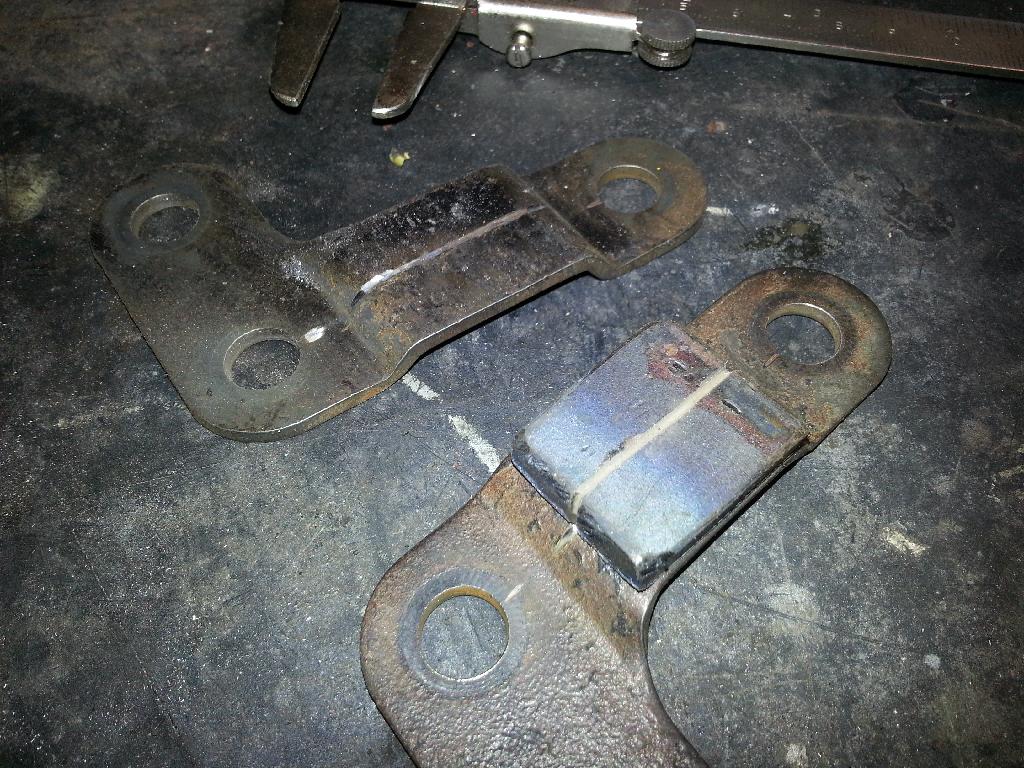
Then I cut a piece of flat stock to fit on top of the plate and made a scribe mark down the middle of it. Note that the mark goes down the side which will be important later.
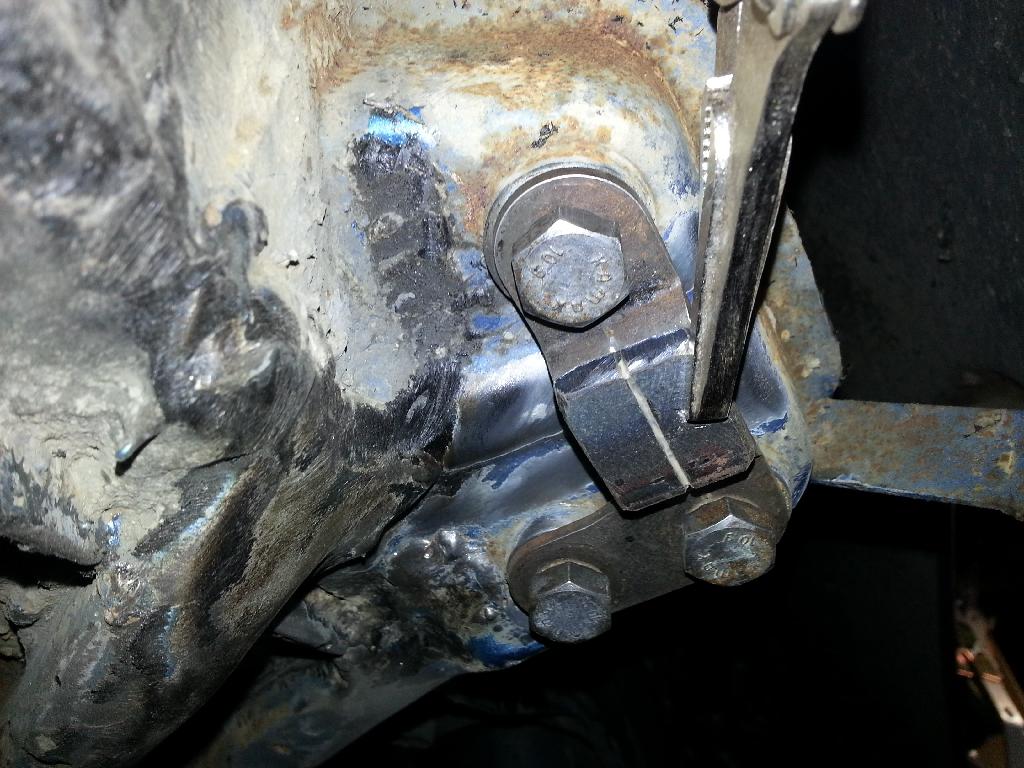
Next, to build the jig on the good drivers side, I needed to figure out how to clamp the flat stock to the mounting plate now on the car. Small needle nose vise grips work well in the confined area. Align the flat stock's marks to those on the suspension plate.
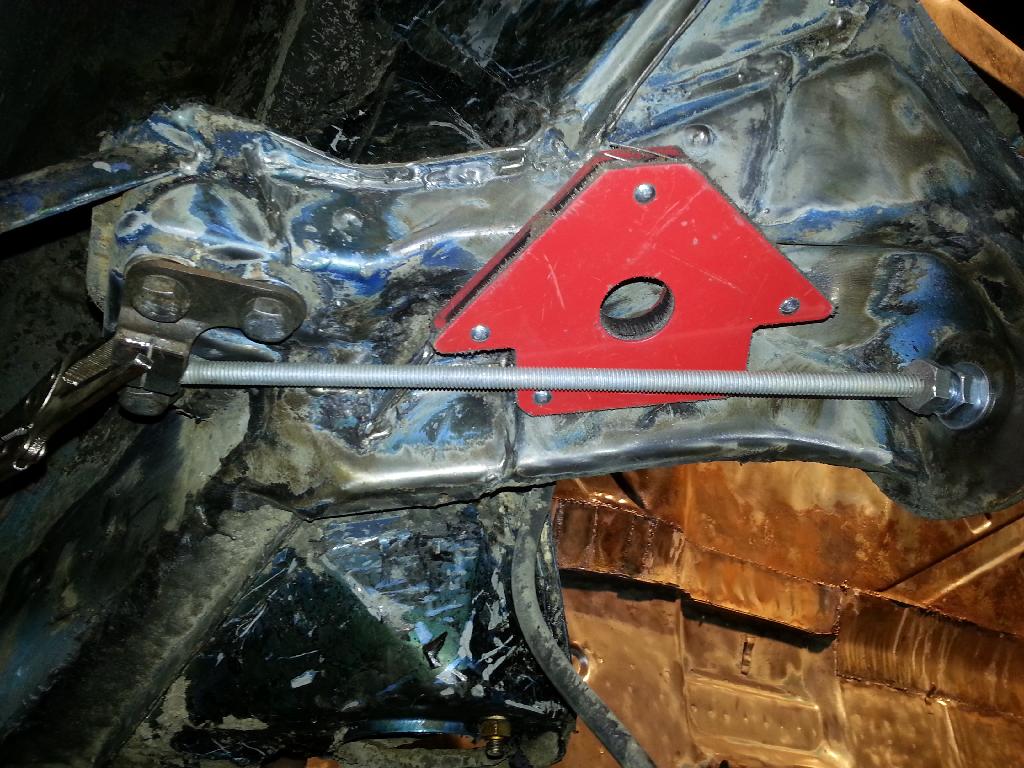
The other components of the jig are a section of 3/8" threaded rod, a 1/2" x 2" bolt with two flat washes and two nuts. I used one nut and washer as a backing, ran the bolt through the inner mounting point and tightened. Note that a 9/16" bolt will work better but of course Home Depot or Lowe's didn't have them. Then I started trimming the threaded rod to fit in-between the bolt head and the fixed piece of bar stock. Try to have the rod mate right in the center of the bolt head and the middle of the flat stock plate on the side. I used a large magnet to assist in this process. Trimming, grinding, checking till it fit just right. Once I got everything just right, I took the mig welder to the two joining points (bar stock to threaded rod and threaded rod to bolt head).
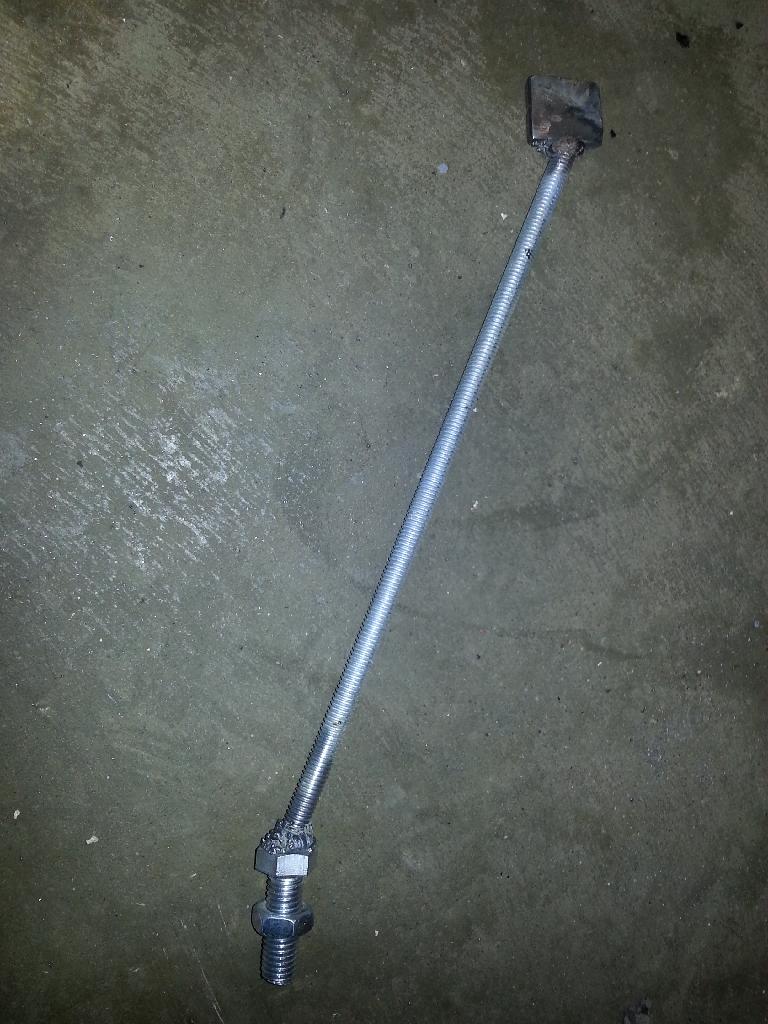
A couple of tack weld and then finish the welding with the jig in a vise. Note that my first attempt I didn't get good penetration on the bolt head and that weld failed later. Crank up the amps and feed when you weld that.
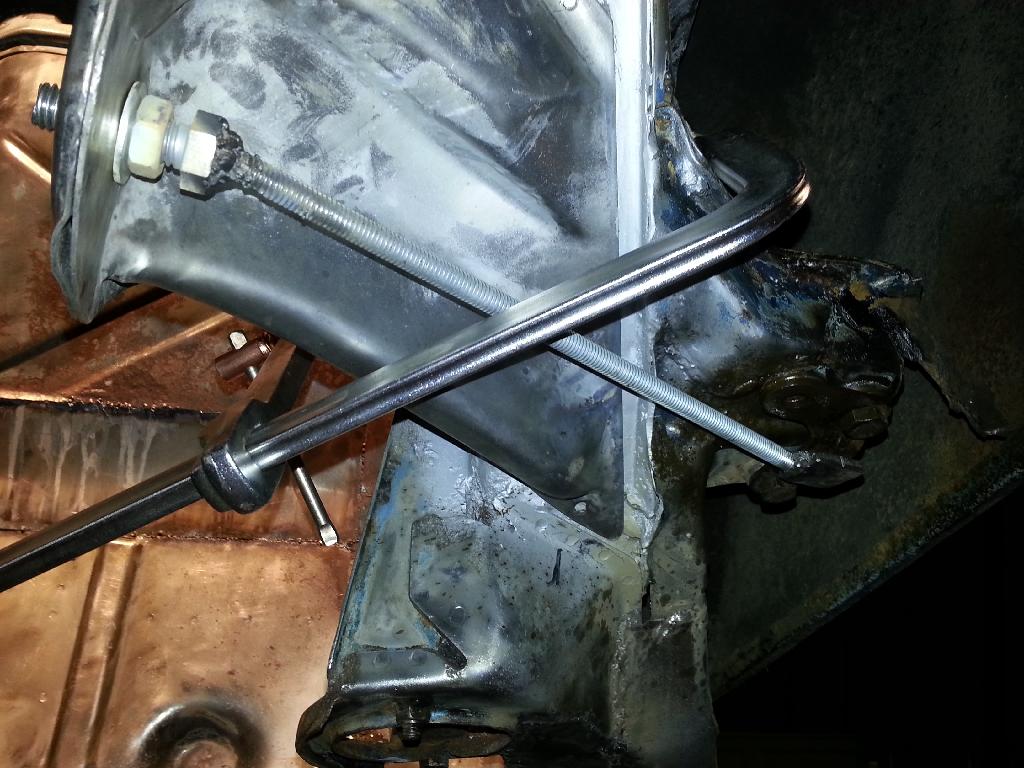
I clamped the new suspension console to the long using the old spot welds for rough location. Then I put the jig in the suspension hole and started tapping the console with a nylon hammer to get the plates aligned. It took another clamp in-between the console and motor mount to suck the console tight against the long.
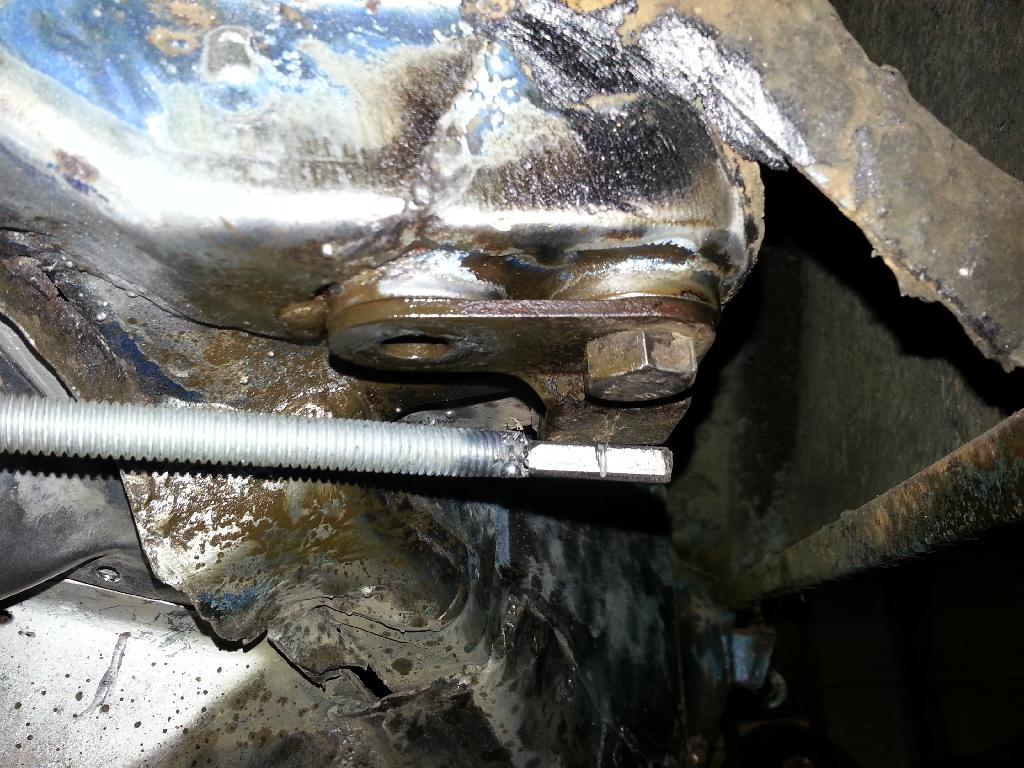
The cool thing about this little jig is when you flip it over for the other side - all the dimensions and angles are the same - almost. There's is a slight difference in the elevation of the mounting plate and the inner mount hole. So when you flip the jig over, the alignment plate is a little lower (about 1/2") but you can still get an eyeball on the center lines and the location of the bar stock to the mounting plate (side to side and front to back).
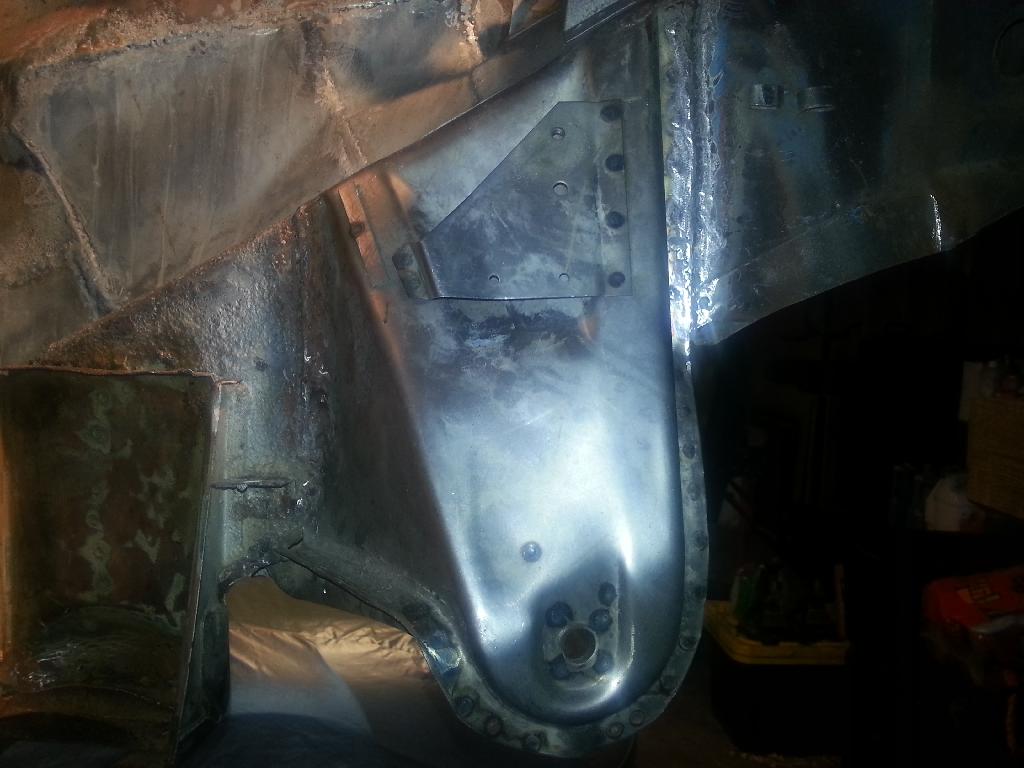
I had already drilled the console for spot welds on the sides, top and bottom. The only place you can't get spot welds is down the long seam under the long but after spot welding (and checking the jig repeatedly) I followed up with seam welds along all sides.
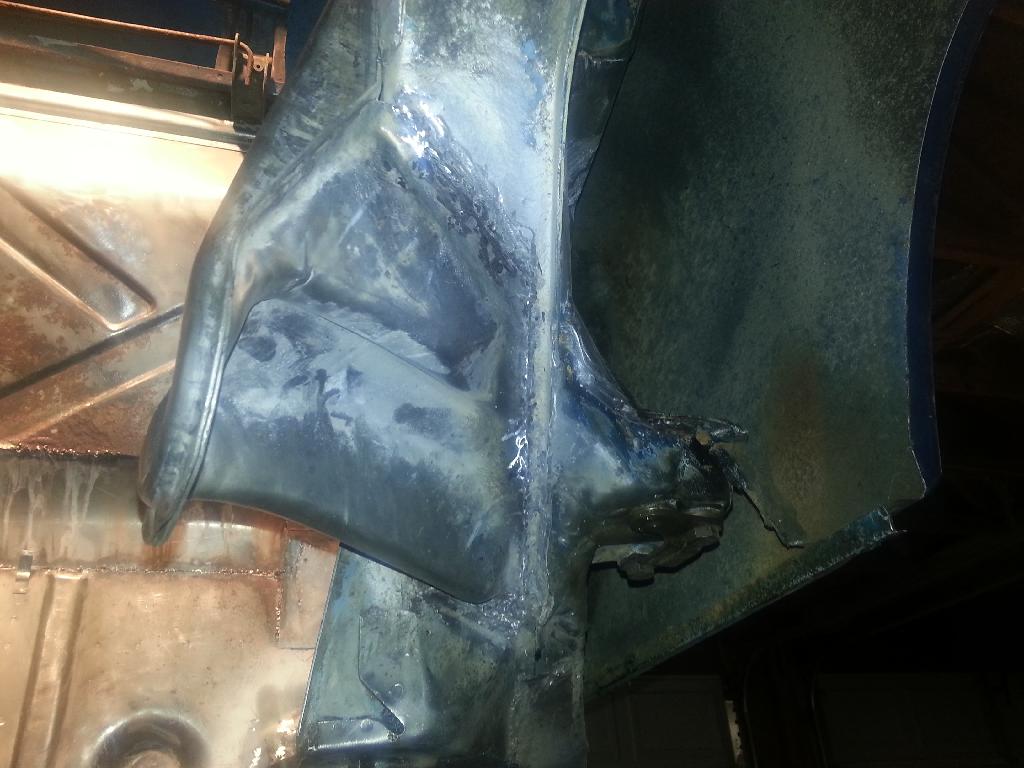
Although not a perfect alignment tool, I believe this jig got me well within the tolerances for good rear alignment. With how the RD suspension console is made - I think the deficiencies of elevation are not a factor. It would be really hard to change the elevation without effecting the other dimensions. I guess I'll find out when I get the suspension and wheels back on this joker.