Jeff Hail
Mar 8 2008, 07:38 PM
Finished welds at the inner long to rear long joint. Clean!
Wes V
Mar 8 2008, 08:33 PM
Jeff;
This might be jumping ahead, but I've got a question for you.
In the following photo, you show the frame rail section purchased from AA.
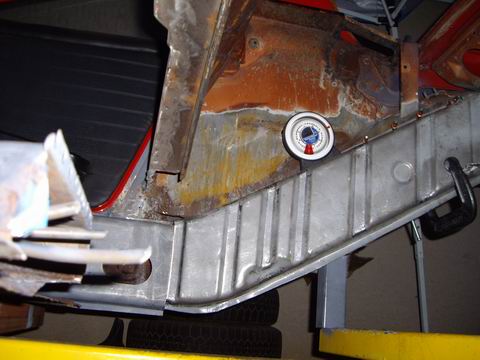
Is there another "layer" that goes over this and hides the corrugations, creating a double skin panel? It would be put in place prior to re-installing the engine tray, engine mount, rear suspension bracket, and battery tray?
My car seems to have a double skin panel in this location. (the outter skin rotted due to battery acid, the corrugated section looks reasonable)
I called AA and was told by them that the suspension console (and such) gets welded directly to the part shown in your photo. I'm pretty sure they are wrong.
I've removed the engine mount on the drivers side, and the exposed section of the frame rail is smooth.
Wes V
Jeff Hail
Mar 8 2008, 09:15 PM
QUOTE(Wes V @ Mar 8 2008, 06:33 PM)

Jeff;
This might be jumping ahead, but I've got a question for you.
In the following photo, you show the frame rail section purchased from AA.
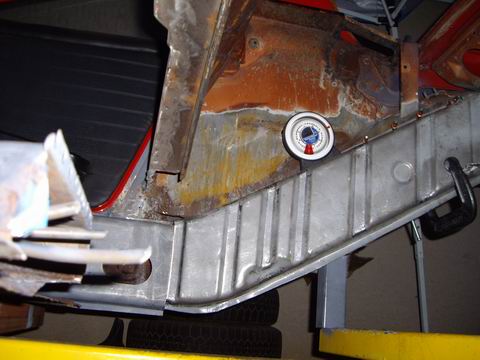
Is there another "layer" that goes over this and hides the corrugations, creating a double skin panel? It would be put in place prior to re-installing the engine tray, engine mount, rear suspension bracket, and battery tray?
My car seems to have a double skin panel in this location. (the outter skin rotted due to battery acid, the corrugated section looks reasonable)
I called AA and was told by them that the suspension console (and such) gets welded directly to the part shown in your photo. I'm pretty sure they are wrong.
I've removed the engine mount on the drivers side, and the exposed section of the frame rail is smooth.
Wes V
The factory piece has the corrugations as a reinforcement on the inside of the rail. The outer overlay is what you see in a factory car. The corrugated piece does not connect to the outer wheelhouse as it only on one side and then bends over the sides of the box about an inch and half. My take is it keep's the rail side from collapsing under suspension loads ( compression, rebound and side loads). The corrugated reinforcement extends all the way down to the seatbelt anchor plate but is basicly flat once it meets the straight inner long.
The AA part is thicker than the original inner 3 sided box but not equal to both pieces of metal combined. I question this myself and will be reinforcing this area in mine.
Here is a picture of my old part cut out. You will see how it is made up.
Jeff Hail
Mar 8 2008, 09:25 PM
Here's a couple pics that better show the rear rail/ inner corrugated reinforcements.
This area was a little different on very early cars. It was not as robust.
The later cars had little pieces here and there to reinforce parts of the car better.
( striker brackets behind the lock pillar's and the front inner longs below and inside the hinge pillar)
Wes V
Mar 8 2008, 10:54 PM
Thanks!
That's pretty much what I thought.
So, in the factory installation; the corrugated section stiffens the side wall, but isn't welded to the other side of the box.
The outer (smooth) section is what welds to the other side of the box.
What AA is selling isn't technically correct, in that it replaces the two piece "composite" that the factory used.
Jeff Hail
Mar 8 2008, 11:26 PM
QUOTE(Wes V @ Mar 8 2008, 08:54 PM)

Thanks!
That's pretty much what I thought.
So, in the factory installation; the corrugated section stiffens the side wall, but isn't welded to the other side of the box.
The outer (smooth) section is what welds to the other side of the box.
What AA is selling isn't technically correct, in that it replaces the two piece "composite" that the factory used.
Yes,
Yes,
Yes ....because it it easier to manufacturer in one piece. For the most the AA part will be sufficient. Most moden cars have frame rails that are made exactly the same way. (ala "crush zones")
Jeff Hail
Mar 9 2008, 07:58 PM
Finished grinding the welds on the inside of the wheelhouse and some more epoxy primer.
Is it perfect? No there is a thin weld bead where it was sectioned and I did not want to grind it too thin. Just above where the battery tray mounts is the most noticable. I can live with that as everything else is all good steel now.
Also fitted the lock pillar to the door and welded it up. These were brazed by the factory where they meet the sill and it took some time removing the old brass. A few rust pits where the pillar goes horizontal wiped clean with some media blasting.
Jeff Hail
Mar 16 2008, 09:41 PM
Sean,
This is what you are looking for..............
These measurements were taken from an undamaged car and cross referenced to mine. The measurements on the inner ear will vary car to car due to rust, collison, console fatigue etc. Expect a 1/4 variance when you go to take measurements. Those inner ears take a beating over a lifetime.
By triangulating from the hole in the firewall to both right and left ears you will not have a problem when you are ready to set the camber and toe.
Using the measurements in the diagram:
Taking this to another level. You can get the inner console tacked in. Then mount your control arm. Use an "All-thread" with a spherical rod end or piece of tubing where your shock mounts to the control arm, the top of the All-thread goes to the shock tower with some washers. Base the length of the All-thread on your normal ride height (sitting on the ground). Then using a camber gauge check it to see where you are before you weld everything solid. Install a wheel and tire and you can also check toe while static.
Gint
Mar 17 2008, 05:55 AM
QUOTE(Jeff Hail @ Mar 9 2008, 07:58 PM)

Is it perfect? No there is a thin weld bead where it was sectioned and I did not want to grind it too thin. Just above where the battery tray mounts is the most noticable. I can live with that as everything else is all good steel now.
Beats rust... nice work.
sean_v8_914
Mar 17 2008, 02:38 PM
thanks Jeff. I made some door gap bars with turn buckles also. I'll go make some "shock simulators and check alignment spec with a wheel back on. Im about to weld in teh ear and Im wondering if the heat induced wil move the car. Brer and I did teh cross check body measurements per teh factory manual last night. amazingly everything is within 1/8th to 1/16th. I will be very mindfull of warping,. next is teh inner long stiffener made by ENGMAN.
I used teh #s from your yellow pad schetch posted earlier to tac in teh ear. this new dwg is super sexy.
sean_v8_914
Mar 17 2008, 02:40 PM
HOLY COW!!! it measured correctly 1st shot. Im going to buy a lotto ticket (after alignment check)
brer
Mar 17 2008, 03:03 PM
I've learned alot from this thread.
Unfortuneately it means I now have to redo my entire car.
Jeff Hail
Mar 17 2008, 06:17 PM
QUOTE(sean_v8_914 @ Mar 17 2008, 01:40 PM)

HOLY COW!!! it measured correctly 1st shot. Im going to buy a lotto ticket (after alignment check)
Regarding the suspension console:
Nah it won't warp. Not enough constant heat in that area welding thin to thick metal.
Just move around with the gun a bit and get your buddy holding the beer to grab an airhose and blow to cool in between welds.
Regarding the Engman kit:
Go slow......really slow.....tack first .........then alternate the plug welds as you go on the 3 pieces. DONT weld one piece in one shot. Move around...get that buddy to blow compressed air around the weld zones. If you think its getting too hot stop and wait then go back.
sean_v8_914
Mar 17 2008, 11:48 PM
thanks for the warning. I'll go left, right, front, back.
Jeff Hail
Mar 20 2008, 09:08 PM
Little things take time!
Actually about 15 minutes
Fabricated new brackets for the airtubes. Not concerned if they look pretty. Once they are in they will never see daylight again. Removed the original, smacked it flat with a finishing hammer. Traced onto a sheet of 20 gauge steel and cut it out with hand nibbler.
I destroyed one removing the tube from the car and the other one was a non-existant little patch of iron oxide that was swept away.
Last of the original
Rough cut and bends
Final fit to the tubes
Will drop the tubes off at the media blaster tomorrow.
Jeff Hail
Mar 22 2008, 07:36 PM
Media blasted the air tubes. Welded the brackets I fabricated and epoxy primed, wet on wet with a final coat of Alu-Zinc. They will never ever rust again!
Jeff Hail
Mar 22 2008, 07:41 PM
Repaired the rust in the passenger side lock pillar.
Cut out the rusted area highlighted in yellow.
Cut some backing pieces and tacked them in. Being the metal is so thin
in this area it is a must. Even on the lowest heat setting on my Miller 180 it can still blow holes. Little fast trigger pulls.
Jeff Hail
Mar 22 2008, 07:47 PM
After welding and then slowly grinding the two areas.
The area where the air vent is is tough to get a grinder into. This rea has to be right or the door weatherstrip will not seal correctly.
Jeff Hail
Mar 22 2008, 07:49 PM
Some epoxy primer after shaping.
Oops closed the door on wet primer! Thats how I know the weatherstrip seals good.
No sail panel molding fastener holes either. Welded those up too.
The backing plates I welded in on the backside of the pillar.
sean_v8_914
Mar 23 2008, 10:25 AM
Jeff, what do you recommend to clean this up. that white paint, layers of old glue, crusty has got to go. sand, grind, paint stripper...?
sean_v8_914
Mar 23 2008, 10:27 AM
I was also thinking about fastening the battery tray and support with screws for future removal for cleaning.
Jeff Hail
Mar 23 2008, 01:35 PM
Get in there with a course wire wheel to remove any loose scale and coatings.
Depending on what you find underneath you may need to do some rust repair.
With the amount of pitting I see in the photo I would media blast the area, even some light blasting with sand will get rid of the rust . Refrain from grinding as that will remove/ thin the metal.
The white undercoating is factory primer. You can featheredge this back until you find clean metal and work on the localized area. A new product has come to the US market about a year ago. 2k Epoxy primer available in a rattle can perfect for small spot repairs such as yours.
http://www.autobodytoolmart.com/showproduc...productid=14526http://carpaint.blogspot.com/2006/03/spray-max-primer.htmlBattery tray fastened with screws? Bad idea. 25-30 pounds bouncing around will
tear it loose quickly. At least weld the lower bracket to the rail. Most of the battery weight is supported here.
Jeff Hail
Mar 23 2008, 07:01 PM
Installed the rt quarter panel that I had to cut off for the wheelhouse.
Used the butt-welding clamps to secure and align the panel. Making a series of tack weld's while stopping to cool the panel with compressed air.
More tacks, let cool, and many, many more tacks, let cool etc etc etc until one solid weld is complete all the way across the gap.
Jeff Hail
Mar 23 2008, 07:07 PM
When butt-welding along with good weld penetration the key is the grinding and finishing process.
I begin with a spot weld grinding disc to take the crown of the weld down to just above panel height. Move slow and let the panel cool. A grinder will warp thin sheetmetal just like overheating while welding.
Then I use a 3 inch 36 grit disc on a angle die grinder to take the crown down a little more.
Then I switch to a 6 inch flat flap disc and follow the crown back and forth eliminating any high spots.
Jeff Hail
Mar 23 2008, 07:14 PM
At the end I then use a different type of flap disc on a straight die grinder. I follow just the butt weld crown. This will level the weld and not dig into the surrounding metal. This type of disc is like 250 grit emery cloth.
Then I take a dual action sander with 40 grit and enlarge the area of finishing. The DA really smooths the weld and surrounding area well. Switch to 80 grit paper and then 120.
I then knocked down the inside of the qtr panel with 80 grit 3 inch discs and then a squirt of primer. I will let the primer dry and block sand the the panel Tuesday.
No bondo.
Will see after block sanding. Most likely just a skim coat of metal glaze is all it will require if that.
Still need to finish the lock pillar joint but I had plans and have to run.
sean_v8_914
Mar 23 2008, 09:08 PM
could you send me a close up of your butt weld? ...or the high res version of that photo
type11969
Mar 24 2008, 05:39 AM
Jeff-
I think you should take an extended vacation in Philadelphia. Bring your tools.
-Chris
Wes V
Mar 24 2008, 08:43 AM
Dang Jeff, I'm confused about the sequence on how you are doing this!!
In your last entry, you are welding the fender back in place.
And yet it doesn't look like you have welded the outer suspension bracket back on!!!
I know (from reading this string a lot) that you are planning on installing the Tangerine Racing (CFR) suspension relocation set-up, but from what I've been able to figure out, you will need that fender partially removed to weld everything in place! (the gusset plates in particular)
So, did you already install that and didn't say anything or what?
Are you planning on installing metal flares and feel confident that the opening for the flare (prior to welding in place) will allow you to weld in the suspension?
Wes V
Jeff Hail
Mar 24 2008, 08:15 PM
QUOTE(sean_v8_914 @ Mar 23 2008, 08:08 PM)

could you send me a close up of your butt weld? ...or the high res version of that photo
Lets see how large a file the site will let me post. I always reduce them out of courtesy to the site owner. Someone is paying for web space.
Jeff Hail
Mar 24 2008, 09:04 PM
I started blocking the primer today and ran into 2 prior repairs above the weld line.
Pink filler and yellow filler. Get out the "Mud Hog". Oh well it's only a little primer wasted.
The pink filler is below the color coat (copper) and yellow on top of old color where it shouldnt be. Hard to featheredge when it is like that. 6 coats of paint and primer I counted not including filler. The old filler is very thin and doesnt cause any concern. The red does as it is acrylic enamel or possibly Nason synthetic enamel and it has to go away because past experience dictates it will lift or react with solvent. It will get stripped even know the substrates are in suprisingly good condition.
As far as the butt weld line there are 2 small low spots (below the pink filler) and 1 more at the lock pillar that can be bumped out with a hammer and dolly or skim coated.
I have a set of steel flares and most likely will go that route although I have been talking to a fiberglass supplier that is willing to do a wide street weight version of belt line qtr panels with a reinforcement in the debris impact area. We will see?
Wes,
Lots of room under the wheelwell to install the pickups. All I need is a 3 inch cutoff wheel, an airsaw and a angle grinder.
Jeff Hail
Mar 24 2008, 09:11 PM
As close up as I can get of the butt weld line blended in
1970 Neun vierzehn
Mar 24 2008, 09:22 PM
The title of this thread should read......
Carrozzeria Hail High accolades are in order here, not only for your craftsmanship, but also for selecting a 914 to be on the receiving end of your obvious skill and talent.
Paul
Jeff Hail
Apr 10 2008, 09:22 PM
Few days off from "work"........time for play
Fitted the heater tubes. I repaired the passenger side muffler. Was a bit chewed up and falling apart on the rear end of the can . Some resin and mat should keep it together. Sprayed with high temp paint. Never to be seen again. Have not decided if I am going to run heat or not....better safe than sorry.
Welded in the Heater-J tube. Cannot install this later with the firewall on. I tried everyway possible but I really want to get the rocker done and closed up. Decided in the end it would be easier to cut a slit on the firewall and bend it back around the tube.
One important thing. The heater tube exit hole on the replacement inner long does not come flared. This is a load bearing member and flaring the hole is vital to safety. The hole needs to be radiused and the edges flared. I do not have a 2-1/2 inch punch flare so I had to get creative. Ever wonder why aircraft windows are not perfect squares? If they had squared corners they will fatigue and crack. If you round them and flare (chamfer) the opening they will simply flex. Besides the flare adds strength where the metal has been removed.
Jeff Hail
Apr 10 2008, 09:31 PM
Mocked up the firewall and lower reinforcements again (actually before I welded the heater -J tube in). Pays to recheck fit as you go. Small adjustments are easier then big ones that aren't expected.
Clutch and throttle cable conduits lined up perfect. These will be cut to proper length when the time comes.
Jeff Hail
Apr 10 2008, 09:49 PM
Cut and trimmed the new outer rocker panel to fit (I call the outer bolt on part a rocker molding).
At the rear where it fits the wheelhouse was tight so I had to bust a few welds top and bottom to get it to slide in all the way. It was hitting the inner reinforcement. Tried shoehorning it with a body spoon to persuade it but it wasn't moving back where it needed to be.
Added a backer plate at the front which will provide a clean butt weld and something to burn into. The backer is a piece of the new part that was trimmed off.
Final fit and trim..........and ran out of daylight.
Tomorrow I will punch all the holes and get this piece welded up.....
craig downs
Apr 11 2008, 12:29 AM
Its just incredible what you have done to save this car. Anybody else would have just cut it up.
Jeff Hail
Apr 11 2008, 01:57 AM
QUOTE(craig downs @ Apr 10 2008, 11:29 PM)

Its just incredible what you have done to save this car. Anybody else would have just cut it up.
All this because an Exige S pissed me off and a friend said take the 914, its free!
tdgray
Apr 11 2008, 08:39 AM
Great Job Jeff.... keep it up.
KELTY360
Apr 11 2008, 10:30 AM
QUOTE(craig downs @ Apr 10 2008, 11:29 PM)

Its just incredible what you have done to save this car. Anybody else would have just cut it up.
Well actually, he has cut it up......and now he's putting it back together.
Amazing work Jeff.
Jeff Hail
Apr 11 2008, 09:07 PM
QUOTE(tdgray @ Apr 11 2008, 07:39 AM)

Great Job Jeff.... keep it up.
Todd,
You made me laugh my ass off with:
"ass-hat (adj)- One whose head is so far up their rear end it could pass for a hat; used to describe a person who is stubborn, cruel, or otherwise unpleasant to be around".Thats a great one!
Thanks
Jeff Hail
Apr 11 2008, 09:18 PM
Welded up the right rocker. I plug welded the top from inside the car. No holes were punched on the new outer panel....the lower was done from underneath the car.
First -it's easier welding thru old steel into new metal
Second- no grinding a gazillion plugs on the exterior. No pin holes on the outside to leak.
Butt weld with a backer at the front and seam welded the rear outer wheelhouse (another area that is prone to water because the outer panel faces towards the front of the car)
Jeff Hail
Apr 11 2008, 09:40 PM
Can someone clarify if this is what a 914 rocker is supposed to look like?
I am kind of new at this and mine originally came with the translucent iron oxide version! (sick 914 humor)
I also misplaced some measurements I noted somewhere. Now where the hell did I put them? Body panels make great sticky notes!
Day is done for now. A quick squirt of primer and its time for a
Jeff Hail
Apr 20 2008, 10:38 PM
Passenger side sill plate is in.
Ran out of C02/Argon so I couldn't weld the sill triangles in.
Good tip....do not throw out those old weatherstrips. They are still important
when fitting parts such as the sill to make sure you get a proper seal on the door shell.
Jeff Hail
May 3 2008, 10:21 PM
Lite duty this week. Carpal Tunnel sucks.
Welded in the sill triangles I fabricated and prepped the threshold area.
Jeff Hail
May 3 2008, 10:26 PM
Tomorrow I will coat the gap where the rocker and sill plate meet with Wurth Seal Fix. WSF is closed cell sealer and semi rigid. Water and moisture will not get past it like the factory sealer.
Notice I installed the triangles flat side forward. The factory should have done this so as not to be a catchers mitt for road debris.
Jeff Hail
May 3 2008, 10:31 PM
The right tool for the job.
Stripped the right front wheelhouse of its undercoating in about 3 minutes.
Elbow grease....Not!
(Brake Cleaner also works like a charm and strips about everything else in the process if you don't want to invest in one of these.)
Zimms
May 4 2008, 06:45 AM
NICE WORK! Keep it coming!
Eric_Shea
May 4 2008, 08:55 AM
QUOTE
if you don't want to invest in one of these
What's that called again?
Jeff Hail
May 4 2008, 02:08 PM
QUOTE(Eric_Shea @ May 4 2008, 07:55 AM)

QUOTE
if you don't want to invest in one of these
What's that called again?
Wurth DBS 3500 (aka "the flail")
Eric_Shea
May 4 2008, 02:25 PM
@ $479.00 that may be worth it for even one car... kinda pricey though when considering a soda blast for $600.
Cool tool.
This is a "lo-fi" version of our main content. To view the full version with more information, formatting and images, please
click here.