Jeff Hail
Jun 13 2008, 12:55 AM
Didn't get much done today.
Fit the Tarett Engineering Anti Sway Bar. Holes measured drill and punch a 1-1/4 inch hole.
The brake line bracket didn't want to leave home peacefully which ended up with a slight wound requiring a quick weld and some grinding.
Measuring and installing the kit only takes about 30 minutes. It took another hour to true the wheelhouse sheetmetal so the bar doesnt bind on the bearing blocks.
If the bar binds the bushings will turn in the bores (not good) and become loose. I don't think I have to say what will happen if the bar doesn't move freely while in operation.
I also added Engmans reinforcement to the wheelhouse. Easy to understand what it's purpose is. A few folks say it doesn't do anything. I disagree. If you know how thin the wheelhouse sheetmetal really is I think it can't hurt.
The bearing blocks must be parallel to each other or the bar will bind and this is the tricky part. Engmans reinforcement helps achive this and keep them parallel.
This section and the sheetmetal directly below the fuel tank cavity are similar to a 911's design yet they are very different. This is an area I feel is a weakness in the 914 compared to the 911 body. The 911 also has it's own inherant weakness as there is no bulkhead between the strut towers. The 911 towers tend to splay open where the 914 also does just not as much. Long story but some homework supports this.
I am contemplating welding a tube from side to side to each nutplate triangle. The bar will ride inside the tube. This will keep the bearing blocks parallel at all times eliminating the what if part? ( I hate what if's when they come later)
Jeff Hail
Jun 13 2008, 01:00 AM
After the reinforcements were welded in I used some Wurth Panel Bond Structural Adhesive around the perimeter of the plates. First to seal the edges from any water getting behind them and second to give an aeshtetic blend once they are coated. Third they ain't never going to move ever! (Better Living thru Chemicals)
Once the Structual Adhesive has cured I will smooth the area out with a DA and final coat of primer.
The left wheelhouse still needs the old coating's removed and has two small rust spots at the pinchweld (flash in my book) that need to be addressed before epoxy primer can be applied.
Jeff Hail
Jun 13 2008, 01:19 AM
While waiting for glue to cure I played with some other parts.
U-Tabs welded to the front control arms and the bushing friction points POLISHED.
Yes POLISHED!
Brake line brackets fabricated, backing plate brackets painted. Rear caliper halves done....The inners are somewhere in Utah. (plug for Shea)
The caliper outers are color matched to Porsche Monoblocks. They are very red but appear very orangish in the photo.
After much thought the inner calipers would be too much a pain in the ass to powdercoat. The area where the e-brake lever pivots doesn't have enough clearance to apply 4-6 mils of powder without rubbing. The inners will be plated by Eric (two plugs for Shea in the same post) because he is THE CALIPER MASTER.
On another note I am envious of Chris Foley. He now has an assistant. I could use an assistant.....couldnt we all? CFR has added Heidi to it's staff who is internet savvy, artistic and from what I hear she has taken control of Chris's shop with an old 914 (thumper) torsion bar to ensure things get done.
Jeff Hail
Jun 14 2008, 09:54 PM
Final prep of the reinforcements, one last mockup of the bar and bearing blocks (pivots with finger pressure), weld on the brake line brackets and squirt some primer. Enough for today.
Have a
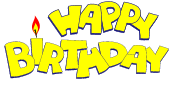
to attend.....Mine and I am going to do some heavy
and get
Tomorrow is Father's Day and will be

with pop and will do some more
Until next week.....
ChrisFoley
Jun 17 2008, 06:40 PM
Heidi's been following me around all day with one of our new Solid Trailing Arm Pivot Shafts in hand.

So here's a couple pics of today's rollcage progress for you Jeff:
Click to view attachmentClick to view attachmentI've gotta go home and tend to my wounds now.
Jeff Hail
Jun 17 2008, 08:08 PM
QUOTE(Racer Chris @ Jun 17 2008, 05:40 PM)

Heidi's been following me around all day with one of our new Solid Trailing Arm Pivot Shafts in hand.

So here's a couple pics of today's rollcage progress for you Jeff:
Click to view attachmentClick to view attachmentI've gotta go home and tend to my wounds now.

Awesome! Thats my spec cage.
I like your surface plate with the modified 914 mockup sections. Interesting how you did that. Very flexible system. Post a few more pics once the full mockup is complete for posterity.
Eric_Shea
Jun 17 2008, 08:40 PM
Happy Belated Birthday Lil'Feller!
oh no, not again!
Jun 17 2008, 09:19 PM
Hey Jeff- Seems my new "alter-ego avatar" is doing her job well......

all business from now on.....
Eric_Shea
Jun 17 2008, 10:42 PM
grrrrrrrowl
Jeff Hail
Jun 17 2008, 11:15 PM
QUOTE(oh no, not again! @ Jun 17 2008, 08:19 PM)

Hey Jeff- Seems my new "alter-ego avatar" is doing her job well......

all business from now on.....

Yes she is.... Love it!
(check Chris's email)
oh no, not again!
Jun 18 2008, 09:50 AM
QUOTE(Jeff Hail @ Jun 18 2008, 01:15 AM)

QUOTE(oh no, not again! @ Jun 17 2008, 08:19 PM)

Hey Jeff- Seems my new "alter-ego avatar" is doing her job well......

all business from now on.....

Yes she is.... Love it!
(check Chris's email)
heh, heh, heh.....we need a new emoticon, one craking a whip!
Now get back to work, all of you!!!!!!
ChrisFoley
Jun 18 2008, 11:15 AM
QUOTE(oh no, not again! @ Jun 18 2008, 11:50 AM)

heh, heh, heh.....we need a new emoticon, one craking a whip!
Now get back to work, all of you!!!!!!

Jeff Hail
Jun 28 2008, 01:10 AM
Well lets see ..................what else could go wrong today?
Received notice that the cage Chris Foley built for me was damaged in transit.
I think Chris and I are going to be optimistic and hope it just fell out of the box. Obviously not Chris's fault. In fact we are both wondering what happened? After all it's a bunch of tubing. What could happen? Did I ever say I think very highly of Chris? Never met the man in person but I just like the guy. He is just a racer kind of guy and does stuff that makes things go faster. That's good enough for me.
Received notice from another shipper that a package has been lost now for 15 days and cannot be located. WTF? How can you lose a package that has tracking numbers all over it and be insured for a bundle? Actually this was a full aluminum engine turned interior for a very important friends Pro-Stock race car that took two weeks to complete.
Today turned into a bummer !!!!!!Aaaahhhhhhhhhhhhhh!!!!!!
The good new's!
At least one package showed up today without a hitch. Inner caliper halves Eric Shea cleaned up for me. Did I ever say I think very highly of Eric? Never met the man in person but I just like the guy. He is just a racer kind of guy and does cool stuff with brakes. That's good enough for me. Listen to Eric as he has words of wisdom when it comes to brakes.
Despite todays downturn of events I had to get away and enter the inner sanctorum for therapuetic purposes.
REAR CALIPERS
BIG brakes while retaining the 914 caliper body and E-Brake with slight modifications. 14 mm spacers....for 24mm Carrera vented rotors. I didn't even fling any C-Clips across the shop! Amazing something went right today. I am calling it the J-Caliper. I bet Shea just eat's that up?
KELTY360
Jun 28 2008, 01:25 AM
QUOTE(Jeff Hail @ Oct 1 2007, 10:35 PM)

I look at rust like a diamond in the rough. Rust is afraid of me because it know's it cannot live in my world. Metal becomes submissive because I have confidence in my metal working talents.
Jeff - these bold words were part of your 1st post in this thread. You've certainly proved they are not idle boasts. I've been fascinated by your careful techniques and rigid quality standards.
Given your skills and experience, I'm curious about why you've chosen to invest this much time and energy in a 914? Other than the opportunity to scare lots of rust straight.
Jeff Hail
Jun 28 2008, 02:46 AM
QUOTE(KELTY360 @ Jun 28 2008, 12:25 AM)

QUOTE(Jeff Hail @ Oct 1 2007, 10:35 PM)

I look at rust like a diamond in the rough. Rust is afraid of me because it know's it cannot live in my world. Metal becomes submissive because I have confidence in my metal working talents.
Jeff - these bold words were part of your 1st post in this thread. You've certainly proved they are not idle boasts. I've been fascinated by your careful techniques and rigid quality standards.
Given your skills and experience, I'm curious about why you've chosen to invest this much time and energy in a 914? Other than the opportunity to scare lots of rust straight.
Because I can!.........Seriously this build has something special motivating it. Not easy to put words to it. It is what it is. In time everyone watching will see the light. Time is something I have for this one. To most it may seem like a lot of hard work for a car many would have passed on. The high road always has the better view!
In racing every class has a formula to follow. With a big grin I only know how to lead......second place is not an option.
ChrisFoley
Jul 1 2008, 10:19 AM
QUOTE(Jeff Hail @ Jun 28 2008, 03:10 AM)

Well lets see ..................what else could go wrong today?
Received notice that the cage Chris Foley built for me was damaged in transit.
...
I can hardly believe the box made it to the warehouse in Sun Valley and a FedEx worker there decided it had to come back to Connecticut.

I highly doubt the cage was damaged, but I fully expected the cardboard box to get beat up. All the indiviual pieces were strapped to the main hoop assembly with large zip ties to keep them together in the event of a containment breach. Now I won't know until next week what the problem is. It just left Bloomington, CA in a trailer this morning. Maybe if I called there yesterday I could have gotten it to go in the right direction again. Sorry Jeff, I thought I had the shipping details worked out so this sort of problem was unlikely.
Jeff Hail
Jul 13 2008, 10:59 PM
Let the insanity begin.........
Fender molds completed
1) 1st lay up in 1/2 oz fiberglass mat with epoxy resin and vacuum bagged. (1/16th inch thick buildup) This mat is so thin you can see through it when its wet. All it is for is to make an egg shell form from a conventional lay up of gelcoat, mat and resin (epoxy versus polyester). Let it cure for a few days. Weighs about 1-1/2 lbs. This was also done done to prevent mat print through with the heavy carbon fiber mat used later.
2) Kevlar tape reinforcements bonded in the stone impact zone. Metal backers (stand offs) bonded where the Dzus fasteners mount in all four corners. This will prevent crush and cracks. Metal reinforcement at the rocker molding mounting/ rear lower fender also.
3)One big ass piece of carbon fiber 5-1/2 oz mat. Ended up doing the lay up in 4 pieces. Easier to work with in wetting out the compound curves. The outside will be flawless. The underside will show the mat seams. (who cares)
Technically this type of lay up is cheating (3 stages). First - It insures less heat build up and warpage with the end thickness desired during cure. Have to sand between cured coats with 80 grit to abrade the surface in between laminates. Going this route require's carefull attention between coats to eliminate air pockets. Worth it in the end.
With fiberlgass resin (poly) you can sand it in a few hours. Epoxy is a different bird. It is not as rigid as (poly) which requires wait time until fully cured. More working time is afforded by epoxy resin depending on which hardener is used. I prefer to let cure for at least 24-36 hours. Epoxy resin has many advantages over (poly). It is UV resistant where as poly is not. It will take an impact and flex before it breaks where as poly will crack or rupture.
4) All cured and ready for trimming.
5) The finished product ready for a coat of DuraTec on the exterior.
Jeff Hail
Jul 13 2008, 11:17 PM
Products used for the lay ups and coatings. 60 minute hardener really helps. It will not cure the epoxy resin in 60 minutes but that is when the kickoff time begins. For every 10 degree's over 70 you can deduct 10 minutes. Was 90 so it was perfect. Lots of time to fix things in process before gel time.
Composites are not my specialty but easy to learn and work. Not much different than working fiberglass just different ingredients to bake the cake. I owe credit to my friend who works in the motion picture/ prop industry for assistance in this step of the game especially the molds. I learned a lot. What to and what not to do. The lay up work is very easy. Tooling the molds -well thats a little bit of a challenge.
Some things I learned....Carbon fiber is just like fiberlgass mat. It works and wets the same. In fact I felt it followed curves better. To me the same except a different color. End product is much lighter weight and stronger than fiberglass mat.
Kevlar is another animal. It cannot be sanded or grinded with ease. It will cut with a body saw once cured with epoxy resin but it is extremely abrasive resistant. As long as it has some epoxy over it it can be bonded and re-bonded by sanding the resin. It will not tear or fray. This is a new material to me and has all sorts of potential uses going thru my head now.
Final thickness is 4-5/16. Like any resin it will flow downhill with gravity to the lowest point. Perfect for street use and 3/4 bullit proof!
Jeff Hail
Jul 14 2008, 12:03 AM
By the way Eric glad to see your daughter was ok after the camping incident. As a camper myself I know strange unexpected things comeout of knowhere without warning. Been there with both extreme weather and large animals myself. It can be humbling.
Looked like an exceptional location to pitch a tent. Better weather next time.
Eric_Shea
Jul 14 2008, 12:14 AM
Thanks Jeff,
Love those newfangled Carerrraa calipers.
Jeff Hail
Jul 14 2008, 12:30 AM
QUOTE(Eric_Shea @ Jul 13 2008, 11:14 PM)

Thanks Jeff,
Love those newfangled Carerrraa calipers.

Hindsight. Should have probably gone silver (clear) plating. The Red and Yellow (gold) reminds of a zip code in 90210.

Oh well. But hey the price was right and will function as intended!
I am having ARP make the correct 7mm bolts in 12.9 grade for an undisclosed sum. Jimmy got an ear full from me over that. Always best to move forward and that is what I am doing.
Jeff Hail
Jul 21 2008, 12:01 AM
Busy week. Didn't have any time to get out into the garage.
Finally got a moment late last night (100am) to finish the right front fender and give it a squirt of Duratec. One product I really like using. It covers, it hides, it sticks and anything underneath isnt ever coming through everrrrrrrrr!
Right fender done.
Jeff Hail
Jul 21 2008, 12:02 AM
Dzus fasteners and mounting plates. I will most likely add a baffle at the rear of the fender to stop road crud from accumulating at the front of the door shell and hinge area. Nice light thin aluminum piece is in mind.
Eric_Shea
Jul 21 2008, 07:34 AM
Looks slick Amigo. Sure wish you had made an extra set of fenders. You dzus good werk.
Todd Enlund
Jul 21 2008, 01:40 PM
Man, that is one lucky 914
Jeff Hail
Aug 8 2008, 12:54 AM
Projects, projects........always a monkey wrench thrown in for good measure somewhere.
One of the projects formula was I had to retain the stock rear calipers and use spacers for the wide Carrera rear rotors. (to retain the E-brake) Spacers easy. Fasteners not so easy. I could have used Grade 10 1/4x28 bolts but I did not feel the safety factor of 20% was there. I researched and contacted Verbus. They provided the specs for the original 914 caliper bolts and confirmed my research that Grade 10 did not provide the safety/ failure factor I required. Verbus also does not make a longer caliper half/bolt in 12.9 grade. No one makes an off the shelf bolt this length.
Guess what no one including Multi-Specialty-Metric fasteners had the M7 bolts that would survive hell and back with a 20% safety factor. I learned long ago do not sacrifice or compromise anything when it comes to brakes and hardware. First rule in racing is you can only go as fast as you can stop.
I called an old aquaintance to the challenge. Gary at ARP (Automotive Racing Products). Through the "specialty department" I worked with Jay in manufacturing custom M7 fasteners that would even exceed the 8mm bolts used on the 911 Carrera calipers. 190Ksi caliper bolts with 12 point heads. Unobtainium!
Cost was startling but I did not have much choice. Still a bargain when you compare to a ready set of 914/6 calipers.
These fasteners come into "unobtainium" category when you look at the tensile strength specs. Far exceeding the 20% safety factor and the extra 14 mm in width will not flex or break. Money well spent.
Wes V
Aug 8 2008, 10:53 AM
Jeff;
Couldn't ARP have done it with studs and nuts with hardened washers. It sure would have been easier to manufacture.
Wes V
Jeff Hail
Aug 8 2008, 01:18 PM
QUOTE(Wes V @ Aug 8 2008, 09:53 AM)

Jeff;
Couldn't ARP have done it with studs and nuts with hardened washers. It sure would have been easier to manufacture.
Wes V
The length was an issue as strength diminishes with length. 8mm was not an option as the calipers do not have enough meat to drill out. The strength is based on the diameter ,grip area and length of the fasteners. Longer bolts (through), washers and nuts were not recommended with the heat span calipers are subject to. Growth and contraction with heat affect dimensions. This possibly could result in the caliper halfs shifting ever so slightly which could result in fluid seepage between the halfs. Studs were considered but would have still had "play" because the outer half would still need to be drilled to 7mm.
12.9 and higher grade fasteners require a 90% proof rating. In plain english when you torque the fasteners properly a given amount of stretch occurs. Grade 12.9 bolts are tightened right up to their 90% proof load. There is no other effective way to tighten a grade 12.9 bolt. Grade 12.9 bolts do not work effectively with spring washers or shakeproof washers. These don't bite into the hardened surface of the bolt.
Eric_Shea
Aug 8 2008, 06:26 PM
So... ARP makes the fasteners. Red Green supplied the spacers.

I just finished a set of Carera

rear calipers with the "honk'n" spacers (not as sexy as your's mind you...) and the Verbus M7 hardware was (I think) 65 and 70mm. No workie?

Damn

I just mailed them out this AM and I could have checked.
Fasteners look slick Mr.
Jeff Hail
Aug 8 2008, 07:49 PM
QUOTE(Eric_Shea @ Aug 8 2008, 05:26 PM)

So... ARP makes the fasteners. Red Green supplied the spacers.

I just finished a set of Carera

rear calipers with the "honk'n" spacers (not as sexy as your's mind you...) and the Verbus M7 hardware was (I think) 65 and 70mm. No workie?

Damn

I just mailed them out this AM and I could have checked.
Fasteners look slick Mr.
Funny thing is M7 hardware is found all over the world on cars, bikes everwhere. Just cant find replacements in these lengths in the aftermarket.
Your measurements are correct 65,70mm -why did they not work?. Bet they were 8's huh?
I thought the Carrera bolts were 8mm? Actually I think the early one's were 7mm.
Fronts were 8 for sure....maybe....ok I admit not sure on the early's.

The lates pretty damn sure though.
Never dealt with Red. Wasn't he the guy from "The Taking of Pelum One Two Three" back in 1974?
Jeff Hail
Aug 8 2008, 07:55 PM
Haven't worked on the tub in a few weeks. Now I can get back to my regular programming.
Then today my friend Chris sends me this. Have a feeling I am going to get sidetracked helping out.
Eric_Shea
Aug 8 2008, 08:23 PM
QUOTE
Your measurements are correct 65,70mm -why did they not work?. Bet they were 8's huh?
No, they worked fine for me. I was asking why they wouldn't have worked for you. It seems it would be less expensive to pick up a core pair of rear Carrera calipers and steal the fasteners.
I'm fairly certain all rear Carrera calipers are M7. The set I rebuilt had the 65 and 70mm M7... I really can't recall if they were Ribe or Verbus. The funny thing with M7 stuff on Porsche calipers is they are both Verbus and Ribe on the same caliper. Ribe made the longer fasteners on the 914 front caliper and Verbus made the shorter ones. Maybe this is why Verbus didn't have anything listed...

Ribe is listed at 12.9 and Verbus is 11.9
Jeff Hail
Aug 8 2008, 10:04 PM
QUOTE(Eric_Shea @ Aug 8 2008, 07:23 PM)

QUOTE
Your measurements are correct 65,70mm -why did they not work?. Bet they were 8's huh?
No, they worked fine for me. I was asking why they wouldn't have worked for you. It seems it would be less expensive to pick up a core pair of rear Carrera calipers and steal the fasteners.
I'm fairly certain all rear Carrera calipers are M7. The set I rebuilt had the 65 and 70mm M7... I really can't recall if they were Ribe or Verbus. The funny thing with M7 stuff on Porsche calipers is they are both Verbus and Ribe on the same caliper. Ribe made the longer fasteners on the 914 front caliper and Verbus made the shorter ones. Maybe this is why Verbus didn't have anything listed...

Ribe is listed at 12.9 and Verbus is 11.9
The original Verbus I pulled off was 12.9 on all. One concern was when they are proofed (torqued to 90%) they really arent supposed to be reused over and over. I doubt I would ever have a problem but don't want to find out.
Jeff Hail
Aug 9 2008, 08:46 PM
Back to the regular program.........
Stripped the nose and primed today.
3rd pic shows driver side cowl with a bit of rust in the usual place.
Jeff Hail
Aug 9 2008, 08:47 PM
Easy day
KELTY360
Aug 9 2008, 08:58 PM
QUOTE(Jeff Hail @ Aug 8 2008, 06:55 PM)

Haven't worked on the tub in a few weeks. Now I can get back to my regular programming.
Then today my friend Chris sends me this. Have a feeling I am going to get sidetracked helping out.
So when does the engine go back in the Mulholland RSR?
plymouth37
Aug 9 2008, 09:48 PM
My god those fenders are fricken amazing! How much for a set, serously I need those, where should I send the check?
You are going into production with these whether you like it or not!
Jeff Hail
Aug 9 2008, 10:15 PM
QUOTE(KELTY360 @ Aug 9 2008, 07:58 PM)

QUOTE(Jeff Hail @ Aug 8 2008, 06:55 PM)

Haven't worked on the tub in a few weeks. Now I can get back to my regular programming.
Then today my friend Chris sends me this. Have a feeling I am going to get sidetracked helping out.
So when does the engine go back in the Mulholland RSR?
When my phone rings?
Jeff Hail
Aug 9 2008, 10:53 PM
QUOTE(plymouth37 @ Aug 9 2008, 08:48 PM)

My god those fenders are fricken amazing! How much for a set, serously I need those, where should I send the check?
You are going into production with these whether you like it or not!
Lot of time to make them Dana. I did make 4, other 2 are in storage as spares- I hope I will never need them. Believe me I thought about making a run but they were very time intensive to do. The last two I pulled in a big hurry and distroyed both molds in the process. No kidding.
I will be doing a set of 12 inch rear flares in c/f soon. These will be tricky as I have no plug to pull a mold from. I have a few ideas though

....running around this head of mine.
By the way nice project you are doing. You have impressive skills.
Jeff Hail
Aug 20 2008, 09:11 AM
Fitting the front structure. Just tacked so I can square all the pieces during the mockup.
Fit of the pieces is perfect considering it began as an email and photo in California and fabbed in Conneticuit (by Chris Foley). Chris's work is first rate.
All ties into the lower control arm and suspension crossmember control points at the same time triangulating the nose and cowl. Very light weight.
Hey Chris think the headlight motors are going to fit?
Eric_Shea
Aug 20 2008, 09:25 AM
Looking great Jeff. Is a GT shroud going to fit in there? Are those bottom pieces going to tie into the crossbar somehow?
I've been wanting to do the same bracing up front but I haven't been able to figure out a way around the oil lines on the left and the fuel pump on the right. Looks like your design would clear the fuel pump though.
Jeff Hail
Aug 20 2008, 10:02 AM
QUOTE(Eric_Shea @ Aug 20 2008, 08:25 AM)

Looking great Jeff. Is a GT shroud going to fit in there? Are those bottom pieces going to tie into the crossbar somehow?
I've been wanting to do the same bracing up front but I haven't been able to figure out a way around the oil lines on the left and the fuel pump on the right. Looks like your design would clear the fuel pump though.
The lower base plates at the bulkhead attach directly on the opposite side of the suspension crossmember mounts. Those will get reinforced also inside the tunnel spreading the load area out further.
Gt shroud? Nope! Have something else in mind.
Jeff Hail
Aug 30 2008, 08:02 PM
Have not had much time to play. Day job busy. Helping others with projects. Like they say nice guys finish last!
The passenger side of the car is officially completed (minus RR flare which is will be done soon in CF).
Today I finished all the mounts for the right side front fender. Added the two remaining Dzus fasteners on top. Little things take time. Done!
All the mount brackets on the underside also have backing plates bonded to the fender itself so it does not crush or crack.
Jeff Hail
Aug 30 2008, 08:05 PM
Finished up the front structure.
It is still only tacked at the base plates but all the tube to tube joints are welded.
I need to cut the tacks and work on the right side front control arm mount bracket. (it has a minor issue to address)
ChrisFoley
Aug 31 2008, 05:45 AM
Looks good Jeff!
Eric, a gt cooler shroud would fit fine. The tubular structure is wider and higher than the f/g piece.
Rocket Man
Sep 5 2008, 08:20 PM
Jeff,
Awesome work and great thread…

you have inspired me.
I have a couple of questions to help me determine where to re-start on my garage queen teener.
1. Where did you find the factory tolerance info on the starting page of your thread, quoted below?
“Keep in mind that tolerances for the 914 were 7-9mm from the factory so anything you can do to make it better is worth it.”
Is this info documented anywhere, and do the tolerances include door gaps and hood-fender gaps?
My rear trunk lid to fender gap gets wider on both sides going from the back to the front…I suspect it could be from a questionable fender flaring process from the PO.
2. Is there a preferred way to remove/separate parts that have previously been seam welded rather than spot welded together, such as a previously replaced battery box or front fender, without damaging either the part being removed, or the part it is removed from? A battery box is not so valuable, but a front fender is. I want to remove and re-use the fender, and do it right, unlike the PO.
Thanks, and keep your progress updates coming.
Eric_Shea
Sep 5 2008, 08:58 PM
QUOTE
Eric, a gt cooler shroud would fit fine. The tubular structure is wider and higher than the f/g piece.
That's what I was thinking. There might be hope for a suspension tie-in for me yet.
Jeff Hail
Sep 12 2008, 02:44 PM
r_towle
Sep 12 2008, 02:49 PM
What did Jeff do this week???
Inquiring minds want to SEE
Rich
Jeff Hail
Sep 13 2008, 09:00 PM
QUOTE(r_towle @ Sep 12 2008, 01:49 PM)

What did Jeff do this week???
Inquiring minds want to SEE
Rich
CF+EPR= REAR FLARES DONE
No showy yet. Just pulled from the molds.
This is a "lo-fi" version of our main content. To view the full version with more information, formatting and images, please
click here.