Trying to do as Ben says and keep plugging along. Yesterday, I got a lesson in why it is so important to wear underwear when doing a project like this because I just about

my pants when I bolted on the door and dry fit the jamb to check door gaps. They were WAY off

It was hard to tell how much was because the jamb needed to be tweaked for fitment, and how much was a real problem. But the gap was zero near the door handle, and (I'm just guessing) 15mm lower on the door. I decided I needed to trim the sail panel enough to clamp it on for a dry fit so I could properly align the jamb the way it will be in in its final resting place. That took a bit of fiddling to get right, but I finally got there and things started looking MUCH better.
Click to view attachment But there was still a major concern. At the spot labeled "A" in the above pic, the door was 2mm higher than the quarter panel. I adjusted the sail panel as much as possible but still couldn't get things to line up. I looked for any possible adjustments at the door hinges and found none. It was puzzling because my measurements from roll bar to window frame, and across the door opening were both spot on with factory specs.

It made no sense and I was getting really worried that something was seriously bent or torqued. Then I decided to just push down on the door above the handle area and presto, the door went into perfect alignment.
Click to view attachment Click to view attachmentIt's a little unsettling, but other than a couple small rust patches in the skin, the door is solid. Apparently, there is enough give in the door that it can be bent up or down a few mm.
Anywho, with that little nightmare out of the way, I spent the next couple hours plug welding the long shut. I'm getting better at my plug welding technique, but still have a tendency to overfill the holes a bit, leaving enough dome that they need to be touched with a grinder.
Click to view attachment After welding, the door fitment and measurements were unchanged.
Click to view attachment Just as a refresher of where this door started:
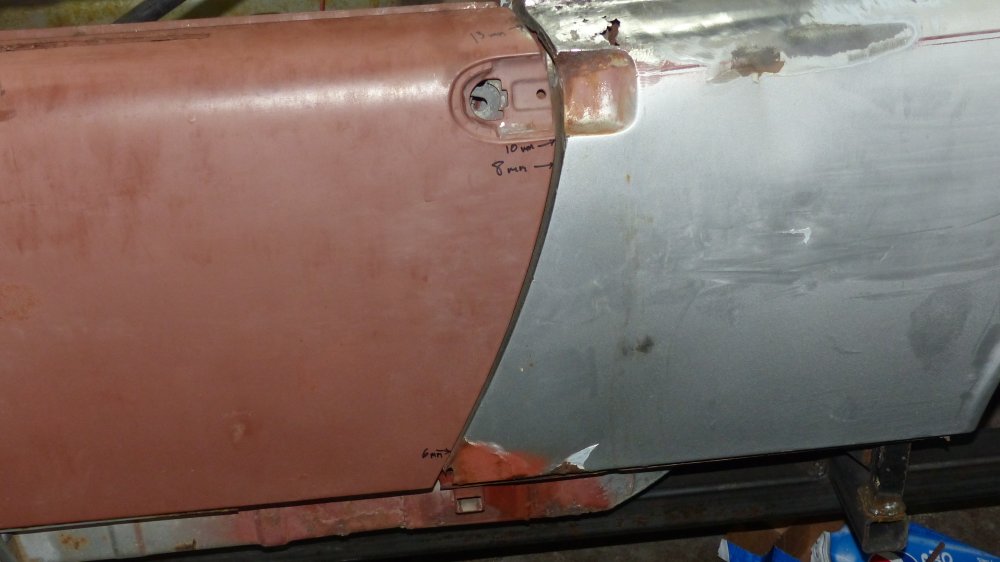
Nice improvement.
Last night, I got the jack tube welded in. Unfortunately, the replacement gun liner I ordered for my welder was for the newer style Handler and didn't fit my old unit. This leaves me with no way to run .035 wire until I find a replacement. So the inside weld around the tube required some grinding to not look like a pile of bear crap. After getting the tube in, I called it a night.
This morning, my welder gas was running on empty so I tried to use it all up in time for a run into town for a fresh exchange. I welded on the jack pyramid. I'll leave welding around the tube until I can run thicker wire.
Click to view attachment I was still getting 20 lbs of pressure at the gun so I kept going. I welded in the threshold.
Click to view attachment Still had gas, so I burned on the brackets.
Click to view attachment Still had gas. So I started on the door jamb. Got it plugged on in a few spots and the gas gave out... 10 minutes too late to get to the welding shop before they closed at noon
Click to view attachment Oh well, welding is over for the weekend. But there is plenty of other stuff to do. I ended with clamping the sail panel back on to admire the progress.
Click to view attachment The gap is down to 2mm at the door handle, but that is just because I don't have the sail panel aligned exactly right. It will be fine with final fitment. I think this will be a good time to do a little shop cleanup and organizing.